Мы поможем в написании ваших работ!
ЗНАЕТЕ ЛИ ВЫ?
|
Расчет продольных технологических размеров
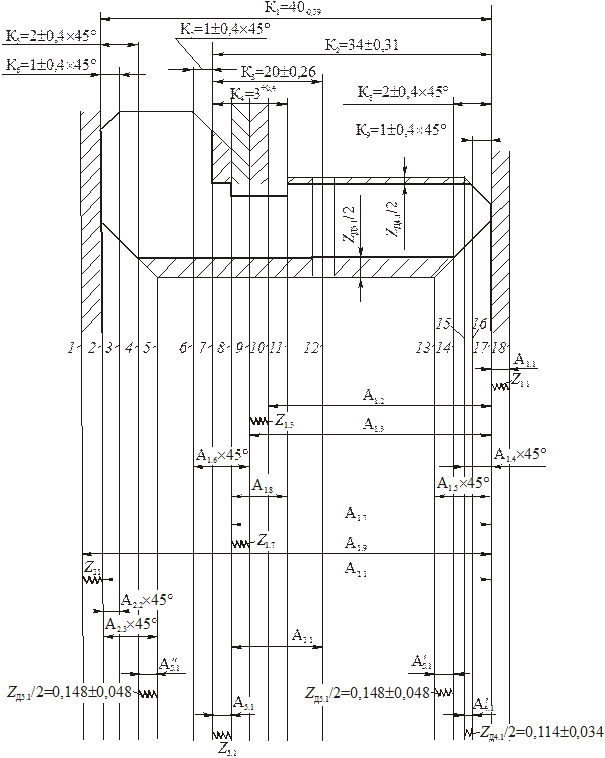
Рис.3.15. Размерная схема технологического процесса изготовления втулки (продольное направление)
Для расчета строится размерная схема технологического процесса изготовления втулки в продольном направлении (рис.3.15) и граф технологических размерных цепей (рис.3.16), облегчающий их выявление. Технологические размерные цепи, формирующиеся при изготовлении втулки, показаны на рис.3.17. В круглых скобках рядом с обозначением технологических размеров указаны допуски, обеспечиваемые спроектированным технологическим процессом, а рядом с обозначением припусков даны их минимальные значения.

Рис.3.16. Граф технологических размерных цепей, формирующихся при изготовлении втулки (продольное направление)
Некоторой особенностью технологического процесса является то, что при шлифовании наружной поверхности Æ мм и шлифовании отверстия Æ мм происходят изменения продольных размеров втулки (размеров фасок). Указанные изменения при угле фасок 45° могут быть приняты равными половине удаляемых при шлифовании припусков на диаметр и (см.рис.3.15). При расчете продольных технологических размеров эти припуски одновременно рассматриваются и как известные (заданные) технологические размеры. Учитывая (см.предыдущий раздел), что =0,2965±0,0965 мм и =0,2285±0,0685 мм, имеем (см.рис.3.15 и 3.17) = =0,14825±0,04825»0,148±0,048 (мм) и = =0,11425±0,03425»0,114±0,034 (мм).
Как видно из рис. 3.17, число составляющих звеньев в подавляющем большинстве технологических размерных цепей не превышает двух и поэтому их расчет будем вести методом максимума-минимума. В технологической размерной цепи № 7 число составляющих звеньев равно четырем и поэтому для ее расчета будем использовать вероятностный метод (в предположении о нормальном распределении технологических размеров и ).
Перед началом расчета технологических размеров необходимо проанализировать технологические размерные цепи, замыкающими звеньями которых являются непосредственно не выдерживаемые конструкторские размеры, и проверить возможность их обеспечения с требуемой точностью. Т.е. при использовании метода максимума-минимума проверить выполнение неравенства (3.7), а при использовании вероятностного метода – неравенства (3.8).
Для размерной цепи № 2 (см.рис.3.17)
.
Для размерной цепи № 3
.

Рис.3.17. Технологические размерные цепи, формирующиеся при изготовлении втулки (продольное направление)
Для размерной цепи № 4
.
Для размерной цепи № 5
.
Для размерной цепи № 7

Для размерной цепи № 8
.
Для размерной цепи № 9
.
Таким образом, убеждаемся, что спроектированный технологический процесс будет обеспечивать требуемую точность всех непосредственно невыдерживаемых конструкторских размеров. Более того, допуски на технологические размеры фасок , , целесообразно расширить с 0,3 мм до 0,6 мм, что позволит снизить затраты на наладку и подналадку станков. Значения расширенных допусков на эти технологические размеры приведены на рис.3.17 около их обозначений в квадратных скобках.
Далее нужно рассмотреть двухзвенные размерные цепи № 1 и № 6 (рис.3.17). Из этих цепей имеем мм и =1±0,4 мм.
Затем можно перейти к анализу двухзвенных цепей № 10 и 14. Из цепи № 10 определяем технологический размер , совпадающий с припуском 
=0,4 (мм);
=0,4+0,3=0,7 (мм);
(мм).
Так как размер получается при механической обработке и не относится ни к отверстиям, ни к валам, то в качестве его номинального значения принято использовать среднее значение. Учитывая это, окончательно запишем =0,55±0,15 мм.
Аналогичным образом из цепи № 14 находим технологический размер , совпадающий с припуском 
=0,2 (мм);
=0,2+0,2=0,4 (мм);
(мм).
Окончательно получим =0,3±0,1 мм (размер не относится ни к отверстиям, ни к валам).
После этого последовательно рассматриваем размерные цепи (рис.3.17) с одним неизвестным технологическим размером и, используя способ средних значений, в итоге определяем его номинальное значение и предельные отклонения.
Из цепи № 2 найдем технологический размер . Для этого подсчитываем его среднее значение
=34-0,3=33,7 (мм).
Окончательно запишем =33,7±0,15 мм (размер не относится ни к отверстиям, ни к валам).
Из цепи № 3 аналогично найдем технологический размер . Его среднее значение составит
=20-0,3=19,7 (мм).
Окончательно запишем =19,7±0,075 мм (размер не относится ни к отверстиям, ни к валам).
Из цепи № 4 определим технологический размер . Среднее значение этого размера будет равно
=3,2-0,3=2,9 (мм).
Таким образом, получим =2,9±0,06 мм. Так как этот размер относится к отверстиям, то окончательно мм.
Из цепи № 5 подсчитаем технологический размер . Его среднее значение составит
=2+0,148=2,148 (мм).
Предварительно запишем =2,148±0,3 мм. После округления номинального значения получим =2,15±0,3 мм (размер не относится ни к отверстиям, ни к валам).
Из цепи № 8 найдем технологический размер . Среднее его значение определится как
=2+0,148=2,148 (мм).
Предварительно запишем =2,148±0,3 мм. После округления номинального значения =2,15±0,3 мм (размер не относится ни к отверстиям, ни к валам).
Из цепи № 9 определим технологический размер . Его среднее значение найдется так:
=1+0,114=1,114 (мм).
Предварительно запишем =1,114±0,3 мм. После округления номинального значения примем =1,1±0,3 мм (размер не относится ни к отверстиям, ни к валам).
Из цепи № 12 найдем технологический размер . Для этого сперва подсчитаем
(мм).
Затем определим среднее значение этого технологического размера
=33,7-0,5=33,2 (мм).
Окончательно примем =33,2±0,15 мм (размер не относится ни к отверстиям, ни к валам).
Из цепи № 11 аналогично найдем технологический размер . Определим
(мм).
Подсчитаем
=33,2-0,61=32,59 (мм).
Предварительно запишем =32,59±0,06 мм. После округления номинального значения окончательно получим =32,6±0,06 мм (размер не относится ни к отверстиям, ни к валам).
Из цепи № 13 определим технологический размер . Для этого подсчитаем
(мм).
Найдем среднее значение размера , которое составит
(мм).
Подсчитаем среднее значение размера 
=39,805+0,525=40,33 (мм).
Предварительно запишем =40,33±0,15 мм. Так как этот размер относится к валам, то примем мм. После округления номинального значения окончательно получим мм.
Наконец, из цепи № 7 найдем технологический размер . Его среднее значение будет равно
=1+0,3+0,3+33,7=1,8 (мм).
Окончательно примем =1,8±0,15 мм (размер не относится ни к отверстиям, ни к валам).
Результаты расчета продольных технологических размеров целесообразно отражать в таблице, аналогичной табл. 3.2 для рассмотренного примера.
Таблица 3.2
Обозначение технологического размера
| Среднее значение технологического размера
| Принятое номинальное значение и предельные отклонения технологического размера
|
| 39,805
| 40-0,39
|
| 0,3
| 0,3±0,1
|
| 33,7
| 33,7±0,15
|
| 19,7
| 19,7±0,075
|
| 2,9
| 2,84+0,12
|
| 0,148
| 0,148±0,048
|
| 2,148
| 2,15±0,3
|
|
| 1±0,4
|
| 33,2
| 33,2±0,15
|
| 1,8
| 1,8±0,15
|
| 0,148
| 0,148±0,048
|
| 2,148
| 2,15±0,3
|
| 0,114
| 0,114±0,034
|
| 1,114
| 1,1±0,3
|
| 0,55
| 0,55±0,15
|
| 32,59
| 32,6±0,06
|
| 40,33
| 40,5-0,3
| Приложение 1
Средние статистические погрешности механической обработки ( )
Вид обработки
| Оборудование и методы обработки
| Способ обеспечения точности
| Рабочий ход
| Шероховатость, мкм
| Точность
|
|
| диаметральных размеров
| до 80
| 80…260
| 260…500
| св.500
|
|
|
|
|
|
|
|
|
|
|
| Токарная обработка
| Токарно-винторезные станки
| По предварительно настроенному лимбу с использованием поворотного резцедержателя
| I
|
| --
| 12…13
| 0,30
| 0,40
| 0,50
| 0,70
| II
| --
| 2,5
|
| 0,12
| 0,20
| 0,25
| 0,30
| Прецизионные токарные станки
| То же
| I
|
| --
| 8…9
| 0,08
| 0,10
| 0,12
| 0,15
| II
| --
| 1,25
| 6…7
| 0,04
| 0,054
| 0,084
| 0,10
| Токарные станки с ЧПУ
| По программе
| I
|
| --
|
| 0,20
| 0,25
| 0,30
| 0,40
| II
| --
| 2,5
|
| 0,12
| 0,17
| 0,20
| 0,25
| Малые карусельные станки
| По предварительно настроенному лимбу
| I
|
| --
| 12…13
| 0,25
| 0,30
| 0,35
| 0,45
| По упорам
| II
| --
| 2,5
| 8…9
| 0,07
| 0,10
| 0,12
| 0,18
| Операционные токарные станки
| По упорам
| I
|
| --
|
| 0,15
| 0,20
| 0,25
| 0,30
| II
| --
| 2,5
| 8…9
| 0,06
| 0,08
| 0,10
| 0,12
| Токарно-револьверные станки
| По упорам от технологических баз
| I
|
| --
| 12…13
| 0,25
| 0,30
| 0,35
| 0,40
| II
| --
| 2,5
|
| 0,15
| 0,17
| 0,20
| 0,25
| От настроечной базы между позициями
| I
|
| --
| 12…13
| 0,30
| 0,35
| 0,40
| 0,45
| II
| --
| 2,5
|
| 0,20
| 0,25
| 0,30
| 0,35
| Между резцами в многорезцовой державке
| I
|
| --
| 12…13
| 0,12
| 0,17
| 0,20
| 0,25
| II
| --
| 2,5
|
| 0,08
| 0,10
| 0,12
| 0,15
|
Продолжение
|
|
|
|
|
|
|
|
|
|
| Токарная обработка
| Многорезцовые токарные полуавтоматы
| По упорам от технологических баз
| I
|
| --
| 12…13
| 0,25
| 0,30
| 0,35
| 0,40
| II
| --
| 2,5
|
| 0,17
| 0,20
| 0,25
|
| Между резцами в одном блоке
| I
|
| --
| 12…13
| 0,15
| 0,20
| 0,25
| 0,30
| II
| --
| 2,5
|
| 0,08
| 0,10
| 0,12
| 0,15
| Между резцами с различных суппортов
| I
|
| --
| 12…13
| 0,20
| 0,25
| 0,30
| 0,35
| II
| --
| 2,5
|
| 0,12
| 0,17
| 0,20
| 0,25
| Гидрокопировальные токарные полуавтоматы
| По копиру от технологической базы
| I
|
| --
| 12…13
| 0,25
| 0,30
| 0,35
| 0,40
| II
| --
| 2,5
|
| 0,15
| 0,17
| 0,20
| 0,25
| Между резцами в одном блоке
| I
|
| --
|
| 0,17
| 0,20
| 0,25
| 0,30
| II
| --
| 2,5
| 8…9
| 0,12
| 0,17
| 0,20
| 0,25
| Между резцами с различных суппортов
| I
|
| --
| 12…13
| 0,20
| 0,25
| 0,30
| 0,35
| II
| --
| 2,5
|
| 0,17
| 0,20
| 0,25
| 0,30
| Вертикальные многошпиндельные токарные полуавтоматы
| По копирам и упорам от технологических баз
| I
|
| --
| 12…13
| 0,20
| 0,25
| 0,30
| --
| II
| --
| 2,5
|
| 0,12
| 0,15
| 0,20
| --
| Между резцами в одном блоке
| I
|
| --
|
| 0,17
| 0,20
| 0,25
| --
| II
| --
| 2,5
| 8…9
| 0,08
| 0,10
| 0,12
| --
| Между резцами с разных суппортов и позиций
| I
|
| --
| 12…13
| 0,20
| 0,25
| 0,30
| --
| II
| --
| 2,5
|
| 0,15
| 0,20
| 0,25
| --
| Автоматы фасонно-продольного точения
| По копирам от настроечной базы
| I
|
| --
|
| 0,12
| 0,17
| --
| --
| II
| --
| 2,5
| 7…8
| 0,08
| 0,10
| --
| --
| Между резцами с различных суппортов
| I
|
| --
|
| 0,10
| 0,12
| --
| --
| II
| --
| 2,5
| 7…8
| 0,06
| 0,08
| --
| --
|
Продолжение
|
|
|
|
|
|
|
|
|
|
| Токарная обработка
| Токарно-револьверные автоматы
| По копирам от настроечной базы (с револьверными головками)
| I
|
| --
|
| 0,12
| 0,17
| --
| --
| II
| --
| 2,5
| 8…9
| 0,08
| 0,10
| --
| --
| От упора или настроечной базы с поперечного суппорта
| I
|
| --
|
| 0,12
| 0,17
| --
| --
| II
| --
| 2,5
| 8…9
| 0,08
| 0,10
| --
| --
| Фасонным резцом
| I
|
| --
|
| 0,02
| 0,04
| --
| --
| Многорезцовой державкой
| I
|
| --
|
| 0,06
| 0,08
| --
| --
| Горизонтальные многошпиндельные токарные автоматы и полуавтоматы
| По копирам от технологической или настроечной базы с продольного суппорта
| I
|
| --
|
| 0,12
| 0,17
| --
| --
| II
| --
| 2,5
| 8…9
| 0,08
| 0,10
| --
| --
| I
|
| --
|
| 0,12
| 0,17
| --
| --
| II
| --
| 2,5
| 8…9
| 0,08
| 0,10
| --
| --
| То же, с независимых инструментальных суппортов
| I
|
| --
|
| 0,15
| 0,20
| --
| --
| II
| --
| 2,5
| 8…9
| 0,10
| 0,12
| --
| --
| По упорам с поперечных суппортов
| I
|
| --
|
| 0,12
| 0,17
| --
| --
| II
| --
| 2,5
| 8…9
| 0,08
| 0,10
| --
| --
| Между резцами в многорезцовой державке
| I
|
| --
|
| 0,10
| 0,12
| --
| --
| II
| --
| 2,5
| 8…9
| 0,06
| 0,08
| --
| --
| Фасонным резцом
| I
|
| --
|
| 0,02
| 0,04
| --
| --
| Сверление
| Обработка глухих отверстий на вертикально-сверлильных и агрегатных станках спиральными сверлами
| По лимбу
| --
|
| --
| 12…13
| 0,15
| 0,20
| 0,30
| --
| По упорам
| --
|
| --
| 12…13
| 0,10
| 0,15
| 0,20
| --
|
Продолжение
|
|
|
|
|
|
|
|
|
|
| Сверление
| То же, ружейными сверлами
| По лимбу
|
|
| --
| 8…10
| 0,15
| 0,20
| 0,30
| --
| По упорам
|
|
| --
| 8…10
| 0,10
| 0,15
| 0,20
| --
| То же, зенкерование черных отверстий
| --
| --
|
| --
| 12…13
| --
| --
| --
| --
| То же, зенкование после сверления
| --
| --
|
| --
| 10…11
| --
| --
| --
| --
| То же, развертывание
| --
| --
| --
| 2,5
| 6…7
| --
| --
| --
| --
| То же, зенкование
| По упорам
| --
|
| --
| 12…13
| 0,15
| 0,20
| 0,30
| --
| То же, цекование
| По упорам
| --
|
| --
| 12…13
| 0,15
| 0,20
| 0,30
| --
| То же, обработка ступенчатых отверстий комбинированным инструментом
| --
| --
|
| --
| 11…13
| 0,15
| 0,20
| 0,30
| --
| Растачивание
| Растачивание ступенчатых отверстий на горизонтально-расточных станках
| По лимбу
| I
|
| --
|
| 0,15
| 0,20
| 0,25
| --
| II
| --
| 2,5
| 8…9
| 0,10
| 0,15
| 0,20
| --
| Между резцами в одной борштанге
| I
|
| --
|
| 0,10
| 0,12
| 0,15
| --
| II
| --
| 2,5
| 8…9
| 0,05
| 0,08
| 0,10
| --
| Между резцами в одной головке
| I
|
| --
| 8…9
| 0,05
| 0,06
| 0,08
| --
| II
| --
| 1,25
| 6…7
| 0,02
| 0,04
| 0,06
| --
| Между инструментами с разных головок
| I
|
| --
| 8…9
| 0,08
| 0,10
| 0,12
| --
| II
| --
| 1,25
| 6…7
| 0,04
| 0,05
| 0,06
| --
|
Продолжение
|
|
|
|
|
|
|
|
|
|
| Фрезерование
| Фрезерование цилиндрическими фрезами на горизонтальных и универсальных станках
| По установам и упорам
| I
|
| --
| 12…13
| 0,20
| 0,25
| 0,30
| 0,40
| II
| --
| 2,5
|
| 0,12
| 0,17
| 0,20
| 0,25
| III
| --
| 1,25
| 8…9
| 0,06
| 0,08
| 0,12
| 0,15
| Фрезерование торцовыми фрезами на горизонтальных и универсальных станках
| По установам и упорам
| I
|
| --
| 12…13
| 0,20
| 0,25
| 0,30
| 0,40
| II
| --
| 2,5
|
| 0,12
| 0,17
| 0,20
| 0,25
| III
| --
| 1,25
| 7…8
| 0,04
| 0,06
| 0,10
| 0,12
| Фрезерование на двухсторонних карусельных и барабанных станках
| От базы по установам
| I
|
| --
| 12…13
| 0,20
| 0,25
| 0,30
| 0,40
| II
| --
| 2,5
|
| 0,12
| 0,17
| 0,20
| 0,25
| Между фрезами
| I
|
| --
| 12…13
| 0,10
| 0,15
| 0,17
| 0,20
| II
| --
| 2,5
|
| 0,08
| 0,10
| 0,12
| 0,15
| Строгание
| Долбежные станки
| По лимбу
| I
|
| --
| --
| 0,40
| 0,45
| 0,50
| 0,60
| II
|
| --
| --
| 0,20
| 0,25
| 0,30
| 0,40
| Поперечно-строгальные станки
| По лимбу и установам
| I
|
| --
| --
| 0,40
| 0,45
| 0,50
| 0,60
| II
| --
| 2,5
| --
| 0,12
| 0,17
| 0,20
| 0,25
| Продольно-строгальные станки
| По лимбу и установам
| I
|
| --
| --
| 0,20
| 0,25
| 0,30
| 0,40
| II
| --
| 2,5
| --
| 0,12
| 0,17
| 0,20
| 0,25
| Внутреннее протягивание
| --
| I
| --
| 2,5
| 6…7
| --
| --
| --
| --
| Наружное протягивание
| --
| I
| --
| 2,5
| --
| 0,12
| 0,17
| 0,20
| 0,25
|
Продолжение
|
|
|
|
|
|
|
|
|
|
| Шлифование
| Круглошлифовальные станки
| По лимбу и пробным проходам
| Предварит.
| --
| 2,5
|
| --
| --
| --
| --
| Чистовое
| --
| 0,63
| 6…7
| --
| --
| --
| --
| Тонкое
| --
| 0,16
| 5…6
| --
| --
| --
| --
| Торцекруглошлифовальные станки
| По упорам
| Предварит.
| --
| 2,5
|
| 0,15
| 0,17
| 0,20
| 0,25
| Чистовое
| --
| 0,63
| 6…7
| 0,08
| 0,10
| 0,12
| 0,15
| С позиционированием
| Предварит.
| --
| 2,5
|
| 0,10
| 0,12
| 0,15
| 0,17
| Чистовое
| --
| 0,63
| 6…7
| 0,06
| 0,08
| 0,10
| 0,12
| Внутришлифовальные станки
| По лимбу, упорам и пробным проходам
| Предварит.
| --
| 2,5
|
| 0,20
| 0,25
| 0,30
| --
| Чистовое
| --
| 0,63
| 6…7
| 0,12
| 0,17
| 0,20
| --
| Тонкое
| --
| 0,16
| 5…6
| 0,06
| 0,08
| 0,12
| --
| Плоскошлифовальные станки
| По упорам, лимбу и пробным проходам
| Предварит.
| --
| 2,5
| --
| 0,15
| 0,20
| 0,25
| --
| Чистовое
| --
| 0,63
| --
| 0,08
| 0,10
| 0,12
| --
| Тонкое
| --
| 0,16
| --
| 0,05
| 0,08
| 0,10
| --
| Безцентровошлифовальные станки
| По упорам
| Предварит.
| --
| 2,5
| 8…9
| --
| --
| --
| --
| Чистовое
| --
| 1,25
| 6…7
| --
| --
| --
| --
|
Продолжение
|
|
|
|
|
|
|
|
|
|
| Доводка
| Хонингование
| --
| Предварит.
| --
| 0,32
| --
| Точность обработки примерно соответствует точности предварительно выполненных размеров
| Чистовое
| --
| 0,32
| 5…6
| Суперфиниширование
| --
| Предварит.
| --
| 0,32
| --
| Чистовое
| --
| 0,08
| --
| Доводка (притирка)
| --
| Предварит.
| --
| 0,32
| --
| Тонкое
| --
| 0,08
| --
| Многопроходная размерная притирка
| --
| --
| --
| 0,08
| Точнее 3
|
Приложение 2
Шероховатость и величина дефектного слоя поверхностей, полученных различными методами
Метод обработки
| Шероховатость , мкм
| Дефектный слой, мкм
| Литье в песчанно-глинистую форму при ручной формовке
| 100…500
| 200…600
| Литье в песчанно-глинистую форму при машинной формовке
| 80…300
| 150…400
| Литье в металлические формы
| 100…200
| 100…300
| Центробежное литье
| 40…100
| 100…200
| Литье в оболочковые формы
| 20…80
| 150…250
| Литье по выплавляемым моделям
| 10…40
| 80…150
| Литье под давлением
| 10…40
| 80…150
| Ковка
| 300…500
| 400…600
| Штамповка обычной точности
| 100…250
| 200…400
| Штамповка повышенной точности
| 80…200
| 150…300
| Прокат горячекатанный обычной точности
| 80…150
| 100…150
| Прокат повышенной точности
| 50…100
| 80…150
| Прокат холоднотянутый калиброванный
| 40…80
| 50…100
| Рубка на прессах и ножницах
| 100…300
| 100…150
| Разрезание пилами на станках
| 80…160
| 100…150
| Точение черновое
| 80…150
| 50…100
| Точение получистовое
| 30…50
| 40…60
| Точение чистовое
| 15…25
| 20…30
| Точение тонкое
| 6…10
| 10…20
| Строгание предварительное
| 80…150
| 100…150
| Строгание окончательное
| 15…25
| 20…30
| Сверление
| 80…150
| 50…100
| Сверление глубокое
| 15…30
| 25…50
| Зенкерование черновое
| 30…50
| 40…50
| Зенкерование чистовое
| 20…30
| 30…40
| Развертывание предварительное
| 10…20
| 15…25
| Развертывание чистовое
| 6…10
| 5…10
| Растачивание алмазное
| 3,2…6,3
| 4…10
| Фрезерование обдирочное
| 80…150
| 80…100
| Фрезерование чистовое
| 20…50
| 40…60
| Фрезерование тонкое
| 3,2…6,3
| 10…30
| Протягивание черновое
| 6…10
| 10…20
| Протягивание чистовое
| 3,2…6,3
| 5…10
| Растачивание черновое
| 40…80
| 50…100
| Растачивание чистовое
| 10…20
| 15…30
| Шлифование черновое
| 20…40
| 30…50
| Шлифование чистовое
| 5…10
| 15…25
| Шлифование тонкое
| 1,5…3,5
| 5…10
| Хонингование
| 1…3
| 3…6
| Суперфиниш
| 0,2…0,8
| 3…5
| Притирка предварительная
| 0,8…3,2
| 3…5
| Притирка окончательная
| 0,05…0,4
| 3…5
| Полирование
| 0,05…0,4
| 2…3
| Приложение 3
Точность геометрической формы и расположения поверхностей при механической обработке
Вид обработки
| Метод обработки и оборудование
| Рабочий ход
| Вид погрешности
| Величина погрешности (мкм) в зависимости от номинального размера, мм
| до 10
| 10…50
| 50…100
| 160…300
| 300…500
| св. 500
|
|
|
|
|
|
|
|
|
|
| Токарная
| Токарные, револьверные, карусельные, многошпиндельные и прочие токарные станки
| Первый
|
| 6…16
| 10…30
| 25…50
| 40…80
| 60…120
| 100…250
|
| 10…24
| 20…40
| 30…60
| 50…100
| 80…150
| 150…300
|
| 25…60
| 40…120
| 100…200
| 150…360
| 300…450
| 400…1000
|
| 40…80
| 50…100
| 80…120
| 100…200
| 150…250
| 200…400
| Второй
|
| 2,5…6
| 4…16
| 10…25
| 16…35
| 25…50
| 40…100
|
| 2…10
| 6…16
| 8…20
| 10…25
| 12…30
| 16…50
|
| 6…16
| 10…40
| 16…50
| 25…80
| 40…100
| 80…300
|
| 20…30
| 30…60
| 40…80
| 60…100
| 80…160
| 100…500
| Третий
|
| 0,6…1
| 1…2,5
| 1,6…6
| 4…10
| 8…16
| 10…40
|
| 1,2…3
| 2,5…4
| 3…8
| 5…10
| 7…12
| 10…25
|
| 1,6…4
| 4…10
| 6…16
| 8…20
| 10…30
| 16…100
|
| 5…16
| 8…20
| 10…25
| 12…30
| 16…40
| 20…80
|
Продолжение
|
|
|
|
|
|
|
|
|
| Сверление растачивание
| Сверление спиральными сверлами
| Один
|
| 12…25
| 16…40
| 20…50
|
|
|
|
| 25…60
| 40…120
| 80…250
| 160…400
|
|
| Сверление ружейными сверлами
| Один
|
| 2…5
| 4…10
| 8…16
| 12…20
|
|
|
| 2,5…6
| 4…16
| 10…25
| 25…50
|
|
| Зенкерование
| Один
|
| 2…8
| 6…12
| 8…20
|
|
|
|
| 4…10
| 8…16
| 10…25
| 16…40
|
|
| Развертывание
| Один
|
| 1,5…2
| 2,5…8
| 5…10
| 8…16
|
|
|
| Может увеличиваться на 10% по сравнению с исходным
| Алмазное растачивание
| Один
|
| 0,4…1
| 0,8…2
| 1,2…4
| 2,5…8
| 6…10
|
|
| 0,5…1,2
| 1…2,8
| 2…5
| 4…10
| 6…16
| 10…20
|
| 0,6…1,6
| 1,2…4
| 2,5…6
| 4…8
| 6…10
| 8…16
|
| 2,5…6
| 3…8
| 5…10
| 6…12
| 8…16
| 10…20
| Фрезерование
| Вертикальные, горизонтальные и продольно-фрезерные станки
| Первый
|
| 6…16
| 10…20
| 16…40
| 28…80
| 50…120
| 100…600
|
| 25…60
| 40…120
| 100…250
| 200…360
| 250…450
| 400…1200
| Второй
|
| 1…4
| 2,5…10
| 6…16
| 10…20
| 16…30
| 20…100
|
| 4…10
| 6…30
| 20…60
| 40…80
| 60…120
| 100…400
| Протягивание
| Протягивание и прошивание
| Один
|
| 1,6…4
| 2,5…8
| 6…16
| 8…20
| 10…25
|
|
| 2…5
| 4…8
| 5…12
| 8…16
| 10…20
| 16…30
|
| Может увеличиваться на 30% по сравнению с исходным
|
| Перпендикулярность торцов к оси отверстий 0,15:100
| Продолжение
|
|
|
|
|
|
|
|
|
| Шлифование
| Круглошлифовальные, внутришлифовальные и плоскошлифовальные стаки
| Предварительный
|
| 2,5…6
| 4…10
| 6…16
| 10…25
| 20…40
| 20…100
|
| 1,6…4
| 2,5…8
| 5…12
| 8…16
| 10…20
| 16…40
|
| 4…10
| 8…20
| 16…30
| 20…50
| 30…60
| 50…160
|
| 20…30
| 25…50
| 40…60
| 50…80
| 60…100
| 80…200
| Чистовой
|
| 1…4
| 2,5…8
| 6…12
| 10…20
| 16…25
| 20…60
|
| 0,8…2,5
| 1,6…4
| 2,5…5
| 4…6
| 5…8
| 6…16
|
| 1,6…4
| |
| Поделиться:
|
|