Резьбонарезные самооткрывающиеся головки с круглыми гребенками
изготовляются по ГОСТу 3307 — 61 трех типов:
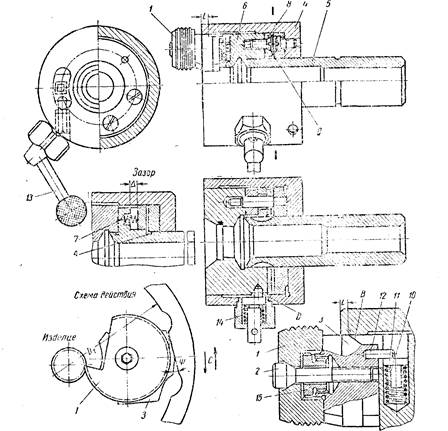
Рис. 339. Резьбонарезная невращающаяся головка с круглыми гребенками
1) невращающиеся — для нарезания резьб на револьверных и то- карных станках;
2) вращающиеся — для нарезания резьб на автоматах, сверлиль- ных и болторезных станках;
3) невращающиеся — к автоматам типа 1124, 1136.
В зависимости от размеров нарезаемых резьб головки обознача- ются номерами 1К, 2К, ЗК и 4К и т. д.
У резьбонарезной головки с круглыми гребенками (рис. 339) певрлщающегося типа четыре круглые гребенки / с кольцевой резьбой, укрепленные винтами 2на
399
специальных кулачках 3, сближаются к центру или разводятся посредством нажим- ного кольца 4. Поступательное движение кольца вдоль оси головки дает возмож- ность благодаря уступу кулачков 3 (рис. 339, внизу слева) сводить их к центру и раз- водить в конце нарезания резьбы. Поворот кольца (показан на схеме стрелками С) позволяет точно регулировать диаметр нарезаемого болта площадками, скошенными под углом i! f.
На рис. 339 головка изображена в закрытом положении, плашки сведены, и головка движется вместе с суппортом. Как только суппорт остановится, вместе с ним остановится и хвостовик 5. Плашкодержатель 6 при этом продолжает движе- ние вперед (на величину зазора А), сжимая пружины 7 кольцом 8, привернутым ■ интами 9; нажимное кольцо 4 остановится, так как упирается в выступ А на хво- стовике; при этом происходит «вытягивание» плашкодержателя из кольца 4. Как только плашкодержатель вместе с кулачками выйдет на величину /, кулачки 3, раздвигаясь под действием пружин 10, нажимающих на штифты // и шпильки 12, своими скосами В отбросят нажимное кольцо назад (вправо), и головка раскрывается. Для закрытия головки необходимо рукоятку 13, на которую нажимает пружина 14, повернуть и кольцо 4 возвратить в первоначальное положение. Кольцо 4 заставит кулачки, скользя по скосам В, сойтись к центру. Режущие гребенки / установлены на кулачках 3 (см. рис. 339, внизу слева). Для того чтобы зафиксировать определенное положение гребенки на кулачке, она садится на цилиндрический выступ (пуговку) кулачка. Между кулачком и гребенкой устанавливается двухвенцовая звездочка 15, имеющая зубья на двух разных диаметрах. Одним зубчатым венцом звездочка вхо- дит в кулачок, а другим — в гребенку. Гребенка закрепляется на кулачке винтом 2. Звездочка имеет неодинаковое число зубьев на обоих венцах; венец, закладываемый в кулачок, имеет число зубьев на один меньше, чем венец, закладываемый в гребенку.
Если повернуть звездочку относительно кулачка на один зуб вправо, а относи- тельно плашки —- на один зуб влево, то общий поворот М плашки относительно кулачка (для головки 2К) определится так:

Размеры кулачков и гребенок для резьб нельзя выбирать произвольно, так как каждая резьба имеет определенный диаметр и шаг, а следовательно, и угол подъема со.
Длина гребенки выбирается с такум расчетом, чтобы длины калибрующей и за- борной частей вместе составляли не менее семи-восьми шагов резьбы. Угол ср за- борной части гребенки принимается равным 20°.
Задний угол а обеспечивается расположением центра гребенки выше центра заготовки на величину q (для головок /К и 2К q — I.-*J мм). На рис. 339 показано расположение гребенки относительно заготовки в сечении / — /, проходящем через
400
первый калибрующий зуб плашки. Задний угол а в этом сечении может быть опреде лен по формуле 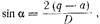
где а - снос вершины режущей части гребенки.
Гребенки для лучшего отвода стружки и обеспечения работы самозатягиванием имеют наклон передней поверхности к оси под углом . При установке гребенки на кулачок к углу прибавляется угол со и получается угол = + Значе- ние углов и и сноса а приведены в табл. 34.
Заточка гребенок мо- жет производиться только в со- бранном виде. Для установки ку- лачков вместе с гребенками на заточной станок предусмотрено спе- циальное приспособление, пока- занное на рис. 340.
Необходимо, чтобы углы и и снос а были одинаковы у всех гре- бенок. Для проверки правильно- сти заточки гребенок применяется приспособление (рис. 341), которое имеет два микрометра: микрометр А упирается в наружный диаметр гребенки, а микрометр Б — в пе- реднюю поверхность. Промер должен производиться на уровне пер- вого витка калибрующей части.
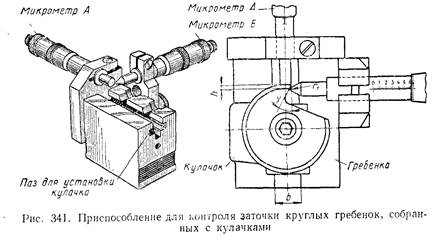
Кроме описанных, получили распространение головки (называ- емые патронами) с круглыми гребенками для нарезания наружных конических резьб на трубах большого диаметра.
401
РЕЗЬБОВЫЕ ФРЕЗЫ
Фрезы разделяются на два основных типа: 1) дисковые или однони- точные и 2) цилиндрические гребенчатые (многониточные). Дисковые резьбовые фрезы применяют при нарезании длинных резьб (в основ- ном трапецеидального профиля) на различных ходовых винтах и чер- вяках. Фрезерование применяется только как предварительный ме- тод обработки резьб ходовых винтов. Чистовое нерезание резьбы обыч- но производится резцом или профильным шлифовальным кругом.
Применение фрез с симметричным (рис. 342, а) и с несимметричным (рис. 342, б) профилем вызывается конструкцией резьбофрезерного
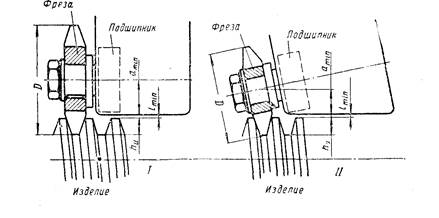
а) 6)
Рис. 342. Схема расчета диаметра фрезы:
а — ось шпинделя станка параллельна оси детали; б — ось шпинделя станка наклонена к оси детали
станка. Диаметр фрезы с симметричным или несимметричным профи- лем определяется приближенно по формуле
D» (2hu + lmin + amin).
Как видно из рис. 343, а, у фрезы с симметричным профилем раз- мер а min вызван необходимостью размещения в шпиндельной головке подшипников шпинделя и передающего механизма. В конструкции станка для фрез с несимметричным профилем (см. рис. 342, б) благо- даря наклону шпинделя появляется возможность при тех же габаритах подшипников уменьшить ат in, а следовательно, и диаметр фрез.
Профиль фрезы должен быть криволинейный. При небольших уг- лах подъема резьбы (меньше 10') обычно делают фрезы с прямолиней- ным профилем, но с корректированным углом профиля.
Угол профиля определяется по формуле
ig -=tgcos,
где — угол подъема резьбы; — угол профиля детали.
Дисковые резьбовые фрезы для трапецеидальных резьб делаются с остроконечными зубьями.
При фрезеровании резьб небольшой длины с небольшим шагом и небольшим углом подъема резьбы применяются гребенчатые (много- ниточные) резьбовые фрезы. Процесс фрезерования резьбы происхо- дит за один оборот заготовки, причем для образования винтовой ли- нии резьбы фреза перемещается за это время вдоль оси на один шаг. Резьбовые гребенчатые фрезы изготовляются насадные и концевые. На рис. 343, а показаны насадные гребенчатые фрезы с затылованными зубьями и кольцевой резьбой. Канавки фрез делаются прямые и вин- товые с небольшим углом наклона. Фрезы с винтовыми канавками ра- ботают более плавно, но
изготовление их слож- нее. Диаметр фрезы выбирается по ГОСТу 1336—62.
Длина фрезы L ф (в стандарте не задается) зависит от длины наре- заемой резьбы детали lu:
L ф = lu + (2 ¸ 3)S,
где S — шаг резьбы в мм.
Элементы затылован- ного зуба и канавки вы- бирают исходя из тех же соображений, что и для обычных затылованных фрез (см. стр. 329).
Так как высота профиля метрической и дюймовой резьбы незначи- тельна, то можно брать канавку более широкую, чем обычно. Угол у делается в пределах 30—45°, радиус закругления г =4,5лш. Вели- чина затылования К выбирается из расчета получения заднего угла в пределах 8—12°. Размеры профиля фрезы определяются по задан- ному профилю резьбы.
Вершина резьбы на фрезе изнашивается быстрее боковых сто- рон профиля, поэтому по вершинам дается запас на износ. Но с уве- личением этого запаса уменьшается площадка б резьбы, затрудня- ется изготовление фрезы и снижается ее стойкость. Минимальную площадку б принимают равной 3/4 площадки б1 теоретического про- филя резьбы.
Для большего удобства контроля размеры профиля резьбы зада- ются от линии среднего диаметра. Размеры hv и h 2 для метрической и дюймовой резьбы приводятся в ГОСТе 1336 — 62.
Резьбовые гребенчатые фрезы применяются также и для фрезеро- вания конических резьб (рис. 343, б). Отличительными особенностя- ми конструкции таких фрез являются винтовые канавки постоянного
402
403
шага, выполненные на конической поверхности фрезы. Канавки приходится делать расширяющимися по направлению к большему диа- метру фрезы.
При нарезании резьбы фреза вращается, и за каждый оборот де- тали она перемещается на один шаг по направлению образующей ко- нуса, как показано стрелкой на рис. 343, б. Получающаяся на де- тали коническая резьба будет иметь переменный угол подъема.
§ 9. ЭЛЕМЕНТЫ РЕЖИМА РЕЗАНИЯ И МОЩНОСТЬ ПРИ ФРЕЗЕРОВАНИИ РЕЗЬБЫ
Скорость резания, допускаемая режущими свойствами гребенча- тых многониточных фрез, изготовленных из быстрорежущей стали Р18, определяется по формулам: при обработке стали марки 45 с охлаждением эмульсией

при обработке ковкого чугуна

при обработке без охлаждения конструкционных углеродистых, хромистых и хромоникелевых незакаленных сталей вихревой голов- кой с резцами из сплава Т15К.6
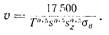
В этих формулах: Т — стойкость в мин (30—60 мин); s — шаг нарезаемой резьбы в мм; S z — подача на один резец в мм;
s в — предел прочности стали при растяжении в кГ.'мм2. Формула дана при нормативном износе h 3 = 0,7 мм. При п3 =0,4 мм подсчитанную по этой формуле скорость резания надо умножить на коэффициент 0,8, а при h 3» 1 мм — на коэффи- циент 1,3.
Подача при резьбофрезеровании определяется (по данным НИИБТН) как длина дуги по окружности заготовки за один срез (на один зуб фрезы, на один резец вихревой головки) и обозначается sz, в мм/зуб (табл. 35).
Мощность при нарезании вихревой головкой диаметром D v резьбы на заготовках из конструкционных углеродистых, хромистых и хро- мипикелевых сталей
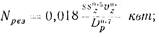
Значения подач в мм при резьбофрезеровании
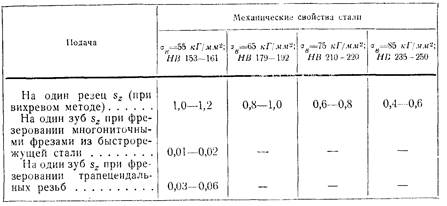
при нарезании трапецеидальной резьбы на тех же сталях

Формулы даны при износе h 3 =0,7 мм. При износе h 3 =0,4 мм поправочный коэффициент 0,83, а при износе h 3 = 1 мм коэффици- ент 1,1.

404
Раздел ПРОТЯГИВАНИЕ
IX
Принято подразделять протяжки на внутренние (предназначен- ные для обработки отверстий) и наружные (для обработки незамкну- тых поверхностей).
Протяжки могут иметь зубья режущие и уплотняющие; последние не режут, а уплотняют тонкие слои металла. Уплотняющие—выг-
Глава XXIV ПРОЦЕСС РЕЗАНИЯ ПРИ ПРОТЯГИВАНИИ
Протягиванием можно обработать сквозные отверстия любой фор- мы, прямые или винтовые канавки, наружные поверхности разнооб- разной формы, зубчатые колеса наружного и внутреннего зацепления.
Протяжка — многозубый инструмент, которому в отличие от резца придается определенное движение подачи на глубину резания; у протяжки эта подача осуществляется в самой конструкции, так как каждый последующий зуб выше предыдущего. Движение резания прямолинейное и реже — круговое (рис. 344).
Протяжка обычно закрепляется в ползуне станка и перемещается вместе с ним. При работе круглой протяжкой это перемещение осуществляется вдоль оси отверстия (рис. 344, а). Постепенно уве- личивающиеся в размерах зубья протяжки срезают слои металла, увеличивая при этом размеры отверстия. Если сила прилагается к хвостовику, то корпус протяжки.работает на растяжение (рис. 344, а). Если сила прилагается к задней части протяжки, то это уже прошивка, которая в отличие от протяжки работает на сжатие (рис. 344, б). Во избежание продольного изгиба прошивка должна быть короче протяж- ки, и ее длина обычно не превышает 15-кратного диаметра.
Несмотря на сравнительно низкие скорости резания (2—15 м/мин), применяемые при протягивании, производительность протягивания очень высокая, так как велика суммарная длина режущих кромок, работающих одновременно. Производительность при протягивании еще более повышается, если используются протяжные станки с неп- рерывным рабочим движением и автоматической загрузкой заготовок.
Вследствие высокой производительности и точности обработки (3—2-го класса точности), а также обеспечения чистоты обработан- ной поверхности (5—9-го класса) протяжки получают все большее распространение в машиностроении и металлообработке. Однако протяжки — дорогой инструмент, и их применение оправдывается в основном только при крупносерийном и массовом производстве.
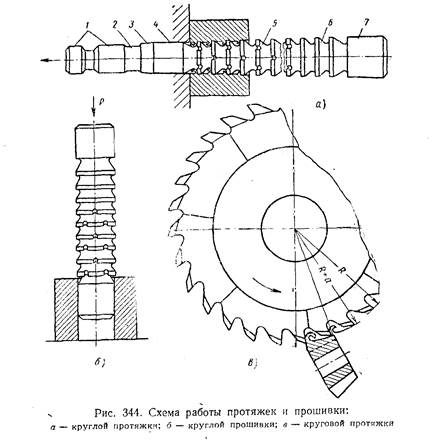
лаживающие протяжки могут увеличивать отверстия на очень малую величину.
На рис. 345 показаны основные типы внутренних протяжек: про- тяжки для круглых отверстий, например круглые режущие (рис. 345, а); сборные (рис. 345, б); с винтовым зубом (рис. 345, в); выглаживающие (рис. 345, г); шлицевые протяжки — прямошлицевые (рис. 345, д) и спиралыю-шлицевые (рис. 345, е?); фасонные различного профиля, например эвольвентные (рис. 345, ж) или остроуголыю-шлицевые (рис. 345, з); комбинированные, например круглые и шлицевые в одной протяжке (рис. 345, и) и т. д.
-106
407
Наружные протяжки подразделяются по типу обрабатываемых поверхностей на плоские, круглые и фасонные протяжки.
Хотя протяжки работают с небольшими скоростями резания, но, как показала практика, целесообразно их изготовлять из быстроре- жущих сталей. В отдельных случаях можно применять сталь ХВГ,
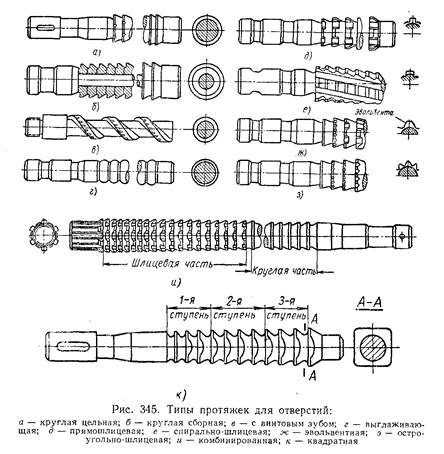
которая мало деформируется при термической обработке, что очень важно, когда протяжки имеют значительную длину.
В последнее время протяжки оснащают твердым сплавом (ВК8, ВК6М), так как их стойкость значительно повышается по сравнению с быстрорежущими протяжками, например, при обработке чугуна. Наружные и круглые протяжки диаметром свыше 80 мм часто изго- товляются сборными.
Каждая внутренняя протяжка имеет ряд основных частей; напри- мер, круглая внутренняя протяжка (рис. 344, а) имеет: 1 —хвостовик
408
(для закрепления протяжки в патрон протяжного станка); 2 —шейку; 3—переходной конус; 4— направляющую часть (для направления протяжки в начале ее работы по предварительно обработанному от- верстию); 5—режущую часть протяжки, на которой расположены зубья, срезающие основной припуск; 6 —калибрующую часть, на ко- торой расположены зубья, калибрующие отверстие и обеспечивающие необходимую чистоту поверхности; 7—заднюю направляющую часть, служащую для удержания длинной протяжки от провисания и не до- пускающую перекоса детали в конце процесса протягивания (в момент выхода последнего зуба).
§ 1. ГЕОМЕТРИЧЕСКИЕ ЭЛЕМЕНТЫ ЗУБА ПРОТЯЖКИ
Задний угол зубьев протяжки в сечении, совпадающем с направлением резания, выбирается независимо от обрабатываемого металла; он должен обеспечивать хорошие условия резания, умень- шая трение задней поверхности об обработанную поверхность.
У калибрующих зубьев делается цилиндрическая ленточка шири- ной f = 0,05¸0,2 мм (рис. 346, зуб 3). Значения заднего угла берутся
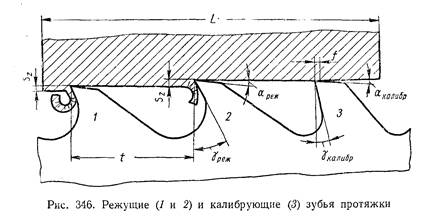
в зависимости от вида операции (черновой или чистовой) и типа про- тяжек (табл. 36).
Малое значение заднего угла у протяжек для внутреннего протяги- вания объясняется тем, что при большем значении угла заточка про- тяжки, которая проводится по передней поверхности, вызовет значи- тельное изменение размеров зубьев (протяжек) в поперечном сечении. Из-за этого же делается незначительным и задний угол на фаске у зубьев калибрующей части.
Передний угол выбирается в зависимости от обрабатывае- мого материала (табл. 37).
409
§ 2. ЭЛЕМЕНТЫ РЕЖИМА РЕЗАНИЯ ПРИ ПРОТЯГИВАНИИ
Определение режимов резания при протягивании сводится к на- значению скорости резания, так как подача sz и ширина среза b обус- ловливаются элементами конструкции протяжки.
Подачей sz или подъемом на зуб протяжки (см. рис. 346) называют разность между высотами соседних зубьев протяжки. Подачу s, обычно определяют по эмпирическим данным.
В табл. 38 (см. стр. 418) даны рекомендации по выбору подач у различных видов и конструкций протяжек.
Ширина среза b измеряется вдоль режущей кромки. У шпоночной протяжки — это ширина паза; в протяжках круглых,
шлицевых и т. д. ширина среза будет соответственно равна длине ак- тивной части режущей кромки, для круглой протяжки — длине ок- ружности, для шлицевой — суммарной ширине шлицев и т. д.
Площадь поперечного сечения /, приходящаяся на один зуб:
для шпоночной (одношлицевой) протяжки
f = szb мм 2;
для многошлицевой
f = szbn мм2;
для круглой
f = sz D MM 2 f
где sz — подача (подъем зуба) в мм; Ъ — ширина шлица в мм; п- число шлицев; D — диаметр круглой протяжки. Суммарная площадь поперечного сечения среза
F = fz мм2,
где г _ число зубьев, одновременно находящихся в работе.
Машинное время за один проход при протягивании можно опре- делить по формуле
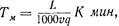
где L — длина рабочего хода протяжки в мм;
К — коэффициент, учитывающий соотношение между скоростями
рабочего и обратного хода; обычно К = 1,4¸1,5; v — скорость резания в м/мин; q — количество одновременно обрабатываемых деталей.
§ 3. ПРОЦЕСС СТРУЖКООБРАЗОВАНИЯ И СИЛЫ РЕЗАНИЯ ПРИ ПРОТЯГИВАНИИ
Во время стружкообразования при протягивании имеют место все явления процесса резания: деформации, тепловыделение, наросто- образование, трение и износ протяжки. Процесс резания при протя- гивании осуществляется часто с очень тонкими стружками, особенно при внутреннем протягивании, когда s z доходит до 0,015 мм. При об- работке сталей получается сильно деформированная сливная стружка, при обработке чугунов — стружка надлома.
При протягивании важно знать форму и размеры стружки, так как от этих данных зависит правильная работа протяжки. Впадины между зубьями должны быть таких размеров и формы, чтобы в них
411
свободно помещалась стружка. Если стружка не укладывается во впадине, происходит ее прессование, что может привести к разрыву протяжки. Часто для уменьшения ширины стружки и для более удоб- ного размещения ее в канавках на режущих зубьях делают стружко- разделительные канавки.
При протягивании сталей образуется нарост (застойная зона). Чем больше толщина среза, меньше передний угол зуба протяжки и больше радиус округления режущей кромки, тем больше нарост [123]. Нарост часто сходит под заднюю поверхность зуба протяжки и резко ухудшает чистоту обработанной поверхности.
Протягивание осуществляется с малыми подачами s z и малыми ско- ростями резания; в этом случае очень большое значение имеет приме- нение смазочно-охлаждающих жидкостей. При протягивании сталей применяют в основном сульфофрезол (8—15 л/мин при внутреннем протягивании и 30—40 л/мин при наружном), при протягивании нержавеющих сталей 10%-ную эмульсию.
Протягивание серого и ковкого чугуна производится обычно без охлаждения. Протягивание алюминия рекомендуется со специальной смесью масла и керосина (1:1).
Сила резания Pz зависит от физико-механических свойств обрабатываемого материала, геометрических параметров зубьев про- тяжки, подачи sz, числа и формы одновременно находящихся в работе зубьев.
Сила резания при протягивании определяется по формуле
P z = F b кГ,
где F — сила резания, отнесенная к 1 мм длины режущей кромки, в кГ/мм; b — суммарная длина режущих кромок всех одновременно ра- ботающих зубьев в мм. Значение F зависит от величины подачи на зуб s z и обрабатывае- мого материала и приводится в соответствующий карте режимов реза- ния [124].
Суммарная длина b режущих кромок определяется по формулам: для цилиндрических отверстий

для шлицевых отверстий и шпоночных пазов

где d — наибольший диаметр зубьев в мм;
zc — число зубьев в секции (для протяжек, работающих с обы- чной, не прогрессивной схемой резания, zc. — 1); zi - — наибольшее число одновременно работающих зубьев; b п — ширина протягиваемой поверхности в мм; п — число шлицев или шпонок.
§ 4. ИЗНОС, СТОЙКОСТЬ ПРОТЯЖЕК И СКОРОСТЬ РЕЗАНИЯ
В общем случае зуб протяжки изнашивается по задней поверхности, по уголкам, по ленточке (у калибрующих зубьев) и по передней поверх- ности. Наиболее характерным и чаще всего лимитирующим износом является износ по задней поверхности h 3 (рис. 347).
Учитывая, что протяжка в основном применяется как чистовой инструмент (исключение составляют наружные протяжки),' за кри- терий износа принимаем технологический износ — ухудшение чисто- ты поверхности, искажение геометрии или изменение размеров про- тягиваемых поверхностей.
Максимально допустимый износ по задней поверхности зуба и уголкам стружкоразделительных канавок принимается (при обработке
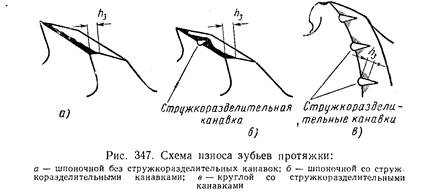
стали и чугуна) в пределах: для цилиндрических протяжек до 0,2 мм, для шлицевых и шпоночных до 0,3 мм.
Средние периоды стойкости для быстрорежущих протяжек из ста- лей Р9, Р 18 рекомендуются следующие: а) для протяжек шпоноч- ных (с шириной паза 10 мм) 120 мин при обработке стали и 180 мин при обработке чугуна; б) для шлицевых протяжек диаметром 32—52 мм 420 при обработке стали и 600 мин при обработке чугуна; в) для цилинд- рических протяжек (диаметром 30 мм) 180 мин при обработке стали и 270 мин при обработке чугуна.
Средние стойкости протяжек выражаются также в суммарной длине протянутых поверхностей в метрах.
Скорость резания при протягивании лимитируется не красностой- костью инструмента, а условиями получения высококачественной обработанной поверхности. Увеличение скорости резания при протя- гивании не дает заметного увеличения производительности труда, так как вспомогательное время в операции протягивания имеет зна- чительный удельный вес по отношению к машинному времени.
412
413
Формула скорости резания при протягивании имеет следую- щий вид:
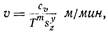
где с v — коэффициент, характеризующий условия обработки;
Т — стойкость протяжки в мин; m и у — показатели степени при стойкости и подаче, зависящие от обрабатываемого материала, материала протяжек и других условий.
Например, при протягивании цилиндрического отверстия в заго- товке из стали марки 35 (НВ 197—269) при условии получения 2-го класса точности и чистоты обработанной поверхности Ñ6 для быстро- режущей протяжки v = 6 м/мин. Для других условий протягивания см. режимы резания [124].
Мощность при протягивании
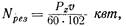
где Pz — сила резания в кГ;
v — скорость резания в м/мин. Мощность электродвигателя протяжного станка должна быть не меньше, чем требуется по формуле

где — к. п. д. станка, равный 0,75—0,9.
Тяговое усилие станка Q (должно быть несколько больше или, в крайнем случае, равно силе резания Pz) можно подсчитать по формуле
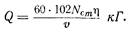
|