Чертежи приспособлений разрабатываются проектными
институтами станкоинструментальной промышленности, кон-
структорскими бюро отделов главного технолога предприя-
тий, технологическими бюро цехов.
Универсальные и специализированные приспособления,
комплекты УСП и УСПП, установочные, зажимные, направ-
ляющие, измерительные и другие стандартизованные и нор-
мализованные системы и элементы изготавливаются центра-
лизованно на специализированных предприятиях, а также в
специальных цехах станкоинструментальных заводов по
принципам массового, крупносерийного и серийного произ-
водств. Неразборные специальные приспособления (НСП),
наладки к специализированным и универсальным наладоч-
ным приспособлениям (СНП и УНП), отдельные детали и
сборочные единицы к сборкам УСП и УСПП изготавливают-
ся индивидуально или малыми партиями инструментальны-
ми цехами машиностроительных предприятий единичного и
мелкосерийного производств. Цеховые приспособления изго-
тавливаются инструментальными службами механических,
механосборочных и сборочных цехов.
Заготовки для деталей НСП изготавливаются из сортово-
го проката, ковкой, а иногда литьём. Заготовки сложной
конфигурации крупных и средних размеров часто изготав-
ливаются сваркой из предварительно заготовленных плит,
планок, угольников, шайб, втулок, косынок и других эле-
ментов проката. В этом плане важную роль играет заводская
унификация деталей приспособлений, широкое использова-
ние в конструкциях НСП стандартных деталей (корпусов,
установочных, зажимных, направляющих, измерительных
и других элементов).
Заготовки корпусных и других ответственных деталей
следует подвергать отжигу, а перед отделочной механичес-
кой обработкой целесообразно осуществлять их естественное
или искусственное старение для снятия остаточных напря-
жений. Особое внимание нужно уделить сварным конструк-
циям. Перед сваркой все элементы должны очищаться от
ржавчины, окалины, масла и других загрязнений, собирать-
ся на струбцинах с выверкой относительного положения и
предварительно свариваться (прихватываться) в отдельных
точках. После снятия струбцин вновь производится выверка
и только потом, желательно дуговой электросваркой, накла-
дываются основные швы, которые для уменьшения дефор-
мации могут быть прерывистыми.
Детали с точно координированными отверстиями (корпу-
сы, кондукторные плиты, диски делительных устройств и т.п.)
могут изготавливаться при допусках на межосевые расстоя-
ния в десятых долях миллиметра разметкой, при допусках в
сотых и тысячных долях миллиметра обработкой на коорди-
натно-расточных станках (КРС). Повышение точности поло-
жения отверстий, например, кондукторных плит, приводит
к повышению ресурса сверлильных приспособлений за счёт
увеличения допуска на износ кондукторных втулок.
Существуют способы обеспечения высокой точности поло-
жения отверстий паточных токарных или вертикально-фре-
зерных станках в условиях, когда отсутствует КРС. Один из
способов предусматривает сверление по разметке отверстий
диаметрами, меньшими диаметров растачивания, с нарезани-
ем в них резьбы. Посредством этих отверстий на лицевой сто-
роне заготовки при помощи мер длины точно в соответствии с
межосевыми расстояниями отверстий по чертежу детали ус-
танавливаются эталонные втулки. Затем заготовка с закреп-
лёнными винтами через шайбы втулками устанавливается на
планшайбе токарного или столе фрезерного станка так, чтобы
ось одной из втулок совпадала с осью вращения шпинделей
станков, что достигается выверкой с помощью индикатора,
закрепляемого в резцедержателе токарного или шпинделе
фрезерного станков. После этого втулка снимается и отвер-
стие растачивается до требуемого диаметра. Аналогично вы-
веряются и растачиваются другие отверстия. При этом обес-
печивается точность межосевых расстояний до 0,01 мм.
Возможно растачивание отверстий с обеспечением высо-
кой точности их относительного положения на токарных стан-
ках без разметки с использованием планшайбы с угольни-
ком, который позволяет по мерам длины устанавливать за-
готовку по её плоским базам так, чтобы ось вращения шпин-
деля станка совпадала с осью будущего отверстия. После об-
работки первого отверстия путём переустановки заготовки
относительно граней угольника совмещается с осью враще-
ния станка ось второго отверстия, потом третьего и так далее
до окончания обработки всех отверстий детали.
Сокращение затрат и сроков изготовления НСП для се-
рийного производства обеспечивает отливка корпусных и
других деталей из эпоксидных компаундов (рис. 1.14). Из
них можно отливать ложементы (негативные отпечатки) для
установки заготовок по внешним фасонным поверхностям.
Основанием ложемента обычно служит сварная коробка (кас-
сета), в которую на определённом уровне устанавливается
деталь. Затем коробка заполняется компаундом, после зат-
вердевания которого остаётся негативный отпечаток, пред-
назначенный для базирования заготовок по фасонной повер-
хности. Полученное приспособление оснащается зажимны-
ми элементами и может использоваться для обработки заго-
товок из алюминиевых сплавов, других цветных металлов и
неметаллических материалов.
Сборка неразборных приспособлений и наладок к СНП и
УНП обычно производится с выполнением пригоночных работ
и обработкой «по месту». Для получения сопряжений требуе-
мой точности используются припиливание, пришабривание,
притирка (доводка). В процессе сборки производится точная
выверка относительного положения деталей и сборочных еди-
ниц приспособления с последующей фиксацией найденного
положения контрольными штифтами. Для неподвижных со-
единений деталей, работающих на сдвиг и сжатие, целесооб-
разно применять склеивание. Прочность на сдвиг при исполь-
зовании, например, эпоксидных клеев достигает 30...35 МПа.
Разборка клеевых соединений в случае необходимости ремон-
та приспособления возможна при нагреве деталей соединений
до температуры 150 °С. Для повышения точности НСП прак-
тикуется отделочная обработка отдельных деталей в сбороч-
ных единицах (после сборки). С целью обеспечения малых
отклонений от соосности нескольких отверстий в корпусных
деталях, ступенчатых отверстий, а также ступенчатых наруж-
ных цилиндрических поверхностей (шеек) их отделочную об-
работку следует производить с одной установки заготовки.
Точность относительного положения рабочих поверхностей
установочных элементов может быть повышена с помощью
шлифования путём их установки на корпусе приспособления.
Обработка элементов приспособления в сборе используется
также при малом значении параметра точности относительно-
го положения рабочих поверхностей установочных элементов
и базовых поверхностей корпуса.
Сборка специальных по назначению приспособлений из
элементов УСП и УСПП осуществляется слесарями-конструк-
торами непосредственно в производственных цехах или на
централизованных участках УСП небольших заводов. Исход-
ными документами для сборки приспособления являются
заявка цехового технолога, операционные карты техпроцес-
са с эскизами на предыдущую операцию и на последующую,
для которой готовится данное приспособление. Необходима
также одна заготовка, обработанная на предыдущей опера-
ции. В случае необходимости технологом по согласованию со
слесарем-конструктором выполняются эскизы на специаль-
ные детали собираемого приспособления, которые передают-
ся в инструментальную службу цеха для изготовления.
На цеховые приспособления (простые накладные кондук-
торы, оправки, разрезные втулки, державки для инструмен-
та, подставки для запрессовки втулок и т.п.) технологом или
по его заданию конструктором инструментальной службы цеха
делаются чертежи (эскизы), по которым станочниками и сле-
сарями этой службы изготавливаются приспособления. Та-
кой путь оснащения техпроцессов часто используется в мел-
косерийном и серийном производствах. Он сокращает время
изготовления оснастки.
11.2 Приёмка и техническое обслуживание оснастки
После изготовления приспособление подлежит проверке и
приёмке. Проверка предусматривает: внешний осмотр на от-
сутствие дефектов на рабочих поверхностях; контроль комп-
лектности в соответствии с чертежом; выявление плавности
перемещений и лёгкости сдвига подвижных элементов, плот-
ности посадок и герметичности соединений, опробование при-
способления на действие установочных, зажимных и измери-
тельных элементов и механизмов, поворотных устройств, фик-
саторов, выталкивателей, приводов; контроль точности изго-
товления приспособления по заданным параметрам и по пара-
метрам обработанных и собранных на них образцов заготовок
и сборочных единиц. Возможна проверка и настройка приспо-
соблений с использованием эталонных деталей.
Проверка встроенных в оборудование приспособлений со-
вмещается с проверкой станков-автоматов, автоматических
линий. Подвесные кондукторы проверяются в комплекте с
многошшшдельными головками. В приспособлениях для
ППД, помимо перечисленного выше, контролируются разме-
ры инструмента (диаметры шаров и роликов, радиусы скруг-
ления алмазных наконечников и роликов, шаги расположе-
ния и биение гофр профильных роликов); число инструмен-
тов и возможность их вращения в сепараторах и на осях;
пределы развиваемых сил поджима инструмента.
При соответствии неразборного специального приспособ-
ления для установки заготовки, инструмента и сборки всем
требованиям чертежа и ТУ оно принимается работниками ОТК
инструментального цеха и на него, как правило, заводится
паспорт, в который вносятся следующие данные: наименова-
ние и шифр приспособления; номер чертежа; наименование и
номер операции, инвентарный номер и модель станка, для
которых предназначено приспособление; дата приёмки, зак-
лючение и подписи сдатчика и приёмщика (обычно производ-
ственного и контрольного мастеров инструментального цеха).
Для внесения сведений по эксплуатации приспосбления
в паспорте предусматриваются разделы для таких данных:
время работы приспособления после приёмки (последней пе-
риодической проверки); число изготовленных деталей или
собранных изделий; замечания технологов, мастеров и рабо-
чих-станочников или сборщиков; дата и причина выхода
приспособления из строя; дата ремонта; заключение о годно-
сти; дата и подписи. Сведения из паспорта должны учиты-
ваться при конструировании подобных приспособлений.
Новые контрольные приспособления проходят наладку и
проверку на точность. Они подвергаются полному метроло-
гическому исследованию путём сопоставления результатов
измерений объектов в приспособлении с результатами изме-
рений их на более точных приборах. При этом анализируют-
ся погрешности измерения, стабильность показаний измери-
тельных элементов, надёжность работы приспособления. На
принятое контрольное приспособление оформляется аттестат,
составляется инструкция по использованию и карта перио-
дических проверок.
Организация эксплуатации приспособлений является ча-
стью планово-предупредительной системы обслуживания ос-
настки, когда межремонтное обслуживание и контроль при-
способления выполняются строго по плану, а его ремонт про-
изводится по необходимости. Межремонтное обслуживание
паспортизированных приспособлений включает эксплуатаци-
онный уход (наружный осмотр, выявление неисправностей,
смазывание и т.п.) и технический надзор за правильностью
эксплуатации и хранения. Если периодичность проверок не
предусмотрена ТУ, то их можно проводить для приспособле-
ний повышенной точности (П, обработка заготовок по 5...7-му
квалитетам точности) с периодичностью по таблице 11.1.
Таблица 11.1
Периодичность проверок приспособлений
Приспособления
| Тип производства
|
Единичное и мелкосе- рийное
| Се- рий- ное
| Крупносе- рийное и массовое
|
Период между проверками, мес.
|
1
| 2
| 3
| 4
|
Сверлильные и расточные:
|
|
|
|
подставки
| 6
| 4
| 2
|
кондукторы
| 5
| 3
| 2
|
многошпиндельные головки
| 10
| 5
| 1
|
для растачивания (горизонтального)
| 2
| 1
| 1
|
Токарные:
|
|
|
|
оправки (гладкие, шлицевые)
| 3
| 2
| 1
|
планшайбы, люнеты
| 2
| 1
| 1
|
устанавливаемые на шпиндель и суп- порт
| 5
| 3
| 2
|
патроны (поводковые, самоцентрирую- щие, кулачковые)
| 6
| 3
| 2
|
патроны и оправки с упругими зажим- ными элементами
| 5
| 2
| 1
|
Фрезерные, строгальные, долбёжные:
|
|
|
|
поворотные с вертикальной осью вра- щения
| 6
| 3
| 2
|
поворотные с горизонтальной осью вращения
| 5
| 2
| 1
|
с круговой подачей
| 4
| 2
| 1
|
для обработки зубьев шестерен
| 3
| 2
| 1
|
поворотные с наклонной осью вращения
| 5
| 2
| 1
|
Шлифовальные к станкам:
|
|
|
|
с прямолинейным движением и с верти- кальной осью вращения столов
| 4
| 2
| 1
|
с горизонтальной осью вращения стола
| 3
| 2
| 1
|
Продолжение таблицы 11.1
1
| 2
| з
| 4
|
Прочие:
|
|
|
|
с копирами для токарных и шлифоваль- ных станков
| 6
| 3
| 2
|
для протяжных работ
| 6
| 3
| 2
|
для сборочных работ
| 12
| 6
| 3
|
для опрессовочных работ
| 6
| 3
| 2
|
для сварочных работ
| 9
| 4
| 3
|
контрольные
| 2
| 1
| 1
|
Для приспособлений нормальной точности (Н, обработка
заготовок по 8... 13-му квалитетам точности) периоды между
проверками удлиняются в два раза по сравнению с приспо-
соблениями категории П.
Периодическая проверка контрольных приспособлений
в процессе их эксплуатации осуществляется цеховыми кон-
трольными пунктами, являющимися подразделениями цен-
тральной измерительной лаборатории (ЦИЛ) отдела тех-
нического контроля (ОТК), по индивидуальной инструк-
ции при наличии чертежа приспособления, аттестата и
карты периодической проверки. Приспособления с обна-
руженными дефектами и предельным износом элементов
направляются в ремонт (цеховая инструментальная служ-
ба или инструментальный цех). После ремонта приспособ-
ления вновь проходят ОТК и аттестацию. При этом приме-
няются универсальные измерительные средства и эталон-
ные детали. Последние используются для настройки конт-
рольных приспособлений, снабжённых отсчётными изме-
рительными средствами. Эталонные детали имеют паспор-
та и сами проходят периодическую проверку в ЦИЛ. О
годности приспособлений делается отметка в аттестате и
карте проверок с указанием даты и подписями работников
ОТК.
Требования эргономики и охраны труда
В процессе разработки и изготовления приспособлений
необходимо учитывать требования, обеспечивающие удобство
и безопасность эксплуатации оснастки. Оценка эргономичес-
ких свойств оснастки в совокупности со станком может осу-
ществляться при помощи координатной сетки с нанесённы-
ми на ней контурами станка, приспособления, зонами разме-
щения органов управления, местом расположения рабочего
и зонами его досягаемости (рис. 11.1). Желательно все орга-
ны управления, особенно аварийные, располагать в зонах
лёгкой досягаемости, и только редко используемые органы
(не более 5...8 раз в смену) допускается размещать за преде-
лами зоны досягаемости.
Другим эргономическим требованием является соблюде-
ние допустимых нагрузок, которые не должны превы-
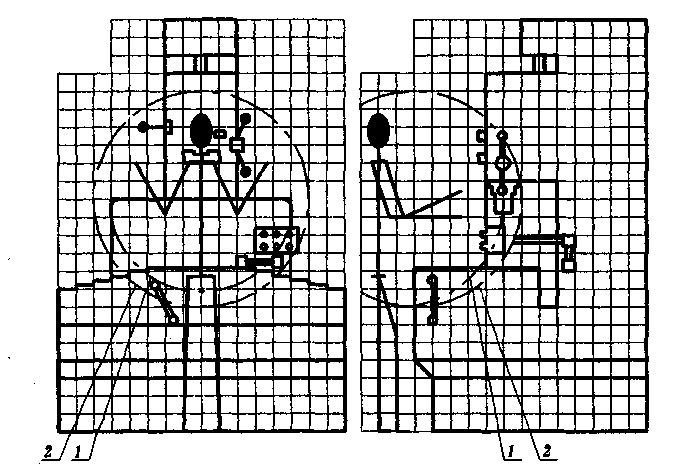
Рис. 11.1 Зоны расположения органов управления
станком и оснасткой:
1 — удобная; 2 — допустимая
шать 10 Н при работе кисти руки; 20...40 Н при работе руки
до локтя; 80... 100 Н при работе всей руки, в любом случае
сила воздействия рабочего на привод оснастки не должна пре-
вышать 150 Н. В зависимости от зоны расположения орга-
нов управления допустимые нагрузки изменяются (рис. 11.2):
Зона
| I
| II
| III
| IV
|
Сила на рукоятке, Н
| 20...40
| 40...50
| 35...50
| 55...7S
|
Рис. 11.2 Схема расположения зон размещения органов управления станком и оснасткой
|
Следует учитывать, что рукоятки с использованием
5...8 раз в смену можно располагать в зоне на высоте от 1600
до 1700 мм при работе стоя и от 600 до 1200 мм при работе
сидя; в крайних случаях допустимо размещение рукояток в
виде кнопок на высоте от 300 до 1850 мм. Органы управле-
ния, используемые только для настройки, можно распола-
гать на высоте до 2500 мм. Рекомендуется для часто исполь-
зуемых рукояток уменьшать допустимые силы по сравнению
с приведёнными выше на 20...40 %. При более чем одном
закреплении-откреплении в минуту сила ручного привода
должна снижаться со 100 (максимум 150) Н до 50 Н. Значе-
ния моментов, развиваемых рукой на рукоятках различных
конструкций и размеров, приведены в таблице 11.2.
Таблица 11.2
Предельные значения моментов М, обеспечиваемых
при различных конструктивных формах и размерах
элементов ручных зажимных устройств
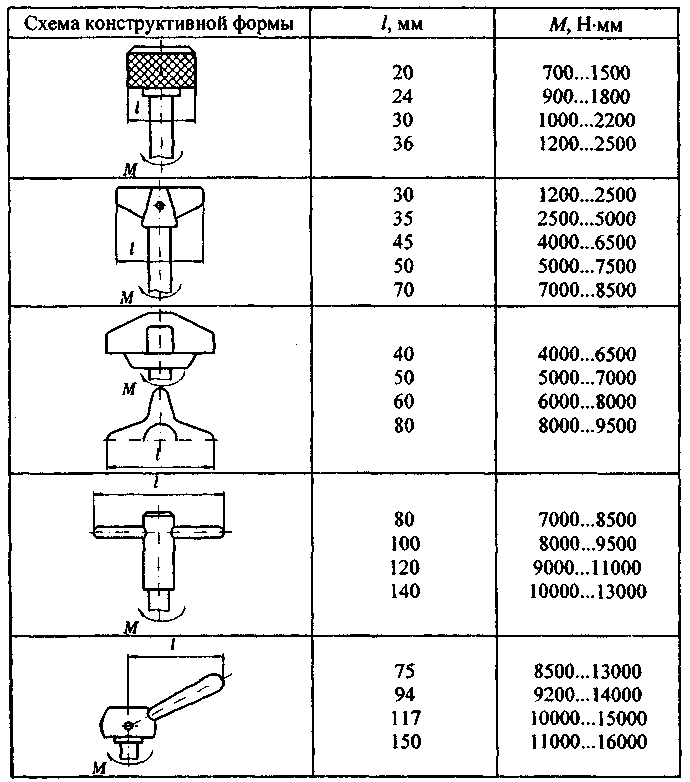
Средняя продолжительность закрепления заготовок (до-
талей, сборочных единиц) различными зажимными устрой-
ствами с: ключом в трёхкулачковом патроне — 4; одним вин-
товым зажимом (ключом) — 4,5; штурвалом — 2,5; поворо-
том рычага — 2,5; маховиком или звёздочкой — 2; поворо-
том рукоятки пневмо- или гидрокрана — 1-1,5. С увеличе-
нием числа зажатий-отжатий следует применять механизи-
рованные зажимы. Значения вспомогательного времени для
выполнения различных движений по закреплению-откреп-
лению заготовок (деталей) в приспособлениях приведены в
таблице 11.3.
Требования к безопасности приспособлений стандартизо-
ваны. В зоне расположения рукояток и маховиков должны
отсутствовать выступающие элементы (выступы, головки
винтов), которые могут нанести травму рабочему или мешать
ему. Все наружные элементы деталей приспособлений долж-
ны иметь закругления радиусом 1 мм, должны быть обтека-
емыми с малой шероховатостью и не иметь острых кромок и
углов. Расстояние от неподвижной детали до вращающегося
маховика (рукоятки) следует предусматривать не менее 30 мм.
Для маховиков диаметром более 60 мм рекомендуется рас-
стояние от неподвижной части станка, оснастки до охваты-
ваемой рукой части не менее 60 мм. На рисунке 11.3 пред-
ставлены нерекомендуемые и рекомендуемые исполнения
маховика (штурвала), кнопки, рукоятки. Консольное распо-
ложение рукоятки не должно вызывать изгиба вала 1
(рис. 11.3, в). Для обеспечения его жёсткости желательно пре-
дусмотреть в конструкции приспособления стакан 2.
Выступающие за габариты станков элементы приспособ-
лений не должны мешать работе рабочего и ограничивать
его доступ к органам управления. Для исключения травми-
рования рук при установке-снятии заготовок (деталей) в кон-
струкции приспособлений следует предусматривать специаль-
ные ниши для размещения руки, блокировочные устройства,
предотвращающие включение привода зажима или других
подвижных частей в период нахождения в рабочей зоне руки
Таблица 11.3
Время на закрепление и открепление заготовки (детали)
в приспособлениях, мин.
Способ закрепления
| Количество зажимов
| Масса заготовки (детали), кг
|
1
| 5
| 12
| 20
| Свы- ше 20
|
Закрепление в приспособлениях
|
Рукояткой пневматического или гидравлического зажимов
| 1
| 0,024
| 0,024
| 0,024
| 0,024
| 0,024
|
Рукояткой эксцентрикового зажима
| 1
2
| 0,03
| 0,034 0,054
| 0,36 0,061
| 0,065
| 0,082
|
Винтовым зажимом с помо- щью маховичка или звёздочки
| 1
2
| 0,034 0,06
| 0,042 0,076
| 0,055 0,097
| 0,068 0,12
| 0,128 0,196
|
Винтовым зажимом с помо- щью гаечного ключа
| 1 2 3 4
| 0,094 0,153
| 0,11 0,18 0,24 0,3
| 0,135 0,22 0,29 0,39
| 0,16 0,26 0,35 0,44
| 0,2 0,32 0,42 0,55
|
Винтовым зажимом с быстро- съёмной шайбой с помощью гаечного ключа
| 1
| 0,085
| од
| 0,12
| 0,135
| 0,17
|
Рукояткой пневматического зажима и винтовым зажимом
| 2
| 0,052
| 0,06
| 0,071
| 0,083
| 0,137
|
Рукояткой эксцентрикового зажима и винтовым зажимом
| 9
| 0,058
| 0,068
| 0,082
| 0,095
| 0,154
|
Закрепление отки
| цной или скользящей планкой
|
Рукояткой пневматического зажима
| 1
| 0,034
| 0,042
| 0,046
| 0,05
| 0,06
|
Рукояткой эксцентрикового зажима
| 1
| 0,04
| 0,052
| 0.058
| 0,064
| 0,079
|
Винтовым зажимом вручную
| 1
| 0,044
| 0,06
| 0,077
| 0,094
| 0,163
|
Винтовым зажимом с помо- щью гаечного ключа
| 1
| 0,104
| 0,123
| 0,157
| 0,186
| 0,235
|
Рукояткой пневматического зажима и винтовым зажимом
| 2
| 0,062
| 0,078
| 0,093
| 0Д09
| 0,172
|
рабочего. В целях устранения попадания руки или пальца
рабочего в зазоры между подвижными элементами конструк-
ции их ширину следует предусматривать не более 5 мм.

Piic. 11.3 Примеры исполнения маховика, штурвала (а),
кнопки (б) и рукоятки (в)
Приспособление должно быть надёжно закреплено на стан-
ке, сбалансировано, проверено на рабочих частотах враще-
ния, а значения допускаемых частот вращения и неуравно-
вешенности следует указывать в паспорте и других эксплуа-
тационных документах.
У приспособлений для обработки заготовок следует пре-
дусматривать каналы, окна, ниши для отвода, размещения
и беспрепятственного удаления стружки. В этих целях воз-
можно использование потока СОЗК. Для защиты от разлета-
ющейся стружки необходимо применять специальные экра-
ны. С целью удаления загрязнённого при обработке специ-
фических материалов воздуха и СОЖ желательно предусмат-
ривать отсасывающие и отводные устройства.
Вручную допускается устанавливать оснастку массой до
16 кг. В приспособлениях массой более 16 кг должны пре-
дусматриваться устройства в виде рым-болтов, цапф, отвер-
стий и т.п., обеспечивающие надёжный захват, безопасное
перемещение и установку грузоподъёмными средствами. При
массе обрабатываемых заготовок более 12 кг также должны
использоваться грузоподъёмные средства и предусматривать-
ся специальные площадки для предварительной их уста-
новки с последующим безопасным перемещением в рабо-
чую зону.
Особо следует остановиться на недопустимости раскреп-
ления заготовок во время их обработки из-за отказа при-
вода, падения давления в пневмо-, гидросетях, отключе-
ния электроэнергии. В этих целях в конструкциях оснаст-
ки следует применять самотормозящиеся зажимные уст-
ройства (винтовые, клиновые, эксцентриковые), исключа-
ющие возвратные перемещения зажимных элементов. В
случае невозможности применения таких устройств следу-
ет ограждать рабочую зону приспособлений специальными
экранами.
Гидравлические и пневматические устройства оснастки
должны быть испытаны под давлением, в 1,5 раза превыша-
ющим номинальные (рабочие), с выдержкой 5... 10 мин., о
чём делается отметка в паспорте с указанием допускаемого
срока эксплуатации. Следует исключать выброс отработав-
шего сжатого воздуха в сторону рабочего, так как он может
содержать и увлекать за собой частицы абразива, стружки и
быть причиной травмы. Пневмо- и гидросистемы должны быть
оборудованы устройствами для контроля давления и с оп-
ломбированными элементами, разрегулирование которых
может создать аварийную ситуацию.
Электромеханические и электромагнитные приспособ-
ления должны быть надёжно заземлены и защищены от
влаги. При использовании электропривода необходимо ис-
ключить самопроизвольное его включение; токоведущие
части требуется надёжно изолировать; следует предусмот-
реть средства световой сигнализации и аварийного отклю-
чения, вводный выключатель всей системы питающей сети,
необходимые блокировки; должна осуществляться перио-
дическая проверка электросистемы на надёжность изоля-
ции и заземления.
К органам управления, которыми недопустимо пользо-
ваться при перемещении (вращении) приспособлений, долж-
ны крепиться указатели с предупредительными надписями,
хорошо читаемыми на расстоянии не менее 500 мм. Элемен-
ты приспособлений, нагревающиеся в процессе эксплуата-
ции до температуры выше 318 К, должны быть теплоизоли-
рованы или ограждены щитками.
Открытые элементы, перемещающиеся со скоростью бо-
лее 9 м/мин., и вращающиеся приспособления должны
иметь ограждения и предохранительные кожухи. В мес-
тах приспособлений, где в условиях эксплуатации возможно
самоотвинчивание гаек и винтов, необходимо предусмот-
реть контргайки, шплинты и другие предохранительные
устройства.
Наладка, обслуживание и ремонт приспособлений на ра-
ботающих станках не допускаются. Следует обращать вни-
мание на уровни возможной вибрации и шума, которые не
должны превышать допустимые санитарные нормы.
11.4 Примерная тематика
лабораторно-практичееких и курсовых работ
1. Изучение и анализ реальных приспособлений.
2. Определение сил закрепления заготовки в станочном
приспособлении и их экспериментальная проверка.
3. Исследование факторов, влияющих на силу закрепле-
ния заготовок на магнитной плите.
4. Расчёт и экспериментальная проверка потребного дав-
ления в гидропластмассовой оправке для создания по-
требного момента трения между заготовкой и тонко-
стенной оболочкой.
5. Экспериментальные исследования сил закрепления за-
готовок при использовании пневмоцилиндров, пневмо-
камер и вакуумных устройств.
6. Исследование погрешности установки заготовок в раз-
личных приспособлениях.
7. Исследование погрешности базирования при различ-
ных схемах приспособлений.
8. Анализ и расчёт приспособлений на прочность по чер-
тежам с обоснованием выбора материалов.
9. Исследование точности делительных механизмов при-
способлений.
10. Исследование точности обработки отверстий сверле-
нием свёрлами без направления и с направлением кон-
дукторными втулками.
11. Проектирование и компоновка приспособлений из УСП.
12. Исследование точности и производительности конт-
рольных приспособлений.
13. Исследование производительности сборочных приспо-
соблений.
14. Расчёт и разработка схемы приспособления для вы-
полнения одной из операций обработки заготовки или
сборки сборочной единицы.
15. Расчёт и разработка схемы приспособления для обра-
ботки заготовок ППД.
16. Определение экономической эффективности примене-
ния приспособлений различного типа.
В курсовом и дипломном проектах по технологии маши-
ностроения традиционно выполняются разделы по констру-
ированию новых и модернизации существующих приспособ-
лений. В них представляются обоснование конструкций, их
механизация и автоматизация, полный расчёт приспособле-
ний, формируются технические условия изготовления и экс-
плуатации. В курсовом проекте разрабатывается одна конст-
рукция приспособления для установки заготовки или инст-
румента, для контроля заготовок или сборочных единиц. В
дипломном проекте этот раздел обычно представляется в виде
конструкций двух приспособлений (станочного и контрольно-
го, станочного и сборочного и т.п.). При этом одно из приспо-
соблений желательно автоматизировать или сделать встро-
енным в станок-автомат или в автоматическую линию.
Контрольные вопросы
1. Каковы особенности изготовления технологической ос-
настки и где разрабатывается документация на неё?
2. В чём заключается приёмка изготовленной оснастки и
какие документы при этом оформляются?
3. Как осуществляется техническое обслуживание и ре-
монт оснастки на заводах?
4. В чём заключается планово-предупредительная систе-
ма обслуживания и ремонта оснастки?
5. Каким требованиям эргономики должны соответство-
вать разрабатываемые приспособления?
6. Как обеспечиваются требования охраны труда и безо-
пасности работы в конструкции оснастки?
7. В чём состоит повседневный уход за эксплуатируемым
приспособлением?
ПРИЛОЖЕНИЕ 1
Пример расчёта и конструирования приспособления
Общая часть.
Задание: спроектировать приспособление к специально-
му двухшпиндельному станку для одновременного сверле-
ния отверстий 06 и 010,5 в вале ступенчатом по чертежу
(рис. П1). Остальные поверхности вала обработаны в разме-
ры по чертежу.
Исходные данные: годовой объём выпуска деталей
N = 120000 шт. Производство крупносерийное. Работа одно-
сменная. Принятый режим сверления отверстий:
а) 06; Sol = 0,18 мм/об; пх = 540 об/мин. (при этом
и1 = Юм/мин.; SM 1 = 97 мм/мин.; Рг = ИЗО Н;
Мх = 3450 Н-м);
б) 010,5; So 2 = 0,3 мм/об; п2 = 310 об/мин. (при этом
у0 = 10,2 м/мин.; SM 2 = 93 мм/мин.; Р2 = 3070 Н;
М2 = 1460 Н-м).
Рис. П1 Чертёж вала ступенчатого
|
Расчётное основное (технологическое) время сверления
t 0 = 0,45 мин., масса детали 1 кг. Материал детали — сталь
20Х (ав = 750 МПа, НВ 180). Неуказанные предельные от-
клонения размеров: охватывающих — по HI4, охватывае-
мых — по Ы4, других — ± Н14/2; отклонения от соосности
поверхностей А, Б и В не более 0,1 мм.
Принятие решений. Анализ обрабатываемой заготовки,
выбор элементов приспособления и схемы установки. Из рас-
смотрения чертежа детали (рис. П1) следует, что обрабаты-
ваемые отверстия 06 и 010,5 выполняются по 14-му квали-
тету точности (Н14). Точность диаметральных размеров обес-
печивается инструментами (свёрлами), точность положения
осей отверстий 06 и 010,5 относительно осей цилиндричес-
ких поверхностей А и Б и торца Г — базированием заготов-
ки и точностью положения направляющих элементов для
свёрл относительно установочных элементов приспособления.
Точность положения отверстия 010,5 относительно отвер-
стия 08 (поверхность Д) должна обеспечиваться базирова-
нием и относительным положением установочного элемен-
та, базирующего заготовку по поверхности Д, и направляю-
щего элемента инструмента (сверла).
Из анализа заготовки видно, что для установки её в при-
способление за базы следует принять поверхности А, В, Г и
Д. В качестве установочных элементов для базирования за-
готовки целесообразно использовать:
а) две призмы — базирование по цилиндрическим повер-
хностям А и В;
б) торец призмы, в которую вал устанавливается цилинд-
рической поверхностью А — базирование в осевом на-
правлении по торцу буртика вала (поверхность Г);
в) плавающий конический срезанный ромбический па-
лец-фиксатор — базирование по поверхности Д отвер-
стия 08.
Для уменьшения числа зажимных элементов целесооб-
разно зажимать заготовку по верху поверхности Б одним
вилкообразным прихватом (рычагом). В качестве направ-
ляющих элементов для свёрл принимаются кондукторные
втулки.
; Схема базирования, закрепления и обработки заготовки
(рис. П2). Заготовка 9 размещается в призмах 1 и 2 с упо-
ром поверхностью Г бурта в торец призмы 2. Плавающий
конический палец 3 под действием пружины входит в от-
верстие 08 и исключает поворот заготовки 9 относительно
оси. Для направления сверла 4 служит горизонтальная кон-
дукторная втулка 5 (06F7), сверла 6 — вертикальная втул-
ка 7 (010,5F7). В качестве зажимного элемента использо-
ван вилкообразный прихват 8.
Схема приспособления. В соответствии с заданием при-
нимается схема одноместного однопозиционного приспособ-
ления.
Рис. П2 Схема базирования, закрепления и обработки
Заготовки