Мы поможем в написании ваших работ!
ЗНАЕТЕ ЛИ ВЫ?
|
Безопасность эксплуатации баллонов для сжатых, сжиженных и растворенных газов.
Баллоны предназначены для хранения и транспортировки относительно небольшого количества определенного вида газа: сжатого (воздух, кислород, азот, водород и др.), сжиженного (газообразные углеводороды, аммиак, хлор) или растворенного (ацетилен). Верхняя часть баллона имеет горловину, в которую на резьбе устанавливают запорный вентиль с боковым выпускным штуцером. Если баллон находится в нерабочем состоянии, то на штуцер навинчивают заглушку. Для защиты вентиля от повреждения на баллон устанавливают металлический или пластмассовый колпак. Введена строгая маркировка баллонов. Боковые штуцера вентилей для баллонов с горючими газами выполняют с левой резьбой, а для баллонов с кислородом и другими негорючими газами - с правой, чтобы предотвратить применение не по назначению и образование взрывоопасных смесей. Баллоны следует предохранять от ударов, а также высоких и низких температур. Предельное рабочее давление в баллоне при температуре 20"С для сжатых и растворенных газов составляет 15МПа (150кгс/см2), а для сжиженных - 3МПа (30кгс/см2). Если температура баллона значительно превышает указанное значение, давление газа может превзойти допустимое. На верхней, сферической, части каждого баллона нанесены клеймением следующие данные: • товарный знак завода-изготовителя; • номер баллона; • фактическая масса порожнего баллона (для баллонов вместимостью до 12л включительно - с точностью 0,1кг, от 12 до 55л включительно - с точностью 0,2кг, свыше 55л - в соответствии с государственным стандартом или техническими условиями на их изготовление); • дата (месяц и год) изготовления и год следующего освидетельствования; • рабочее давление; • пробное гидравлическое давление; • вместимость баллона (для баллонов вместимостью до 12л включительно - номинальная, от 12 до 55л включительно - фактическая, с точностью 0,3л, свыше 55л - в соответствии с государственным стандартом или техническими условиями на их изготовление); • клеймо ОТК завода-изготовителя круглой формы диаметром 10мм (за исключением стандартных баллонов вместимостью свыше 55л); номер стандарта для баллонов вместимостью свыше 55л. Высота знаков на баллонах вместимостью до 55л включительно должна составлять не менее 6мм, а свыше 55л - не менее 8мм. Масса баллонов, за исключением баллонов для ацетилена, указывается с учетом массы нанесенной краски кольца для колпака и башмака, если таковые предусмотрены конструкцией, но без массы вентиля и колпака. Место на баллонах, где выбиты паспортные данные, должно быть покрыто бесцветным лаком и обведено отличительной краской в виде рамки. Баллоны для растворенного ацетилена заполнены пористой массой и растворителем согласно государственному стандарту. Ответственность за качество и количество пористой массы несет завод, наполняющий ею баллоны. Ответственность за качество и количество растворителя несет завод, заполняющий им баллоны. После заполнения баллона пористой массой и растворителем на его горловине выбивается масса тары (масса баллона без колпака, но с пористой массой и растворителем, башмаком, кольцом и вентилем). В связи с тем что ацетилен при давлении 200кПа становится взрывчатым, для его безопасного хранения и транспортировки при более высоком давлении внутреннюю полость баллона (2/3 объема) заполняют пористой массой - березовым активированным углем, пропитанным ацетоном, хорошо растворяющим ацетилен. Для предупреждения вытекания растворителя (вместе с ацетиленом) наполненные баллоны должны постоянно находиться в вертикальном положении. Окраска и нанесение надписей на вновь изготовленном баллоне производятся заводами-изготовителями, а в дальнейшем - заводами-наполнителями, наполнительными или испытательными станциями. Надписи на баллонах наносят по окружности, не менее чем на ее 1/3 часть, а полосы - по всей окружности, причем высота букв на баллонах вместимостью более 12л должна составлять 60мм, а ширина полосы - 25мм. Размеры надписей и полос на баллонах вместимостью до 12л зависят от площади боковой поверхности баллонов. Баллоны, находящиеся в эксплуатации, подвергаются освидетельствованию не реже чем один раз в 5 лет. Баллоны, предназначенные для наполнения газами, которые вызывают коррозию, а также баллоны для сжатых и сжиженных газов, применяемых в качестве топлива для автомобилей и других транспортных средств, подлежат освидетельствованию не реже чем один раз в 2 года. Периодическое освидетельствование баллонов проводится работниками заводов-наполнителей, наполнительных или испытательных станций. В случае получения удовлетворительных результатов на каждый баллон наносят клеймо (круглой формы, диаметром 12мм) завода-наполнителя, на котором выполнено освидетельствование, дату проведенного и следующего освидетельствования (в одной строке с клеймом завода-изготовителя). Результаты освидетельствования баллонов заносят в журнал испытаний. Разрешение на освидетельствование баллонов выдает организациям местный орган Госгортехнадзора России. Освидетельствование ацетиленовых баллонов должно проводиться на заводе, осуществляющем их наполнение ацетиленом, не реже чем один раз в 5 лет. Оно включает в себя осмотр наружной поверхности, проверку пористой массы и пневматическое испытание.
69. Технологические трубопроводы. Категорирование, предупредительная окраска. Прокладка трубопроводов.
Технологические трубопроводы классифицируют по роду транспортируемого вещества, материалу труб, рабочим параметрам, степени агрессивности среды, месту расположения, категориям и группам. По роду транспортируемого вещества технологические трубопроводы можно разделить на нефтепроводы, газопроводы, паропроводы, водопроводы, мазутопроводы, маслопроводы, бензопроводы, кислотопроводы, щелочепроводы, а также специального назначения (трубопроводы густого и жидкого смазочного материала, трубопроводы с обогревом, вакуум-проводы) и др. По материалу, из которого изготовлены трубы, различают трубопроводы стальные (из углеродистой, легированной и высоколегированной стали), из цветных металлов и их сплавов (медные, латунные, титановые, свинцовые, алюминиевые), чугунные, неметаллические (полиэтиленовые, винипластовые, фторопластовые, стеклянные), футерованные (резиной, полиэтиленом, фторопластом), эмалированные, биметаллические и др. По условному давлению транспортируемого вещества трубопроводы разделяют на вакуумные, работающие при давлении ниже 0,1 МПа, низкого давления, работающие при давлении до 10 М Па, высокого давления (более 10 МПа) и безнапорные, работающие без избыточного давления. По температуре транспортируемого вещества трубопроводы подразделяют на холодные (температура ниже 0°С), нормальные (1...45 °С) и горячие (от 46 °С и выше). По степени агрессивности транспортируемого вещества различают трубопроводы для неагрессивных, малоагрессивных, среднеагрессивных и агрессивных сред. Стойкость металла в коррозионных средах оценивают скоростью проникновения коррозии — глубиной коррозионного разрушения металла в единицу времени, мм/год. К неагрессивной и малоагрессивной средам относят вещества, вызывающие коррозию стенки трубы, скорость которой менее 0,1 мм/год, среднеагрессивной — в пределах 0,1... 0,5 мм/год и агрессивной — более 0,5 мм/год. Для трубопроводов, транспортирующих неагрессивные и малоагрессивные вещества, обычно применяют трубы из углеродистой стали; транспортирующих среднеагрессивных вещества, — трубы из углеродистой стали с повышенной толщиной стенки (с учетом прибавки на коррозию), из легированной стали, неметаллических материалов, футерованные; транспортирующих высокоагрессивные вещества — только из высоколегированных сталей, биметаллические, из цветных металлов, неметаллические и футерованные. По месторасположению трубопроводы бывают внутрицеховые, соединяющие отдельные аппараты и машины в пределах одной технологической установки или цеха и размещаемые внутри здания или на открытой площадке, и межцеховые, соединяющие отдельные технологические установки, аппараты, емкости, находящиеся в разных цехах. Внутрицеховые трубопроводы по конструктивным особенностям могут быть обвязочные (около 70 % общего объема внутрицеховых трубопроводов) и распределительные (около 30 %). Внутрицеховые трубопроводы имеют сложную конфигурацию с большим числом деталей, арматуры и сварных соединений. На каждые 100 м длины таких трубопроводов приходится выполнять до 120 сварных стыков. Масса деталей, включая арматуру, в таких трубопроводах достигает 41 % общей массы трубопроводов в целом. Межцеховые трубопроводы характеризуются довольно длинными прямыми участками (длиной до нескольких сот метров) со сравнительно небольшим числом деталей, арматуры и сварных соединений. Масса деталей в межцеховых трубопроводах (включая арматуру) составляет около 3...4%, а масса П-образных компенсаторов — около 7 %. Стальные трубопроводы разделяют на категории в зависимости от рабочих параметров (температуры и давления) транспортируемого по трубопроводу вещества и группы в зависимости от класса опасности вредных веществ и показателей пожарной опасности веществ.
Наружную поверхность трубопроводов окрашивают для защиты от коррозии. Окраска бывает различной в зависимости от места прокладки, наличия тепловой изоляции и температуры транспортируемого продукта.
Защитной окраске подлежат все надземные трубопроводы из углеродистой стали с тепловой изоляцией, покрытой кожухами, или без нее, прокладываемые как на открытом воздухе, так и в помещениях. Исключение составляют изолированные трубопроводы, покрытые асбестоцементной штукатуркой, асбестоцементным
формованными изделиями, а также имеющие кожух из коррозионно-стойких металлов /алюминия, оцинкованного железа и др./. Трубопроводы окрашивают масляной краской, эмалями и лаками
/перхлорвиниловыми, эпоксидными/. Применяют также способ металлизации алюминием, цинком и другими защитными средствами в зависимости от условий, в которых работает трубопровод. Трубопроводы, прокладываемые в непроходных каналах, неизолированные и имеющие тепловую изоляцию, при рабочей
температуре поверхности трубы или изоляции до 25°С окрашивают битумным лаком. При более высоких температурах поверхностей такие трубопроводы не окрашивают.
Помимо основной защитной окраски, все технологические трубопроводы должны иметь опознавательную цветную окраску. Опознавательную окраску /ГОСТ 14202-69/, предупреждающие знаки и маркировочные щитки трубопроводов применяют для того, чтобы определить содержимое трубопровода
70. Технологические трубопроводы. Компенсация тепловых деформаций. Теплоизоляция.
Тепловую изоляцию технологических трубопроводов применяют для защиты горячих и холодных поверхностей от потерь теплоты и холода, для сохранения температуры транспортируемого вещества, предотвращения его застывания, конденсации, для защиты от ожогов, если температура поверхности трубопроводов выше 60°С, в местах возможного нахождения эксплуатационного персонала.
Тепловую изоляцию применяют для прокладываемых в помещениях и туннелях трубопроводов, если температура транспортируемого вещества 45°С и выше. Для тепловой изоляции трубопроводов широко используют типовые детали, полносборные и комплектные теплоизоляционные конструкции заводского
изготовления, допускающие выполнение монтажа индустриальными методами. Детали и конструкции изготовляют из различных теплоизоляционных материалов /минеральной ваты, диатомита, перлита, асбеста, стеклоцемента, стеклопластика, ячеистых материалов/.
Для изоляции трубопроводов выпускают большое количество комплектных и полносборных изделий /рис. 4.7/: цилиндры, полуцилиндры /скорлупы/, плиты из различных теплоизоляционных материалов /минеральной ваты, диатомита, перлита/. Для покрытия изоляций применяют оболочки из листового металла,
асбестоцемента, стеклотары, стеклоцемента и стеклопластика.
71. технологические трубопроводы. Техническое освидетельствование трубопроводов
К технологическим трубопроводам (ПБ 03-108-96) относятся трубопроводы в пределах промышленных предприятий, по которым транспортируется сырье, полуфабрикаты и готовые продукты, пар, вода, топливо, реагенты и другие вещества, обеспечивающие ведение технологического процесса и эксплуатацию оборудования, а также межзаводские трубопроводы, находящиеся на балансе предприятия. Они непосредственно предназначенны для транспортирования газообразных, парообразных и жидких сред в диапазоне от остаточного давления (вакуум) 0,001 МПа (0,01 кгс/кв. см) до условного давления 320 МПа (3200 кгс/кв. см) и рабочих температур от минус 196 до плюс 700 град. C на химических, нефтехимических, нефтеперерабатывающих, газоперерабатывающих, химико- фармацевтических, целлюлозно - бумажных, микробиологических, коксохимических, нефте- и газодобывающих предприятиях.
В зависимости от рабочего давления технологические трубопроводы, подразделяются на технологические трубопроводы низкого давления с условным давлением до 10 МПа (100 кгс/кв. см) включительно и технологические трубопроводы высокого давления с условным давлением свыше 10 МПа (100 кгс/кв. см) до 320 МПа (3200 кгс/кв. см).
УСЛОВНЫЕ ОБОЗНАЧЕНИЯ ТРУБОПРОВОДОВ ГОСТ 21.206-93 (System of building design document. Pipelines. Symbols for presentation).
Приведенные ниже условные обозначения трубопроводов и их элементов применяются при создании чертежей и схем технологических, тепломеханических, санитарно-технических и других систем, сетей, коммуникаций при проектировании предприятий, зданий и сооружений различного назначения.
Условное обозначение трубопровода состоит из графического условного обозначения или упрощенного изображения трубопровода и буквенно-цифрового или цифрового обозначения транспортируемой среды, характеризующего ее вид, назначение и параметры.
Буквой или первой цифрой обозначают вид транспортируемой среды, последующими цифрами - назначение и/или параметры транспортируемой среды.
Графические условные обозначения и упрощенные изображения трубопроводов и их элементов приведены в таблице 1.
Видимые участки проектируемых трубопроводов изображают сплошной толстой основной линией, невидимые (например, в перекрытых каналах) - штриховой линией той же толщины.
Существующие трубопроводы изображают соответственно сплошной или штриховой тонкой линией.
Таблица 1
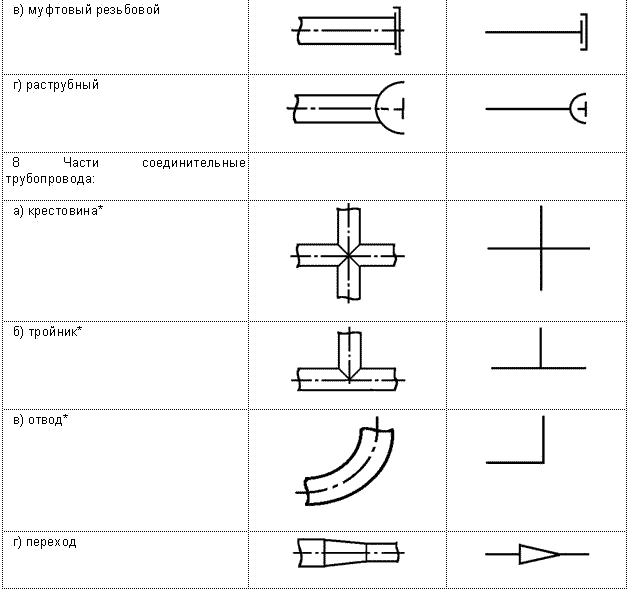
* Изображают в соответствии с их действительной конфигурацией
При изображении трубопровода на чертеже (схеме) буквенно-цифровые или цифровые обозначения указывают на полках линий-выносок или над линией трубопровода, а в необходимых случаях - в разрывах линий трубопроводов (рисунок 1).
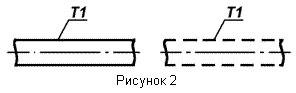
При упрощенных графических изображениях трубопровода (две линии) буквенно-цифровые или цифровые обозначения указывают на полках линий-выносок (рисунок 2) или непосредственно над графическим изображением трубопровода (рисунок 3).
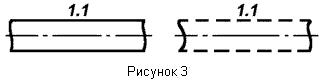
Количество проставляемых буквенно-цифровых или цифровых обозначений на линиях трубопроводов должно быть минимальным, но обеспечивающим понимание чертежа (схемы).
72 Арматура химических установок.
Арматурой называются устройства, которые устанавливаются на трубопроводах и емкостях и обеспечивают управление потоком (движением) рабочих сред. По области применения арматуру подразделяют на пароводяную, энергетическую, нефтяную, судовую и т. п. По материалу корпусных деталей арматура делится на чугунную, стальную, из коррозионностойкой стали, цветных металлов и сплавов, а также из неметаллических материалов. Выделяют арматуру с защитным покрытием пластмассой или эмалью и арматуру с эластичным деформируемым затвором. Различают условное, рабочее и пробное давление. Условные давления ру образуют, согласно ГОСТ 8032—56, следующий ряд (в кгс/см2): 1; 2,5; 4; 6; 10; 16; 25; 40; 64; (80); 100; (125); 160; 200;-250; 320; 400; 500; 640; 800 и 1000. Арматуру и соединительные части на условные давления, заключенные в скобки, не рекомендуется применять: они используются только для замены вышедшей из строя арматуры, установленной на эксплуатирующихся линиях. По условным давлениям арматуру можно разделить на шесть групп: 1) для высокого и сверхвысокого вакуума — для абсолютного давления ниже 1 • 10~3 мм рт. ст.; 2) для низкого и среднего вакуума —для абсолютного давления от 1 • 10~3 мм рт. ст. до 1 кгс/см2; 3) для малых давлений —до 16 кгс/см2; 4) для средних давлений — от 25 до 100 кгс/см2; 5) для высоких давлений — от 160 до 800 кгс/см2; 6) для сверхвысоких давлений — от 1000 кгс/см2 и выше*. Условные (ру) рабочие (рр) и пробные (/?пр) давления для арматуры из стали, чугуна, бронзы и латуни регламентированы ГОСТ 356—68. Рабочие давления равны условным для арматуры из углеродистой стали при температуре среды t = 0 -т- 200 °С, для арматуры из чугуна, бронзы или латуни — при ^ = 0-М20°С. При повышении температуры допускаемое рабочее давление снижается в зависимости от материала корпусных деталей арматуры. ГОСТ 356—68 предусматривает 14 температурных ступеней, в пределах которых рабочее давление по мере повышения температуры * 1 мм рт. ст. = 133,3 Па, 1 кгс/см2 = 9,81 • 104 Па «0,1 МПа.
|