Мы поможем в написании ваших работ!
ЗНАЕТЕ ЛИ ВЫ?
|
Особенности мокрого способа производства.
Сырьевые материалы, поступающие с карьерной влажностью, подлежат первичной переработке: известняк – дроблению, а глина измельчается в валковых или молотковых-самоочищающихся дробилках и размучивается в мельницах типа «гидрофол» или болтушках. Дробленый известняк из бункеров через питатель поступает в шаровую мельницу, глина закачивается насосом-дозатором. Шаровая мельница измельчает материал, который содержит 38-42% воды. При помоле необходимо получить смесь с размером зерен менее 80 мкм (остаток на сите 008 – 8-10%).Полученная шихта закачивается в корректирующие банки, а из них поступает в шламбассейн где происходит усреднение состава смеси. Затем шихта направляется в печь обжига.
Достоинства мокрого способа производства:
- нет предварительной сушки сырьевых материалов;
- легче достигнуть однородности сырьевой смеси;
- в присутствии воды упрощается процесс помола;
- надёжнее осуществляется транспортировка смеси;
- улучшаются санитарно-гигиенические условия.
Недостатки мокрого способа производства:
- возрастает металлоёмкость печной установки;
- значительный расход воды обусловливает рост энерго- и теплозатрат на обжиг на 30-40%, то есть 5,8-6,7 МДж/кг клинкера расходуется тепла на удаление воды.
Технологическая схема. На рисунке 1 (стр. 15-16) изображена технологическая схема производства многокомпонентного цемента по мокрому способу.
Описание технологической схемы. Известняк добывается в карьере. Производятся буровзрывные работы, после чего разрыхленная порода грузится одноковшовым экскаватором и транспортируется на склад сырья завода при помощи автотранспорта. Куски породы должны быть размером не более 1200мм, более крупные глыбы дробят пневматическими перфораторами. Со склада известь грейферным краном (Табл. 4, п.1) направляется в бункера. Откуда материал подаётся пластинчатым питателем ПС-24-120 (Табл. 4, п.2), для обеспечения равномерной и непрерывной подачи, в щековую дробилку производительностью 500 т/ч (Табл. 4, п.3). После первой стадии дробления известняк ковшовым элеватором (Табл. 4, п.4) поднимается в бункер, из которого пластинчатым питателем подаётся на вторую стадию дробления в две молотковые дробилки СМ-19А (Табл. 4, п. 5) (размер выходящих зёрен 0-25мм). После измельчения материал ковшовым элеватором подаётся в бункера, из которых весоизмерителями ленточными ВЛ 1058(Табл. 4, п.6) направляется в две шаровые двухкамерные мельницы (Табл. 4, п.15) (размер измельчённых частиц < 80 мкн). В качестве мелющих тел используются металлические шары, общая масса которых превышает массу сырьевой смеси. Камеры мельницы футерованы кварцитными плитами [1].В мельницы подаётся вода для обеспечения влажности смеси 38-42%.
Глина добывается с помощью ковшовых экскаваторов типа прямая лопата или при помощи роторных экскаваторов, в зимний период частично могут проводится буровзрывные работы. Из карьера сырьё доставляется автотранспортом на склад. Грейферным краном (Табл. 4, п.1) он подаётся в бункер, откуда пластинчатым ПС-18-90 (Табл.4, п.7) подаётся на дробление в молотковую самоочищающуюся дробилку СМ-19А (Табл.4, п.5) (размер входящих кусков – 300мм, выходящих – 0-25мм).После дробления глина ковшовым элеватором подаётся в бункер, из которого пластинчатым питателем (Табл. 4, п.7) направляется в мельницу «Гидрофол» (табл.4,п.8), где глина измельчается и смешивается с водой, образуя вязко-текучую массу. Полученная смесь центробежным насосом (Табл.4, п.9) перекачивается в шаровые мельницы, где происходит совместный, помол известняка и глины в присутствии воды до образования водной суспензии-шлама с влажностью от 36 до 50%. Образовавшийся шлам центробежным насосом ВШН-150-1 (Табл.4, п.9) перекачивается в корректирующие банки, при помощи которых усредняют состав шлама и направляют затем в горизонтальные шламбассейны. Из шламбассейнов по шламопроводу шлам влажностью от 30 до 45% подаётся насосом-дозатором 6Ш8 (Табл.4, п.8) в четыре вращающиеся печи обжига с цепными завесами. В качестве топлива используется природный газ, который подается к форсунке по трубопроводу, оборудованному задвижкой для регулирования количества топлива, поступающего в печь. Необходимый для горения воздух просасывается через печь дымососом.Отходящие топливные газы подвергаются очистке в осадительной камере, циклонах (Табл.4,п.24) и электрофильтрах УГТ1-30-3 (Табл.4,п.25).Полученная пыль отправляется в шаровую мельницу, а очищенный воздух выбрасывается в атмосферу.Зона спекания вращающейся печи футеруется тальковым или магнезитовым кирпичом Из печи клинкер подаётся в колосниковый холодильник Волга-50с (Табл.4,п.13), а затем пластинчатым транспортёром горячего клинкера подаётся на склад клинкера силосного типа. Со склада клинкер весоизмерителем ВЛ-1058 (Табл.4,п.14) дозируется в две шаровые мельницы (Табл.4,п.15), после измельчённая смесь подвергается классификации в проходном сепараторе. Крупная фракция отправляется на домол в шаровую мельницу, а пыль осаждается в циклонах (Табл.4,п.24), из которых отправляется в силосы.
Гипсовый камень доставляется автотранспортом на склад сырья, откуда грейферным краном (Табл. 4, п.1) подаётся в бункер, из которого ленточным питателем с шириной ленты 400мм (Табл. 4, п.17) дозируется в конусную дробилку СМД-105 (Табл.4,п.19). Из дробилки элеватором (Табл. 4, п.18) измельчённый гипсовый камень подаётся в бункер, откуда ленточным питателем (Табл. 4, п.17) направляется в сушильный барабан V=28м3 (Табл.4,п.20). Оттуда высушенный материал элеватором (Табл. 4, п.18) подаётся в бункер попадает в шаровую мельнику (Табл. 4, п.21). Из мельницы гипсовый камень поднимается в бункер на промежуточное хранение. Откуда ленточным дозатором ЛДА-32с направляется в смеситель (Табл. 4, п.23) куда помамо гипсового камня дозируется помолотый клинкер. Так же можно в смеситель вводить различные добавки. При данной технологии производства можно выпускать ризличные марки цемента благодоря лёгкой вариации содержания компонентов. Смешение компонентов смеси происходит во вращающемся барабане, содержащим металлические стержни,каскадное движение которых и вращение воеруг своей оси обеспечивают необходимый эффект. Пыль осаждается в циклонах. Из которых отправляется в цементные силосы. Из силосов цемент отправляется на упаковку и отгрузку потребителям. Упаковывается цемент в специальных, изготовленных из многослойной натронно-целлюлозной бумаги, мешках, которые не промокают и выдерживают t=150˚С. Упаковка производится в специальных отделениях завода, где устанавливаются упаковочные машины.
При упаковочном отделении имеется склад бумажных мешков, располагаемый в непосредственной близости от упаковочной машины. Пустые мешки подаются в кипах к упаковочным машинам автопогрузчиками.
шламбассейн сырьевой смеси
| склад клинкера силосного типа
|
Составление материального баланса
| 4. Составление материального баланса
Режим работы предприятия. Режим работы предприятия (цеха) определяется в зависимости от характера производства, мощности и других факторов. Под режимом работы понимается число рабочих дней в году, количество смен в сутки и продолжительности смены в часах, предусмотренных действующим законодательством и характером производства.
Определение режима работы предприятия. Различают фонд времени работы предприятия, в соответствии, с которым рассчитывают выпуск продукции, потребность в сырье, топливе и др., и фонд времени работы технологического оборудования, который используется при расчете и выборе оборудования.
Материальный баланс предприятия. Материальный баланс производства (производственная программа) включает определение объема выпускаемой готовой продукции (по видам), потребностей цехов в каждом исходном сырьевом компоненте в расчете на сухое вещество, а также в состоянии естественной влажности в год, сутки и час.
Материальный баланс предприятия. Материальный баланс производства (производственная программа) включает определение объема выпускаемой готовой продукции (по видам), потребностей цехов в каждом исходном
сырьевом компоненте в расчете на сухое вещество, а также в состоянии естественной влажности в год, сутки и час.
Расчёт материального баланса предприятия. Расчет материального баланса ведется на основе указанной в задании производительности предприятия, химического и минералогического состава сырья, состава имеющихся в сырье примесей, естественной влажности компонентов.
Годовая производительность предприятия с учётом потерь определяется по формуле:

где: Пгод. – заданная готовая производительность, т;
Производительность предприятия по готовой продукции определяется по формулам 9, 10, 11:


Составление материального баланса
|
Потребность в сырьевых материалах с учётом влажности и потерь рассчитывается по следующим формулам:






Таблица 3. Материальный баланс предприятия.
Название
материала
| Потери
%
| W,
%
| Режим
работы,
сут/см.
| Потребность, т.
| год.
| сут.
| см.
| час.
| Вяжущее
|
| -
| 365/3
|
| 4328,6
| 1442,8
| 180,4
| Клинкер
| 0,5
| -
| 365/3
|
|
|
|
| Гипс. кам.
|
|
| 365/2
| 64266,3
| 214,4
| 107,2
| 13,4
| Сырьевая
смесь
| -
| -
| 365/3
|
|
|
|
| Известняк
| 2,5
|
| 365/3
| 1928724,9
| 5510,4
| 1836,8
| 229,6
| Глина
| 2,5
|
| 365/2
| 522832,7
| 1742,4
| 871,2
| 108,9
| Сырьевая смесь
| 2,5
| W
| 365/3
| 2451557,6
| 7003,2
| 2334,4
| 293,8
|
Выбор и обоснование технологического оборудования. Выбор оборудования осуществляется исходя из потребной производительности для каждой операции по справочникам и каталогам.
Количество каждого вида оборудования рассчитывается по формуле:
= 174/(50*0,85) = 3;
где: Пчас. – необходимая производительность цеха или передела, т/час;
Ппасп. – паспортная производительность отдельного вида оборудования, т/час.;
Кисп. – коэффициент использования оборудования, по нормативам обычно 0,85-0,95.
Составление материального баланса
| Выбранное оборудование занесено в таблицу 4, где приведена краткая характеристика, габаритные размеры и его количество.
Составление материального баланса
| Спецификация оборудования
№
п/п
| Наименование
| Тип
или
марка
| Краткая техническая характеристика
| Коли-чество, шт.
| Мощность эл/двигателя, кВт.
| Габаритные размеры
| 2.
| Пластинча-тый питатель
| ПС-24-120
| П=300м3/час
|
| -
| Шир =2400мм
Дл.=14511мм
Выс.=2077мм
| 3.
| Дробилка
щековая
| 1500*
2100*
| П=500т/ч
DЗ=1500мм
DВ=180мм
Кисп=0,9
|
|
| -
| 4.
| Элеватор
| -
| П>100т/ч
|
| -
| -
| 5.
| Молотко-вая дробилка
| ДМРЭ-17*145
| П=150-500т/ч
DЗ=600мм
DВ=20-180мм
|
|
| -
| 6.
| Автоматический ленточный
дозатор
| ЛДА-
|
|
|
|
| 7.
| Пластинча-тый питатель
| ПС-18-
| П=175м3/час
|
| -
| Шир.=2400мм
Дл.=11511мм
Выс.=2077мм
| 8.
| Гидрофол
| ММС 70-23
| П=46,8т/час
|
|
| Диам.=3м
Дл.=1,06м
| 9.
| Насос
| ВШН 150-1
| П=150 м3/час
Напор=50м
|
|
| -
| 10.
| Насос-дозатор
| 6ш8
| П=300 м3/час
Напор=54м
|
|
| -
| 11.
| 2-х камерная шаровая мельница
| -
| П=160т/ч ω=16,2об/мин
|
|
| Дл.1=6,7м
Дл.2=6,4
| 12.
| Печь вра-
щающаяся
| -
| П=1200т/сут
ω=1,11 об/мин
|
|
| Диам.=4,5м
Дл.=170м
| 13.
| Холодиль-ник
| Волга-
50с
| П=50т/ч
|
|
| Дл.=23,5м
Выс.=10,2м
Шир.=5,6м
|
|
|
|
|
|
|
| 14.
| Весоизме-ритель
| ВЛ-1058
| П=200т/ч
ω=50об/мин
|
| -
| Шир.=700мм
Диам.=320мм
| 15.
| шаровая мельница
| 4*13,5
| П=160т/ч ω=16,2об/мин
|
|
| Дл1=6,7м
Дл2=6,4м
| 16.
| Сепаратор
циклонный
| СМЦ-420
| П=160-180т/ч
|
| Ротора-180
Дымососа-250
| Диам.=5м
Выс.=10.8м
| 17.
| Ленточный питатель
| -
| П=5,4-46,5 м3/час
|
|
| Шир.=400мм
| 18.
| Элеватор
| -
| П=10-25т/ч
|
| -
| -
| 19.
| Конусная дробилка
| СМД-
| П=5-15т/час
DЗ=40мм
Dр=5-15мм
|
|
| Дл.=1,6м
Шир.=1,5м
Выс.=4,7м
| 20.
| Сушиль-ный барабан
|
| V=28
|
| -
| -
| 21.
| 2-х камерная шаровая мельница
| 2*10,5
| П=16т/ч
|
|
| Диам.=2,948м
Шир.= 10,520м
| 22.
| Автоматический ленточный
дозатор
| ЛДА-32с
| П=32т/ч
|
| -
| Шир.=990мм
| 23.
| Смеситель
| СК-58
| П=100-120 м3/час
|
|
| Дл.=3200мм
Диам.=1500мм
| 24.
| Циклон
| СДК, ЦН-33
| -
|
| -
| -
| 25.
| Эл.фильтр
| УГТ 1-30-3
| -
|
| -
| Дл.=14м
Шир4,5м
| Таблица 4. Специфика оборудования.
Расчёт основных производственных площадей
| 5. Расчёт основных производственных площадей.
Расчёт складов. Для производственной деятельности завода сооружают общезаводские и цеховые склады. Они могут быть открытые, закрытые, штабельные, силосные, бункерные. Выбор типа склада зависит от климатических условий, вида материала, сроков хранения, организации перевозок и погрузо-разгрузочных работ.
Расчёт складов сырья Площадь складов рассчитывается по формуле 19:

где: - площадь склада, м2;
- суточная потребность в материалах, т/сут;
- норма хранения, сут;
- насыпная плотность материала, т/м3;
- высота укладки штабеля, м.
Склад известняка

Склад маршалита

Склад глины

Склад гипсового камня

Склад клинкера (силосного типа)

Склад высушенного гипсового камня (силосного типа)

Расчёт складов готовой продукции. Емкость складов готовой продукции может зависеть от необходимости вылеживания вяжущего до отправки его потребителю. Силосные склады - железобетонные цилиндрические емкости с одним или двумя разгрузочными отверстиями.
Объем силосного склада в м3, для каждого компонента составляет:

где: - производительность завода по готовой продукций, т/год;
- число суток нормированного запаса;
- насыпная плотность материала, т/м3;
- коэффициент заполнения силоса.
Полезный объём силоса диаметром 12м и высотой 33м составляет 3000м3.
Следовательно количество силосов (nс) будет равно:
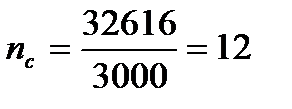
|