Глава скорость резания, допускаемая
VII РЕЖУЩИМИ СВОЙСТВАМИ РЕЗЦОВ
Как было отмечено выше (стр. 36), увеличение скорости резания приводит к уменьшению машинного времени Тм.
Однако скорость резания нельзя назначать без учета конкрет- ных условий обработки, так как при ее увеличении резко возра- стет интенсивность износа резца (рис. 104), т. е. снизится его
стойкость — машинное время работы инструментом от пере- точки до переточки (или до определенной величины износа). Это вызовет частую переточку резца, а следовательно, и затрату тру- да заточника, затрату времени на снятие и установку резца и пе- ревод в отходы (при заточке) определенного количества материала,
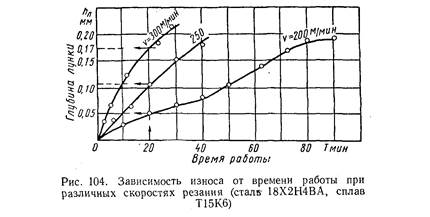
идущего на изготовление режущей части инструмента. Таким образом, износ инструмента (или его стойкость) оказывает влияние на произ- водительность и себестоимость обработки.
Чем большую скорость резания допускает резец при одной и той же стойкости, тем выше его режущие свойства, тем он более производителен.
ВЛИЯНИЕ РАЗЛИЧНЫХ ФАКТОРОВ
НА СКОРОСТЬ РЕЗАНИЯ, ДОПУСКАЕМУЮ РЕЗЦОМ
На скорость резания, допускаемую резцом, влияют следующие факторы:
стойкость режущего инструмента; физико-механические свойства обрабатываемого металла; материал режущей части инструмента; подача и глубина резания; геометрические элементы режущей части резца; размеры сечения державки резца; смазывающе-охлаждающая жидкость; максимально допустимая величина износа резца; вид обработки.
Зависимость между скоростью резания и стойкостью. Экспе- риментально установлено, что между скоростью резания и ^стой- костью режущего инструмента из инструментальных сталей су- ществует зависимость: чем выше скорость резания, тем меньше стойкость резца (рис. 105, кривые / и 2). Это вполне объяснимо описанным выше влиянием скорости резания на тепловыделение ,и износ.
110
т
По отношению к инструменту, оснащенному твердым сплавом, зависимость между скоростью резания и стойкостью более сложная. Из представленной (для некоторых условий резания незакаленной стали) на рис. 105 зависимости (кривая 3) следует, что при увеличении скорости резания стойкость твердосплавного резца сначала умень- шается, затем увеличивается и вновь уменьшается; при этом чем больше твердость обрабатываемого металла, тем меньше величина критических скоростей, соответствующих точкам перегиба (см. зави- симости на рис. 105 и 106). Такая зависимость между скоростью резания и стой- костью для твердосплавных резцов объясняется тем, что

при малых v вследствие низкой температуры резания износ протекает медленно. По мере увеличения v температура на по- верхностях соприкосновения резца с заготовкой и стружкой увеличивается, что содействует слипанию (свариванию) в местах контакта и соответственно повышению интенсивности износа и снижению стойкости резца. При дальнейшем увеличении v (на- чиная с v = 10 м/мин, рис. 106) повышение температуры содей- ствует размягчению (и даже микрооплавлению) поверхностей струж- ки и заготовки, что уменьшает слипание, облегчает относительное скольжение и снижает интенсивность износа (повышает стойкость); этому содействует также повышение ударной вязкости твердого сплава (особенно в интервале температур 600—800° С) и уменьшение сил, действующих на резец. При дальнейшем же увеличении скорости (v» 20 м/мин) и соответственно температуры резания резко сни- жаются твердость и прочность твердого сплава, что (при все возра- стающем пути трения за один и тот же промежуток времени) приводит к повышению интенсивности износа резца и соответствующему сни- жению стойкости.
При одинаковой стойкости резцов, например 50 мин (рис. 105), выгоднее (производительнее) работать со скоростью v = 160, чем с v — 45 м/мин, а потому зоной рационального использования твер- дого сплава следует считать участок, расположенный вправо от точки перегиба максимальной стойкости. Поэтому зависимость между вели- чинами v и Т будем рассматривать на второй ниспадающей ветви, которая в простых координатах выражается в виде кривой (рис. 107, а), а в логарифмических координатах — в виде прямой линии (рис. 107, б).
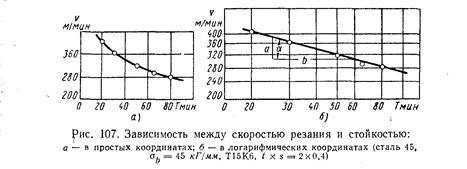
Математически эта зависимость выражается так:

где Т — стойкость в мЯн, соответствующая данной скорости реза- ния V, '. " m — показатель относительной стойкости, характеризующий влия-
ние стойкости на скорость резания; А — постоянная величина, зависящая от условий обработки (материала резца и заготовки, охлаждения, сечения среза
и ДР-)- >, Логарифмируя первое выражение, получим

г. т. е. в логарифмических координатах зависимость между скоростью
I резания и стойкостью выражается уравнением прямой линии, тангенс
■' угла наклона которой и есть показатель относительной стойкости
(рис. 107, б) 
Показатель относительной стойкости характеризует степень изменения скорости резания с изменением стойкости резца. Он зависит от обрабатываемого металла, 1. материала режущей части резца, толщины среза, вида и условий обработки. , Для проходных, подрезных и расточных резцов из быстрорежущей стали тср =
=0,125 при обработке с охлаждением стали, стального литья и ковкого чугуна; для резцов, оснащенных пластинками твердых сплавов, т= 0,125¸0,3 (тс„ = = 0,2).
Зная стойкость 7\ при скорости vt, по указанной выше зависимости можно определить стойкость Ti при скорости и2 (при прочих одинаковых условиях резания) или скорость уа при стойкости Тг. Из уравнения vTm = А = const следует, что
| Так как показатель относительной стойкости различен при низких и высоких скоростях резания, то полученная зависимость может дать неправильные резуль- таты в случае пересчета скорости резания с малых стойкостей на очень высокие (например, на Т > 500 мин).
В общем случае стойкость и соответствующая ей скорость резания должны быть такими, чтобы при достаточно хорошем качестве обра- ботанной поверхности была высокая производительность труда и низкая себестоимость обработки.
В зависимости от условий обработки, конструкции режущего инструмента и станка, общего технического уровня производства и технико-экономических условий эксплуатации станка и инструмента значения стойкости и соответствующей ей скорости резания должны быть различными. В частности, при многоинструментной обработке (автоматы и полуавтоматы), когда замена затупленного инструмента и его подналадка связаны с большой затратой времени и труда, стойкость инструмента должна быть выше, чем для одноинструментных, более простых работ.
Для обычных токарных резцов, оснащенных твердым спла- вом, рекомендуется Т = 60 ¸90 мин [67]. Если при Т = 60 мин допускаемую твердосплавным резцом скорость резания принять за единицу, то для другого значения стойкости эта скорость в количест- венном отношении выразится следующими поправочными коэффи- циентами К r

Приведенная выше зависимость может быть записана так:

Влияние обрабатываемого материала. Большое влияние на ско- рость резания, допускаемую резцом, оказывают физико-механические свойства обрабатываемого металла. Это влияние предопределяется в основном тепловыделением в процессе резания и распределением тепла между стружкой, заготовкой, резцом и окружающей средой.
На скорость резания оказывают влияние химический состав стали, ее термическая обработка и характер структуры, получаемой при
термической обработке [63]. Так, при уменьшении содержания угле- рода в конструкционной углеродистой стали допускаемая скорость резания повышается, а при введении легирующих металлов (Сг, Мп и др.) понижается; для стали 40Х наибольшая допустимая скорость резания будет при отжиге T= 900° С, для стали 40 — при нормали- зации с T= 900 ¸950° С, а для быстрорежущих сталей — при изотермическом отжиге 1. Наибольшая допустимая скорость резания наблюдается при зернистом перлите, когда цементит имеет форму мелких шарообразных зерен, равномерно распределенных в феррите, а из структур наибольшую скорость резания допускает феррит, затем (в порядке уменьшения допустимой скорости резания) перлит (точеч- ный, зернистый, пластинчатый, сорбитообразный) сорбит и троосто- сорбит.
Из практики известно, что мелкозернистые стали обрабатывать легче, чем крупнозернистые, и что небольшим введением некоторых элементов (например, до 0,1% S и до 0,2—0,25% РЬ [68]) можно повысить обрабатываемость стали, не изменяя почти ее механических свойств.
Скорость резания, с которой можно обрабатывать данный металл при определенной стойкости резца, является основной характеристи- кой обрабатываемости2 металлов. Чем выше скорость, тем лучше обрабатываемость данного металла по сравнению с тем, который при той же стойкости и прочих одинаковых условиях допу- скает обработку с меньшей скоростью резания. Наихудшую обрабаты- ваемость имеют инструментальные быстрорежущие, хромоникелеволь- фрамовые, хромомарганцовистые, хромокремнистые, хромокремнемар- ганцовистые и кремнемарганцовистые стали.
Очень низкой обрабатываемостью обладают жаропрочные стали и сплавы. Это объясняется тем, что жаропрочные материалы имеют зна- чительное количество легирующих элементов (в том числе титан и мар- ганец), склонны к свариванию (к адгезии) с режущим инструментом, незначительно изменяют прочность при нагреве до температуры 800° С, имеют высокий предел прочности на сдвиг (в 2—3 раза выше по сравнению с конструкционной углеродистой сталью); у жаропрочных материалов высокий предел прочности сочетается с большой вяз- костью, они способны к сильному упрочнению (наклепу) и имеют низкую теплопроводность. Все это вызывает при резании большие силы, высокую температуру (в 2—4 раза выше температуры при реза- нии конструкционных сталей [69]), интенсивный износ режущего инструмента, большую шероховатость обработанной поверхности, т. е. низкую обрабатываемость этих материалов, а потому их относят к труднообрабатываемым.
1 Нагрев при Т — 870°С втечение 4 ч, быстрое охлаждение до Т = 740°С и вы- держка в течение 2 ч.
2 Обрабатываемость металлов характеризуется также шероховатостью обработан- ной поверхности (что особенно важно при окончательных—чистовых операциях) и силами, действующими на инструмент в процессе резания.
115
Легко (с большой скоростью резания) обрабатываются автоматные стали, цветные и легкие сплавы.
Алюминий обрабатывается со скоростью резания в 5—б раз боль- шей по сравнению с углеродистой конструкционной сталью (С £0,6%, в= 75 кГ/ммг); для силумина и литейных алюминиевых сплавов эта скорость выше в 4—5 раз.
Чугун вследствие меньшей теплопроводности, большего истираю- щего действия и сосредоточения давления от стружки на малом участке вблизи режущей кромки допускает меньшую скорость резания по сравнению с углеродистой конструкционной сталью.
В зависимости от предела прочности стали при растяжении ско- рость резания, допускаемая резцом при определенной стойкости,

При обработке резцами, оснащенными твердым сплавом, конструкционных углеродистых и легированных незакаленных сталей
X = 1.
Таким образом, если известна скорость резания vu, допускаемая резцом при данной стойкости для стали оп, то легко найти скорость v ' u для стали с авг, так как
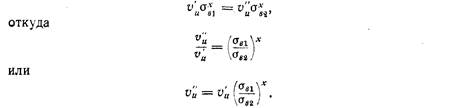
Если при обработке углеродистой конструкционной и легиро- ванной незакаленной стали с ае = 75 кГ/мм2 скорость резания, до- пускаемую резцом, принять за единицу, то при других значениях ав поправочными коэффициентами KMV на скорость резания будут зна- чения


Приведенная выше формула может быть записана так:

В зависимости от твердости чугуна НВ скорость резания, допу- скаемая резцом при определенной стойкости,

116
При работе резцами, оснащенными пластинками твердых сплавов, у =25 [52].
На скорость резания, допускаемую режущими свойствами резца, оказывают влияние и состояние обрабатываемого материала, характер заготовки и состояние ее поверхности. Так, если для горячекатаной стали скорость резания принять за единицу, то для холоднотянутой стали необходимо ввести коэффи- циент 1,1, т. е. принять скорость резания на 10% выше. Для норма- лизованной стали этот коэффициент будет 0,95, для отожженной 0,9 и для улучшенной 0,8.
Если при обработке стальной заготовки из проката или поковки без корки (корка срезана предыдущим проходом или протравлена) скорость резания принять за единицу, то в случае обра- ботки стальной отливки скорость резания уменьшается (коэффи- циент 0,9).
Твердая корка, получившаяся на чугунной заготовке после от- ливки, окалина после поковки и горячего проката стали — резко влияют на повышение износа инструмента и в связи с этим снижают скорость резания (окалина на 10—20%, корка на 20—40%).
Влияние материала режущей части резца. Износ инструмента во многом предопределяется физико-механическими свойствами мате- риала, из которого сделана его режущая часть. Поэтому, если для быстрорежущих сталей допускаемую скорость резания принять за единицу, то по отношению к другим материалам коэффициент на скорость резания Км1 v будет меньше еденицы для легированых и углеродистых инструментальных сталей и больше единицы для твер- дых сплавов и керамических материалов.
Ниже приведены значения коэффициента KMlv Для различных марок сталей:
Марка стали режущей части резца................... Р18, Р9 9ХС У10А, У12А
коэффициент KMlv....................................... 1 0,5 0,5 и ниже
. Для твердых сплавов Км1ь = 3-5-10 и больше (при соответст- вующей оптимальной геометрии режущей части резца).
Если скорость резания для твердого сплава Т15К6 принять за единицу, -то для сплава Т5К10 необходимо ввексти коэффициент 0,65, а для сплава Т30К4 1,3—1,5 (при получистовом точении с t = 1 ¸ 2,5 мм, s =0,1—0,3 мм/об); твердый сплав Т14К.8дает воз- можность повысить скорость резания в сравнении со сплавом T5K10 на 25%.
По отношению к сплаву ВК6 для сплава ВК8 коэффициент на скорость резания равен 0,83, а для твердого сплава ВК.ЗМ—1,15 (при получистовом точении). Сплав ВК2 позволяет повысить скорость резания (при чистовой обработке) в среднем на 35—40% по сравнению со сплавом ВК8, сплав ВК4 — на 20—30% (как при чистовой, так и при черновой обработке).
117
Резцы с керамическими пластинками при чистовой и получистовой обработке сталей-допускают скорость резания в 1,1—1,3 раза боль- шую, чем с пластинками из сплава Т15К6; при чистовой и предчистовой обработке чугуна — в 1,5 раза большую, чем из сплава В Кб. На отдельных операциях эти коэффициенты еще выше (до 3 раз).
Влияние подачи и глубины резания. Подача и глубина резания, влияющие на силы и температуру при резании, оказывают большое влияние и на скорость резания, допускаемую резцом. Чем больше подача и глубина резания, тем выше силы, действующие на резец, и температура резания, тем интенсивнее износ резца, тем меньшую скорость резания будет допускать резец при одной и той же стойкости. Зависимость между скоростью резания, подачей и глубиной резания при стойкости 60 мин можно выразить следующей формулой:
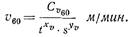
где С60 — постоянный коэффициент, зависящий от обрабатывае мого металла, материала режущей части резца, гео метрии резца, охлаждения и других условий обработки (в нашем случае одним из этих условий является стойкость резца, равная 60 мин); t — глубина резания в мм; s — подача в мм/об; xv и yv — показатели степеней, различные для разных обрабаты- ваемых металлов, материала резца и условий обработки. При наружном точении и растачивании заготовок из углеро- дистой стали резцами из быстрорежущей стали при подаче s £ 0,25 мм/об xv = 0,25, yv = 0,33; при подаче же s > 0,25 мм/об xv = 0,25, yv = 0,66 (при s < t *).
Из приведенных значений следует, что показатель степени при подаче больше, чем при глубине, т. е. увеличение подачи более резко сказывается на уменьшении скорости резания, чем увеличение глу- бины резания. Это вызывается более интенсивным износом резца при увеличении s, чем при увеличении t что, в свою очередь, объяс- няется большей термодинамической нагрузкой на единицу длины режущей кромки, так как при увеличении s, при неизменной длине активной части режущей кромки увеличивается и толщина среза (см. рис. 70, б).
При одинаковой площади поперечного сечения среза для обычного резца ( 0 при s < t) легче работать с меньшей подачей и большей глубиной резания; для станка же (по мощности), наоборот, легче работать с большей подачей и меньшей глубиной резания, так как на силу резания глубина оказывает большее влияние, чем подача (см. стр. 81).
При обратных срезах (s > t глубина резания влияет в большей степени, чем подача, т. е. xv > yv.
Влияние геометрических элементов резца. Чем больше величина угла резания, тем больше деформации, тепловыделение и силы, действующие на резец, тем интенсивнее износ резца и ниже его стой- кость. При уменьшении угла резания (увеличении положительного значения переднего угла) деформации, силы резания и тепловыделение снижаются и стойкость сначала повышается (рис. 108). Но вместе с увеличением угла + уменьшается угол заостренмя и объем головки резца, вследствие чего теплоотвод от поверхностей «трения резца и прочность режущей кромки уменьшаются, и, начиная с некоторого значения угла резания, износ повышается (возможно и выкрашивание режущей кромки) и стойкость понижается. Поэтому для каждого материала заготовки, материала резца и других условий обработки
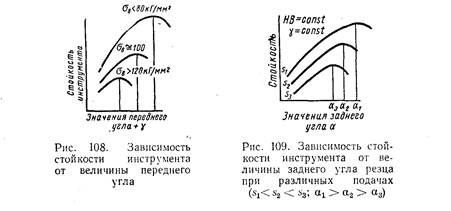
есть свое оптимальное значение угла резания (переднего угла), при котором стойкость, а следовательно (при одинаковых стойкостях), и скорость резания будут наибольшими. При этом чем выше s или НВ обрабатываемого металла, тем меньше положительное значение опти- мального переднего угла.
Чем больше задний угол резца, тем меньше трение резца о заготовку, тем меньше его износ и выше стойкость. Однако повы- шение стойкости идет до определенного значения угла а, так как с увеличением заднего угла уменьшается одновременно угол заостре- ния, резец становится менее прочным, и начиная с некоторого значения а режущая кромка (особенно у твердых сплавов) начинает выкраши- ваться и стойкость резко падает (рис. 109); будет падать, следовательно, и скорость резания (при одной-и той же стойкости).
Одним из геометрических элементов, сильно влияющих на допу- скаемую резцом скорость резания, является главный угол в плане. Чем больше этот угол, тем больше (при одинаковых подаче и глубине резания) толщина среза, тем меньше длина актив- ной части режущей кромки и активный (в основном воспринимающий тепло) объем головки резца (см. рис. 19), тем выше термодинамическая
118
119
нагрузка на единицу длины кромки, интенсивнее износ резца и меньше его стойкость. Поэтому резцы с малыми углами в плане допускают (при прочих одинакоых условиях) большую скорость резания (рис. 110).
Если для твердосплавного резца с углом <р = 45° при резании стали скорость резания принять за единицу, то для других значений главного угла в плане скорость резания выразится следующими коэффициентами К j v
Главный угол в плане <р°............. 10 20 30 45 60 75 90
Коэффициент К j v........................... 1,55 1,3 1,13 1 0,92 0,86 0,81
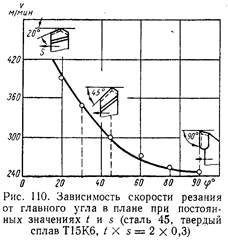
| Вспомогательный угол в плане также влияет на износ резца, а следовательно, и на его стойкость. При малом вспомо- гательном угле в плане ( вспомогательная режущая кром- ка принимает большое участие в побочном резании, что вызы- вает большие тепловыделение и износ резца, а следовательно, по- нижается его стойкость. По мере увеличения угла работа ре- зания от вспомогательной ре- жущей кромки уменьшается, что приводит к некоторому повы- шению стойкости и, вследствие этого, к повышению скорости, допускаемой резцом при оди- наковой стойкости (рис. 111). Однако, начиная с ( = 5 ¸10°, в большей степени сказывается уменьшение объема головки рез- ца, приводящее к ухудшению теплоотвода и к большей температур- ной концентрации на поверхно'стях трения резца, что снижает до- пускаемую скорость резания. Ниже даны поправочные коэффициенты К j v на скорость резания в зависимости от вспомогательного угла в плане, если принять скорость резания при = 10° за еди- ницу.

При увеличении радиуса закругления (сопряжения) при вершине резца в плане, хотя и возрастают деформации и силы Р z и Ру, но вместе с тем увеличиваются длина активной части режущей кромки и объем головки резца. Последнее, способствуя усилению теплоотвода, оказывается преобладающим, а потому с увеличением радиуса закругления при вершине резца в плане стойкость резца, а следовательно, и скорость резания, допускаемая им, несколько
120
повышаются. Так, если для быстрорежущего резца с r = 2 мм допу- скаемую скорость резания принять за единицу, то поправочные коэф- фициенты для других значений r будут [53]: для r = 1 мм К rv 0,94; для r = 3 мм Krv =1,03; для г — 5 мм Krv = 1.13.
Положительное значение угла наклона главной режущей кромки X оказывает большое влияние на упрочнение режущей кромки резца, что особенно важно при ударном (прерывистом) резании, при работе по корке и при работе с неравномерным припуском. В связи с этим по мере перехода от отрицательного значения угла X к поло- жительному (от — 15 до +40) стойкость резца повышается. В диа- пазоне углов — 0 ¸10° изменение стойкости незначительно, и им можно пренебречь.
Форма передней поверхности резца также оказы- вает влияние на скорость резания. Если для резца, оснащенного
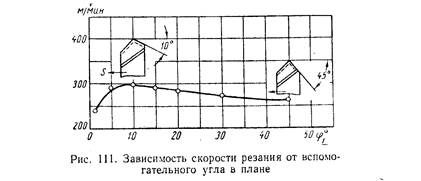
пластинкой твердого сплава, с плоской формой передней поверх- ности (форма /, см. рис. 115), скорость резания принять равной еди- нице, то для плоской или радиусной формы с фаской (формы // и ///) коэффициент на скорость резания будет 1,15, а для плоской с отри- цательным передним углом = — 10° (форма IV) этот коэффициент равен 1,2. Форма IV по отношению к формам // и /// имеет коэффи- циент на увеличение скорости резания 1,05.
Влияние размеров сечения державки резца. На скорость резания, допускаемую резцом, влияют и размеры сечения резца, так как чем больше площадь сечения тела резца, тем интенсивнее теплоотвод от поверхностей трения (износа) резца и ниже температурная концентра- ция. Повышается и жесткость резца, а потому резец, имеющий боль- шие размеры сечения державки, допускает и более высокие скорости резания. Так, если для резца из быстрорежущей стали с сечением державки 20x30 мм2 скорость резания принять за единицу, то для сечения 16x25 мм2 коэффициент на скорость K qv -- 0,97, а для сече- ния 25x40 мм2 — 1,04 (при обработке сталей).
Для резцов, оснащенных пластинками твердых сплавов, влияние размеров сечения державки незначительно, и им можно пренебречь.
121
Влияние смазывающе-охлаждающей жидкости. Смазывающе- охлаждающие жидкости (СОЖ), облегчающие стружкообразование уменьшающие коэффициент трения и снижающие температуру реза- ния оказывают влияние и на скорость резания, допускаемую резцом. Выше отмечалось, что наибольшей охлаждающей способностью обла- дают водные смазывающе-охлаждающие жидкости. При обильном охлаждении (8—12 л/мин) сверху (в месте отделения стальной стружки, см. оис. 94, а) при обдирочных работах резцами из быстрорежущей
стали скорость резания по- вышается на 20—30%, а при чистовых работах (тонких стружках, когда тепловыделение меньше) — на 8—10% по сравнению с обработкой всухую. Рас- ход жидкости при чистовой обработке меньше, чем при черновой, и может состав- лять 4—6 л/мин.
Скорость резания при обработке стали может быть повышена на 40—45% по сравнению с обработкой всухую, если смазывающе- охлаждающую жидкость (эмульсию) предварительно охладить до +2° С. Из за- висимости, данной на рис. 112, видно, что чем ниже температура охлаждающей жидкости, тем дальше от- стоит данная линия от ли- нии, соответствующей обработке всухую, тем большую, следователь- но, скорость резания допускает резец при одной и той же стойкости. Скорость резания для резцов из быстрорежущей стали может быть повышена до 43% [по сравнению с обработкой стали всухую, и в том случае, если смазывающе-охлаждающую жидкость подводить в зону резания снизу в распыленном состоянии (см. рис. 94, б)].
По сравнению с обычным охлаждением сверху (см. рис. 94, о) такой способ подвода жидкости в условиях проведения испытаний (применяемых в работе (711) дал возможность повысить скорость реза- ния на 14,5%, а стойкость резцов (при одной и той же скорости реза- ния) — в 3,2 раза.
Охлаждение инструмента и зоны стружкообразования распылен- ной жидкостью (воздухо-жидкостной смесью) эффективно и для твер- досплавных резцов, особенно при резании высокопрочных и трудно- обрабатываемых сталей. Наряду с повышением стойкости инструмента
(в 2—6 раз по сравнению с обработкой всухую и в 1,5—3 раза по срав- нению с обычным охлаждением — поливом) повышается и качество обработанной поверхности при одновременном снижении расхода эмульсий в 10—20 раз, а масла — в сотни раз [72].
Применение распыленной жидкости для твердосплавных резцов по сравнению с методом обильного потока (см. стр. 94, а) целесооб- разно и в том отношении, что при высоких скоростях резания (с кото- рыми обычно работают твердосплавные резцы) при обильном потоке жидкость сильно разбрызгивается вокруг станка.
При резании серых чугунов с применением обильного охлаждения происходит большое загрязнение станка кашицеобразной массой,
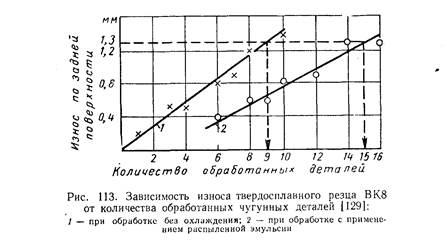
образуемой из чугунной пыли и мелкой стружки. Поэтому здесь целе- сообразно применение жидкости в распыленном состоянии, что спо- собствует повышению стойкости резцов в 2—3 раза [129].
При резании высокопрочных и износостойких чугунов твердосплав- ными резцами применение распыленной жидкости способствует повы- шению скорости резания до 50%.. Применение распыленной эмульсии способствует также уменьшению запыленности воздуха чугунной
пылью.
Эффективность применения распыленной эмульсии при резании чугуна графически наглядно представлена на рис. ИЗ.
В заключение отметим, что для твердосплавного инструмента особенно важно наличие постоянного охлаждения, так как в слу- чае прерывистого охлаждения сильно разогреваемая в процессе реза- ния, а затем резко охлаждаемая пластинка твердого сплава может дать трещины, и резец выйдет из строя.
Влияние допустимой величины износа резца. На скорость резания оказывает влияние и максимально допустимая, по условиям работы,
122
123
величина износа по задней поверхности. Чем больше допустимый износ, тем большую скорость резания можно назначить для резца. Ниже приведены поправочные коэффициенты К hv на скорость резания в зависимости от износа по задней поверхности для резцов, оснащенных пластинками твердого сплава, при обработке незакаленной стали.
Износ h 3 в мм.............................................................................. 0,8—1 1,5—2
Коэффициент Khv........................................................................ 1 1,33
Влияние вида токарной обработки. В зависимости от вида токарной обработки (наружное точение, внутреннее растачивание, подрезка торца, отрезка) изменяются условия, в которых находится резец в процессе стружкообразования.
Так, при внутреннем растачивании резец находится в более тяжелых условиях, чем при наружном продольном точении. Наряду с тем, что вершина расточного резца находится на максималь- ном диаметре (D > D 0, рис. 13), т. е. работает на наибольшей ско- рости, что в данном случае затруднён подвод свежей охлаждающей жидкости и хуже теплоотвод. Отрицательным моментом является и то, что расточным резцам, имеющим меньшее сечение державки и большой вылет, приходится работать в менее жестких условиях; это вызывает прогиб резца и вибрации, а потому при растачивании снимается обычно меньшее сечение среза и снижается скорость резания. Чем меньше диаметр растачиваемого отверстия, тем больше поверхность соприкос- новения резца с заготовкой, тем больше износ по задней поверхности за одно и то же время, тем меньшую скорость резания будет допускать расточной резец по сравнению с резцом для наружного продольного точения (коэффициент уменьшения Kpv = 0,8 для D до 75 мм) для D = 75 ¸ 150 мм; 0,95 для D = 150 ¸ 250 мм; 1 для D > 250 мм)
При поперечном точении (подрезке торца) условия работы для резца более благоприятны, чем при продольном точении, так как резец при подаче от периферии к центру находится под воздей- ствием наибольшей скорости резания небольшой промежуток времени. По мере перемещения резца к центру заготовки эта скорость умень- шается (см. рис. 17), и в центре она равна нулю.
Следовательно, по сравнению с резцом для наружного продоль- ного точения (который находится под воздействием постоянной, максимальной для поперечного точения скорости резания вдоль всей длины обработки) резец для поперечного точения будет изнаши- ваться менее интенсивно, а потому скорость резания для него можно назначить более высокой; причем чем резче перепад между макси- мальной и минимальной скоростями резания, т. е. чем меньше отно- шение (где D — наибольший, a D 0 — наименьший диаметр обра- ботанной поверхности торца), тем более благоприятны условия и выше допустимая скорость резания. Если скорость резания для твер-
124
досплавного резца при продольном наружном точении принять за единицу, то для поперечного точения (при тех же условиях) скорость резания может быть выражена следующими коэффициентами Knv [52]:
при поперечном точении............................. До 0,4 0,5—0,7 0,8—1,0
Коэффициент ............................................. 1,25 1,2 1,05
В тяжелых условиях работают отрезные (прорезные) резцы (см. рис. 14), так как процесс стружкообразования протекает здесь в менее благоприятных условиях. Малые углы при вершине в плане и незначительные размеры сечения головки отрезных резцов обуслов- ливают плохой теплоотвод. Особенно нагруженными в температурном отношении оказываются уголки резца, что приводит к их сильному износу и, следовательно, к значительному уменьшению скорости резания по сравнению со скоростью резания, допускаемой резцами для наружного продольного точения. Для упрочнения уголков отрез- ного резца у них делается переходная кромка (см. рис. 119, в).
Если для отрезки (разрезки) твердосплавным резцом скорость резания принять за единицу, то при прорезке паза на диаметр D0 (см. рис. 14) скорость резания может быть выражена следующими коэффициентами Кпр [52]:
при прорезке паза......................................................... 0,5—0,7 0,8—0,95
Коэффициент Кпр.................................................................. 0,96 0,84
Вследствие специфичности условий резания при отрезании реко- мендуется обязательно применять смазывающе-охлаждающие жид- кости, способствующие как повышению стойкости резцов и облег- чению выхода стружки из канавки, так и снижению сил резания (что особенно важно для малопрочных и маложестких отрезных резцов).
Для твердосплавных отрезных резцов при резании сталей при- менение охлаждения способствует повышению скорости резания до 40%.
§ 2. ФОРМУЛЫ ДЛЯ ПОДСЧЕТА СКОРОСТИ РЕЗАНИЯ
На основании изложенного выше скорость резания, допускаемая резцом, при наружном продольном точении может быть подсчитана по следующей общей формуле:
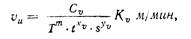
125
где Cv — коэффициент, характеризующий обрабатываемый ме-
талл и условия его обработки; Т —-стойкость режущего инструмента в мин; m — показатель относительной стойкости; t — глубина резания в мм; s — подача в мм/об; — показатели степеней; Кь — общий поправочный коэффициент на измененные усло- вия обработки по отношению к тем, для которых дается значение коэффициента С„ (Kv равен произведению частных поправочных коэффициентов, рассмотренных, в разделе «Влияние различных факторов на скорость резания, допускаемую резцом»). В табл. 5 приводятся для некоторых условий обработки значения для твердосплавного резца Т5КЮ.
Таблица 5
Значения коэффициента и показателей степеней в формуле скорости резания (наружное продольное точение1, сплав Т5К10)
Значения Cv в табл. 5 даны для стали без корки с в = 75 кГ/мм2 при резании без охлаждения твердосплавным резцом (Т5К10), с опти- мальным значением углов g и а с = 45°, = 10°, с отрицательной фаской на передней поверхности (форма //, ///, см. рис. 115), при максимально допустимом износе по задней поверхности.
При других условиях работы на величину коэффициента Cv (или в формулу скорости vu) необходимо в виде сомножителей ввести попра- вочные коэффициенты, приводимые выше или в
|