Превращения при отпуске закаленной стали
Похожие статьи вашей тематики
Принципиальное отличие превращений при отпуске закаленной стали — необратимость происходящих изменений. Не существует условий нагрева и выдержки во всем интервале температур отпуска вплоть до критических температур, при которых продукты отпуска могли бы образовать вновь исходную структуру закаленной стали, состоящую из мартенсита и остаточного аустенита. Следовательно, для всего интервала отпуска наибольшим запасом свободной энергии будет обладать структура закаленной стали, а наименьшим — равновесная феррито-карбидная смесь, соответствующая по фазовому составу и. кристаллическому строению условиям, которые описываются диаграммой состояния. Изменение температуры отпуска и продолжительности выдержки при ней определяет пути структурных изменений и возможную степень приближения к состоянию фазового равновесия. Сложность превращений при отпуске обусловливается возможностью частичного или полного протекания процессов диффузии углерода и различных путей структурных изменений в карбидной фазе и железной основе. Последнее осложняется при легировании необходимостью протекания диффузии легирующих элементов для приближения фаз к состоянию равновесия.
Тема №46
ОТЖИГ СТАЛИ
Отжигом называется операция термической обработки, при которой путем нагрева, выдержки при установленных температурах и последующего медленного охлаждения в стали получают устойчивую структуру, свободную от остаточных напряжений. Цель отжига стальных изделий — снять внутренние напряжения, устранить структурную неоднородность, улучшить обрабатываемость резанием и подготовить к последующей термической обработке.
Отжиг стали может быть с фазовой перекристаллизацией: полный, изотермический, на зернистый перлит и диффузионный, а также без фазовой перекристаллизации — рекристаллизационный.
Отжиг включает следующие операции.
1. Нагрев стали до температур, на 20—30° превышающих верхнюю критическую точку АС1, т. е. лежащих выше линии GS, — полный отжиг для доэвтектоидных сталей (рис. 1), или нагрев стали до температур, на 30—40° превышающих нижнюю критическую точку AC1 т. е. расположенных выше линии PSK, — неполный отжиг.
2. Выдержка детали в течение времени, достаточного для равномерного прогрева ее по всему сечению до заданных температур и для завершения всех структурных (фазовых) превращений, которые должны полностью закончиться. Законченность структурных превращений в стали при отжиге составляет цель данной операции: лишь в этом случае свойства стали после отжига существенно улучшаются.
3. Медленное охлаждение стали от температур отжига со скоростью, меняющейся (от 10 до 100° в час) в зависимости от марки стали, формы и назначения детали.
Полному отжигу подвергают обычно доэвтектоидные стали, нагревая их до температур выше линии GS, выдерживая при них в течение 1/4 продолжительности нагрева и медленно охлаждая вместе с печью до 600 — 400° С. Углеродистые стали охлаждают со скоростью 100—150° в час, легированные — со скоростью 30—50° в час. Полный отжиг сопровождается фазовой перекристаллизацией, в результате чего крупнозернистая сталь получает мелкозернистую структуру, освобождается от внутренних напряжений, становится мягкой и вязкой. Для отжига изделия упаковывают в ящики, трубы или реторты, которые затем наполняют песком, чугунной стружкой или углем, чтобы предохранить поверхность изделий от обезуглероживания и окисления. Наилучшие результаты дает применение защитной атмосферы. Отжиг в защитной атмосфере называют светлым, так как при этом способе обезуглероживания и окисления почти не бывает и поверхность изделий остается относительно светлой.
Неполный отжиг является разновидностью отжига перекристаллизации. При неполном отжиге сталь нагревают до температуры, на 30—40° превышающей нижнюю критическую точку АС1 (см. рис. 1), т. е. до 750—760° С.
Замедленное охлаждение или длительная выдержка стали при температурах 680—750° С способствует образованию крупнопластинчатого перлита, облегчающего обрабатываемость стали резанием. Для мягких доэвтектоидных сталей, содержащих до 0,4—0,5% углерода, этот вид отжига применяют редко, так как они и без отжига достаточно хорошо обрабатываются резанием. Для инструментальных сталей, особенно заэвтектоидных, неполный отжиг является единственным видом отжига. Он способствует снятию внутренних напряжений и улучшению обрабатываемости резанием.
Отжигу на зернистый перлит подвергают эвтектоидные и заэвтектоидные стали. Для отжига сталь нагревают на 20—30° выше критической точки ACi(см. рис. 54) и после выдержки при рабочей температуре в течение 3—5 часов медленно охлаждают (со скоростью 30—50° в час) до 650—600° С. В результате длительной выдержки пластинчатый перлит превращается в зернистый; это явление называется сфероидизацией (округлением). Высокоуглеродистые инструментальные стали, содержащие более 0,65% углерода, со структурой зернистого перлита хорошо обрабатываются резанием и лучше поддаются закалке; они обладают меньшей склонностью к образованию трещин и короблению. В некоторых случаях, чтобы ускорить процесс сфероидизации перлита, нагрев и охлаждение повторяют несколько раз. Такой отжиг называется м а я т н и к о в ы м, или цикличным. При цикличном отжиге инструментальную сталь нагревают до 730—750° С и медленно охлаждают до 650° С; процесс повторяют несколько раз. Все заэвтектоидные (инструментальные) стали отжигают на зернистый перлит.
Изотермический отжиг заключается в нагреве стали выше критической точки АС3 и выдержке при этой температуре в течение времени, необходимого для полного и равномерного прогрева. Затем сталь относительно быстро охлаждают до температуры ниже Ar1(650—700° С). При этой постоянной (изотермической) температуре сталь выдерживают определенное время, необходимое для полного распада аустенита с образованием перлита (в доэвтек-тоидной стали — феррита и перлита), и затем охлаждают на воздухе. Изотермический отжиг имеет почти вдвое более короткий цикл,
чем обычный отжиг.
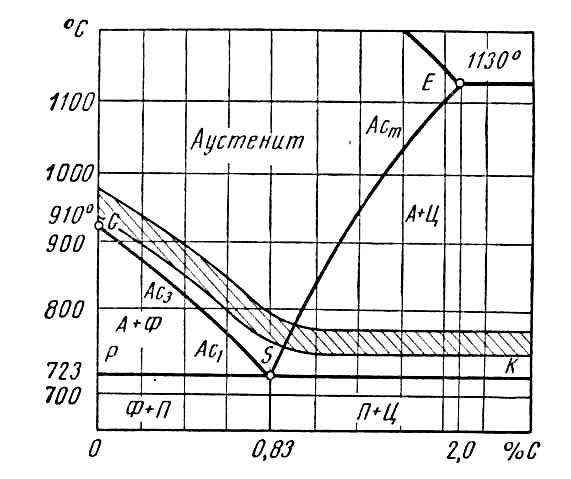
Рис. 2. Интервал закалочных температур углеродистой стали
Преимущества изотермического отжига —однородность структуры и ускорение процесса, особенно при отжиге легированной стали. Для сталей, содержащих большое количество хрома, никеля и других элементов, только изотермический отжиг позволяет добиться превращения весьма устойчивого аустенита в перлит и феррит и обеспечить хорошую обрабатываемость стали режущим инструментом. Диффузионный отжиг применяют для слитков и крупных отливок, чтобы выравнять (путем диффузии) химический состав стали, имеющий внутрикристаллическую ликвацию. Сталь нагревают до 1050—1150° С, выдерживают при этой температуре 10—15 часов и затем медленно охлаждают до 600 — 550° С. Диффузионный отжиг приводит к росту зерна стали; этот дефект устраняют повторным отжигом на мелкое зерно (полный отжиг). Сталь, прошедшая гомогенизацию, обладает более высокими меха* ническими свойствами; особенно повышается ударная вязкость.
Рекристаллизационным отжигом называется отжиг стали, прошедшей холодную прокатку, волочение или холодную штамповку, с выдержкой при температуре 680—700° С и последующим охлаждением. Этой температуры достаточно для того, чтобы возвратить стали свойства, которые она имела до холодной обработки давлением. В результате такого отжига понижается твердость и прочность, но повышаются показатели пластичности — относительное удлинение, ударная вязкость.
НОРМАДИЗАЦИЯ СТАЛИ
Нормализацией называется нагрев стали выше линии GSE на 30—50° (см. рис. 1) свыдержкой при этой температуре и последующим охлаждением на воздухе. Нормализацию применяют для устранения внутренних напряжений и наклепа, повышения механических свойств стали.
Слово «нормализация» указывает на то, что сталь после этой операции получает нормальную, однородную, мелкозернистую структуру; перлит приобретает тонкое строение. Нормализации подвергают отливки и поковки. В настоящее время нормализация распространена в машиностроении больше, чем отжиг, так как она более производительна и дает лучшие результаты.
Тема №47
Закалкой называется операция термической обработки, состоящая из нагрева до температур выше верхней критической точки AC3 для доэвтектоидной стали и выше нижней критической точки АС1
для заэвтектоидной стали и выдержки при данной температуре с последующим быстрым охлаждением (в воде, масле, водных растворах солей и пр.).
В результате закалки сталь получает структуру мартенсита и благодаря этому становится твердой.
Закалка повышает прочность конструкционных сталей, придает твердость и износостойкость инструментальным сталям.
Режимы закалки определяются скоростью и температурой нагрева, длительностью выдержки при этой температуре и особенно скоростью охлаждения.
Тема №48
ОТПУСК ЗАКАЛЕННЫХ СТАЛЕЙ
Образующийся при закалке стали мартенсит, представляет собой неустойчивую структуру, характеризующуюся высокой твёрдостью, хрупкостью и высоким уровнем внутренних напряжений. По этой причине закалённую сталь обязательно подвергать отпуску. Отпуском называют термическую операцию, заключающуюся в нагреве закалённой стали до температур, не превышающих точку Аc1 (т.е. не выше линии PSK), выдержке и последующем охлаждении чаще всего на воздухе. Отпуск является окончательной операцией термической обработки, в результате которой сталь получает требуемые механические свойства. Кроме того, отпуск частично или полностью устраняет внутренние напряжения, возникшие при закалке. Окончательные свойства стали в большей степени зависят от температуры отпуска. Различают три вида отпуска стали в зависимости от температуры нагрева. Низкий (низкотемпературный отпуск) проводят при температурах не выше 250...300°С. При таких температурах происходит частичное обезуглероживание мартенсита и выделение из него некоторого количества избыточного углерода в виде частиц е - карбида железа. Образующаяся структура, состоящая из частичного обезуглероженного мартенсита и е-карбидов, называется отпущенным мартенситом. Выход некоторого количества углерода из решетки мартенсита способствует уменьшению её искажения и снижению внутренних напряжений. При таком отпуске несколько повышается прочность и вязкость без заметного снижения твёрдости. В целом изменение свойств при низком отпуске незначительно. Так закалённая сталь с содержанием углерода 0,5... 1,3 % после низкого отпуска сохраняет твёрдость в пределах 58...63 HRC, а следовательно, обладает высокой износостойкостью. Однако такая сталь не выдерживает значительных динамических нагрузок. Низкому отпуску подвергают режущий и мерительный инструмент из углеродистых и низколегированных сталей, работающий без значительного разогрева рабочей части, а такие детали, прошедшие поверхностную закалку или цементацию. Цель такого отпуска - некоторое снижение внутренних напряжений. Средний (средне-температурный) отпуск выполняют при температурах 350...500°С и применяют преимущественно для рессор, пружин, некоторых видов штампов. При таких температурах происходит дальнейшее обезуглероживание мартенсита, приводящее к его превращению в обычный а-раствор,т.е. в феррит. Одновременно происходит карбидное превращение по схеме; Fe2C ® Fе3С, В результате образуется феррито-цементитная смесь, называемая троститом отпуска. Наблюдается снижение твёрдости до величины 40...50 HRC, а также снижение внутренних напряжений. Такой отпуск обеспечивает высокий предел упругости и предел выносливости, что позволяет применять его для различных упругих элементов. Высокий(высокотемпературный) отпуск проводят при 500...600°С. Структурные изменения при таких температурах заключаются в укрупнении (коагуляции) частиц цементита. В результате этого образуется феррито-цементитная смесь, называемая сорбитом отпуска. Также, как и тростит отпуска, эта структура характеризуется зернистым строением в отличии от пластинчатых структур тростита и сорбита закалки. Твёрдость стали после высокого отпуска снижается до 25,,,35 HRC, Однако уровень прочности при этом ещё достаточно высок, В то же время обеспечивается повышенная пластичность и особенно ударная вязкость, практически полностью снимаются внутренние напряжения, возникшие при закалке. Таким образом, высокий отпуск на сорбит обеспечивает наилучший комплекс механических свойств, позволяющий применять его для деталей, работающих в условиях динамических нагрузок. Такой же отпуск рекомендуется для деталей машин из легированных сталей, работающих при повышенных температурах. Термическую обработку, состоящую из закалки на мартенсит и последующего высокого отпуска на сорбит, называют термическим улучшением. Вообще термическому улучшению подвергают детали из среднеуглеродистых (0,3...0,5%С) конструкционных сталей, к которым предъявляют высокие требования по пределу текучести, пределу выносливости и ударной вязкости. Однако износостойкость улучшенной стали вследствие её" пониженной твёрдости невысока. Скорость охлаждения после отпуска оказывает большое влияние на величину остаточных напряжений. Чем медленнее охлаждение, тем меньше остаточные напряжения. Так охлаждение на воздухе даёт напряжения в 7 раз меньше, а охлаждение в масле в 2,5 раза меньше по сравнению с охлаждением в воде. По этой причине изделия сложной формы во избежание их деформации после отпуска следует охлаждать медленно (на воздухе), а детали из некоторых легированных сталей, склонных к отпускной хрупкости, рекомендуется охлаждать в масле (иногда даже в воде). Легирующие элементы, входящие в состав легированных сталей, особенно такие, как Мо5 W, Cr, Ti, V и Si, сильно тормозят диффузионные процессы, происходящие при отпуске закалённой стали. Поэтому после отпуска при одинаковой температуре легированная сталь сохраняет более высокую твёрдость и прочность. Это делает легированные стали более теплостойкими, способными работать при повышенных температурах.
Тема №49
ПОВЕРХНОСТНАЯ ЗАКАЛКА
Поверхностная закалка применяется с целью получения высокой твердости в поверхностном слое детали с сохранением вязкой сердцевины.
Основные параметры при закалке — температура нагрева и скорость охлаждения. Температуру нагрева для сталей определяют по диаграммам состояния, скорость охлаждения — по диаграммам изотермического распада аустенита.
Доэвтектоидные стали нагревают до температуры выше критической точки Ас3 на 30-50 °С. Если такие стали нагреть до температуры между критическими точками Ас1 и Ас3 и охладить, то в структуре закаленной стали, кроме мартенсита, будет присутствовать феррит, что существенно ухудшает свойства. Такая закалка называется неполной. Заэвтектоидные стали при закалке нагревают до температуры Ас1+ (40,60 °С). После охлаждения с таких температур получают структуру мартенсита с включением вторичного цементита, который повышает твердость и износостойкость режущего инструмента. Если заэвтектоидную сталь нагреть выше критической точки Аст, то после закалки получится дефектная структура грубоигольчатого мартенсита. Время нагрева зависит от размеров детали и теплопроводности стали, и его обычно определяют экспериментально. Для определения времени нагрева в справочниках приведены также полуэмпирические формулы. В таблице 1 приведены значения скорости охлаждения стали в различных средах.
Тема №50
Химико-термической обработкой называют процесс изменения химического состава, структуры и свойств поверхностных слоев и металла.
Такая обработка применима к деталям, от которых требуется твердая и износоустойчивая поверхность при сохранении вязкой и достаточно прочной сердцевины, высокая коррозионная стойкость, высокое сопротивление усталости.
Химико-термическая обработка стали основана на диффузии (проникновении) в атомно-кристаллическую решетку железа атомов различных химических элементов при нагреве стальных деталей в среде, богатой этими элементами.
Наиболее распространенными видами химико-термической обработки стали являются: цементация — насыщение поверхности стальных деталей углеродом; азотирование — насыщение поверхности стальных деталей азотом; цианирование — одновременное насыщение поверхности стальных деталей углеродом и азотом.
Кроме этих основных видов химико-термической обработки, в промышленности применяют также поверхностное насыщение стали металлами: алюминием, хромом, кремнием и др. Процесс этот называется диффузионной металлизацией стали.
Цементация.
Цементация — процесс поверхностного насыщения стальных деталей углеродом. Цель цементации получить детали с вязкой сердцевиной и твердой поверхностью. Такие детали во время работы не разрушаются от ударов и хорошо сопротивляются истиранию. Цементации подвергают детали из углеродистой и легированной стали с содержанием углерода от 0,08 до 0,35%. Богатые углеродом смеси, применяемые для цементации, — карбюризаторы — могут быть твердыми, жидкими и газообразными.
Цементация в твердом карбюризаторе производится путем нагрева деталей, упакованных в железные ящики (рис. 68) вместе с карбюризатором.
Карбюризатор представляет собой порошкообразную смесь, состоящую из древесного угля (70%), углекислого бария ВаСO3 (20—25%) и углекислого кальция СаСO3 (3—5%).
Температуру цементации принимают на 20—50° выше точки АC3. Температура до 920—930° С позволяет почти в два раза сократить длительность процесса без ухудшения механических свойств стали. Насыщение стали углеродом происходит путем непосредственного соприкосновения частиц угля с поверхностью стальных деталей в газовой среде, которая служит передатчиком углерода. При правильном подборе карбюризатора содержание углерода в поверхностном слое не превышает 1,0—1,10%, что можно считать нормальным. Продолжительность цементации — от 5 до 15 и более часов в зависимости от глубины науглероживания и марки стали. Для цементации могут быть использованы самые разнообразные печи — камерные, непрерывного действия, с вращающейся ретортой, обогреваемые мазутом, газом или электрические.
Жидкостной цементации подвергают мелкие изделия; их погружают в расплавленные соляные ванны, состоящие из 75-85% Na2CO3 (сода), 10-15% NaCl (поваренная соль) и 6—10% SiC (карбид кремния).
Газовая цементация в окиси углерода СО впервые была применена П. П. Аносовым. Сущность ее состоит в том, что цементируемые изделия нагревают и выдерживают при температуре 920—950° С в печи, куда в течение всего процесса непрерывно подается цементирующий газ. Для этой цели используют природный газ, состоящий в основном из метана СН4, или искусственные газы, получаемые в результате разложения (пиролиза) нефтепродуктов— керосина, различных масел, бензола, пиробензола и др. Основной составляющей искусственных газов также является метан СН4.
Детали загружают в муфельные печи, в которые вводят цементирующие газы. При газовой цементации продолжительность процесса сокращается в 2—2,5 раза. Так, для получения цементованного слоя глубиной 1,0—1,2 мм требуется затратить 4—5 часов. Кроме этого, газовая цементация обладает и другими преимуществами: возможностью регулировать процесс за счет изменения количества и химического состава подаваемого газа: отсутствием громоздкого оборудования и угольной пыли; возможностью производить закалку непосредственно из печи. Процесс газовой цементации более экономичен.
Азотирование.
Азотированием называется насыщение поверхности стали азотом. Основоположником азотирования стали является русский ученый проф. Н. П. Чижевский, который впервые исследовал и применил этот процесс. Для азотирования используют аммиак NH3. Сущность азотирования заключается в том, что аммиак при температуре 500—750° С разлагается на азот и водород, и активные атомы азота (атомарный азот), диффундируя в поверхностный слой, сообщают поверхности стали большую твердость, не влияя на механические свойства сердцевины деталей. В промышленности для изготовления деталей, подлежащих азотированию, в настоящее время широко применяют сталь марки 35ХМЮА или ее заменитель 35ХВФЮА. После окончательной механической обработки детали закаливают от температуры 960° С с охлаждением в воде или в масле и подвергают отпуску при 600° С также с охлаждением в воде или в масле. Затем детали азотируют. Продолжительность азотирования от 12 до 60 и даже до 90 часов в зависимости от требуемой толщины азотированного слоя и характера процесса.
Длительность выдержки деталей в потоке аммиака в печи влияет на глубину азотированного слоя. В среднем при 500° С азот за каждые 10 часов диффундирует на глубину 0,1 мм. На практике для сокращения времени азотирования процесс ведут путем ступенчатого нагрева: вначале в течение 12—15 часов при температуре 500— 520° С; затем температуру поднимают до 550—600° С и дают выдержку 15—20 часов. При таком режиме длительность процесса удается сократить в 2,0—2,5 раза. В результате азотирования твердость стали достигает НВ 1000—1100; последующей термической обработки не требуется.
Азотирование имеет ряд преимуществ перед цементацией: она дает незначительное изменение размеров деталей, обеспечивает более высокую твердость и износоустойчивость (при нагреве до температуры 500—550° С твердость азотированных деталей не снижается); сообщает деталям хорошую сопротивляемость действию переменных нагрузок, высокий предел выносливости и коррозионную стойкость. Недостаток азотирования — длительность процесса.
Азотирование применяют в машиностроении для получения высокого качества дизельной аппаратуры, измерительного инструмента, зубчатых колес и др.
Цианирование — процесс одновременного насыщения поверхности стали углеродом и азотом для придания ей высокой твердости, сопротивляемости истиранию и коррозионной стойкости.
Одновременное присутствие в среде углерода и азота ускоряет их совместную диффузию в поверхностные слои стали. Такими средами могут быть расплавленные цианистые соли (жидкостное цианирование), науглероживающие и азотирующие газы (газовое цианирование), твердые порошки и пасты (твердое цианирование). Цианированию подвергают углеродистые и легированные стали.
Существует два вида цианирования: высокотемпературное и низкотемпературное.
Высокотемпературное цианирование применяют для деталей из углеродистой и легированной стали с содержанием углерода 0,3—0,4% с целью получения твердого, хороша сопротивляющегося истиранию поверхностного слоя и вязкой сердцевины. Такое цианирование проводится при температурах 780— 930° С, т. е. выше точки ЛГ1, когда сталь находится в состоянии аус-тенита и преобладает процесс насыщения ее углеродом. Этот вид цианирования широко применяют на автомобильных заводах для зубчатых колес и различных мелких деталей.
Низкотемпературное цианирование применяют для инструментов из быстрорежущей стали при температурах 500—600° С, т. е. ниже точки AC1, когда преобладает процесс насыщения стали азотом, с последующим медленным охлаждением цианированного инструмента.
В последнее время на заводах вводится новый процесс цианирования — газовое цианирование, или нитроцементация. Газовое цианирование занимает промежуточное положение между газовой цементацией и азотированием и поэтому иногда называется нитроцементацией.
При газовом цианировании детали нагреваются в смеси газов, содержащих углерод и азот. Для этой цели используют смесь окиси углерода СО и аммиака ΝΗ3. При их химическом взаимодействии образуются активный углерод и азот. В последнее время газовое цианирование (нитроцементацию) производят в печах, оборудованных для газовой цементации, путем введения в рабочее пространство этих печей бензола или пиробензола.
Диффузионная металлизация.
Кроме указанных процессов насыщения поверхности стали углеродом и азотом, широко применяют насыщение стали алюминием, хромом, кремнием и др. Этот процесс применяют главным образом с целью получения стальных деталей, устойчивых против разъедания щелочами и кислотами, а также с целью повышения устойчивости стали против окисления горячими печными газами, т. е. против окалинообразования.
Алитированием называется процесс насыщения поверхности стальных и чугунных деталей алюминием с целью повышения их жаростойкости. Алитированию подвергают главным образом малоуглеродистые стали. Процесс алитирования может происходить в твердой, жидкой и газообразной средах. Наиболее распространен способ алитирования в твердой среде. Детали, подлежащие алитированию, укладывают в железные ящики со смесью, состоящей из 49% порошка алюминия, 49% окиси алюминия и 2% хлористого аммония. Укладывать детали в ящики следует так же, как при цементации в твердом карбюризаторе. Ящики плотно закрывают крышками, обмазывают огнеупорной глиной, погружают в печь и нагревают в течение 5—10 часов при температуре от 900 до 1100° С. За это время образуется алитированный слой глубиной 0,3—1,0 мм.
После алитирования детали подвергаются диффузионному отжигу при температуре около 1000° С с выдержкой 4—6 часов. В результате отжига содержание алюминия в поверхностном слое снижается, что уменьшает хрупкость алитированного слоя.
При алитировании в жидкой среде в стальном тигле расплавляют алюминий, насыщенный 6—8% железа, и в него погружают детали. Алитирование производится при температуре 750—800° С в течение 50—90 минут. Такая выдержка обеспечивает получение слоя глубиной 0,2—0,35 мм.
При газовом алитировании изделие вместе с порошком ферроалюминия погружают в реторту и пропускают хлористый водород. После обменных реакций, протекающих при температуре 850 — 1000° С, атомарный алюминий диффундирует в поверхностные слои деталей.
Процесс газового алитирования длится обычно не более 4 часов. За это время можно получить алитированный слой глубиной 0,4 мм. После окончания процесса как жидкого, так и газового алитирования рекомендуется производить диффузионный отжиг.
Диффузионным хромированием называют процесс насыщения поверхности стали хромом. Хромирование может производиться в твердых, газовых и жидких средах.
При хромировании в твердой среде применяют порошкообразную смесь из 60—65% металлического хрома или феррохрома, 30— 35% глинозема и 5% хлористого аммония. Процесс ведется при температуре 1000—1150° С в течение 7—12 часов. При хромировании низкоуглеродистой стали на поверхности деталей за это время образуется хромированный слой толщиной 0,1—0,25 мм.
При жидком хромировании изделия нагревают в ванне из расплавленных хлористых солей бария, магния и кальция с добавкой феррохрома и хлористого хрома. Процесс ведется при температуре 980-1000° С.
При хромировании в газообразной среде изделия нагревают до 950—1050° С в атмосфере парообразного хлористого хрома.
В низкоуглеродистых сталях хром растворяется в α-железе. В высокоуглеродистых сталях хром образует карбиды.
Хромированию подвергают различные детали и инструменты, от которых требуются высокая износоустойчивость, коррозионная стойкость и жаропрочность,—такие, как сверла, калибры, клапаны компрессоров и т. д. Жаростойкость хромированных сталей составляет 800—850° С.
Силицированием называют процесс поверхностного насыщения стали кремнием с целью повышения кислотоупорности, сопротивления износу и жаростойкости деталей. Силицирование проводят в твердом, жидком и газообразном цементаторе.
Для твердого силицирования используют смесь ферросилиция с шамотом. Чтобы ускорить процесс, добавляют хлористый алюминий. Процесс ведут при 1100 — 1200° С. При выдержке 4—10 часов образуется силицированный слой глубиной 0,2—0,7 мм.
При жидком силицировании используют хлористые соли с добавкой ферросилиция. Процесс ведут при 950— 1000° С.
Газовое силицирование имеет наибольшее промышленное значение; его проводят аналогично алитированию, с использованием ферросилиция. Процесс идет более интенсивно, чем в предыдущих случаях. После выдержки при 1050° С в течение 2 часов получают слой толщиной 1,0 мм, насыщенный кремнием.
Характерной особенностью силицированного слоя является его пористость. Если проварить деталь в масле при температуре 150— 200° С, масло, впитываясь в поры, способствует самосмазыванию детали, повышая ее стойкость при работе на истирание. Жаростойкость силицированных деталей не превышает 800—850° С.
В последние годы разработаны новые процессы повышения износоустойчивости стальных деталей, которые называются сульфидированием и сульфоцианированием. Сущность сульфидирования заключается в насыщении поверхности стальных деталей серой на глубину 0,2—0,3 мм путем их нагрева в расплавленных серноазотистых солях при температуре 550—600° С с выдержкой в течение 2—3 часов. В результате поверхность деталей насыщается серой до 0,5% и азотом до 1,0%. Сульфидированные детали хорошо работают на трение. По лабораторным исследованиям износоустойчивость деталей после сульфидирования повышается в 2—3 раза.
Сульфоцианирование — процесс поверхностного насыщения стали серой, углеродом и азотом. Совместное влияние серы и азота в поверхностном слое металла обеспечивает более высокую износоустойчивость. Сульфоцианирование проводится обычно в соляных ваннах при температуре 550—600° С.
Тема №51
ЛАТУНЬ
Сплав
| Марка
| Состав сплава, %
| Медь
| Примеси, не более
| Томпак
| Л96
| 95-97
| 0,2
| Л90
| 88-91
| 0,2
| Полутомпак
| Л85
| 84-86
| 0,3
| Л80
| 79-81
| 0,3
| Латунь
| Л70
| 69-72
| 0,2
| Л68
| 67-70
| 0,3
| Л63
| 62-65
| 0,5
| Л60
| 59-62
| 1,0
| Сплав меди с цинком, процентное содержание цинка в котором составляет от 5 до 45%, называется латунью. Латунь, в состав которой входит 2-20% цинка, называется томпак или красная латунь. Если содержание цинка равно 20-36%, то такая латунь называется жёлтой. Латуни, с более чем 45% цинка в своём составе, применяются крайне редко.
Классификация латуней:
· Простые (двухкомпонентные) – сплавы которые состоят из цинка и меди с незначительными примесями других элементов;
· Специальные (многокомпонентные) латуни в своём составе помимо меди и цинка включают ряд других легирующих элементов.
Простые латуни
Двухкомпонентные латуни обозначаются заглавной буквой «Л», за которой следует двузначная цифра, определяющая среднее значение процентного содержания меди в сплаве (Л80-латунь, в состав которой входит 80% меди и 20% цинка).
Классификация простых латуней приведена в таблице:
Простые латуни легко поддаются обработке давлением. Обычно, они поставляются в виде труб и трубок, отличающихся по форме сечения, в виде лент, полос, проволоки, листов. Для изделий из латуни, обладающих высоким внутренним напряжением, хапактерно растрескивание, которого можно избежать, если перед длительным хранением провести отжиг при низких температурах (200-300°C).
Специальные латуни
Многокомпонентные латуни представлены в большей разновидности, чем простые.
Маркировка специальных латуней начинается с заглавной буквы «Л», после которой обозначается последовательность легирующих элементов сплава (за исключением цинка) и их процентное содержание, начиная с преобладающего в сплаве элемента. Количество цинка определяется в соответствии с разницей от 100%.
Легирующие элементы латуни, среди которых основными являются кремний, марганец, свинец алюминий, железо и никель, оказывают существенное влияние на свойства латуней:
· Олово способствует повышению прочности и коррозийной стойкости латуней в морской воде;
· Марганец (особенно сочетаясь с оловом, железом и алюминием), а также никель повышают устойчивость сплава к коррозии и его прочность;
· Свинец, входящий в состав сплава, ухудшает его механические свойства, обеспечивая при этом лёгкость в обработке резанием, поэтому латуни, которые предполагают дальнейшую обработку см помощью станков-автоматов, имеют именно свинец в качестве основного легирующего элемента;
· Содержание кремния в сплавах из латуни негативно сказывается на их прочности и твёрдости. Однако если латуни легированы одновременно свинцом и кремн6ием, их антифрикционные свойства повышаются, и такие латуни могут заменить более дорогостоящие сплавы (например, оловянные бронзы).
Специальные латуни применяются:
· Деформируемые латуни ЛАЖ60-1-1 применяются в качестве прутков, труб, ЛЖМц59-1-1 и ЛС59-1 в качестве труб, прутков, полос, проволоки
· Литейные латуни ЛЦ40Мц3Ж применяются в деталях, сложных по своей конфигурации, гребных винтах и лопастях и др.; ЛЦ30А3- детали, устойчивые к коррозии; ЛЦ40С нашли применение в арматуре, сепараторах шариковых втулках и др.
Тема №52
БРОНЗА
Бронзой называется сплав меди с алюминием, кремнием, оловом, бериллием и другими элементами, кроме цинка. Бронзы бывают алюминиевыми, кремниевыми, оловянными, бериллиевыми и т.д. – в зависимости от легирующего элемента.
Маркировка бронзы представляет собой определенную последовательность, начинающуюся с буквосочетания «Бр», после которого указываются легирующие элементы. Легирующие элементы перечисляются, начиная с элемента, который находится в максимальном процентном содержании относительно остальных.
Все бронзы подразделяются на оловянные и безоловянные
Оловянные бронзы
Оловянные бронзы применяются в химической промышленности и в качестве антифрикционных материалов благодаря высоким антикоррозийным и антифрикционным свойствам.
Легирующие элементы оловянных бронз – фосфор, цинк, никель. Цинк, входящий в состав оловянных бронз в количестве до 10%, служит для того, чтобы стоимость бронз стала меньше. Фосфор и свинец способствуют повышению антифрикционных свойств бронзы и улучшают их обрабатываемость резанием.
Литейные оловянные бронзы применяются:
· Деформированные бронзы - БрОФ6,5-0,4; БрОЦ4-3; БрОЦС4-4-2,5 – используются в качестве пружин, антифрикционных деталей, мембран
· Литейные бронзы - БрО3Ц12С5, БрО3Ц12С5, БрО4Ц4С17 – используются в антифрикционных деталях, арматуре общего назначения
Безоловянные бронзы – это двойные или многокомпонентные бронзы без олова, в состав которых входя такие элементы как марганец, алюминий, свинец, железо, никель, кремний, бериллий.
Алюминиевые бронзы обладают высокими технологическими и механическими свойствами, коррозийной стойкостью в условиях тропического климата и в морской воде. Для глубокой штамповки на практике используют однофазные бронзы, двухфазные бронзы применяются в виде фасонного литья и подвергают горячей деформации. 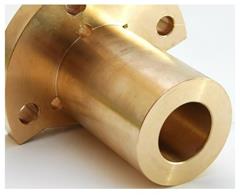
Алюм
|