Форма абразивного инструмента
Абразивный инструмент изготовляется различных форм и конструк- ций.
Шлифовальные круги. По ГОСТу 2424—60 предусматривается 22 профиля шлифовальных кругов диаметром 3— 1100 мм, высотой 0,5—200 мм, с диаметром отверстий 1—305 мм. Наиболее распростра- ненные виды из них представлены на рис. 369.
Плоские круги прямого профиля ПП применяют для круглого наружного, внутреннего и бесцентрового шлифования, для плоского шлифования периферией круга и для заточки инструмента. В последнем случае в качестве рабочей поверхности используют как торцовые поверхности, так и цилиндрическую.
Плоские круги с двухсторонним коническим профилем 2П применяют для шлифования зубьев шестерен и шлифования резьбы.
Плоские круги с выточкой ПВ и с двухсторонней выточкой ПВД характерны тем, что в выточках помещаются зажимные фланцы, которые дают возможность более свободно подвести круг к обрабаты- ваемой заготовке и совместить круглое шлифование с подрезкой торца. Круги формы ПВД применяют также при бесцентровом шлифовании (для ведущих кругов).
Цилиндрические чашки ЧЦ применяют для заточки инструмента и для плоского шлифования торцом, имея надежное (флан- цевое) крепление к шпинделю станка.
Конические чашки ЧК применяют для заточки режущего инструмента и для плоского шлифования. Работа ведется торцом круга, который вследствие малой поверхности легко поддается правке. Кони-
448 -
ческая форма чашки облегчает подвод затачиваемого инструмента к рабочей поверхности круга.
К р у г и - т а р е л к и 2Т имеют две конические поверхности (под углом = 25° и = 5°), что облегчает правку круга по конической поверхности, которая при заточке винтовых поверхностей режущего инструмента является рабочей поверхностью.
Алмазные круги. Алмазные круги в отличие от кругов из других абразивных материалов изготовляются не цельными, а состоящими из

алмазоносного кольца (толщиной 0,5—3 мм), закрепленного на кор- пусе из дуралюмина, стали или из пластмассы (рис. 370). Концентра- ция алмазных зерен в единице объема алмазоносного слоя1 50, 100 и 150% (за 100%-ную концентрацию условно принято содержание 0,878 мг алмазного порошка в 1 мм3 алмазоносного слоя). В качестве связки алмазных зерен применяют керамические, органические (баке- литовую), а также металлические материалы (чаще бронзу).
По ГОСТу 9206—59 зернистость алмазных порошков колеблется от величин меньше 1 мк (AMI) до 630 мк (А50), В отличие от абразив- ных материалов по ГОСТу 3647—59 в обозначении зернистости естест-
1 Состоит из алмазных зерен, связки и наполнители (твердых минералов)
15 В. А. Аушнков 449
венных алмазных зерен (порошков) впереди числа зернистости ста- вится буква А.
Синтетические алмазы, из которых делают круги, выпускаются трех марок [140]: АСО — для изготовления инструмента на керамической связке; АСП — для изготовления инструмента на металлической и керамической связках, а также для изготовления паст и свободных порошков для притирочных и доводочных операций1; АСВ — для изготовления инструмента на металли- ческой связке, работающего при высоких удельных нагрузках.
Алмазные порошки марки АСО выпускаются зер- нистостью, начиная с АС025 (250 мк) и менее, марки АСП — начиная с АСП40 (400 мк) и менее, марки АСВ — начиная с АСВ50 (500 мк) и менее. Цифры, стоящие после букв АСО, АСП и АСВ, указывают на размер зерен синтетических алмазов.
В зависимости от размера зерен синтетические алмазы делятся на две группы: на шлифпорошки (размер зерен 630—40 мк) и на.микропорошки (40 мк и менее). Микропорошки из синтетических алмазов обозначаются АСМ40, АСМ28 и т. д. Алмазные зерна имеют более острые углы между гранями, что спо- собствует получению более качественно обработанной поверхности по сравнению с другими абразивными материалами.
Наряду с кругами плоского прямого профиля алмазные круги делаются чашечными, тарельчатыми, специальными (профильными). Алмазные круги применяют для заточки и доводки инструмента, оснащенного твердым сплавом 2 (что по сравнению с обычной заточкой и доводкой способствует повышению стойкости инструмента в 2 раза), а также для шлифования различных деталей из твердых сплавов.
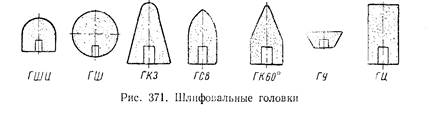
Шлифовальные головки. По ГОСТу 2447—64 шлифовальные головки выпускаются семи форм (рис. 371). Они применяются для внутреннего шлифования и для зачистки деталей, когда не могут быть применены шлифовальные круги. Головки не имеют сквозных посадочных отвер-
1 Для получения 1—2-го класса точности н 10—-14-го класса чистоты алмазные пасты (АП) г.ыпускаются зернистостью от 100 до 1 мк,
2 См. [11] и стр. 472.
стий и приклеиваются к специальным шпилькам. Диаметр головки 3—40 мм.
Шлифовальные сегменты. ГОСТ 2464—60 предусматривает сегмен- ты девяти различных форм по сечению; некоторые из них приведены на рис. 372. Длина сегментов 125—300 мм. Сегменты применяют для плоского шлифования; шлифовальный круг в этом случае состоит из нескольких сегментов, закрепленных тем пли иным способом в головке (см. рис. 378) или в патроне. К достоинствам сегментных кругов отно-
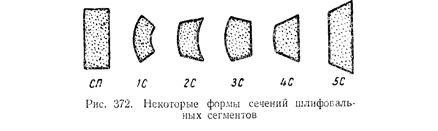
сится то, что при повреждении какого-либо сегмента не надо выбрасы- вать весь круг, так как поврежденный сегмент легко заменяется новым. Пространство между сегментами облегчает подвод смазывающе-охлаж- дающих жидкостей к месту резания, отвод стружки и отработанных частиц круга. Меньшая площадь соприкосновения круга с заготовкой способствует и уменьшению нагрева шлифуемой заготовки.
Шлифовальные бруски. По ГОСТу 2456—60 предусматривается шесть форм сечения брусков (рис. 373).
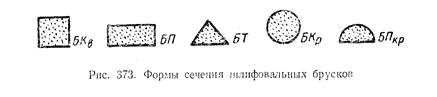
Шлифовальные бруски применяют для ручных слесарных работ, а также для хонингования и суперфиниширования (отделочных опера- ций); в последних случаях используются бруски квадратные БКb;. пло- ские БП и специальные плоские хонипговальные БХ, которые крепятся в специальных головках.
Шлифовальные шкурки. Они состоят из основы (бумаги, хлопчато- бумажной ткани), на которую наклеены абразивные зерна. Шкурки применяются для ручной и машинной зачистки и отделки различных деталей и изделий
Для шкурок, работающих без водного охлаждения, применяют мездровый клей; для работы с водным охлаждением шкурку (водо- стойкую) изготовляют па специальных лаках и смолах. Шкурки делают в виде листов и ленг.
450
15-
451
Кроме рассмотренных основных форм абразивного инструмента, абразивные зерна используют для шлифовальных дисков на фибровой основе, для бесконечных лент (на тканевой основе), для абразивных паст (когда зерна связываются маслами, воском, животными жирами, стеарином и др.).
Пасты применяют для доводки (притирки) режущего инструмента и отдельных деталей машин.
§ 4. ЗАКРЕПЛЕНИЕ АБРАЗИВНОГО ИНСТРУМЕНТА
Для успешной и безопасной работы шлифовальный круг должен быть прочно закреплен на шпинделе, хорошо отбалансирован, испытан на прочность (перед постановкой па станок) и надежно огражден защит- ным кожухом. Круг должен свободно надеваться на посадочную поверх- ность (диаметр отверстия круга должен быть на 0,1— 1,5 мм больше диаметра поверхности, на которую он ставится). Между зажимными поверхностями и кругом должны быть поставлены прокладки (резина, картон, кожа) толщиной 0,5—3 мм (в зависимости от диаметра круга).
Рис. 374. Крепление при- Рис. 375. Крепление на клеиванием винтнте
По ГОСТу 2270—54 предусматривается семь основных м етодов к р с п л с н и я абразивного инструмента.
Шлифовальные головки приклеиваются к шпильке (рис. 374).
Круги малых диаметров (DK до 70 мм) крепят винтом (рис. 375).
На рис. 376, й показано крепление на шпинделе (оправке) винтом (для DK до 100 мм), а на рис. 376, б — крепление на шпинделе флан- цами (для кругов диаметром DK до 500 мм).
- Крепление на переходных фланцах (рис. 377) предусматривается для DK до 1100 мм и втом случае, когда диаметр отверстия круга больше диаметра шпинделя.
Крепление сегментов в сегментной головке показано на рис. 378. Крепление на переходных фланцах наклеиванием показано на рис. 379.
Б а л а и с и р о в к а кругов производится как после их изготов- ления (заводом-изготовителем), так и при установке кругов на станок, особенно при креплении кругов DK ³ 125 мм на переходных флан- цах. Это необходимо делать потому, что при неуравновешенности круга могут возникнуть вибрации, приводящие к ухудшению качества обра- ботанной поверхности и к усилению износа подшипников шпинделя; возрастает и опасность разрыва круга.
Статистический дисбаланс круга характеризует неуравновешен- ность шлифовального круга, вызванную несовпадением его центра тяжести с осью вращения. Дисбаланс (величина которого определяется

ГОСТом 3060—55) на заводах-изготовителях проверяется на специаль- ных балансировочных станках и устраняется заливкой свинца в гнезда, специально вырубленные для этого в круге. На заводе-потребителе круги балансируют как на балансировочных приспособлениях, так и непосредственно на шлифовальном станке перемещением сухариков в специальных ба- лапсириых фланцах. Хорошо отбалансиро- ванный круг должен иметь устойчивое равно- весие при повороте и остановке его в любом положении по окружности.
Круги, работающие со скоростями і 50 м/егк, должны подвергаться баланси- ровке и после каждой их правки.
Испытания кругов на прочность производят на специальных испытательных станках, вращением круга со скоростью, в 1,5 раза превышающей рабочую скорость, в течение определенного времени (7—10 мин).
Во избежание травматизма при разрыве круга он во время работы должен быть огражден защитным кожухом, сделанным из стали или ковкого чугуна. Кожух должен иметь достаточную прочность, надежное за- крепление на станке и предохранять рабочего от разбрызгивания жидкости.
Расположение защитного кожуха и наибольшие углы раскрытия должны соответствовать ГОСТу 3881—65 (рис. 380).
При работе на обдирочных и заточных станках максимальный угол раскрытия 900, по отношению к горизонту 65" (рис. 380, а); когда при
453
454
работе на тех же станках деталь располагается ниже оси круга — 125° и 65° (рис. 380, б); при работе на круглошлифовальных и бесценшо- вошлифовальных станках 180° и 65° (рис. 380 s); на плоскошлифоваль- ных стайках при работе периферией круга 150° и на 15е ниже горизонта (рис. 380, г); для переносных станков с гибким валом и для обдирочных станков с качающейся рамой 180° и 0° (рис. 380, д); максимальный угол
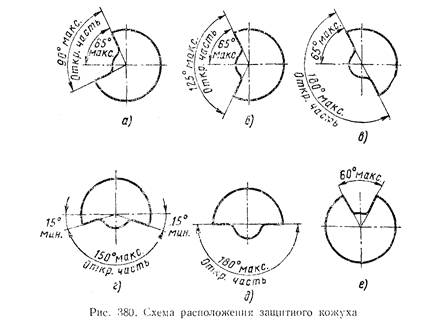
раскрытия 60° применяется для кругов, работающих наиболее высокой своей точкой (рис. 380, г).
По ГОСТу 3881—65 зазор между новым кругом и внутренней цилинд- рической поверхностью кожуха 3—25 мм (в зависимости от диаметра круга); зазор между кругом и боковой стенкой кожуха 10—15 лиг.
Край подручника, применяемого для поддержки деталей, подавае- мых к кругу вручную, должен отстоять от рабочей поверхности круга не менее чем на половину толщины шлифуемой детали; но этот зазор не должен быть более 3 мм.
§ 5. ИЗНОС И ПРАВКА АБРАЗИВНОГО ИНСТРУМЕНТА
В процессе шлифования зерна абразивного инструмента (например, круга) изнашиваются и он теряет режущую способность.
На уменьшение режущей способности круга, наряду с износим зерна, влияет также и заполнение пространства между зернами —
455
отходами шлифования (спекшаяся металлическая пыль, продукты износа зерен и связки).
Изношенный и «засаленный» круг перестает резать, и для восста- новления его режущих способностей необходима его правка (заточка). Наряду с удалением затупленных зерен и отходов шлифования при правке восстанавливается и правильная геометрическая форма круга, потерянная им в результате неравномерного износа.
Так как шлифование является в основном чистовой (отделочной) операцией, то за критерий износа круга принимается технологический критерий (дробленая обработанная поверхность, прижоги обработан- ной поверхности, плохая чистота, риски).
За период стойкости часто принимается не время работы круга от правки до правки, а количество обработанных деталей или поверхно- стей.
При определенных условиях обработки может происходить «само- затачивание» шлифовальных кругов во время работы. У самозатачиваю- щихся кругов затупившиеся абразивные зерна вырываются из связки (или разрушаются1) под действием возросшей в результате затупления нагрузки. При выпадении затупленных зерен в круге обнажаются новые, острые зерна, которые и продолжают процесс резания. Если при работе круга без самозатачивания силы резания и температура резания растут по мере увеличения времени работы (износа), то при самозатачивающемся режиме силы резания и температура колеблются в незначительных пределах в течение всего времени работы. Правка самозатачивающихся кругов делается лишь с целью придания кругу правильной формы, искаженной вследствие неравномерного износа.
Несмотря на определенные достоинства самозатачивания, оно, однако, может получиться лишь при специальном подборе характери- стик круга и элементов режима обработки. Чаще всего это возможно при обработке твердых металлов специальными мягкими кругами при высоких элементах режима резания, характерных для обдирочных работ. В практике чаще встречаются условия, когда шлифовальный круг по мере его износа необходимо править принудительно.
Исследованиями ВНИИАШа установлено, что для восстановления режущей способности круга достаточно удалить с затупившейся поверх- ности слой толщиной 0,08 мм.
Режим и способ правки оказывают большое влияние на качество обработанной поверхности, получаемой после шлифования заправлен- ным кругом, так как чем меньше неровности на поверхности шлифо- вального круга, тем чище обработанная поверхность детали.
Существует два метода правки абразивного инструмента: алмазная и безалмазная правка.
При алмазной правке в качестве правящего инструмента применяют алмаз в виде одного зерна (0,25—2 карата), закрепляемого в стальной оправке (механически, зачекапкой или пайкой), или в виде
1 Сопротивление изгибу у абразивных зерен низкое [8—15 кГ/мм ].
456
алмазно-металлических карандашей, когда несколько мелких зерен алмаза (0,003—0,3 карата) заделывают в специальный вольфрамомедно- алюминиевый сплав (в форме цилиндриков).
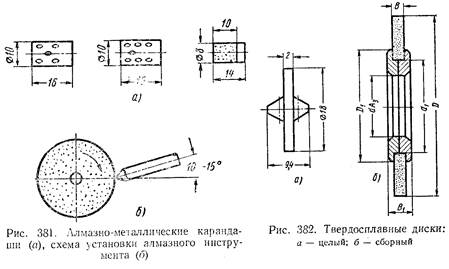
Алмазно-металлические карандаши (рис. 381, а) изготовляют не- больших размеров (4—10мм) и закрепляют в специальных оправках.
На станке алмазный правящий инструмент должен устанавливаться с наклоном в сторону вращения шлифовального круга на 10—15° и так, чтобы рабочая кромка алмаза находилась на уров- не оси круга (рис. 381, б) или ниже ее на 1— 2 мм.
—2
Режимы правки алмазным инструментом: скорость вращения круга максимально допустимая; продольная подача 0,05—0,4 м/мин; попе- речная подача 0,005—0,03 мм/ход; число проходов черновых 2—3, чистовых 1—2. Чем меньше величина продольной и поперечной подач, тем меньше шероховатость рабочей поверхности шлифовального круга.
457
При безалмазной правке в качестве инструмента приме- няют монолитные твердосплавные (ВКЗМ, ВК6М) диски (рис. 382); диски из зерен твердого сплава сцементированных латунью (рис. 383); металлические диски и звездочки (сталь ШX15, 20Х; рис. 384); абразив- ные диски (из черного карбида кремния па керамической связке, диаметр 60—150 мм, высота 20—-32 мм).
Безалмазпая правка, хотя и менее эффективна по сравнению с ал- мазной, но не требует применения дорогих алмазов, обеспечивая после правки получение шлифованной поверхности Ñ 7— Ñ 9.
Безалмазная правка осуществляется двумя методами: 1) обкатыва- нием (рис. 385, а), когда правящий инструмент вращается от шлифо- вального круга вследствие сил трения; 2) шлифованием (рис. 385, б),
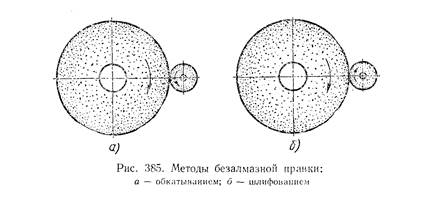
когда правящий инструмент получает принудительное вращение (от специального привода или от привода передней бабки шлифовального станка).
По методу обкатывания, когда удаление затупленных зерен из круга происходит вследствие вдавливания инструмента, могут рабо- тать все виды безалмазного правящего инструмента. По методу шлифо- вания работают в основном абразивные диски.
Безалмазный правящий инструмент крепят в специальных оправ- ках (металлические диски и звездочки крепят по несколько штук). На рис. 386 дана одна из таких оправок. Оси вращения шлифовального круга и правящего инструмента чаще всего располагают параллельно, по могут находиться и под углом 10—15°.
Из всех инструментов для безалмазпой правки наибольшее распро- странение, получили абразивные диски. Зернистость их берется на три-пять степеней крупнее, а твердость на пять-шесть степеней выше (по сравнению с шлифовальным кругом, подвергающимся правке). При правке по методу шлифования при круглом наружном шлифовании скорость вращения абразивных дисков приравнивается к скорости вращения заготовки, а шлифовальный круг вращается со скоростью, соответствующей его характеристике. Число проходов при правке —
.458
3—5, продольная подача 0,5—0,9 м/мин; поперечная 0,01—0,03 мм;
последние (чистовые) проходы ведут без поперечной подачи и с умень- шенной продольной подачей (0,4—0,5 м/мин). Безалмазная правка сопровождается обильным охлаждением.
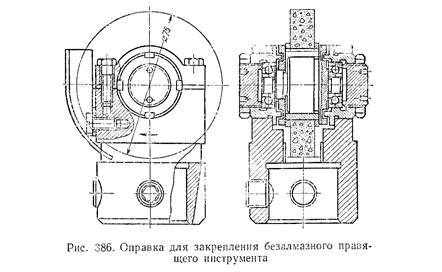
Алмазные круги правят только при потере ими точности формы. При правке алмазных кругов на металлической связке применяют абразивные бруски из зеленого карбида кремния на керамической связке, зернистостью 16 и 12, твердостью СМ1— СМ2; алмазные круги на бакелитовой связке правят куском пемзы. Правку проводят при рабочей скорости круга, с охлаждением.
§ 6. НАРУЖНОЕ КРУГЛОЕ ШЛИФОВАНИЕ В ЦЕНТРАХ
Наружное круглое шлифование в центрах применяется для обра- ботки цилиндрических наружных поверхностей. Имеется три способа круглого наружного шлифования в центрах: с продольной подачей (рис. 387, а); глубинное шлифование (рис. 387, б); с поперечной пода- чей (метод врезания — рис. 387, в).
При наружном круглом шлифовании с продольной пода- чей шлифовальный круг имеет два движения: вращательное вокруг оси и поступательное в глубину обрабатываемой заготовки (попереч- ная подача для постепенного снятия припуска). Заготовка же имеет вращательное движение вокруг осп и поступательное движение вдоль оси (продольная подача с целью обработки по всей длине заготовки). Поступательное движение шлифовального круга, т. е. поперечная подача па определенную глубину, осуществляется в конце продольного
459
й
хода заготовки и может происходить за один ее ход или за два хода (за один двойной ход).
Есть такие конструкции круглошлифовальных станков, у которых заготовка имеет только одно вращательное движение, а шлифовальный круг осуществляет три движения (вращательное, поступательное в нап- равлении поперечной подачи или глубины шлифования и поступатель- ное вдоль оси заготовки, т. е. в направлении продольной подачи).
Наружное круглое шлифование с продольной подачей применяют для шлифования круглых заготовок значительной длины. Припуск
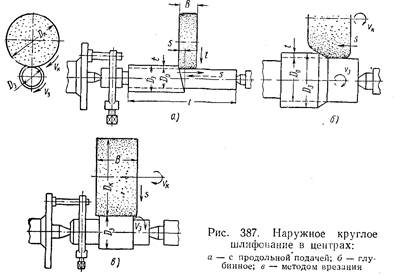
на шлифование на сторону назначается в пределах 0,15—1,15 мм и зависит от длины и диаметра заготовки, чистоты и точности предвари- тельной обработки, степени искажения геометрической формы после термической обработки и др.; 60—80% от общей величины припуска отводится под черновое (предварительное) шлифование, а 40—20% — под чистовое, окончательное.
При наружном круглом глубинном шлифовании (см. рис. 387, б) круг правится на конус или ступенями и весь припуск (0.1—0,4 мм) снимается за одии-два продольных хода круга (с пода- чей 1— 6 мм/об заготовки). Круг, кроме поступательного (продольного) перемещения вдоль оси заготовки, имеет вращательное движение вок- руг своей оси; заготовка же имеет только вращательное движение.
Глубинное шлифование применяют при обработке коротких (жест- ких) заготовок.
При наружном круглом шлифовании с поперечной по- дачей или метод ,м врезания (рис. 387, е) продольное перемещение
460
круга или заготовки отсутствует. Шлифовальный круг перекрывает всю ширину (длину) обрабатываемой поверхности заготовки, которая имеет только вращательное движение вокруг своей оси. Шлифовальный круг вращается и одновременно перемещается в поперечном направ- лении (0,0025—0,02 мм/об заготовки). Этот способ применяют при шли- фовании заготовок относительно небольшой длины (особенно при фасонном шлифовании); он дает высокую производительность.
Рассмотрим элементы режима резания при наружном круглом шли- фовании в центрах с продольной подачей (см. рис. 387, а).
Глубина резания (поперечная подача) измеряется в нап- равлении, перпендикулярном к обработанной поверхности, и представ- ляет собой слой металла, снимаемого шлифовальным кругом за один продольный ход:
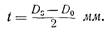
При черновом шлифовании поперечная подача на каждый ход стола t = 0,01 ¸ 0,025 мм, причем большие значения берутся при s < 0,5В мм/об заготовки1; меньшие — при s ³ 0,5В мм/об заго- товки.
При чистозом шлифовании поперечная подача t = 0,005 ¸ 0,015 мм; при прочих одинаковых условиях наиболее чистая обработанная поверхность получается при работе с большими окружными скоростями вращения шлифовального круга, с меньшими продольными подачами, с меньшими окружными скоростями вращения заготовки и с меньшими глубинами шлифования.
Вследствие отжима заготовки, неравномерного износа и выпадения зерен и отсутствия у круга сплошной режущей кромки круг будет искрить, удаляя некоторый слой металла и при проходах без попереч- ной подачи. Поэтому для получения требуемой точности и повышения чистоты обработанной поверхности совершаются «холостые» продоль- ные хода без поперечной подачи (процесс «выхаживания»). Это приво- дит к увеличению машинного времени, что учитывается в формуле вве- дением коэффициента точности (см. ниже).
Продольная подача s — величина относительного поступа- тельного перемещения круга.и заготовки вдоль ее оси за один ее оборот (мм/об заготовки). Обычно продольная подача задается в долях ширины круга s 0, т. е. s == s d В мм/об заготовки, где s d = 0,3 ¸ 0,5 — для черновой обработки, D 3, ³ 20 мм; s 0 = 0,7 ¸ 0,85 — для черновой обработки, D 3 ³ 20 мм; sd = 0,2 ¸ 0,4 — для чистовой обработки; В — ширина круга в мм; D 3, — диаметр заготовки.
1 Д-р техн. паук, проф. Е. И. Маслов впервые показал, что вследствие отсутствия у шлифовального круга сплошной режущей кромки фактическая глубина резания t ф после первого прохода круга будет значительно больше величины поперечной подачи t.
461
Минутная продольная подача или скорость продольного хода стола
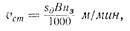
где пэ — число оборотов заготовки в минуту.
Скорость вращения з а г о т о в к и измеряется в mImu h и может быть подсчитана по формуле
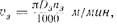
где D 3 — диаметр заготовки в мм;
п3 — число оборотов заготовки в минуту. Скорость вращения шлифовального круга (скорость резания) измеряется в метрах в секунду и подсчитывается по формуле
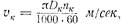
где Dk — диаметр шлифовального круга в мм;
n к — число оборотов шлифовального круга в минуту.
Для выявления сущности процесса шлифования и определения влияния различных факторов на него большое значение имеет глу- бина резания tx (толщина среза), снимаемая одним абразивным зерном шлифовального круга. Величиной tx определяется нагрузка на зерно круга (а следовательно, п стойкость круга) и качество обра- ботанной поверхности. Чем меньше tx, тем меньшая нагрузка прихо- дится на зерно, тем выше его стойкость, тем менее глубокими будут риски, оставляемые зерном, т. е. более качественной' будет обработан- ная поверхность. Их экспериментальных и теоретических работ следует, что t 1 увеличивается с увеличением окружной скорости заготовки, поперечной подачи, расстояния между абразивными зернами и умень- шается с увеличением окружной скорости круга, диаметра заготовки (при постоянной окружной скорости ее) и диаметра шлифовального круга.
Из этого следует, в частности что для увеличения стойкости круга и получения более чистой обработанной поверхности (что получается при малых t 1) необходимо v 3 уменьшить, a vK увеличить. Но уменьшение окружной скорости заготовки приводит к увеличению машинного вре- мени (снижению производительности), а потому очень низкое значение v 3 невыгодно; повышенное же значение v 3 приводит к увеличению износа круга (снижению стойкости).
Кроме того, с уменьшением у" возрастает время контакта между шли- фовальным кругом и деталью, что приводит к повышению температуры шлифования и может вызвать прижоги обработанной поверхности; с увеличением же v t возрастают центробежные силы и амплитуда виб- раций, что может привести к «дробленой» (некачественной) обработан-
462
ной поверхности. Поэтому о, должна быть в определенных преде- лах (см. [128]).
Скорость вра ш, е н и я шлифовального круга выгодно брать всегда возможно наибольшей, что ограничивается, однако, прочностью круга, зависящей, в свою очередь, в основном от рода связки и формы круга. Окружные скорости шлифовальных кру- гов па обычной керамической связке при работе с автоматической пода- чей 30 — 35 м/сек, на бакелитовой связке 35— 40 м/сек. Шлифовальные круги на специальных высокопрочных керамических связках дают возможность работать со скоростью вращения шлифовального круга 50 м/сек и выше (скоростное шлифование).
Машинное время при наружном круглом шлифова- нии в центрах методом продольной подачи подсчитывается по формуле.
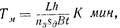
где L — длина шлифования в мм;
h — припуск на сторону в мм;
п3, — число оборотов заготовки в минуту;
s д — долевая подача (в долях ширины круга за один оборот заготовки);
В — ширина круга в мм; t — глубина резания (поперечная подача) на каждый ход в мм;
К — коэффициент точности (коэффициент выхаживания), равный при черновом шлифовании 1,1; при чистовом— 1,4. Силы (рис. 388) Рz, Py, и Рx. по величине небольшие. Наибольшей из сил является радиальная сила Р,., отжимающая шлифовальный круг от заготовки. Большее значение силы Ру по отношению к танген- циальной силе Р. объясняется тем, что внедрение зерен в обрабатывае- мую заготовку затруднено наличием неправильной их геометрической формы и округленных вершин, вы- зывающих отрицательное значение пе- реднего угла. Сила Py = (1,5 ¸ 3) Р., причем это соотношение тем боль- ше, чем больше поперечная подача и окружная скорость вращения Заготовки. Рис 388 Силы при наружном
Теоретически и эксперимепталь- шлифомшш
но установлено, что сила Р- увели- чивается с увеличением v 3 s, t и уменьшается с увеличением vK.
Так как vK значительно больше v 3 (v к / v 3 = 60 ¸ 100), то мощность, затрачиваемая на вращение шлифовального круга, значительно больше мощности N3, затрачиваемой на вращение заготовки, а потому мощность N, обычно редко подсчитывается. В практике для расчета мощности, затрачиваемой на резание (или мощности на вращение шлифовального
463
круга), при наружном круглом шлифовании методом продольной подачи (с поперечной подачей на каждый ход стола), пользуются фор- мулой

Формула приведена для ширины круга В = 40 ¸ 63 мм, твердо- стью СМ1 — СМ2, при диаметре заготовки 40—63 мм. Для других условий обработки см. в литературе [1281.
По мощности Npe 3 может быть определена сила Р/.

Необходимая (расчетная) мощность электродвигателя станка

Для осуществления шлмфования вдоль всей: длины заготовки она имеет продоль- ную подачу, получающуюся от ведущего круга, установленного для этой цели под некоторым углом наклона = 1 ¸ 4,5°. Скорость ведущего круга v в.к. расклады- вается на скорость v 3 (скорость вращения заготовки) и на скорость продоль- ной подачи vs. С этой скоростью vs и осуществляется перемещение заго- товки вдоль кругов 1.
§ 8. ВНУТРЕННЕЕ КРУГЛОЕ ШЛИФОВАНИЕ
При внутреннем круглом шлифовании, применяемом для обработки отверстий, шлифовальный круг находится в отверстии заготовки (рис. 390), а потому DK < D3. Шлифовальный круг и заготовка вращаются обычно в разные стороны. Кроме вра- щательного движения, круг совершает возвратно-поступательные движения вдоль оси отверстия заготовки (продольная подача) и движение «на глубину резания» (поперечная подача t), которое осуществляется в конце двойного продоль- ного хода.
Схема работы, показанная на рис. 390, а, применяется при обработке относи- тельно небольших заготовок. При шлифовании же отверстий у тяжелых и громозд- ких заготовок, закрепление и вращение которых затруднительно, применяют станки
§ 7. БЕСЦЕНТРОВОЕ НАРУЖНОЕ КРУГЛОЕ ШЛИФОВАНИЕ
При бесцентровом шлифовании на проход заготовка 1 (рис. 339), опираясь на упор (нож) 2, пропускается между шлифовальным 3 и ведущим 4 (регулирующим) кругами, установленными на расстоянии, которое меньше диаметра заготовки на вели- чину слоя ~ 2 t, снимаемого за один проход. Круги вращаются по часовой стрелке,
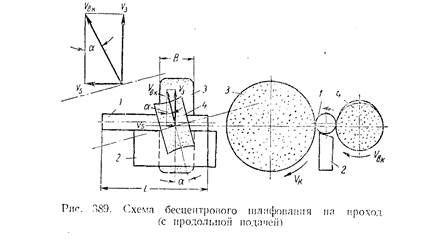
я заготовка, получающая вращение от ведущего круга и имеющая, применю, ту же окружную скорость (10-90 м/мин), против часовой стрелки. В нолях 'повышении трепня между ведущим кругом и заготовкой ведущий круг делается на вулканитовой связке, достаточно твердым (СТЗ-Т1) и мелкозернистым (зернистость 16-10). Наряду с вулканитовой связкой применяется и бакелитовая. Шлифовальный круг (на керамической связке) по отношению к ведущему кругу вращается со значительно большей скоростью (30—35 м/ сек) и осуществляет процесс резания.
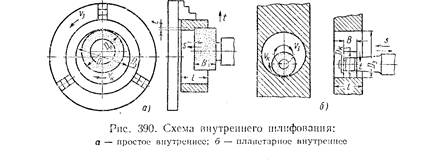
с планетарным движением шпинделя (рис. 390, б). В последнем случае заготовка неподвижна, а круг совершает не только вращательное движение вокруг своей оси vK, но одновременно и круговое движение вокруг оси шлифуемого отверстия; скорость движения вокруг оси заготовки представляет собой как бы скорость вращения за- готовки v 3 в первой схеме. Кроме этих двух движений, как и в первом случае, круг имеет продольную s и поперечную t подачи.
На рис. 391 видно, что при прочих одинаковых условиях (I, DK, D 3) дуга со- прикосновения круга с заготовкой при круглом внутреннем шлифовании А В больше дуги соприкосновения при круглом наружном шлифовании A 1 B 1. Большим будет и число зерен, одновременно участвующих в работе, а потому глубина резания, приходящаяся на одно зерно, при круглом внутреннем шлифовании меньше, чем глубина резания, приходящаяся па одно зерно при круглом наружном шлифовании.
Диаметр шлифовального круга DK берегся в зависимости от диаметра шлифуе- мого отверстия D 3; Dk = (0,75 ¸ 0,95) D3 причем, чем меньше диаметр отверстия, тем больше переходной коэффициент. Ширина шлифовального круга В» 16 ¸- ¸fJO мм, н в диапазоне длины обрабатываемого отверстия l = '25 ¸ 75 мм В < l на 10-15 ММ.
В целях повышения интенсивности охлаждения и сня'.нпною лим повышения производительности (на 10—2 О%), уменьшения шероховатости обработанной no-
Подробнее см. литературу [32].
При шлифовании торцом круга вследствие большой площади соприкосновения круга с заготовкой происходит большое тепловыделение, вызывающее прнжог обра-
| верхности (на один класс), во избежание прижогоз и трещин, повышения точности обработки, для уменьшения расхода шлифовальных кругов и резкого улучшения условий труда рабочего-шлифозщика при внутреннем шлифовании можно применять
внутреннее охлаждение через поры шлифоваль- ного круга на керамической связке [130].
Подача жидкости к шлифовальному кругу осуществляется (рис. 392) через сквозное (осевое) отверстие А в шпинделе и радиальные отвер- стия Б и В, просверленные в головке шпинделя

и во втулке, на которой крепится круг. Под давлением центробежной силы, проходя через поры круга, жидкость выходит на периферию круга, т. е. к месту резания, очищая при этом круг от продуктов отхода.
Лучшей жидкостью для внутреннего охлаждения шлифовального круга яв- ляется вода с добавкой небольшого количества кальцинированной соды и мела с эмульсией малой концентрации 1.
ПЛОСКОЕ ШЛИФОВАНИЕ
Плоское шлифование применяют для обработки плоскостей. Этот пр
|