Червячные фрезы для червячных колес
Похожие статьи вашей тематики
У червячных фрез для цилиндрических колес габаритные размеры фрезы выбирались из соображений точности профиля, прочности фрезы и т. д. Таким образом, диаметр и угол наклона (подъема) вит- ков фрезы не зависели от конструкции зубчатого колеса.
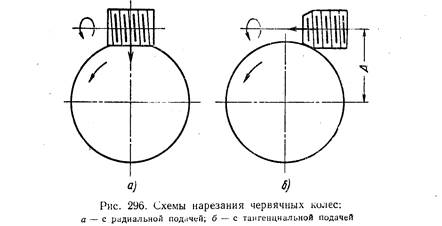
Иное положение получается при разработке червячных фрез для червячных колес. Фреза для червячного колеса должна быть копией червяка, поэтому диаметр фрезы, шаг и угол наклона (подъема) витков должны в точности соответствовать тем же элементам червяка.
Для червячной передачи могут быть приняты" все три типа червя- ков (архимедов, эвольвентный и с прямолинейным профилем в нор- мальном сечении). Выбор типа червячной фрезы зависит от типа червяка, принятого в червячной передаче.
Различают два способа фрезерования червячных колес: фре- зерование с радиальной (рис. 296, а) и с тангенциальной подачей (рис. 296, б). В первом случае углубление фрезы в деталь происхо-' дит в радиальном направлении путем постепенного сближения детали и фрезы. Во втором случае расстояние А между осями червячного колеса и фрезы остается постоянным, а фреза имеет поступательное движение вдоль своей оси. Фрезьг предназначенные для тангенциаль- ной подачи, снабжаются заборным конусом. Второй способ фрезеро- вания является более точным, поэтому первый способ (радиальной
подачи) применяется только в тех случаях, когда на станке нельзя сообщить фрезе тангенциальную подачу.
Фрезы для червячных колес выполняются как насадными, так и хвостовыми (это зависит от диаметра и модуля червяка.) Хвосто-
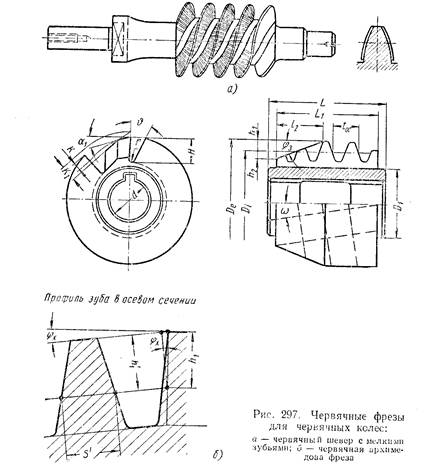
вые фрезы употребляются лишь в тех случаях, когда не представляется возможным сделать отверстие во фрезе.
На рис. 297, а показана червячная эвольвентная фреза с насе- ченными мелкими зубьями. Она представляет собой инструмент для снятия очень мелкой стружки, так называемый червячный шевер.
Зубья такой фрезы срезают тонкие стружки — «скоблят», образуя профиль червячного колеса. Такие фрезы применяются для оконча-
352
12 В. А. Аршипов
353
тельной обработки червячных колее, сцепляющихся с эвольвентным червяком.
На рис. 297, б изображена фреза, предназначенная для работы с тангенциальной подачей. Она имеет заборный конус, на котором расположены зубья, имеющие затылование по конусу.
Существуют червячные одмозубые фрезы-летучки (рис. 298). Фреза- летучка имеет один режущий зуб 1, выполненный по профилю рейки и вставленный в оправку 2. Фреза очень проста в изготовлении, но малопроизводительна и поэтому применяется только в случае крайней необходимости, когда требуется нарезать одно или несколько червячных колес, а обычную червячную фрезу изготовить сложно. Широкое распространение получили червячные фрезы, в основу конструкции которых положена архимедова винтовая поверхность (вследствие простоты изготовления точного архимедова червяка).
Исходными данными -для проектирования этих фрез являются модуль т; число заходов червяка n; средний диаметр червяка Dcp; угол зацепления d 0; максимальное число h 2 ' зубьев червячного колеса; высота ножки зуба червячного колеса и червяка hi '.
Разберем расчет основных элементов чер- вячной фрезы в том порядке, в каком он
п пп„,, обычно производится.
Рис. 298. Червячная одно- „ '
зубая фреза-летучка Определение делительного
диаметра Dt. Нам известен средний диа- метр Dcp червяка. Необходимо учесть, чтофреза должна перетачиваться, поэтому диаметр Dt принимают больше сред- него диаметра Dcp червяка на величину запаса на переточки. Этот запас устанавливается до (0,1¸0,05) т, т. е. Dt = Dcp + (0,l¸0,05) m (чем больше модуль, тем меньше относительный запас [121]).
Угол наклона канавок на расчетном диаметре определяется по формуле

где т — модуль;
п — число заходов червяка.
Высота головки зуба h 1 фрезы должна быть равна высоте h 2" ножки зуба червячного колеса. Высота ножки зуба к, фрезы должна быть равна высоте ЛГ поиски червяка. Полная высота профиля h = h 1 + h 2.
Осевой шаг t, x от зуба к зубу должен- соответствовать осевому шагу червяка и может быть подсчитан по формуле
t ос = m.
Если червяк многозаходный, то осевой будет равен осевому шагу, умноженному на число заходов, т. е.
t = mn — t oc n.
Радиусы закругления головки r 1 и ножки r 2 зуба фрезы прини- маются по профилю исходной рейки для червячной передачи (про- филь исходной рейки должен быть задан при проектировании).
Наружный диаметр фрезы должен складываться из делительного диаметра и двух высот головки:
De = Dt + 2 h 1
Задний угол а, на вершине зубьев находим исходя из минималь- ного угла ах в нормальном сечении:

Число междузубых канавок определяем по формуле
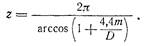
После такого предварительного расчета следует вычертить зуб фрезы и убедиться в правильности принятого числа зубьев.
Шаг винтовых канавок SK определяется так же, как у червячных фрез для цилиндрических колес, по формуле
SK = Dt ctg .
Углом канавочной фрезы v вначале задаются, а затем проверяют его пробным вычерчиванием впадин. Обычно угол v колеблется в пре- делах 22—30°.
Величину затылования К можно найти по формуле

где обычно равен 8—12°.
Если профиль фрез шлифуется, следует делать двойное затыло- вание; К1 = (1,2¸1,3)К.
Глубину Н канавки можно определить по формуле

Радиус закругления r дна канавки фрезы задается из конструк- тивных соображений. Можно использовать для расчетов формулу
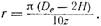
Угол х наклона верхних участков профиля к оси фрезы рас- сматриваем в осевом сечении. Прежде чем определить угол x, рас- смотрим, какие особенности вносит затылование в построение про- филя зуба в осевом сечении.
354
355
На рис. 299 показана схема затылования боковых сторон про- филя зубьев червячной фрезы. Резец, начинающий затылование пер- вого зуба в точке D1 при вращении фрезы и перемещении затыло- вочного суппорта, должен за один оборот фрезы занять положение, показанное пунктиром; при этом точка D 1 переместится в положение D2.
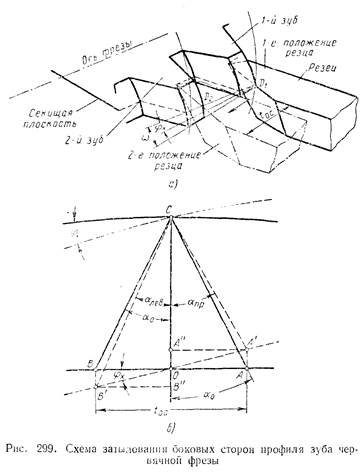
На рис. 299, а показана секущая плоскость, проходящая через ось фрезы. Так как каждый зуб фрезы должен быть затылован по архи- медовой спирали, то благодаря наличию винтовых канавок с углом w точка D., ближе к осп фрезы, чем точка D1. Следовательно, каждый зуб фрезы будет находиться и разных стадиях затылования, и в сече- нии осевой плоскосш вершины зубьев буду! наклонены под углом q > x к оси фрезы.
356
Угол фд. определим по формуле

где SK — шаг канавок фрезы;
К — величина затылования фрезы; z — число зубьев фрезы.
Углы профиля прав и лев (правой и левой стороны) определяются следующим образом. На рис. 299, б сплошными линиями показана сторона профиля червяка с углом 0. Когда площадки зубьев будут наклонены по углом x., исказится и весь профиль. Точка А пере- местится в положение А'; точка В — в положение В', но осевой шаг t c как в первом, так и во втором случае останется постоянным.
Отсюда можно найти следующие соотношения.
Для правой стороны профиля отрезок
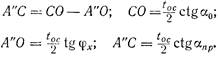
Подставив найденные длины отрезков, получим

После сокращения получим

Для левой стороны профиля получим соответственно

По этим формулам определяются углы апр и а.„.в. Эти углы должны быть проставлены на чертеже осевого сечения затылованного зуба. Высота h \ головки зуба в осевом сечении

Толщина S ' зуба на начальном диаметре

Угол з заборного конуса фрезы

где т — модуль;
R — наружный радиус червячного конуса. Длина /2 заборного конуса

357
Длина L1 рабочей части фрезы
L 1 = l 2+ h ctg0+ toc.
Остальные элементы фрезы (общая длина, тип крепления, номер конуса и т.д.) должны быть увязаны со шпинделем зубофрезерного станка, на котором производится работа. Рекомендуется при этом вычертить в масштабе два положения детали (в начале и в конце наре- зания), вычертить фрезу и графически определить все остальные ее элементы.
Насадные фрезы дешевле, и только в тех случаях, когда диаметр фрезы мал и не позволяет делать фрезы с отверстием, допускается проектирование хвостовой фрезы.
§ 4. ЧЕРВЯЧНЫЕ ФРЕЗЫ ДЛЯ КОНИЧЕСКИХ КОЛЕС СО СПИРАЛЬНЫМ ЗУБОМ
Для нарезания конических колес со спиральным зубом по методу
обката на специальных станках применяются конические червячные
фрезы. Схема процесса показана на рис. 300.
Обрабатываемое колесо находится в зацеплении с воображаемым
плоским колесом; вместе с плоским колесом совершает движения
коническая червячная фреза, об- катывая при этом нарезаемое колесо. В результате обката на нарезаемом колесе фрезеруются спиральные зубья, образующая которых представляет собой удлиненную или укороченную эвольвенту.
На рис. 301 показана чер- вячная фреза для нарезания конических колес со спиральным зубом. Угол конуса фрезы при- нимается постоянным и равным 60э. На наружной поверхности фрезы профрезерованы прямые канавки, образующие зубья фре- зы. Профиль зубьев выполнен в форме рейки. Шаг рейки, изме- ренный по образующей, равен
нормальному шагу tn плоского колеса. Угол профиля рейки равен 20°.
В принципе по всей длине образующей должен быть один шаг tn = m
и одна толщина зуба рейки, равная ; но практически делают нерав- номерную толщину зуба, а именно: у переднего конца фрезы толщину зуба берут больше + 0,01, на длине 1/3 рабочей части фрезы от
переднего конца толщину берут равной ' ; далее толщину равномерно
увеличивают к заднему концу до ' + 0,102 т. Такая фреза в сере- дине будет фрезеровать более толстые зубья колеса, чем у краев.
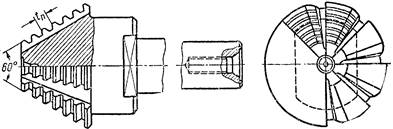
Рис. 301. Червячная фреза для конических колес
Создается некоторая бочкообразность зубьев нарезаемого коничес- кого колеса, что обеспечивает пятно контакта в середине колеса и ком- пенсирует до известной степени ошибки установки колес; этим облег- чается монтаж колес. Зубья фрезы делают затылованиыми с двойным затылком, так как профиль зубьев фрезы обычно шлифуется.
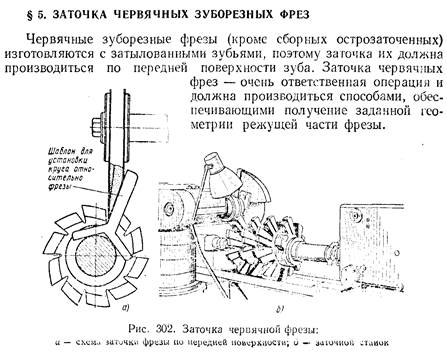
358
359
На рис. 302, а показана принципиальная схема заточки. Заточка должна производиться обязательно конической стороной тарельча- того круга, так как при заточке плоской стороной круга получается «развал» канавки. Если форма круга коническая, то касание круга с передней винтовой поверхностью происходит по линии и канавка фрезы получается по винтовой поверхности без развала.
Поскольку передняя поверхность зуба фрезы является винтовой с определенным шагом SK, то при заточке должно быть обеспечено относительное перемещение круга по этой винтовой поверхности с тем же шагом SK.
§ 6. ДОЛБЯКИ
Долбяк представляет собой режущий инструмент, выполненный в виде зубчатого колеса, имеющего режущие кромки. Долбяки раз- деляются на долбяки для прямозубых колес и долбяки для косо- зубых и шевронных колес.
По конструкции долбяки делятся на дисковые (рис. 303, а); хвос- товые (рис. 303,6); чашечные (рис. 303, в); втулочные (рис. 303, г); сборные с привернутыми зубьями (рис. 303, д) и комбинированные.
На рис. 304 показан дисковый долбяк для прямозубых колес, его основные элементы.
Долбяк имеет внешнюю 1 и внутреннюю 2 опорные плоскости, переднюю поверхность 3, скос или фаску 4, режущую часть с зубьями 5, отверстие для крепления долбяка 6, хвостовик (только у хвостового долбяка) (см. рис. 303), крепежную резьбу (только у втулочного долбяка), шейку долбяка (только у хвостовых и втулочных долбяков).
К элементам долбяка, которые определяются расчетом, относятся: т — модуль; д — угол зацепления (на делительной окружности долбяка); z — число зубьев долбяка; — расстояние до расчетного сечедия; а b — задний угол на вершинах зубьев; d — диаметр отвер- стия; b — ширина ступицы; — передний угол.
Долбяк представляет собой зубчатое колесо, но в отличие от послед- него он имеет задний угол а b, и поэтому диаметры долбяка в сечениях на различном расстоянии от торца различны (рис. 304).
Размеры долбяка в расчетном (теоретическом) сечении //—//; Dt — диаметр делительной окружности; D — диаметр окружности выступов; Dt — диаметр окружности впадин; Sd — толщина зуба по дуге делительной окружности. Размеры несточенпого (нового) долбяка в переднем торце (сечение /—/) обозначаются так же, с добав- лением к De штриха. Например, диаметр окружности выступов обоз- начается D ' e, и т. д.
В любом сечении профиль зуба эвольвентного долбяка должен быть очерчен по эвольвенте. Для расчета долбяка принимается опре- деленное сечение //—//, отстоящее от торца на расстоянии а. В этом сечении элементы долбяка в точности соответствуют элементам зуба колеса. Но долбяк по мере затупления его кромок необходимо пере-
360
тачивать по передней поверхности, а эвольвентный профиль не должен изменяться в Любом его (долбяка) сечении. Неизменности эвольвент- ного профиля долбяка можно достичь только тогда, когда боковые поверхности зубьев долбяка будут представлять собой винтовые эволь- вентные поверхности. Если в сечеиии II — I I долбяк соответствует колесу и эвольвента профиля зуба его образована от определенной основной окружности D 0, то переточенный долбяк в сечении III — I II должен также иметь эвольвентный профиль зуба, причем во избежание искажений эвольвента должна быть образована от той же основной окружности D 0.
Чтобы выдержать это условие, зуб в сечении 111— I II должен быть тоньше зуба в сечении II — I I.
В сечении II — I I шаг по делительной окружности долбяка равен шагу обрабатываемого зубчатого колеса, т. е. t = т. Диаметр D 0 основной окружности эвольвенты может быть рассчитан по формуле
D0 — Dt cos ад,
где D0 — диаметр основной окружности долбяка;
Dt — диаметр начальной (делительной) окружности долбяка;
ад — угол зацепления долбяка (равен углу зацепления колеса). Толщина зуба Sd, измеренная по дуге делительной окружности, в сечении //—// будет такая же, как и у зубчатого колеса:

Сечение /—/ отстоит от сечения II — I I на величину а, и благо- даря наличию заднего угла b долбяк приобретает коническую форму. Это равносильно тому, что в сечении /—/ исходный контур образую- щей рейки смещен на величину х, т. е. в сечении /—/ колесо будет корригированным.
Величина смещения х определяется по формуле

Если построить прямоугольный треугольник ABC (см. рис. 304), в котором гипотенуза ВС параллельна задней поверхности' долбяка, а катет АВ — х, катет АС = а, то можно определить (пренебрегая при этом наличием угла — 5°) величину а:

На рис. 304 показана развертка сечения зуба долбяка по дели- тельному цилиндру. Определим толщину S ' d долбяка по дуге дели- тельной окружности, измеренную в плоскости передней поверхности (сечение /—7):

но
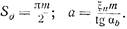
362
Угол av бокового зазора можно определить, зная задний уголаа, по вершинам зубьев долбяка и угол зацепления au по формуле
tg x = tg b tg0.
Подставив, получим

или окончательно
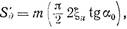
где u — коэффициент смещения; т — модуль.
Диаметр делительной окружности Dt долбяка необходимо делать возможно меньшим, так как чем меньше этот диаметр, тем меньше вылет режущих кромок относительно осы штосселя, тем более жестко и устойчиво будет закреплен долбяк.
Получили распространение следующие номинальные размеры дели- тельного диаметра, положенные в основу ГОСТа 9323—60 для чис- товых зуборезных долбяков: 25, 38, 50, 75, 100, 125, 160 и 200 мм. Существуют долбяки и с большим делительным диаметром, но для применения таких долбяков необходимы крупные станки.
Если, например, выбирается долбяк с номинальным делитель- ным диаметром 75 мм и необходимо нарезать колесо с модулем, рав- ным 2, то, безусловно, придется пересчитать делительный диаметр и принять долбяк с делительным диаметром, равным Dt = m z = = 2 ·38 =-76 мм, и с числом зубьев, равным,38.
Наметив делительный диаметр р долбяка, определим расстояние а от передней плоскости долбяка до исходного сечения. Поскольку долбяк можно рассматривать в исходном сечении как корригирован- ное зубчатое колесо, расстояние а определим по формуле

где а b — задний угол на вершине долбяка; принимается обычно 6° при 20°-ном зацеплении.
По исследованиям д-ра техн. наук В. М. Матюшина, задний угол а b следует увеличить до 9°, а передний угол увеличить до 12—17°, тогда стойкость долбяков возрастает.
Максимальный коэффициент смещения можно определить, зная минимальную допустимую толщину S ' e зуба долбяка на окружности выступов (см. рис. 304).
Если толщина зуба на окружности выступов будет меньше допус- тимой величины, то долбяк быстро притупится, так как зуб будет слишком тонкий. Поэтому стараются выбирать такой коэффициент смещения u, который бы давал возможность получить еще доста- точную толщину зуба S ' e на окружности выступов в сечении I — I.
363
По данным МИЗа, допустимые минимальные значения толщины зуба S ' e следующие:
| Толщину S ' e зуба по окружности выступов можно определить по формуле [122]

где е — угол давления эвольвенты у вершины зуба.
Задавшись допустимой величиной толщины вершины зуба в сече- нии //, можно определить по вышеприведенной формуле значение максимально допустимого коэффициента смещения umax
Определив максимальный коэффициент смещения, можно опре- делить расстояние а по приведенной выше формуле.
Если смещение umax очень большое, появляется опасность подре- зания долбяков зубьев колеса. В зависимости от числа зубьев нарезаемого колеса подрезание появляется при различных значе- ниях umax
На графике (рис. 305) приведены кривые, по которым можно опре- делить, будет ли иметь место подрезание при соответствующем коэф- фициенте umax смещения исходного контура. Например, для числа зубьев долбяка zu = 19 и коэффициента смещения исходного контура x umax = 0,158 находим zr = 65. Это значение числа zr зубьев будет максимальным числом зубьев колеса, которое еще может быть обра- ботано данным долбяком. Если обрабатывать данным долбяком колесо с числом зубьев больше 65, то у колеса будет происходить подрезание. Отсюда можно сделать вывод, что долбяк не дает возможности про- изводить обработку колеса с любым числом зубьев и имеются некоторые пределы использования долбяка для определенного числа зубьев.
Для вычерчивания долбяка необходимо определить еще ряд кон- структивных элементов. К ним относятся диаметр отверстия d, глу- бина выточки t, общая толщина долбяка В. Эти элементы следует брать по ГОСТу 9323—60.
В рабочем чертеже долбяка, кроме рассчитанных нами элементов, должны быть приведены элементы, по которым производится контро- лирование долбяка.
Толщина зуба долбяка в торцовом сечении по делительной окружности обозначена на рис. 304 через S ' d; она определяется
364
по формуле, приведенной на стр. 373. Эта толщина зуба долбяка должна быть проставлена в чертеже долбяка (для кон- троля зуба при изготовлении долбяка). ?н
Диаметр De окружности выступов в се- чении I — I (см. рис. 304) можно опреде- лить по формуле
D 'e = D, + 2h' + 2C + 2x,
где h ' — высота головки зуба колеса (в расчетном сечении); С — радиальный зазор (в расчетном
сечении); х — смещение исходного контура. Высоту h 'перед зуба (в сечении /—/) можно определить так:
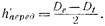
Для обработки косозубых колес при- меняются косозубые долбяки с углом на- клона зубьев = 15 и 23° (ГОСТ 9323—60).
Долбяк для косозубых колес (рис. 306), аналогично долбяку для колес с прямыми зубьями, имеет передний и задний углы.
Существует две конструкции долбяков для косозубых колес, которые отличают- ся формой зуба (рис. 307). У долбяков I типа для улучшения условий резания делается заточка переднего угла с правой стороны и некоторое притупление—с ле- вой стороны.
Долбяк II типа имеет заточку в пло- скости, нормальной к винтовой линии производящей поверхности. Это нормаль- ное сечение (у такого долбяка) назы- вается исходным нормальным сечением.
Рис. 305. Графики определения минимального
числа зубьев колес, снободпых от подрезания при
определенном значении (по Полоцкому [122])
Передняя поверхность зуба долбяка в данном случае затачивает- ся отдельно у каждого зуба, и углы резания делаются на обеих сторонах зуба одинаковые. Если колесо, для которого рассчиты-
365
вается долбяк, имеет определенный модуль тп в нормальном се- чении, то необходимо этот модуль пересчитать на модуль тТ
в торцовом сечении по формуле
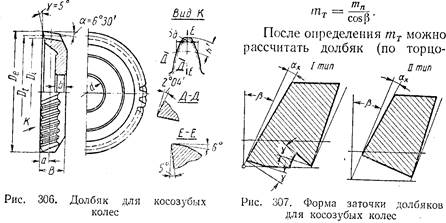
вому модулю) по тем же формулам, которые были приведены для прямозубого долбяка.
Заточка зубьев. Долбяк затачивается по передней по- верхности. Схема установки долбяка по отношению к шлифо-
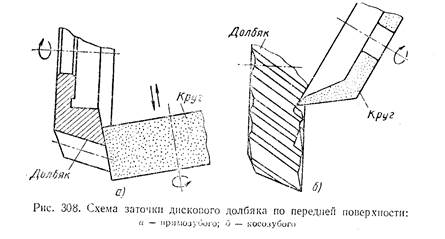
валыюму кругу показана на рис. 308, а. Заточка производится на универсальном круглошлифовальпом или на плоскошлифоваль- J1UM станке с круглым патроном и горизонтальной осью вращения патрона. Для получения достаточно чистой передней поверхности долбяка шлифовальный круг должен, кроме вращения вокруг
365
своей оси, иметь также возвратно-поступательное движение в на- правлении, показанном стрелками. Передний угол принимается равным 5° у чистовых и 10° у черновых долбяков. Долбяки для шевронных и косозубых колес затачиваются иначе — так, чтобы каждый зуб долбяка имел одинаковый угол заострения на обеих сторонах, например, как показано на рис. 308, б.
§ 7. РЕЗЦЫ И РЕЗЦОВЫЕ ГОЛОВКИ ДЛЯ НАРЕЗАНИЯ КОНИЧЕСКИХ КОЛЕС
Для обработки конических колес применяются зубострогаль- ные резцы (для прямозубых конических колес) и резцовые голов- ки (для конических колес с кри- волинейными зубьями).
Зубострогальные резцы. На рис. 309 показана схема обра- ботки прямозубого конического колеса строгальными резцами на специальном зубострогаль- ном станке. Зуб нарезаемого колеса обрабатывается двумя резцами. Люлька, в которой помещаются резцы, представляет собой некоторую часть плоского (воображаемого) колеса, а по-
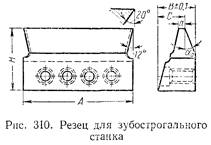
парно движущиеся резцы представляют собой как бы впадину зуба этого колеса. Резцы двигаются возвратно поступательно (по стрелке v), и каждый из них обрабатывает одну сторону зуба колеса; движение резцов совершается попеременно. Если один из резцов движется по направлению к точке A, другой резец в это время движется в обратном направлении. Плоское колесо и обрабатываемая заго- товка связаны между собой кинематически и обкатываются без сколь- жения по начальной плоскости и начальному конусу. В результате этого обкаточного движения прямолинейная кромка резца обраба- тывает боковую поверхность зуба колеса.
367
На рис. 310 показан зубострогальный резец. Этот резец снаб- жен отверстиями с резьбой для крепления его на держателе зубосфогального станка. Рабочая часть резца представляет со- бой плоскость, срезанную под углом 0 При работе, для того чтобы создать задний угол, резец устанавливается па специаль- ной откидной державке (см. рис. 309), которая для устранения тре- ния откидывается при обратном ходе. Передний угол па резце по- лучается благодаря заточке перед- ней поверхности под углом 12 и 20°. В зависимости от размера зубо- строгального станка применяются различные размеры резцов (А, В, С, Н и др.), которые опреде- ляются по ГОСТу 5392—64..
Резцовые головки применяются для нарезания конических зубча- тых колес с криволинейными зубья- ми на специальных зуборезных станках. На рис. 311 показана схема работы резцовой головки.
Резцовая головка представляет собой как бы отдельный кри- волинейный зуб плоского коле- са. Это колесо обкатывается но начальному конусу нарезаемого колеса, в то же время резцовая головка вращается вокруг своей оси по стрелке v и резцы выре- зают материал из впадин колеса. Резцовая головка выполняется в виде диска, в который вставлены по периферии отдельные резцы. Половина этих резцов обрабатывает профиль одной сто- роны зуба, другая половина — профиль другой стороны зуба колеса.
§ 8. ШЕВЕРЫ
Шеверами называют инструменты, предназначенные для окон- чательной обработки боковых сторон зуба колес путем срезания очень тонких стружек. Этот процесс напоминает скобление или шабрение. Шевингование производится на специальных станках.
Шевер представляет собой закаленное зубчатое колесо (дисковый шевер; рис. 312, а), пли закаленную зубчатую рейку (шевер-рейка; рис. 312, б), или, наконец, закаленный червяк с насечкой (червячный шевер; рис. 312, в).
Дисковый шевер, представляющий собой корригированное зуб- чатое колесо, зубья которого снабжены канавками, образующими режущие кромки, вращается вокруг оси 00 (рис. 313), накло-
ненной по отношению к оси заготовки на некоторый угол . При сближении оси шевера, имеющего косые зубья, и оси загоювки,
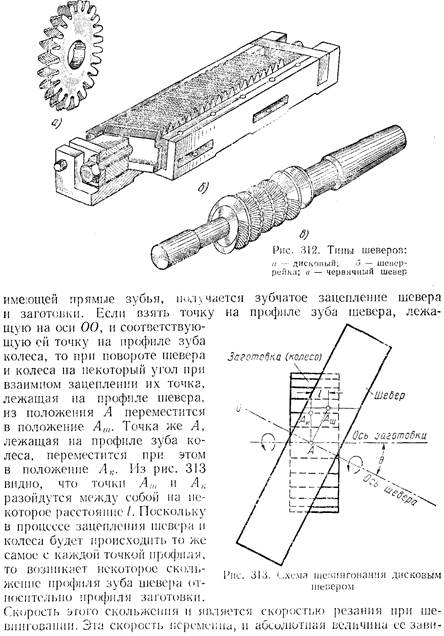
368
369
сит от угла скрещивания осей заготовки и шевера. Обычно этот угол скрещивания осей выбирается в пределах 10—15°. Для того чтобы получить относительное скольжение при обработке прямо- зубых колес, необходимо делать шевер с косыми зубьями, а при обработке косозубых колес — шевер с прямыми зубьями.
На рис. 314 показан чертеж дискового шеверa для прямозу- бых колес с углом зацепления 20°.
Раздел РЕЗЬБОНАРЕЗАНИЕ
VIII

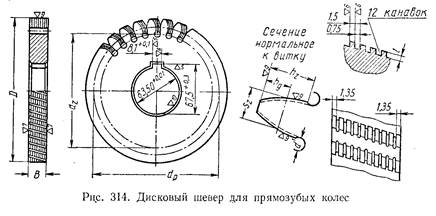
Дисковые шеверы благодаря их небольшим габаритам полу- чили более широкое распространение, чем остальные виды шеве- ров. Шеверы изготовляются для шевингования колес с модулем до 8 (и выше в отдельных случаях).
Аналогично происходит работа шевера-рейки, только зацепле- ние в этом случае обеспечивается не между двумя колесами, а между рейкой и колесом. Однако шевер-рейка из-за сложности изготовления не находит применения.
Червячный шевер, представляющий собой червяк с мелкими насеченными зубьями, работае-т как червячная фреза, только с той разницей, что стружка при этом из-за большого числа часто расположенных зубьев может быть очень мелкой, и поэтому полу- чается чистая поверхность обрабатываемого червячного колеса.

|