Мы поможем в написании ваших работ!
ЗНАЕТЕ ЛИ ВЫ?
|
Со встроенным пневмоприводом и комбинированным
Зажимным устройством
бу 16 и длинные концы рычагов 13, соединённые посред- ством пальцев 15 со стойками шайбы 16.
При этом рычаги 13 поворачиваются на осях 19. Корот- кие концы этих рычагов воздействуют на штоки 10, кото- рые, сжимая пружины Ли перемещаясь во втулке 2, давят на пяты 3 рычагов 4. В результате рычаги 4 поворачиваются вокруг осей 6 стоек 9 и посредством осей 8 и коромысел 5 поджимают с необходимой силой обрабатываемые заготовки к стойкам 7. Зажим обеспечивает заданное положение заго- товок при фрезеровании.
По окончании обработки перекрывается пневмомагист- раль и открывается выход воздуха из камеры в атмосферу. При этом под воздействием пружин 11 штоки 10 отходят вниз и поворачивают в исходное положение рычаги 13. При повороте длинные концы рычагов 13 поднимают вверх шай- бу 16 и способствуют выправлению и обратному прогибу ди- афрагмы 14. С опусканием вниз штоков 10 рычаги 4 под дей- ствием собственной силы тяжести (центр тяжести рычагов смещён от оси их поворота в сторону регулируемых пят 3) поворачиваются вокруг осей 6 и отводят от заготовок зажим- ные элементы — коромысла 5. Зажим отключается, обрабо- танные заготовки вынимаются из приспособления. При ус- тановке новых заготовок цикл повторяется.
Приспособление устанавливается на стол горизонтально- фрезерного станка и ориентируется по Т-образным пазам стола направляющими шпонками 12. Обработка поверхностей А заготовок осуществляется фрезой, устанавливаемой в нуж- ное положение с помощью щупа и установов 22.
В результате рассмотрения приспособления можно сде- лать вывод, что сила, создаваемая диафрагменным пневмо- приводом, передаётся на длинные концы рычагов 13 и при равенстве расстояний 1г и 12 на каждый рычаг действует сила,
равная W /2. На других концах рычагов действуют силы 2/ (без учёта сил трения). Эти силы изменяются по направле-
нию действия и значению рычагами 4. Таким образом, на
каждое коромысло 5 действует одна и та же сила 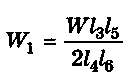
и каждый пакет заготовок при равенстве плеч коромысла поджимается к стойкам 7 двумя силами, равными W 1 /2. В этом плане в приспособлении осуществлена схема параллель- ной передачи сил зажима. Но в каждом пакете три заготов- ки, и силы зажима W 1 /2 последовательно передаются от ко- ромысла 5 на первую заготовку, от неё — на вторую, а от второй — на третью. И в этом плане в приспособлении реа- лизуется схема последовательной передачи сил зажима.
В случаях, когда в многоместном приспособлении обра- батываются различные поверхности заготовок и возникают неодинаковые силы резания (рис. 1.40, б), расчёты потреб- ных сил зажима, зажимных устройств и приводов к ним осу- ществляются отдельно для каждой позиции. Например, для указанного семипозиционного приспособления семь одновре- менно установленных заготовок зажимаются индивидуально предусмотренными устройствами, привод которых осуществ- ляется от 24 гидроцилиндров. При проектировании подоб- ных многоместных приспособлений желательно предусмат- ривать централизованное управление приводами зажимных устройств всех позиций.
Контрольные вопросы
1. Изложите методику и принципы расчёта сил зажима заготовки (детали) в приспособлении.
2. Какие расчётные факторы используются в силовых расчётах приспособлений.
3. Как осуществляется расчёт потребных зажимных сил из условия несдвигаемости заготовки (детали) при об- работке (сборке)?
4. Какие зажимные устройства используются в приспо- соблениях?
5. Какова методика расчёта различных зажимных уст- ройств приспособлений?
6. Как выбираются и используются приводы в приспособ- лениях?
7. Опишите общую методику силового расчёта приспособ- лений.
8. В чём заключается анализ существующих конструк- ций приспособлений? За счёт чего он осуществляется?
9. Изучите описание рассмотренной в разделе конструк- ции приспособления.
10. Ознакомьтесь с приведённым примером силового рас- чёта и самостоятельно выполните силовой расчёт при- способления другой конструкции.
ГЛАВА 10
ВЫБОР МАТЕРИАЛОВ И РАСЧЁТ ОСНАСТКИ НА ПРОЧНОСТЬ
10.1 Выбор конструкционных материалов деталей оснастки
После расчёта точности изготовления приспособления и силового расчёта необходимо выбрать конструкционные ма- териалы для деталей приспособления, назначить термичес- кую (химико-термическую, электрохимическую и т.п.) обра- ботку или вид покрытия и рассчитать размеры элементов из условий прочности.
Материалы для деталей (элементов) приспособлений сле- дует выбирать исходя из условий работы и эксплуатацион- ных требований, предъявляемых к этим деталям. Так, к ус- тановочным элементам приспособлений, которые являются опорами заготовки в приспособлении и определяют её поло- жение в пространстве, предъявляются требования точности, прочности, жёсткости, износостойкости. Применительно к за- жимным элементам на первый план выдвигаются прочность, жёсткость и надёжность. Корпуса объединяют в единую кон- струкцию элементы приспособления и воспринимают все силы, действующие на заготовку в процессе её закрепления и обработки. Поэтому они должны обладать достаточно вы- сокой прочностью, демпфирующими свойствами, жёсткостью и длительное время сохранять точность расположения рабо- чих поверхностей. Подобные требования предъявляются и к другим элементам приспособлений. В определённой степени многие из названных требований обеспечиваются конструк- цией и размерами деталей приспособлений. А вот износос- тойкость, прочность и жёсткость элементов и компактность приспособлений в большей части зависят от правильного выбора конструкционных материалов, химико-термической, отделочной обработки и покрытий.
Рекомендации по применению металлов и неметалличес- ких составов в качестве конструкционных материалов для различных деталей (элементов) приспособлений, применяе- мая химико-термическая обработка, достигаемые твёрдость и технологические свойства материалов в состоянии постав- ки представлены в таблицах 10.1...10.5.
Таблица 10.1 Стали, используемые для деталей приспособлений, их обработка и свойства
Детали и условия их работы
| Марка стали
| Химико- термиче- ская обра- ботка (ХТО)
| Твёр- дость, HRC3
| Сваривае- мость
| 1
| 2
| 3
| 4
| 5
| Прокладки, шайбы, заклёпки
| СтО, Ст1, Ст2
| Без ХТО
| -
| Хорошая
| Сварные детали, щитки, крышки, оправки, валы, оси, клинья, штифты и другие де- тали, работающие при малой и средней нагрузках
| СтЗ, Ст4
| Тоже
| -
| Тоже
|
Ст5
| Нормали- зация
| -
| Тоже
| Шпонки, зубчатые колёса, валы с повышенной прочно- стью и твёрдостью
| Стб
| Закалка в воде, от- пуск
| 49...51
| Ограничен- ная
| Пальцы, оси, зубчатые колёса, кулачковые муфты, шпинде- ли, валы, кондукторные втул- ки диаметром более 25 мм, пальцы и другие детали:
|
| Цемента- ция, за- калка в масле, отпуск
|
|
| повышенной износостойкости
| 10,15,20
|
57...63
| Хорошая
| высокой износостойкости
| 15Х, 20Х, 20ХН
|
59...63
| Удовлетво- рительная
| Крепёжные детали, кондук- торные плиты, прихваты, на- жимные винты, муфты со- единительные, работающие при средних нагрузках
| 25 35
| Закалка в воде, от- пуск
| 28...34 31...51
| Хорошая Ограничен- ная
|
35Х,
35ХН,
ЗОХГСА
| Закалка в масле, отпуск
| 46...51
| Ограничен- ная
| Продолжение таблицы 10.1
1
| 2
| 3
| 4
| 5
| Валы, оси, штоки, шпиндели, зубчатые колёса, плунжеры, эксцентрики, пальцы, ролики и другие детали, работающие на изнашивание при средних скоростях
| 40, 45, 50, 55
| Закалка в воде, от- пуск
| 2S...56
| Тоже
|
40Х, 45Х,
50Х,
40ХГ,
40ХН
| Закалка в масле, отпуск
| 31...56
| //
| Зубчатые колёса, валы, втул- ки, пальцы шаровые, элемен- ты УСП и другие детали, ра- ботающие при больших ско- ростях и нагрузках ударного характера
| 12ХНЗА,
15ХГНТА,
18ХГ,
18ХГТ,
20ХГТ,
ЗОХГТ
| Цемента- ция, за- калка в масле, отпуск
| 57...63
| II
| Эксцентрики, кольца пру- жинные, пружины общего назначения, работающие при средних нагрузках
| 65, 70, 55С2
| Закалка в масле, отпуск
| 38...53
| Плохая
| Зубчатые колёса, валы, оси, диски фрикционные, элемен- ты разжимные и пружины общего назначения, ножи и другие детали, работающие в условиях истирания и знако- переменных нагрузок
| 50Г
| Закалка в масле, отпуск
| 28...60
| Плохая
|
60Г
|
Тоже
|
65Г
|
Тоже
|
35Г2
|
Удовлетво- рительная
|
45Г2
|
Ограничен- ная
|
50Г2
|
Плохая
| Тонкостенные гильзы, гофри- рованные втулки, пружины и другие ответственные преци- зионные детали упругого дей- ствия, работающие в сложных условиях истирания и высо- ких знакопеременных напря- жений
| 55ГС,
50ХФА,
50ХГФА,
50С2,
60С2,
60С2ХА,
60СХФА,
65С2ВА
| Тоже
| 39...61
| Плохая
| Продолжение таблицы 10.1
1
| 2
| 3
| 4
| 5
| Шпиндели, копиры, эксцен- трики, оправки, кулачки, зуб-
| 38ХЮ, 38ХМЮА,
| Азотиро- вание
| 66...69
|
| чатые колёса, гладкие калиб- ры, шаблоны, установки, ро-
| 38ХВФЮ
|
|
|
|
|
|
лики, шары и другие детали с
| 9X1, 12X1, ШХ15
| Закалка в масле, отпуск
|
| Плохая
| высокими поверхностной и твёрдостью и износостойко- стью, работающие при высо-
|
62...65 59...65
|
| ких нагрузках
|
|
|
|
| Пальцы и пластины устано-
|
|
|
|
| вочные, центры, втулки кон-
| У7,
| Закалка
|
|
| дукторные диаметром до
| У7А,
| через воду
| 61 65
| То же
| 25 мм, цанги, оправки и дру-
| У8,
| в масле,
|
|
| гие детали, работающие в
| У8А
| отпуск
|
|
| условиях ударов и толчков
|
|
|
|
| Копиры и копирные ролики,
| У8ГА
|
|
|
| оправки, втулки кондуктор-
| У10
|
|
|
| ные, шаблоны и другие дета-
| У12,
| То же
| 63...67
|
| ли с высокой твёрдостью,
| У12А
|
|
|
| работающие в безударных
| У13А
|
|
|
| условиях
|
|
|
|
| Эталонные зубчатые колёса,
|
|
|
|
| копиры, оправки и другие детали, для которых не до-
| ХВГ
|
| 63...64
| Ограничен-
| пускается коробление при
|
|
|
|
| термообработке
|
|
|
|
| Таблица 10.2 Стали, рекомендуемые для изготовления заготовок деталей приспособлений литьём
Детали (элементы) приспособлений
| Марка стали
| Ненагруженные (плиты, вилки, стаканы, корпусы, кронштейны и т.п.)
| 25Л
| Малонагруженные (рычаги, планшайбы, корпусы патронов, кронштейны и т.п.)
| 35Л
| Особо нагруженные (вилки, цапфы, стержни и т.п.)
| 45Л
| Таблица 10.3 Серые и высокопрочные чугуны, рекомендуемые для отливки заготовок деталей приспособлений
Детали (элементы) приспособлений
| Марка чугуна
| Твёрдость, НВ
(в состоянии
поставки)
| Работающие в условиях средних нагрузок без
|
|
| трения (крышки, планшайбы крупные, плиты,
| СЧ10
| 143...229
| стойки, корпусы, шкивы, маховики и т.п.)
|
|
| Работающие в условиях средних нагрузок с
|
|
| давлениями между трущимися поверхностя- ми, равными примерно 0,5 Н (основания,
| СЧ15
| 163...229
| корпусы, салазки, шкивы, планшайбы)
|
|
| Работающие в условиях средних нагрузок на
|
|
| изнашивание и отливки больших габаритов
|
|
| (втулки подшипников тихоходных передач,
| СЧ18
| 170...229
| корпусы пневмокамер и пневмоцилиндров,
|
|
| корпусы приспособлений)
|
|
| Работающие в условиях больших нагрузок на
|
|
| изнашивание при высокой герметичности
| СЧ20
| 170...241
| (гидроцилиндры, гильзы, корпусы)
|
|
| Ответственные детали, работающие в усло-
|
|
| виях больших нагрузок на изнашивание (от-
| СЧ25
| 180...250
| ливки сложной конструкции)
|
|
| Работающие в условиях изнашивания и виб-
|
|
| рационных нагрузок (корпусы, зубчатые ко-
| ВЧ 45-5
| 160...220
| лёса, кронштейны и т.п.)
|
|
| Ответственные детали, работающие в усло-
|
|
| виях вибрационных нагрузок (корпусы, зуб-
| ВЧ 60-2
| 200...280
| чатые колёса и т.п.)
|
|
| Таблица 10.4 Цветные металлы и сплавы, используемые в производстве приспособлений
Детали (элементы) приспособлений
| Конструкционный материал
|
Наименование
| Марка
| 1
| 2
| 3
| Литые заготовки ответственных деталей (планшайбы, шкивы, ро- торы, корпусы пневмоцилиндров) и крупных нагруженных деталей (корпусы, блоки)
| Сплавы алюминие- вые литейные
| АК9ч
| Литые заготовки деталей сложной конфигурации для работы в усло- виях средней нагруженности, а также для свариваемых деталей
|
АК7ч
| Втулки подшипников при сопря- жении с термически обработанны- ми валами
| Сплавы алюминие- вые литейные
| АК4, АК4-1
| Катоды, контакты, детали, тре- бующие хорошей электропровод- ности, изоляционные слои магнит- ных приспособлений, обмотка электроприводов; литые заготовки подобных по назначению деталей
| Медь
| М1,М2
|
МЗ
| Гайки нажимных винтов, рабо- тающие на истирание в тяжёлых условиях; массивные червячные винты
| Латунь, алюминие-
во-железо-
марганцевая
| ЛАЖМц66-6-3-2
| Детали, обладающие коррозион- ной стойкостью
| Латунь алюминиевая
| ЛА67-2.5
| Арматура, втулки, подшипники скольжения
| Латунь алюминие- во-железная
| ЛАЖ60-1-1Л
| Литые заготовки деталей, втулки
| Латунь свинцовая
| ЛС59-1Л
| Зубчатые колёса
| Латунь марганцево- оловянно-свинцовая
| ЛМцОС58-2-2л
| Упорные и опорные подшипники
| Латунь марганцевая
| ЛМц58-2Л
| Несложные по конфигурации от- ветственные детали
| Латунь марганцево- железная
| ЛМцЖ55-3-1
| Продолжение таблицы 10.4
1
| 2
| 3
| Втулки и вкладыши подшипников сколь-
|
|
| жения, работающие в паре с термически
|
|
| обработанными валами при средних ско-
|
|
| ростях; червячные колёса, работающие в
|
| БрА9ЖЗЛ
| паре с термически обработанными червя-
|
|
ками; детали насосов, работающие на
| Бронзы
|
| истирание; фрикционные диски, упорные
| безоловянные
|
| кольца
|
|
| Втулки и вкладыши подшипников сколь-
|
| жения, работающие в условиях больших
|
| БрСЗО
| нагрузок и высоких скоростей в паре с
|
|
термически обработанными валами
|
|
| Подшипники шпинделей; венцы червяч- ных колёс, работающие в паре с незака- лёнными червяками
| Бронзы оловянные вторичные литейные
| Бр05Ц5С5
| Втулки подшипников, гайки ходовых винтов
|
Бр04Ц4С17
| Ответственные втулки и вкладыши под-
| Бронзы
оловянно-
фосфоритные
|
| шипников скольжения, венцы червячных колёс, работающие в паре с термически обработанными червяками
|
БрОФ1
| Таблица 10.5 Неметаллические конструкционные материалы, используемые для деталей приспособлений
Детали (элементы) приспособлений
| Материал
|
Наименование и марка
| 1
| 2
| Вкладыши подшипников, втулки, зуб- чатые колёса и другие конструкцион- ные детали
| Пластики древесные слоистые: ДСП-В, ДСП-Б
| Самосмазывающиеся подшипники скольжения
| ДСП-В-м, ДСП-Б-м
| Зубчатые колёса, малонагруженные ролики и корпусы сборочных приспо- соблений
| Текстолит конструкционный ПТК
| Неответственные детали (ручки и т.п.)
| ПТ
|
Продолжение таблицы 10.4
1
| 2
| Вкладыши подшипников скольжения
| ПТМ-1, ПТМ-2
| Электроизоляционные детали, про- кладки
| Текстолит листовой электротех- нический (А, Б, Г, ВЧ)
| Детали с антикоррозионной стойко- стью; электроизоляционные детали
| Винипласт листовой ВН и ВП
| Конструкционные детали, обладаю- щие термоизоляционной способно- стью, детали тормозных устройств
| Асботекстолит: А, Г
| Прокладки
| Картон прокладочный А и Б Паронит ПОН
| Конструкционные малонагруженные детали
| Фибра листовая: ФТ
| Детали с электроизоляционной спо- собностью
| ФЭ
| Диафрагмы, прокладки, буфера
| Резина техническая листовая
(ТМКЩ - тепломорозокислото-
щелочестойкая, ОМБ - ограни-
ченно-маслобензостойкая, ПМБ -
повышенно-маслобензостойкая)
| Уплотнительные детали
| Резина для деталей
| Манжеты, прокладки
| Кожа техническая
| Сальники, смазывающие фитили и тампоны
| Войлок технический полугрубо- шерстный
| Рабочие жидкости разжимных и дру- гих устройств
| Гидропластмасса ДМ и СМ
| Клеевые составы для склейки метал- лов, текстолита, фибры
| Клеи БФ-2, БФ-4 и др.
| Клеевой состав для склейки металлов, металлов с кожей, резиной, резины с резиной, кожи с кожей
| Клей № 88
| Гибкие воздуховоды, работающие в условиях давления до 2 МПа
| Рукава резиновые напорные с тек- стильным каркасом
| Корпуса небольших приспособлений, плиты кондукторные, втулки для на- правляющих штанг подвесных кон- дукторов и колонок штампов
| Эпоксидно-диановые смолы и компаунды на их базе с наполни- телями (стекловолокно, стружка металлическая и др.)
| 10.2 Используемые покрытия для деталей и их химико-термическая обработка
При выборе материалов для элементов приспособлений необходимо решить вопросы о виде покрытия поверхностей, химической и электрохимической обработки деталей. Покры- тия и химическая обработка применяются для улучшения эксплуатационных, защитных и декоративных свойств дета- лей приспособлений. Существуют лакокрасочные, гальвани- ческие, химические и металлизационные покрытия, оксид- ные и фосфато-оксидные процессы обработки деталей.
Лакокрасочные покрытия стандартизованы. В зависимос- ти от условий эксплуатации лакокрасочные покрытия подраз- деляются на стойкие внутри помещений, атмосферостойкие, масло- и бензостойкие, водостойкие, электроизоляционные. В выборе цветов покрытия следует руководствоваться цветовы- ми решениями лакокрасочных покрытий оборудования, на ко- тором предполагается использование данного приспособления.
К гальваническим покрытиям металлов относятся мед- нение, хромирование (износостойкое и защитно-декоратив- ное), цинкование, кадмирование и другие процессы.
Меднение используется с целью обеспечения повышен- ных приработочных свойств поверхностей деталей, работаю- щих в узлах трения скольжения (шлицевые соединения, пары трения типа вал-втулка, выступ-паз, «ласточкин хвост» и т.п.); уплотнения зазоров; уменьшения шума и улучшения прирабатываемости зубчатых передач; защиты от коррозии. Средняя расчётная толщина слоя покрытия для достижения указанных выше целей составляет 5... 15 мкм.
Износостойкое хромирование приводит к повышению работоспособности (прежде всего износостойкости) деталей, работающих в условиях истирания (шейки валов, оси, паль- цы, рейки, направляющие и установочные элементы и т.д.). Прочность соединения хрома с основным металлом достаточ- но высокая. Хромовое покрытие обладает стойкостью против воздействия азотной кислоты и растворов щелочей, длитель-
ное время сохраняет свои декоративные свойства (цвет и блеск), хорошо выдерживает равномерно распределённую по поверхности нагрузку, но разрушается в условиях ударных нагрузок. Толщина слоя покрытия обычно равна 10.„30 мкм.
Защитно-декоративное хромирование применяется для деталей несложной формы, работающих в условиях истира- ния при незначительных силовых воздействиях (различные рукоятки, маховички, штурвалы и т.п.). Толщина слоя по- крытия — 2...5 мкм.
Цинкование (толщина слоя 10...30 мкм) используется для защиты деталей из чёрных металлов от коррозии. Обычно этому покрытию подвергаются детали, работающие в усло- виях влаги, мелкие резьбовые (крепёжные) детали и т.д.
Кадмирование (толщина слоя 7... 15 мкм) применяется для покрытия деталей из стали, чугуна, меди и медных сплавов. Слой кадмиевого покрытия более пластичен, чем цинкового. Поэтому кадмирование широко используется для защиты от- ветственных резьбовых соединений и деталей сборочных еди- ниц, которые требуют герметичной (плотной) сборки.
Из химически наносимых покрытий наибольшего внима- ния заслуживает химическое никелирование. В результате никелирования на обрабатываемую поверхность детали при- способления наносится никелевый осадок, образуемый путём химического восстановления ионов никеля ионами гипофос- фата. Химическое никелевое покрытие характеризуется вы- сокой равномерностью слоя по толщине (отклонение не пре- вышает 10 %), повышенной коррозионной стойкостью, малой пористостью и высокой износостойкостью, особенно в услови- ях сухого трения. Толщина слоя покрытия — 10...12 мкм. Химическое никелирование рекомендуется для покрытия плун- жеров, штоков, деталей прецизионных пар трения, работаю- щих в условиях сухого трения, оно улучшает также декора- тивную отделку приспособлений.
Металлизация распылением используется для защиты изделий от коррозии и декоративного оформления. В каче- стве покрытия применяются олово, свинец, цинк, алюми-
ний, кадмий, сталь, бронза. В зависимости от применяемого металла толщина слоя, наносимого за один проход, состав- ляет 0,025...0,08 мм. Преимуществами металлизации распы- лением являются: возможность покрытия крупных деталей сложной конфигурации, простота нанесения металла и не- сложность требуемого для этого оборудования. При решении вопроса о металлизации напылением в конкретных услови- ях следует учитывать, что прочность сцепления слоя покры- тия с основным металлом пониженная, потери напыляемого металла значительные, а в тонких слоях покрытия может наблюдаться пористость.
В качестве химической и электрохимической обработки деталей приспособлений применяются оксидирование, фос- фатирование и другие процессы, заключающиеся в создании на поверхностях металлических деталей неорганической за- щитной плёнки толщиной 5...8 мкм.
Оксидирование стальных деталей осуществляется терми- ческим способом и может быть двух видов — воронение (для мелких деталей) и синение (для полированных деталей). Плёнки, созданные в результате оксидирования и фосфати- рования, защищают детали приспособлений от коррозии. Следует учитывать, что создаваемые плёнки обладают пони- женным сопротивлением истиранию, а фосфатирование мож- но использовать для защиты от коррозии стальных деталей, к декоративной отделке которых не предъявляется высоких требований.
Общие требования к выбору металлических покрытий виды, ряды толщин слоев и обозначения покрытий стандар- тизованы.
10.3 Расчёт деталей оснастки на прочность
Прочность — одно из основных требований, предъявляе- мых к деталям и приспособлениям в целом. Прочность дета- лей может характеризоваться по ряду частных коэффициен- тов запаса (надёжность материала, степень ответственности
детали, точность расчётных зависимостей, действующие силы, другие факторы, определяющие условия работы детали) или по номинальным допускаемым напряжениям. Вероятностные расчёты и расчёты на прочность по коэффициентам запаса могут использоваться в отдельных случаях для высокоответ- ственных деталей машин и в исследованиях их надёжности. Они более точны, но очень сложны и трудоёмки. Расчёты по номинальным напряжениям менее точны, но значительно проще, доступнее, менее трудоёмки, полно отражены в спра- вочной литературе и широко используются в инженерной практике. Поэтому наибольшее внимание уделено методике этих расчётов.
С помощью расчёта можно решать две задачи:
а) проверку на прочность существующих деталей путём сравнения фактических напряжений с допускаемыми (проверочный расчёт);
б) определение размеров сечений деталей приспособлений
(предварительный проектный расчёт). Расчёт на прочность (задача а) детали в виде стержня круглого сечения, нагруженного осевой силой, по допускае- мым напряжениям растяжения (сжатия) осуществляется по формуле:
где а — фактическое напряжение растяжения (сжатия), МПа;
Р — расчётная осевая сила, Н;
d — диаметр опасного сечения (для резьбового стержня- внутренний диаметр резьбы), мм;
[<т] — допускаемое напряжение растяжения (сжатия).
Определение необходимого размера опасного сечения (задача б) для подобного случая можно производить по фор- муле:
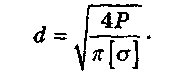
Полученное значение округляется в сторону увеличения до целого или ближайшего стандартного значения. При на- личии шпоночного паза в опасном сечении детали получен- ное расчётом значение d следует увеличить на 5... 10 %.
Расчёты на прочность валов и осей с целью определения их размеров (задача б) можно производить по формулам: на изгиб (детали круглого сечения):
(ЮЛ) на изгиб (детали кольцевого сечения):
на кручение: 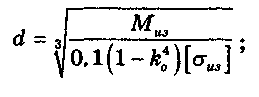

на изгиб с кручением (детали круглого сечения):
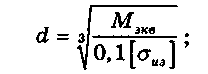
на изгиб с кручением (детали кольцевого сечения):
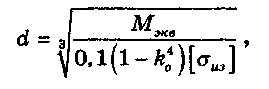
где Миз — изгибающий момент, Нмм; Мкр — крутящий момент, Нмм; Мэка — эквивалентный момент, Нмм;
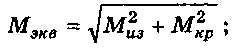
[<тцз] — допускаемое напряжение при изгибе, МПа; хкр — допускаемое напряжение при кручении, МПа;
k 0 — отношение внутреннего диаметра вала (оси) d 0 к наружному d (djd).
Необходимо помнить, что оси рассчитываются только на изгиб и срез, так как они не передают крутящего момента.
Валы и оси можно рассчитывать на жёсткость, но диа- метр деталей в этом случае получается большим, чем при расчёте на прочность. Расчёт на изгибную жёсткость состоит из определения углов наклона и прогибов упругой линии осей и валов и сравнения их с допускаемыми значениями. Следу- ет отметить и сложность расчётов деталей на жёсткость. На- пример, расчёт валов на жёсткость (задача а) при кручении производится по формуле:
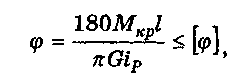
где (р — действительный угол закручивания вала, град;
[<р] — допускаемый угол закручивания (можно прини- мать для большинства валов [<р] = 15' на 1 м длины; для ме- нее ответственных валов [<р] принимается до 2 °);
Мкр — крутящий момент, Н-мм;
I — длина скручиваемой части вала, мм;
G — модуль упругости при сдвиге, МПа (для стали G = 8 • 10 МПа);
iP — полярный момент инерции сечения вала:
— для круглого сечения и
— для кольцевого сечения.
Уточнённый расчёт валов на прочность, в случае возник- новения такой необходимости, заключается в определении коэффициентов запаса для опасных сечений.
При нагружении соединения силами в плоскости (по по- верхности) стыка деталей и в случаях установки штифта (ци-
линдрического гладкого стержня винта) без зазора и работы на срез проверочный расчёт (задача а) штифта (винта) может осуществляться по формуле:
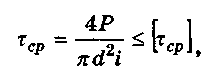
где Р — сила среза, Н;
d — диаметр штифта (стержня винта), мм;
I — число стыков (количество штифтов или винтов) в соединении;
[тср] — допускаемое напряжение среза, МПа.
Расчёт на прочность шпоночных и шлицевых соедине- ний заключается в сравнении фактически передаваемого кру- тящего момента с допускаемым моментом из условий проч- ности шпонок (шлиц).
Расчёт на прочность шпоночных соединений (задача а) производится по формулам: на смятие:
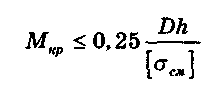
(для призматических шпонок).
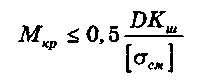
(для сегментных шпонок); на срез: 
(для призматических и сегментных шпонок), где Мкр — крутящий момент (рассчитывается по передавае- мой мощности и частоте вращения вала), Ним;
D — наружный диаметр вала, мм;
h — высота призматической шпонки, мм;
Кш — размер выступающей из паза части сегментной шпонки, мм;
I — рабочая длина шпонки, мм;
[осм] — допускаемое напряжение смятия, МПа;
Ъ — ширина шпонки, мм.
Проверочный расчёт на прочность шлицевых соединений (задача а) может осуществляться по формулам: на смятие:
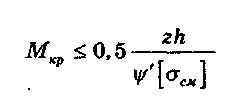
(прямобочный профиль),
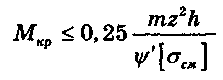
(эвольвентный профиль); на срез: 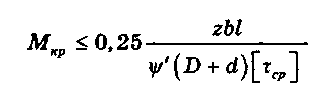
(прямобочный и эвольвентный профили), где Мкр — крутящий момент, Нмм;
г — число шлицев;
h — высота поверхности контакта (для прямобочного профиля h = 0,5(D - d)2 ful, здесь ful — фаска зуба и паза шпоночного соединения, обычно фаска принимается равной 0,3...0,5 мм с допуском +0,2„.0,3; для эвольвентных шли- цев с центрированием по боковым поверхностям h = т, с центрированием по наружной цилиндрической поверхнос- ти h = 0,9m);
D — наружный диаметр вала, мм;
d — внутренний диаметр отверстия, мм;
Ъ — ширина шлица, мм;
т — модуль эвольвентного соединения, мм;
у/' — коэффициент, учитывающий неравномерность рас- пределения нагрузки по шлицам (у/' принимается равным 0,7...0,8).
При необходимости расчёты на прочность сварных соеди- нений, пружин, подшипников, клиноременных, зубчатых передач и других специфических сборочных единиц и дета- лей следует выполнять по рекомендациям литературных ис- точников.
Пример. Рассчитать на прочность опасное звено приспо- собления (рис. 9.18). Из рассмотрения данного приспособле- ния можно прийти к выводу, что одной из наиболее нагру- женных деталей является ось 6 стойки 9. Она воспринимает повышенные нагрузки, связанные с зажимом обрабатывае- мых заготовок. Направление действия создаваемой пневмо- цилиндром силы меняется на противоположное посредством рычагов 13. При этом она увеличивается в несколько раз. Затем через штоки 10 и пяты 3 она передаётся на рычаг 4, получает направление в сторону зажима заготовок и вновь возрастает. Таким образом, на прочность целесообразно рас- считывать наиболее нагруженное звено (в описанном случае ось 6). Ось 6 в отверстиях рычага 4 и стойки 9 установлена с зазором и будет работать на изгиб. В соответствии с приня- тым решением она изготавливается из стали 20Х с цемента- цией и закалкой до твёрдости 57...63 HRCd. Вид нагрузки П (переменная). Допускаемое напряжение [ст^] для приведённо- го случая равно 220 МПа [5]. Из силового расчёта выявлено, что изгибающий момент Миз, действующий на опасное звено приспособления, равен 10800 Нмм.
Минимальный диаметр оси можно рассчитать (задача б) по формуле(10.1):
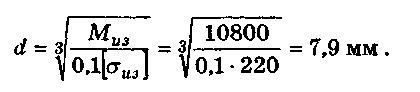
В описанных условиях можно принять размер d = 10 мм, что обеспечит более надёжную работу оси 6.
* Контрольные вопросы
1. Какие требования предъявляются к конструкционным материалам для основных элементов приспособлений?
2. Как выбираются материалы для различных деталей приспособлений?
3. Для чего применяется термическая (химико-термичес- кая) обработка деталей приспособлений?
4. Какие гальванические, химические и лакокрасочные покрытия используются при изготовлении приспособ- лений?
5. Как выбираются детали приспособлений, которые не- обходимо рассчитать на прочность?
6. Какие расчётные факторы используются в расчётах на прочность?
7. В чём отличие, недостатки и преимущества широко используемых в инженерной практике методов расчё- та на прочность?
ГЛАВА 11 ИЗГОТОВЛЕНИЕ И ОБСЛУЖИВАНИЕ ОСНАСТКИ
|