После обоснованного выбора расчётных параметров сле-
дует приступить к непосредственному расчёту приспособле-
ния на точность, т.е. определить точность изготовления при-
способления по принятым параметрам. Ниже изложены от-
работанные приёмы практического выявления значений рас-
чётных параметров и приемлемая для инженерного исполь-
зования методика расчёта приспособления на точность.
На точность обработки влияет ряд технологических фак-
торов, вызывающих общую погрешность обработки е0, кото-
рая не должна превышать допуск д выполняемого размера
при обработке заготовки, т.е. е0 < д.
Для выражения допуска 5, выполняемого при обработке
размера, следует пользоваться формулой:
где Лу — погрешность
вследствие упругих отжатий техноло-
гической системы под влиянием сил резания;
Ан — погрешность настройки станка;
£ — погрешность установки заготовки в приспособлении;
Аи — погрешность от размерного изнашивания инстру-
мента;
Ат — погрешность обработки, вызываемая тепловыми де-
формациями технологической системы;
Т,Дф — суммарная погрешность формы обрабатываемой
поверхности, обусловленная геометрическими погрешностя-
ми станка и деформацией заготовки при обработке и входя-
щая в 5, так как погрешность формы поверхности находится
в пределах поля допуска её размера.
По приведённой формуле можно найти е, принимая её за
допустимое значение погрешности установки е' заготовки в
приспособлении
:
Погрешность установки заготовки в приспособлении как
суммарное поле рассеяния случайных величин определяется
из выражения:

где ?б — погрешность базирования заготовки в приспособ-
лении;
е3 — погрешность закрепления заготовки, возникающая
в результате действия сил зажима;
Апр — погрешность положения заготовки, зависящая от
приспособления.
Дпр — s np + e y + E u»
здесь enp — погрешность изготовления приспособления по выб-
ранному параметру, зависящая от погрешностей изготовления
и сборки установочных и других элементов приспособления;
еу — погрешность установки приспособления на станке;
еи — погрешность положения заготовки, возникающая в
результате изнашивания элементов приспособления).
Для принятой схемы установки обязательно должно вы-
полняться условие е < е'. В противном случае следует изме-
нить построение операции обработки или схему установки
заготовки в приспособлении.
Указанные составляющие Апр представляют собой поля
рассеяния случайных величин. Значение Лпр изменяется в
зависимости от условий и типа производства, а также от осо-
бенностей конструкции приспособления. При использовании
приспособления в мелкосерийном и серийном производствах:
КР = £пР +№+ Зе*.
Здесь епр рассматривается как постоянная величина, ко-
торая может компенсироваться настройкой станка.
В массовом и крупносерийном производствах при исполь-
зовании одноместных приспособлений Лпр = £„ операции строго
закреплены за рабочими местами, епр и еу компенсируются
настройкой технологической системы.
В случае применения многоместных приспособлений:
л пР = у[4р + з4 •
Если используются одновременно много или несколько
экземпляров одного приспособления, например, приспособ-
ления-спутника на автоматической линии:
/2 2 2
АПр ~ \епр + еу + Зеи •
Кроме того, если в приспособлении предусмотрены эле-
менты для направления и определения положения или тра-
ектории перемещения обрабатывающего инструмента (кон-
дукторные втулки, копиры и т.д.), в общей погрешности об-
работки заготовки может появиться ещё одна составляющая
погрешность от перекоса еп инструмента.
Итак, при использовании в работе нескольких (многих)
приспособлений общая погрешность обработки, приравнен-
ная допуску на выполняемый размер, определяется зависи-
мостью:

Отсюда погрешность изготовления приспособления:

По приведённой формуле можно находить значение рас-
чётного параметра приспособления, которым и будет епр.
В связи со сложностью нахождения значений ряда вели-
чин, входящих в приведённую выше формулу для определе-
ния епр, погрешность изготовления приспособления можно
рассчитывать по упрощённым формулам. Расчёт епр при этом
сводится к вычитанию из допуска выполняемого размера всех
других составляющих общей погрешности обработки:
(8.1)
где S — допуск выполняемого при обработке размера заго-
товки;
km — коэффициент, учитывающий отклонение рассеяния
значений составляющих величин от закона нормального рас-
пределения: km = 1...1.2 (в зависимости от количества значи-
мых слагаемых: чем их больше, тем ближе к единице следу-
ет принимать значение коэффициента);
kmi — коэффициент, учитывающий уменьшение предель-
ного значения погрешности базирования при работе на на-
строенных станках: knl = 0,8...0,85;
km 2 — коэффициент, учитывающий долю погрешности
обработки в суммарной погрешности, вызываемой фактора-
ми, не зависящими от приспособления (Лу, Лн, Ли, Лт, Лф),
km 2 = 0,б...0,8 (большее значение коэффициента принимает-
ся при меньшем количестве значимых величин, зависящих
от приспособления);
со — экономическая точность обработки.
Выбранное по таблицам для данных условий значение а>
следует понимать как среднюю экономическую точность об-
работки. Произведением km 2 a > характеризуется суммарная
погрешность обработки, вызываемая факторами, не связан-
ными с приспособлением, а именно: упругими отжатиями
технологической системы под действием сил резания (Лу),
погрешностью настройки станка (Лн), размерным износом
инструмента (Ли), тепловыми деформациями системы (Лт),
геометрическими погрешностями станка и деформацией за-
готовки при обработке (ZAm). Такой путь определения сум-
марного значения указанных погрешностей, не зависящих
от приспособления, вполне оправдан, тем более в условиях
подготовки производства новых изделий.
Погрешности, зависящие от приспособления (еб, е3, su
и £„), рассчитываются в каждом конкретном случае по при-
нятым схемам базирования, закрепления и обработки. По-
грешность закрепления е3 может также приниматься по
таблицам.
Найденное значение выбранного параметра указывается
в качестве допуска отклонения поверхностей или размера
между поверхностями, контактирующими соответственно с
заготовкой и станком, на чертеже общего вида или записы-
вается в ТУ на изготовление и эксплуатацию проектируемо-
го приспособления.
Вычитаемые из допуска составляющие общей погрешно-
сти обработки можно суммировать и арифметически. При
этом отпадает необходимость коэффициента km и уменьша-
ется значение полученной погрешности приспособления епр.
Такой путь расчёта можно рекомендовать применительно к
прецизионным приспособлениям, создаваемым для обеспе-
чения повышенной точности обработки при изготовлении
прецизионных, наиболее ответственных деталей машин и
приборов.
Расчёт на точность кондукторов можно выполнять также
по формуле (8.1). В этом случае полученная погрешность
изготовления приспособления будет являться допуском меж-
центрового расстояния между его кондукторными втулками.
При сверлении отверстий по кондуктору половину допуска
расстояния между осями кондукторных втулок (расчётный
параметр) можно определить при условии, что середины по-
лей допусков межцентровых расстояний в деталях и кондук-
торной плите совпадают (рис. 8.2), по формуле:
(8.2)
где 6 — односторонний допуск расстояния между осями от-
верстий в заготовке (детали);
Јs — сумма максимальных радиальных зазоров;
£е — сумма эксцентриситетов втулок;
Цепр — сумма погрешностей от перекоса инструментов,
которые рассчитываются по формулам (3.4) и (3.5).
Сумма максимальных односторонних радиальных зазо-
ров (рис. 8.2) определяется из выражения

где Sj и s2 — максимальные радиальные зазоры соответствен-
но между сменными и постоянными втулками;
s3 и s 4 — максимальные зазоры между втулками и инст-
рументом (с учётом износа втулок).
Сумма эксцентриситетов
находится следующим образом:
где e - i и е2 — допуски соосности сменных втулок;
е3 и е4 — допуски соосности постоянных втулок.
Обычно ех = e < i = е3 — е4 = 0,005 мм.
При определении допуска расстояния между базовой плос-
костью и осью кондукторной втулки в приведённых выраже-
ниях для определения Јs и Ze по формуле (8.2) s 2, s 4, e 2, e4
принимаются равными нулю. Полученное по формуле (8.2)
значение епр является половиной допуска расстояния между
осями кондукторных втулок или базовой плоскостью при-
способления и осью кондукторной втулки, т.е. размер L в
данном случае должен иметь допуск ±епр (рис. 8.2).
Рис. 8.2 Схема для расчёта суммы максимальных зазоров
|
Один из последних этапов расчёта приспособления на
точность — разбивка допуска размера при его изготовлении
на допуски размеров деталей, которая может осуществлять-
ся решением размерных цепей или по опытным данным. В
первом случае за замыкающее звено размерной цепи прини-
мается погрешность по принятому параметру епр, являюща-
яся допуском изготовления приспособления. После выявле-
ния размерной цепи решается прямая задача, т.е. определя-
ются размеры и допуски звеньев размерной цепи. Во втором
случае разбивка выполняется по принципу: чем сложнее до-
стижение требуемой точности, сложнее деталь и протяжение
её поверхности, тем большая часть допуска приспособления
идёт на допуск размера и наоборот.
8.3 Расчётные факторы и выбор их значений
Для выявления допустимой погрешности изготовления
(точности) приспособления следует рассчитывать епр по фор-
муле (8.1), определив или выбрав по справочным источни-
кам значения всех её составляющих.
Допуск 8 берётся с чертежа детали (при окончательной
обработке поверхностей) или с операционного эскиза техно-
логического процесса обработки заготовки (при предваритель-
ной обработке).
Значения коэффициентов следует принимать в следую-
щих пределах: km = 1,2; kml = 0,8...0,85; km 2 = 0,6...0,8.
Погрешность базирования определяется или рассчитыва-
ется в каждом конкретном случае. В таблице 8.1 представле-
ны схемы базирования и формулы, по которым следует опре-
делять погрешности базирования для некоторых типовых
случаев. Приняты следующие обозначения:
ее — смещение (эксцентриситет) оси отверстия относи-
тельно оси наружной цилиндрической поверхности;
8 D — допуск диаметра наружной поверхности;
s min — односторонний минимальный гарантированный
зазор;
8А — допуск размера базового отверстия;
8В — допуск размера оправки (пальца);
Ац — просадка центров.
Таблица 8.1
Погрешность базирования при обработке в приспособлениях
Погрешность базирования для размеров
|
По центровым отверстиям на жесткий пе- редний центр
|
Продолжение таблицы 8.1
На плавающий
передний
центр
|
По внешней поверхности в
зажимной цанге по упору
|
В самоцентри- рующем па- троне с упором торцом
|
(при параллельном подрезании торцов)
|
В самоцентри- рующих приз- мах
|
На плоской поверхности при обработ- ке отверстия по кондукто- ру
|
Продолжение таблицы 8.1
В призме при
обработке
плоскости или
паза
|
При установке оправки на пла- вающий передний центр, в гиль- зу или патрон по упору,
|
По отверстию на жёсткой оправке со
свободной по- садкой
|
где 8В и 8А — допуски соответст- венно на диаметры оправки и отверстия
|
Продолжение таблицы 8.1
На разжимной оправке, на жёсткой оп- равке с натя- гом
|
При установке оправки на жёст- кий передний центр
|
По двум отвер- стиям на паль- цах при обра- ботке верхней поверхности
|
По плоскости
при обработке
уступа
|
Просадка центров определяется в зависимости от наиболь-
шего диаметра центрового гнезда следующим образом:
Наибольший диаметр центрового гнезда, мм
| 1;2;2,5
| 4; 5; 6
| 7,5; 10
| 12,5; 15
| 20; 30
|
Просадка центров Д,, мм
| 0,11
| 0,14
| 0,18
| 0,21
| 0,25
|
Погрешность закрепления е3 можно определять аналити-
чески в случае, когда рассчитывают весьма малые смещения
заготовок в прецизионных приспособлениях. Иногда в целях
более точного определения е3, прецизионных приспособле-
ний возникает необходимость целенаправленных исследова-
ний. В подавляющем большинстве случаев для расчёта при-
способлений на точность е3 принимается по таблицам техно-
логических справочников и источников.
Погрешность установки приспособления на станке воз-
никает из-за зазоров между направляющими шпонками или
установочными пальцами приспособления и Т-образными
пазами или отверстиями стола станка, что характерно для
фрезерных, расточных и других приспособлений. Для умень-
шения этих погрешностей рекомендуется точнее изготавли-
вать посадочные места, а элементы для ориентации приспо-
соблений на станках следует располагать на корпусе приспо-
собления как можно дальше друг от друга.
Погрешность установки вращающихся приспособлений
на токарные, зубофрезерные и другие станки зависит от
точности их базирования в гнёздах станка (конусное отвер-
стие шпинделя, центральное отверстие поворотного стола,
центрирующий поясок шпинделя или планшайбы станка и
т.д.). Если приспособление базируется на центрирующий
поясок шпинделя (планшайбы), то погрешность положения
в виде отклонения от соосности (эксцентриситета) осей
шпинделя и устанавливаемого приспособления возникает
из-за имеющегося зазора между выточкой корпуса приспо-
собления (например, трёхкулачкового патрона) и центри-
рующим пояском шпинделя или планшайбы. Расчёт еу в
каждом конкретном случае следует вести по схеме установ-
ки приспособления на станке, что иллюстрирует приведён-
ный ниже пример.
Заготовка (рис. 8.3, а) 3 устанавливается на палец 2 при-
способления (рис. 8.3, б) для обработки паза в размеры сип
и поджимается к поверхности Е пальца 2 гайкой 5 с помо-
щью быстросъёмной шайбы 4.
Одним из требований к изготавливаемой детали являет-
ся отклонение осей паза А и базового отверстия Б в преде-
лах, не превышающих 0,1 мм на длине детали т. Расчётны-
ми параметрами при расчёте приспособления на точность
выбраны:
1) для выполнения условия обеспечения заданного поло-
жения осей паза А и отверстия Б заготовки — допуск
параллельности осей рабочей цилиндрической поверх-
ности Б диаметром d пальца 2, на который устанавли-
вается заготовка 3, относительно боковой поверхнос-
ти Г (оси) направляющих шпонок 6 корпуса 1 приспо-
собления;
2) для выполнения размера п из условия, что допуск па-
раллельности поверхностей Д паза относительно оси
отверстия Б должен быть в пределах допуска 8п на длине
заготовки — допуск параллельности оси установочно-
го элемента (пальца) 2 к установочной плоскости В
корпуса 1 приспособления.
Погрешность установки приспособления относительно
Т-образных пазов стола 7 станка влияет на первое условие,
т.е. на точность положения оси паза А относительно оси от-
верстия Б (рис. 8.3).

Рис. 8.3 Схема фрезерного приспособления (б)
для обработки заготовок (а)
На виде сверху приспособления показано относительное
положение направляющих шпонок и Т-образных пазов стола
станка. Если принять, что ширина пазов стола 8 мм, а посад-
ка между шпонками 6 и пазами стола 8!о'о!б мм» то с Учё-
том допуска на изготовление шпонки по размеру 8_0 025 мм
и Т-образного паза стола станка по ширине 8+ ' мм макси-
мальный возможный зазор между шпонками 6 и Т-образны-
ми пазами стола s = 0,05 мм. Наиболее неблагоприятна уста-
новка приспособления, когда одна направляющая шпонка
поджата к одной стороне паза стола, а вторая — к другой. В
этом случае приспособление повернётся на какой-то угол a, a
отклонение параллельности осей установочного пальца отно-
сительно Т-образных пазов стола станка, а значит и относи-
тельно траектории оси движения инструмента (фрезы), при
обработке паза увеличится на значение неточности установ-
ки приспособления на станке.
Погрешность установки приспособления еу в рассмат-
риваемом случае в соответствии со схемой, изображённой
на рисунке 8.4, можно определить следующим образом. При
проведении через точку 02 линии, параллельной 0\0'2 воз-
никает треугольник К\0'2, катет которого равен максималь-
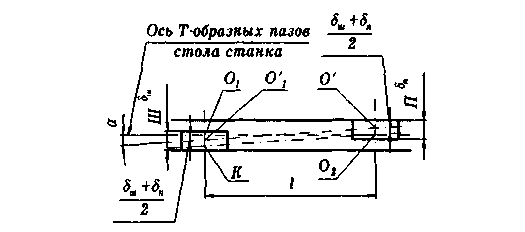
Рис. 8.4 Схема расчёта погрешности установки
фрезерного приспособления:
8Ш — допуск на ширину Ш направляющих шпонок;
5п — допуск на ширину П Т-образного паза станка
ному возможному зазору s = <5„ + <5Ш = 0,05 мм. Это и будет
допуском параллельности осей направляющих шпонок и
Т-образного паза стола станка на длине, равной расстоя-
нию между шпонками I. Для подстановки погрешности ус-
тановки в формулу (8.1) нужно привести полученное зна-
чение допуска параллельности шпонок относительно оси
Т-образного паза к длине детали. В целом погрешность ус-
тановки Еу приспособления на станке для данного случая
можно выразить формулой:

где т — длина детали, мм;
s — наибольший зазор между направляющими шпонка-
ми приспособления и Т-образным пазом стола станка, мм;
I — расстояние между шпонками, мм.
Если т = 50 мм, а I = 80 мм, то по формуле (8.3) по-
грешность установки приспособления на станке на длине
детали:

Погрешность положения обрабатываемых отверстий в за-
готовке, связанная с перекосом и смещением обрабатываю-
щего инструмента (погрешность от перекоса), еп возникает
из-за неточности изготовления направляющих элементов при-
способления. При расчёте еп следует руководствоваться схе-
мой (рис. 8.5) направления обрабатывающего инструмента.
Для уменьшения износа кондукторной втулки между её ниж-
ним торцом и поверхностью заготовки предусматривается рас-
стояние т, через которое выбрасывается стружка. При свер-
лении чугуна и других хрупких материалов т = (0,3...0,5)d;
при сверлении стали и других вязких материалов т = d; при
зенкеровании т < 0,3d (d — диаметр инструмента).
От значения т зависит точность положения оси просвер-
ленного отверстия. Если перекоса сверла нет, то максималь-

Рис. 8.5 Схема расчёта перекоса и смещения сверла
в кондукторной втулке
ное смещение Sj оси сверла от среднего положения равно по-
ловине наибольшего диаметрального зазора 2вг (рис. 8.5). При
перекосе сверла во втулке к параллельному смещению оси
отверстия Si прибавляется смещение s 2, оно, пропорционально
углу а перекоса и расстоянию т.
Суммарное смещение инструмента s = sx + s 2.
При расчёте кондуктора на точность по формуле (8.2)
смещение s 2 представляет собой погрешность от перекоса
инструмента и рассчитывается по следующим зависимостям:
при т > 0,3d
(8.4)
при т = 0
(8.5)
где I — длина направляющего элемента (втулки, рис. 8.5), мм;
-Ш- d — диаметр инструмента, мм;
"к sx — односторонний максимальный зазор между втул-
кой и инструментом, мм.
Значение еп должно дополнительно учитываться при рас-
чёте максимального смещения инструмента относительно оси
направляющего инструмента (кондукторной втулки).
В случае расчёта на точность приспособления, имеющего
направляющие элементы в виде втулок, по формуле (8.1) в
качестве погрешности от перекоса (смещения) инструмента
следует принимать значение s, т.е. при т > 0,3d

при т = 0

Если в приспособлении нет направляющих элементов,
погрешность от перекоса (смещения) инструмента при расчё-
те на точность не учитывается, т.е. еп = 0.
Составляющая общей погрешности положения заготов-
ки еп характеризует изменение положения рабочих поверх-
ностей установочных элементов в результате их изнашива-
ния в процессе эксплуатации приспособления. На интен-
сивность изнашивания установочных элементов влияют их
размеры и конструкция, материал и масса обрабатываемой
заготовки, состояние её базовых поверхностей, а также ус-
ловия установки заготовки в приспособление и снятие её.
Наибольшему изнашиванию подвержены постоянные и
регулируемые точечные опоры, у которых контакт с заготов-
кой осуществляется по малым площадкам. Сильно изнаши-
ваются рабочие поверхности призм, контактирующие с заго-
товкой по узким площадкам, менее интенсивно-опорные пла-
стины, а также цилиндрические пальцы и другие установоч-
ные элементы, у которых контакт с заготовкой происходит
по большим площадям.
Приспособления изнашиваются сильнее, если на них об-
рабатываются заготовки с черновыми базовыми поверхнос-
тями со следами окалины и формовочных материалов (пес-
ка, земли). Изнашивание возрастает с увеличением массы
заготовок и удлинением пути их перемещения (сдвига) по
установочным элементам при их установке в приспособле-
ние и снятии с него.
Изнашивание по поверхности установочных элементов
неравномерно во времени и часто носит местный характер.
Например, опорные пластины больше изнашиваются с одного
края или в середине, а пальцы — со свободного конца. Изна-
шивание установочных элементов с рифлениями и сферичес-
кой головкой, призм и ромбических (срезанных) пальцев про-
исходит в первый период работы быстро, а затем замедляется,
подчиняясь параболическому закону. Более равномерно изна-
шивание опор с развитой несущей поверхностью.
Износ установочных элементов приближенно можно оп-
ределить по формулам:
для опор с малой поверхностью контакта
И = pxN; (8.6)
для опор с развитой поверхностью контакта
H = /32 N; (8.7)
где И — размерный износ опоры, мкм;
Pv Ръ — постоянные, зависящие от вида установочных
элементов и условий контакта (выбираются по табл. 8.2
[5, 10]);
N — количество контактов заготовки с опорой (устано-
вок в приспособлении, снятий с него) в год;
п = 0,4...0,6, приближённо п = 0,5.
Допустим, заготовка в виде плиты устанавливается обра-
ботанной стороной на опорные пластины из стали У8 в при-
способление и обрабатывается с противоположной стороны в
размер по высоте. Объём выпуска деталей — 6000 штук в
год, т.е. N = 6000. По таблице 8.2 выбирается р2 = 0,003.
Таблица 8.2
Значения коэффициентов ($1 и J 32
для различных установочных элементов
Материал установочных элементов
|
|
Установочные элементы
| Стали 20, 20Х, 45
| Углероди- стые ста- ли У8А и Другие
| Хромовое покрытие
| Твёрдые сплавы твер- досплавные наплавления
|
| Коэффициент J3i
|
|
|
Точечные опоры с го- ловкой: сферической
| 0,5...2
| 0,4.-1,8
| 0,2...0,8
| 0,06...0,25
|
рифлёной
| 0,6...2,5
| —
| —
| —
|
плоской
| 0,4...0,8
| —
| —
| —
|
Призмы (при установке заготовок обработанны- ми базами)
| 0,3...0,8
| 0,25...0,7
| 0,12...0,32
| 0,035...0,095
|
Пальцы ромбические (срезанные)
| 0,2...0,6
| 0,15...0,5
| 0,08...0,24
| 0,025...0,07
|
| Коэффициент /8г
|
|
|
Пластины опорные
| 0,002... 0,004
| 0,0015... 0,0035
| 0,0008... 0,0016
| 0,00025... 0,00045
|
Пальцы цилиндрические
| 0,001... 0,002
| 0,0008... 0,0018
| 0,0004... 0,0008
| 0,00012... 0,00023
|
Примечание. Большие значения /?, и ft, принимаются для более тяжёлых
условий работы установочных элементов по нагрузке, пути сдвига, вре-
мени неподвижного контакта и абразивному действию заготовки.
Затем по формуле (8.7) определяется износ:
И = 0,003 • 6000 = 24 мкм = 0,024 мм.
Полученное значение может быть принято за погрешность
от изнашивания установочных элементов либо полностью (в
случае большого допуска выполняемого при обработке разме-
ра), либо частично (в случае жёсткого допуска). Если в расчё-
те приспособления на точность будет принято еи = И= 0,024 мм,
то в ТУ приспособления следует вписать пункт об обязатель-
ной проверке приспособления на точность и замене или ре-
монте установочных элементов после года работы.
В случае, если
, в ТУ нужно указать пункт о про-
верке на точность и замене (ремонте) установочных элемен-
тов через 1/г года. Например,

Тогда в ТУ нужно вписать время работы приспособления
до контроля и ремонта 0,25 года или 3 мес.
При малом износе приспособления и нежёстких по до-
пускам выполняемых размерах заготовки значение еи может
приниматься больше значения И, т.е. еи = Иг. Ресурс работы
приспособления до контроля и ремонта в этом случае возра-
стает до г лет.
Допуски на износ направляющих элементов приспособ-
лений принимаются из соображений, изложенных в разде-
ле 1.4. Допуски на износ кондукторных втулок приведены в
таблице 1.1.
Принятое значение допустимого износа кондукторных
втулок следует считать погрешностью от изнашивания ей
направляющих элементов при расчёте кондукторов на точ-
ность. Погрешность от изнашивания и кондукторных втулок
необходимо учитывать при определении максимальных за-
зоров между инструментом и направляющими элементами
приспособлений.
Сроки контрольных проверок кондукторов следует опре-
делять по данным раздела 1.4, о чём необходимо указывать
в ТУ сборочного чертежа.
Последним расчётным фактором при расчёте приспособ-
ления на точность является экономическая точность обра-
ботки w, которую, исходя из экономически оправданной точ-
ности для принятого метода обработки можно определять по
таблицам технологических справочников и источника.
8.4 Пример расчёта станочного приспособления
на точность
Рис. 8.6 Схема приспособления (а) для фрезерования заготовки (б) на горизонтально-фрезерном, станке
|
Заготовка (рис. 8.6, б) обрабатывается по поверхностям
И, Л, М, Н в приспособлении (рис. 8.6, а) на горизонтально-
фрезерном станке. Обработка ведётся набором фрез на на-
строенном станке способом автоматического получения за-
данных размеров. Заготовка 3 устанавливается плоскостя-
ми Г и Б на опорные пластины 2 и 4, размещённые на корпу-
се 1 приспособления. Ориентация приспособления на столе
станка относительно Т-образных пазов осуществляется по-
средством направляющих шпонок 5. При фрезеровании на-
бором фрез размеры 10+ ' и 18+ ' выдерживаются за счёт
размеров и настройки инструментов, а размеры 30.014 и
8.0>2 — за счёт установки в приспособление.
В первую очередь определяются и обосновываются пара-
метры для расчёта приспособления на точность при выпол-
нении размеров заготовки 30.0 14 и 8_0 2. Для обеспечения
при обработке параллельности базовых горизонтальных плос-
костей Л, Н и боковой плоскости И относительно базовых
поверхностей Б и Г заготовки в пределах заданных допусков
размеров в качестве расчётных параметров следует принять:
отклонение от параллельности рабочей (установочной) плос-
кости Б опорных пластин 2 относительно установочной по-
верхности А корпуса 1 приспособления; отклонение от па-
раллельности боковой установочной плоскости Г опорной
пластины 4 относительно боковой поверхности В направля-
ющих шпонок 5 приспособления. Эти параметры оказывают
определяющее влияние на отклонение от параллельности
плоскостей и выполнение размеров 30.014 и 8-о,2 заготовки-
После обоснования и выбора параметров, характеризующих
точность приспособления, эта величина рассчитывается по
формуле (8.1) в приведённой ниже последовательности.
Расчёт точности изготовления приспособления из усло-
вия обеспечения размера заготовки 30_014:
1. Определяется погрешность базирования, % = 0, так
как в данном случае нет отклонения фактически достигнуто-
го положения заготовки от требуемого.
2. Определяется погрешность закрепления. Для данного
случая (заготовка со шлифованной поверхностью Б с попе-
речными размерами 26x35 мм, зажим её в приспособлении
осуществляется винтовым устройством) е3 = 0,05 мм.
3. Определяется погрешность установки приспособления
на станке еу = 0, так как осуществляется надёжный контакт
установочной плоскости приспособления А с плоскостью сто-
ла станка.
4. Выявляется погрешность от перекоса (смещения) ин-
струмента еп — 0, так как в приспособлении отсутствуют на-
правляющие элементы.
5. Определяется погрешность от изнашивания установоч-
ных элементов. Изнашивание опорных пластин можно опре-
делить по формуле (8.7). В данных условиях (опорные пласти-
ны из стали У8А, заготовки устанавливаются сверху с некото-
рым последующим смещением по опорам 2 до соприкоснове-
ния с опорой 4, базовая поверхность заготовки шлифованная,
т.е. условия работы лёгкие) постоянную /32 можно принять по
таблице 8.2 равной 0,002; количество контактов (одна уста-
новка-снятие на каждую заготовку) N = 5000 в год.
После подстановки в формулу (8.7) выявленных значе-
ний определяется И = faN = 0,002-5000 = 10 мкм = 0,01 мм.
Погрешность от изнашивания установочных элементов еи
можно принять равной и, т.е. еи = И = 0,01 мм. При этом в
ТУ на эксплуатацию приспособления следует указать, что
проверку приспособления и ремонт (замену) установочных
элементов необходимо производить после года работы при-
способления (один раз в год).
6. Определяется экономическая точность обработки. Для
принятия условий (заготовка из стали, фрезерование отделоч-
ное, размер 30 мм, 5 t = 0,14 мм, 11-й квалитет) w = 0,014 мм.
7. Принимаются значения km, kml и km 2. Значение ftml
можно не учитывать, так как еб = 0; km = 1,2; hm 2 = 0,6;
уточняется допуск на обработку. В данном случае dx = 0,140 мм.
После подстановки значений величин в формулу (8.1) выяв-
ляется погрешность изготовления (точность в сборе) приспо-
собления епр для обеспечения размера заготовки 30.014 и от-
клонения от параллельности поверхностей Н и Л относитель-
но поверхности Б заготовки:

Таким образом, на длине 35 мм епр1 — 0,021 мм. Для
указания отклонения от параллельности поверхности Б ус-
тановочных элементов 2 (рис. 8.6, а) относительно устано-
вочной поверхности А корпуса 1 в ТУ на изготовление при-
способления целесообразно привести отклонение от парал-
лельности к округленному значению (например, 50 или
100 мм). Тогда отклонение от параллельности поверхностей Б
и А на длине 100 мм будет иметь значение 0,06/100 мм.
8. По полученному допуску параллельности поверхнос-
ти А относительно поверхности Б приспособления в сборе сле-
дует определить допуски составляющих звеньев размерной
цепи, т.е. корпуса 1 и опорных пластин 2 по размерам соот-
ветственно а и Ъ.
С учётом сложности деталей 1 и 2, которые являются зве-
ньями размерной цепи, и протяжённости их рабочих поверх-
ностей можно принять, что допуски на размер а детали 1
8г = 0,04/100 мм и на размер b детали 2 <5Х = 0,02/100 мм.
Подобные результаты получаются при решении угловой раз-
мерной цепи уй = Yi + У г-
Расчёт точности изготовления приспособления из усло-
вия обеспечения размера заготовки 8.02: