Инструментом, режущие кромки которого представляют собой профиль сопряженной рейки или профиль зуоа сопряженного колеса, и во время обработки инструменте заготовкой образует сопряженную (правильно зацепляющуюся) зубчатую пару.
Глава ПРОЦЕСС ЗУБОНАРЕЗАНИЯ XX ОСНОВНЫЕ ПОЛОЖЕНИЯ
Образование профиля зубьев зубчатого колеса путем удаления
материала впадины режущими инструментами 1 производится фрезе-
рованием, строганием, долблением, протягиванием, шевингованием
и шлифованием. Фрезерование осуществляется профильными фрезами,
дисковыми или пальцевыми; цилиндрическими или коническими
червячными фрезами; торцовыми зуборезными головками с резцами
для черновой и чистовой обработки конических зубчатых колес.
Строгание осуществляется резцами с прямолинейной режущей
кромкой на специальных зубострогальных станках, предназначенных
для обработки конических колес.
Долбление производится на зубодолбежных станках многолезвий-
ным режущим инструментом — долбяком.
Протягивание производится с цомощью специального инструмента
и как способ образования зубьев колес применяется редко.
Шевингование — процесс чистовой обработки зубчатых колес ин-
струментом в виде зубчатого колеса с зубьями, снабженными по про-
филю мелкими режущими зубчиками.
Шлифование используется как процесс чистовой обработки зуба,
а в отдельных случаях, при мелких модулях, — для вышлифовывания
зуба в целой заготовке.
Нарезание зубьев осуществляется двумя методами: 1) методом ко-
пирования, когда форма режущей кромки фасонного инструмента
соответствует форме впадины зуба колеса (так работают дисковые,
пальцевые модульные фрезы, зубодолбежные головки); 2) методом
обката, когда поверхность зуба получается в результате обработки
1 В книге не рассматриваются другие методы получения профиля зубчатых колес
(накатывание, отливка и др.).
324

По методу обката работают самые различные зуборезные инстру-
менты: червячные фрезы, долбяки, гребенки, шеверы и др.
Д и с к о в а я модульная фреза (рис. 281, а) представляет собой
фасонную фрезу, обычно с затылованнымн зубьями, профиль зуба
которой повторяет профиль впадины нарезаемого колеса.
Применение дисковых фрез ограничено, так как точность зубчатых
колес при нарезании дисковыми модульными фрезами получается не-
высокой (9—10-я степень точности по ГОСТу 1643—56).
325
Пальцевая зуборезная фреза (рис. 281, б) применяется в тя-
желом машиностроении для фрезерования профилей косозубых
и прямозубых колес крупного модуля, в том числе и шевронных
колес.
Профиль инструмента, работающего по методу обката, не зависит
от числа зубьев нарезаемого колеса, поэтому одной и той же червячной
фрезой или гребенкой можно нарезать зубчатые колеса с любым чис-
лом зубьев 1.
Точность колеса, получающаяся при обкатке, значительно выше
точности зубчатых колес, получаемых по методу копирования, что
объясняется прежде всего непрерывностью процесса обката. При этом
процессе (за редким исключением) не требуется производить отдельного
деления, что сокращает холостые движения, и поэтому он производи-
тельнее метода копирования 2.
Из инструментов для обработки цилиндрических зубчатых колес,
работающих по методу обката, наибольшее применение получили
червячные зуборезные фрезы, зуборезные долбяки и шеверы.
Червячная фреза, кроме обработки цилиндрических колес
с прямыми и косыми зубьями, применяется также для обработки чер-
вячных колес и конических колес с криволинейными зубьями (в послед-
нем случае специальные конические фрезы).
На рис. 281, в показана схема процесса обработки червячной фрезой
цилиндрического колеса. В процессе обработки фреза вращается (глав-
ное движение) и перемещается вдоль оси заготовки (движение подачи).
Заготовка, будучи кинематически связанная с фрезой, также должна
вращаться, обеспечивая тем самым обкат и нарезание зубьев по всей
окружности заготовки.
Червячная фреза при ее установке на станке поворачивается на
угол со наклона продольной канавки фрезы при обработке колес с пря-
мыми зубьями, на угол ±р при обработке косозубых цилиндриче-
ских колес; знаки плюс и минус определяют направление наклона
зубьев колеса.
Червячные фрезы для цилиндрических колес изготовляют, как
правило, с затылованными (реже с острозаточенными) зубьями и на-
садными по конструкции.
Зуборезный долбяк (рис. 281, г) — режущий инстру-
мент, выполненный в виде зубчатого колеса и снабженный режущими
кромками. Долбяки применяют для предварительного и чистового
(окончательного) нарезания зубчатых колес (чаще для последнего).
Обработка зубчатого колеса долбяком производится на зубодол-
бежном станке. Долбяк и заготовка кинематически обкатываются по
начальным окружностям без скольжения.
1 В отдельных случаях при методе обката одним инструментом нарезается
группа колес одного модуля, несколько ограниченная (например, при шевинговании).
2 При контурном зубодолблении метод копирования более производителен,
чем все основные методы обката.
Кроме движения обката, долбяк имеет возвратно-поступательное
движение вдоль оси заготовки — главное движение резания.
Обычно срезание стружки происходит при движении долбяка
вниз, при обратном ходе (чтобы избежать во время этого хода трения
зубьев долбяка о поверхность зубьев нарезаемого колеса) заготовка
в конце каждого рабочего хода долбяка должна отходить от него на
небольшую величину. В начале рабочего хода она вновь подходит
к долбяку.
Кроме возвратно-поступательного и вращательного движения,
долбяк должен быть подведен в радиальном направлении на глубину
впадины зуба нарезаемого колеса (в случае нарезания с одного про-
хода). При нарезании зубчатых колес в два или три прохода величина
радиального перемещения долбяка, естественно, будет составлять часть
от общей глубины впадины зуба нарезаемого колеса.
Долбяками можно обрабатывать не только прямозубые колеса
внешнего или внутреннего зацепления, но и колеса с винтовыми
зубьями внешнего и внутреннего зацепления, колеса-блоки и колеса
с уступами. При применении долбяков можно обеспечить 6—7-ю сте-
пени точности колес по ГОСТу 1643—56.
Долбяк для колеса с винтовыми (косыми) зубьями представляет
собой также зубчатое колесо, но только с винтовым направлением
зубьев. На схеме работы долбяка для колеса с винтовыми зубьями
(рис. 281, д) видно, что долбяк, закрепленный на штосселе зубодол-
бежного станка, движется возвратно-поступательно и, кроме того,
для обеспечения винтового движения на станке устанавливается спе-
циальный копир, который придает штосселю вращательное движение
дополнительно к поступательному движению вдоль оси. Таким обра-
зом, при помощи копира и обеспечивается винтовое главное движение
долбяка.
Та&лица 26
Значения средних и задних углов режущей части
зуборезных инструментов в град
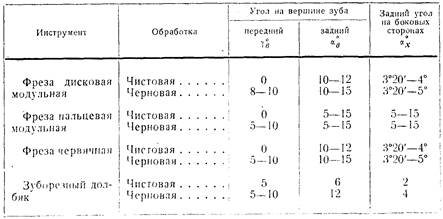
326
У зуборезных инструментов геометрические параметры — перед-
ние и задние углы — принимаются при затылованных зубьях не
столько из условий обеспечения оптимальных условий производитель-
ного резания, сколько из условий сохранения формы профиля при
переточках.
В табл. 26 приводятся величины передних и задних углов для
зуборезных инструментов с затылованными зубьями. Затылование
профиля при достаточных задних углах у вершин зубьев не позволяет
обеспечить достаточные задние углы на боковых сторонах профиля.
Поэтому конструкторы стремятся в целях улучшения геометрии ин-
струмента применять, где это возможно, острозаточенные зубья.
Передние углы зуборезного инструмента, особенно чистового,
также малы или равны нулю (в целях упрощения профилирования
инструмента).
§ 2. ЭЛЕМЕНТЫ РЕЖИМА РЕЗАНИЯ ПРИ ЗУБОНАРЕЗАНИИ
Обработка цилиндрических колес червячной фрезой. Скорость
резания v определяется, как при обычном фрезеровании.
Подача задается перемещением фрезы в миллиметрах за один
оборот заготовки s0 или подачей за один оборот фрезы s^, которая
может быть определена по формуле
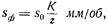
где К — число заходов червячной фрезы;
. z — число зубьев нарезаемого- колеса.
В нормативах по режимам резания [117] рекомендуемые подгчи
даны в ммюб. Средние величины таких подач при предварительном
нарезании прямозубых колес могут быть подсчитаны по формуле
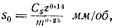
где Cs — коэффициент, зависящий от обрабатываемого металла; для
углеродистой стали с в = 70 ¸ 85 кГ/Мм2 Сs = 2,65;
для хромистой и хромоникелевой стали с в = 75 ¸
¸ 90 кГ/мм- Cs = 2,0 и для чугуна с НВ 160-180 Сs = 3,7;
z — число зубьев нарезаемого колеса;
т — модуль нарезаемого колеса в мм.
При фрезеровании колес с винтовым зубом подача миже! быть
подсчитана по формуле

где — угол наклона зуба колеса.
При чистовом нарезании зубчатых колес червячной фрезой подача
s0 принимается в пределах 0,3—2 мм/об в зависимости от модуля
колеса '.
Глубина резания t при зубофрезеровании равна глубине впадины
зубьев нарезаемого колеса, если колесо нарезается в один проход.
Когда число проходов увеличивается, то глубина резания за каждый
проход соответственно изменяется. Например, при двух проходах
общая глубина резания t = 2,2 т разбивается на tnp = 1,4 т при
черновой обработке и ton — 0,8 т при чистовой.
Мощность, потребная на нарезание зубьев, подсчитывается по фор-
муле 
где CN — коэффициент, зависящий от обрабатываемого материала;
s0 — подача на один оборот заготовки в мм;
т — модуль нарезаемого колеса в мм;
De — наружный диаметр фрезы в мм;
z — число зубьев нарезаемого колеса;
v — скорость резания в м/мин.
Подсчитанные по указанной зависимости значения мощности при-
водятся в соответствующих картах нормативов режимов резания
117].
Машинное время при обработке цилиндрических колес червячной
фрезой может быть подсчитано по формуле

здесь п — число оборотов фрезы в минуту;
s0 — подача в мм за один оборот заготовки;
z — число зубьев нарезаемого колеса;
К — число заходов фрезы;
i — число проходов;
L — путь фрезы в направлении подачи в мм.' который при
осевом врезании определяется так:
L = qb + y + ,
где b — ширина венца нарезаемого колеса в мм;
q — количество колес, одновременно обрабатываемых на станке;
у — величина врезания в мм:
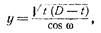
где t — глубина резания в мм;
D — диаметр фрезы в мм;
w — угол установки фрезы на станке (при нарезании прямозубого
колеса).
Подачу s 0 следует выбирать по нормативам,
328
329
При нарезании косозубого колеса в формулу вместо cos со подста-
вляется cos ( ± ), где — угол наклона зубьев.
В целях повышения производительности зубофрезерования (до
15%) можно применять радиальное врезание. При радиальном вре-
зании процесс резания также протекает с более равномерной загрузкой
станка и инструмента, что способствует, но данным ЭНИМСа, мень-
шему износу отдельных частей станка и повышению стойкости червяч-
ной фрезы. Величина поперечной подачи s во время радиального вре-
зания применяется от 0,5 до 0,75 s.
Обработка зубодолблением. Скорость резани я при зу-
бодолблении линейная. Скорость поступательного движения при ра-
бочем ходе долбяка может быть подсчитана по формуле
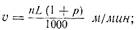
здесь р — отношение vp — скорости рабочего хода долбяка к
vx — скорости холостого хода;
п — число двойных ходов долбяка в минуту;
L — длина хода долбяка: определяется по формуле
L = y + b + A,
где b — ширина венца нарезаемого зуба в мм (см. рис. 283):
у — величина врезания (3—5 мм):
D — перебег (2—3 мм).
Подача s при зубодолблении представляет собой длину дуги,
измеренную по начальной окружности нарезаемого колеса (долбяка),
отнесенную к одному двойному ходу долбяка и называемую круговой
подачей (или подачей обката); обозначается s в ммдв.ход.
Величину технологически допустимой подачи выбирают в зави-
симости от заданного качества поверхности и требуемой точности об-
рабатываемого материала, модуля нарезаемого колеса и мощности
станка.
Глубина резан и я t при работе в один проход равна
глубине впадины зуба колеса. Когда зубодолбление производится
в несколько проходов, глубина резания соответственно распределяется
между проходами (и это следует учитывать).
Мощность затрачиваемая при зубодолблении, определяется по
формуле [140]

Машинное время при зубодолблении за один проход может быть
определено по формуле
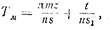
330
где m — модуль нарезаемого колеса в мм;
z — число зубьев нарезаемого колеса;
п — число двойных ходов долбяка в минуту;
s — круговая подача в мм/дв.ход;
t — глубина резания в мм;
s, — радиальная подача при врезании на полную глубину реза-
ния в мм за один двойной ход долбяка, обычно принимается
равной (0,1 -ь 0,30)s в мм/дв.ход.
§ з. износ, стойкость и скорость резания
ЗУБОРЕЗНОГО ИНСТРУМЕНТА
Зуборезный инструмент работает в зоне сравнительно тонких
стружек, поэтому зуб изнашивается в основном по задней поверхности
и неравномерно, а так как при работе должен быть сохранен профиль,
то и средние значения допустимого износа по задней поверхности
обычно небольшие. На рис. 282 показана схема износа зубьев зубо-
резных инструментов. Износ неравномерный; наибольший износ у угол-
ков зуба, который и принимается за лимитирующий износ (табл. 27).

Рис. 282. Износ по задней поверхности зуба:
а — дископой модульной фрезы; б — червячной фрезы; в — долбяка
Период стойкости червячных фрез из быстрорежущей стали при-
нимается по нормативам от 55 до 360 мин; инструмент сложный и
стоимость переточки высокая.
Допустимая скорость резания при заданных величинах подачи и
период стойкости определяются или по справочным таблицам режимов
резания, или по формулам.
При обработке зубчатых колес червячными фрезами и долбяками
скорость резания принимается по формуле

где, например, при черновом нарезании зубчатых колес т — 1,54-6 мм
из стали 45 (НВ 207); С v =312; у v =0,5; х v =0; т1 =0,33.
331
Порядок выбора элементов резания следующий. Вначале опре-
деляют технологическую подачу (подсчитываетcя по формулам или
берется из таблиц справочников)1. Затем подсчитывают скорость ре-
зания, допускаемую режущими свойствами инструмента.

По принятой скорости резания в случае работы червячной фрезой
определяют число оборотов фрезы, а в случае применения зуборезного
долбяка подсчитывают число двойных ходов долбяка в минуту. Затем
корректируют по кинематическим данным паспорта станков число
оборотов или число двойных ходов и подсчитывают действительную
скорость резания.
Для проверки подсчитывают мощность, необходимую для резания,
и соответствующую мощность электродвигателя станка:

КОНСТРУИРОВАНИЕ ЗУБОРЕЗНОГО ИНСТРУМЕНТА, РАБОТАЮЩЕГО МЕТОДОМ КОПИРОВАНИЯ ДИСКОВЫЕ МОДУЛЬНЫЕ ФРЕЗЫ
Пальцевые и дисковые модульные фрезы — частные случаи фа-
сонных фрез с затылованными зубьями и основные элементы их опре-
деляются по зависимостям для фасонных фрез с затылованными
зубьями, приведенным в гл. XIX..
См. нормативы режимов резания [117].
Высота затылуемого профиля фрезы h (см. рис. 276) применительно
к модульным фрезам определяется размерами впадины зубьев колеса.
Профиль зуба дисковой модульной фрезы для фрезерования цилин-
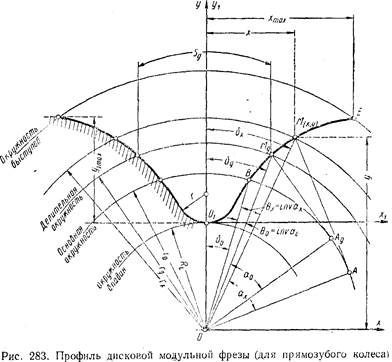
дрических колес с прямым зубом 1 в точности соответствует профилю
впадины колеса (рис. 283), 'состоящего из рабочего участка — зуба
B E (отрезка эвольвенты) и нерабочего участка — зуба O 1 B, ограни-
ченного переходной кривой.
Для расчета координат точек звольвентного участка зуба поместим начало
координат в центр зубчатого колеса. Ось O Y совместим с осью симметрии профиля
впадины. Координаты х и у любой точки М профиля фрезы определяются по фор-
мулам г
х = rx sin х; у = rx cos х,
но угол бх, как видно из рис. 283, определится как сумма двух углов:
d x = dо + x -
1 Профилирование дисковых модульных фрез для колес с косым зубом в главе
не рассматривается; интересующимся рекомендуется книга "Справочник инструмен-
тальщика-конструктора". М., Машгиз, 1958.
2 Подробнее см. литературу [32].
332
333
В свою очередь, 0Л. определится из условия образования эвольвенты как раз-
вертки круга, при,котором длина отрезка МА должна быть равна длине соответ-
ствующей дуги ВА, т. е. МА — ВА,но

тогда

или
q x = tg a x — a. x.
Выражение tgax — ах обозначается invav и называется инволютой. Инволюта,
для углов ах приводится в таблицах 1 в радианах.
Таким образом, подставив в формулу выражение 0V, получим
d x = d0 + inv ax. (1)
Координаты х и у любой точки эвольвенты можно определить, решив уравнения
х = rx sin х; у = rx cos x..
Задаемся рядом значений гх, и для расчета соответствующих углов а,, исполь-
зуем зависимость

Радиус основной окружности

Поскольку при определении профиля зуба фрезы необходимо
найти координаты ряда точек, а расчеты очень трудоемкие, то для
ускорения разработаны таблицы, по которым можно просто и быстро
найти координаты точек профиля [81 ] фрез для нормального заце-
пления с углом 20°.
В расчеты, связанные с определением профиля для различных
колес одного и того же модуля, входит число зубьев колеса, поэтому,
строго говоря, необходимо иметь дисковую модульную фрезу для
каждого профиля впадины. Однако применять большое количество
фрез очень дорого, поэтому можно с известной погрешностью приме-
нять одну и ту же фрезу для нарезания колес с ближайшим числом
зубьев. Неточности профиля, получающиеся при этом, принимаются,
конечно, в пределах допусков колес. Для нарезания зубьев неточных
колес (особенно с небольшими модулями) числа зубьев нарезаемых
колес, начиная от 12 и до бесконечности (число зубьев рейки можно
считать равным бесконечности), разбиты на восемь групп.
Фреза определенного номера нарезает колеса зубьев, лежащие
в пределах:
Номер фрезы 1 2 3 4 5 6 7 8
Число зубьев 12—13 14—16 17—20 21—25 26—34 35—54 55—134 135 и более
' См. Справочник инструментальщика. Т. 1. М., Машгиз, 1948.
334
Такой набор из восьми фрез называется основным набором и при-
меняется для модулей менее 8. Для больших модулей (до 16) разби-
вают все числа зубьев не на 8, а на 15 номеров, а для колес с крупными
модулями — даже на 26 номеров. Расчет координат профиля фрезы,
нарезающей зубчатые колеса с определенным пределом чисел зубьев,
производят по наименьшему числу зубьев. Например, профиль фрезы
№ 6 должен быть рассчитан по впадине шестерни, имеющей 35 зубьев.
Рассчитывать профиль по максимальному числу зубьев 54 нельзя,
так как ошибки в зацеплении могут привести к заклиниванию зубьев
сопрягающихся колес, при расчете по минимальному числу зубьев
заклинивание исключено.
Практически бывает трудно изготовить точный шаблон но координатам, и тогда
заменяют эвольвентный профиль дугами окружности [118]. Однако при такой замене
расчетом должны быть проверены получающиеся неточности, и они должны уклады-
ваться в допустимые отклонения профиля зубчатых колес.
Мы рассмотрели определение координат эвольвентного участка профиля. Для
определения всего профиля дисковой модульной фрезы следует найти координаты
точек не только эвольЕентного участка профиля, но и переходной кривой О1В (см.
рис. 283). Переходную кривую заменяют сопряжением дуги окружности и отрезка
прямой линии.
На рис. 284 приведен полный профиль дисковых модульных фрез. Тип / соот-
ветствует форме профиля для фрез с № 1 до 2. В этом случае профиль образуется
эвольвентным участком СЕ, участком прямой линии СВ и дугой окружности АВ.
Тип // соответствует форме профиля для фрез от № 3 до 7; профиль состоит из
эвольвентного участка BE, дуги окружности В А, прямолинейного участка АО.
Тип /// соответствует форме профиля фрез свыше № 7. Профиль состоит из
эвольвентного участка ЕМ, прямолинейных участков M B и АО и дуги окружности ВА.
Рекомендуемые координаты переходных участков приводятся в соответствую-
щих нормалях.
Дисковые модульные фрезы делятся на черновые (для предвари-
тельной прорезки зуба) и чистовые (для окончательной обработки
впадины зуба). Черновые фрезы для улучшения условий резания проек-
тируются с передним углом 8—10°, так как неточности профиля не
имеют значения при черновой обработке впадины.
Чистовые фрезы рассчитываются для снятия небольшого при-
пуска, но у этих фрез должен быть точный профиль, поэтому передний
угол у приходится делать равным нулю и затачивать зуб по передней
поверхности радиально.
Конструктивные элементы дисковой модульной фрезы (рис. 285) —
наружный диаметр D, диаметр отверстия d и число зубьев z — следует
выбирать по ГОСТу 10996—64 (табл. 28).
Величину затылования К определяют по формуле

и округляют до значения имеющихся затыловочных кулачков (обычно
целые числа). Угол а„ принимают таким, чтобы обеспечить на боковых
сторонах профиля углы ах не менее 3° по формуле

335

Угол м для любой точки образуется между касательной к профилю
в этой точке и осью фрезы.
Конструкция зубьев дисковой зуборезной фрезы показана на
рис. 285, а без подфрезеровки, а на рис. 285, б — с подфрезеровкой.
Высота зуба Н определяется по формулам
Н» h пр + К + r м м; (рис. 285, а)
ориентировочно
Н = hnp (рис. 285, б)
' В формулы входит высота профиля hnp, определяемая после расчета
и построения профиля фрезы. Угол v и радиус г впадины определяются
по тем же формулам, что и для затылования фасонных фрез (см.
гл. XIX). Ширина фрезы В определяется при расчете координат х k
профиля фрезы (см. рис. 284): В =2хк.
После расчета элементов конструкции фрезы рекомендуется вы-
черчивание производить в масштабе. При этом должны соблюдаться
следующие соотношения: толщина т тела фрезы в самом опасном се-
чении над шпонкой должна быть не менее 0,35d (где d — диаметр от-
верстия фрезы); ширина С зуба у основания должна быть не менее
0,75 H.
Черновые модульные фрезы крупных модулей изготовляются сбор-
ными, со вставными ножами, из быстрорежущей стали Р18 или Р9.
Черновые фрезы для мелких и крупных модулей должны иметь на
боковых режущих кромках стружкоразделительные канавки. Допуски
на цельные чистовые дисковые модульные фрезы устанавливаются
техническими условиями по ГОСТу 1678— 53. Чистовые фрезы обычно
изготовляются из быстрорежущей стали Р9.
Дисковые модульные фрезы изготовляются обычно с нешлифован-
ным профилем зуба, однако у фрез из быстрорежущей стали можно
шлифовать профиль зуба. Для облегчения шлифования можно делать
зуб с двойным затылованием.
337
§ 2. ПАЛЬЦЕВЫЕ МОДУЛЬНЫЕ ФРЕЗЫ
Пальцевые модульные фрезы применяются для фрезерования про-
филя прямозубых и косозубых зубчатых колес крупного модуля
(начиная с модуля 10 и выше) тогда, когда нельзя нарезать колесо
червячной фрезой. На рис. 286 показаны пальцевые зуборезные чер-
новые и чистовые фрезы.
Чистовая пальцевая фреза обычно изготовляется с углом у = 0,
т. е. с радиальной передней поверхностью. Профиль зуба такой фрезы
в осевом сечении должен в
точности соответствовать про-
филю впадины колеса, если
обрабатываемое зубчатое ци-
линдрическое колесо имеет
прямые зубья. Когда чисто-
вая фреза предназначается
для фрезерования шевронных
или косозубых колес, то про-
филь несколько отличается
от профиля впадины. Черно-
вая пальцевая модульная фре-
за для обеспечения оптималь-
ных условий резания кон-
струируется с передним углом
у до 8; она имеет также ка-
навки для разделения струж-
ки. Черновые и чистовые
фрезы изготовляются с заты-
лованным, но могут изготов-
ляться и с остроконечным
зубом; тогда необходимо за-
тачивать их по профилю.
Черновые и чистовые фрезы могут быть сборными, со вставными
или с приваренными ножами.
Пальцевые зуборезные фрезы навертываются на оправки. Рас-
пространены две конструкции центрирования и крепления пальцевых
фрез на оправке: с внутренней цилиндрической выточкой (тип а) и
с наружной цилиндрической проточной (тип б).
У фрез типа а (наиболее распространенные) посадочными местами
являются торец и отверстие (рис. 286), а внутренняя резьба нарезается
со значительным зазором и не направляет, а только обеспечивает кре-
пление фрезы. При закреплении фрезы на оправку пользуются гаеч-
ным ключом, для чего имеются лыскн.
Профиль фрез для прямозубых колес рассчитывается по форму-
лам \ приведенным на стр. 343. У фрез для косозубых и шевронных
1 См. литературу [118], а также «Станки и инструмент», 1902, № 2,
колес приходится производить более сложный расчет, так как пальце-
вая зуборезная фреза во впадине колеса должна обрабатывать винто-
вые боковые поверхности зуба колеса и каждая точка фрезы соприка-
сается с винтовой эвольвентной боковой поверхностью зуба в разных
плоскостях.
Наружный диаметр фрезы D определяется с запасом 3—10 мм но
сравнению с максимальной абсциссой xm : lx профиля (см. рис. 283), т. е.
D = 2 xmax + (3 ¸10) мм.
Длина режущей части l Р прини-
мается в зависимости от максималь-
ной глубины у max профиля с запасом
от 3 до 10 мм:
l р = ymax + (3¸10) мм.
Общая длина фрезы L = (1,9¸20) l p.
Диаметр посадочного отверстия d1
диаметр резьбы D и остальные эле-
менты посадочного отверстия могут
быть приняты по нормалям [119].
Для нормальной работы фрезы
важно иметь канавки для стружки
достаточных размеров. Важно раз-
местить зубья у тонкого конца фрезы
так, чтобы, с одной стороны, сохра-
нить прочность зуба, с другой сто-
роны, иметь канавки достаточной
глубины. При большой разнице между
D и d с целью увеличения объема
канавок для выхода стружки часто
приходится зубья у торцовой части
фрезы срезать через один. Угол впа-
дины стружечных канавок принимают
обычно в пределах 45—60°. Число зубьев чистовых фрез рекомен-
дуется с целью облегчения промеров принимать, четным.
На рис. 286 показана черновая пальцевая модульная фреза с боль-
шим объемом канавок для выхода стружки.
Затылование пальцевых фрез можно производить в трех различных
направлениях (рис. 287): радиальное и осевое затылование и затыло-
вание под углом.
При р а д и а л ь и о м з а т ы л о в а н и и (рис. 287, а) изме-
ренная нормалью к профилю величина К1 во всех точках профиля
будет переменной, а при переточках резко изменяется также диаметр,
и это приводит к искажению профиля впадины, потому радиальное
затылование пригодно только для черновых фрез.
При осевом з а т ы л о в а н и и (рис. 287, б) несколько луч-
шие условия в отношении постоянства заднего угла, так как изменение
338
339
величин K1, затылования в различных точках в радиальном направле-
нии направлено так, что частично компенсирует разницу в диаметрах.
Однако при осевом затыловании в точках, где линия профиля парал-
лельна оси фрезы или наклонена к ней под малым углом, получается-
слишком малая величина заднего угла.
При затыловании под углом = 104-15° к оси фрезы
(рис. 287, в) задний угол а остается почти постоянным, так как изме-
нение величины K1 затылования компенсирует разницу в диаметрах
и затылование пригодно для чистовых фрез [120].
ЗУБОДОЛБЕЖНЫЕ ГОЛОВКИ
Разновидностью зуборезного инструмента, работающего мето-
дом копирования, являются специальные зуборезные головки для
контурного зубодолбления (рис. 288). Фасонные резцы, укреплен-
ные в головке, производят одновременное долбление всех впадин
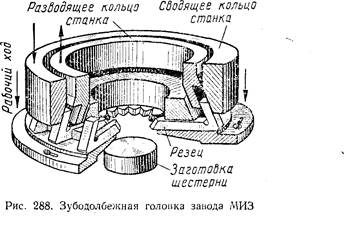
заготовки, т. е. количество резцов соответствует количеству впа-
дин нарезаемого колеса. Каждый резец обрабатывает только од-
ну впадину, и после рабочего хода, при холостом ходе (стрелка
вверх), разводящее кольцо сводит их снова. За несколько двой-
ных ходов резцы углубляются в заготовку на полную глубину
зуба нарезаемого колеса.
Производительность станка с головкой в несколько раз пре-
вышает производительность обычного зубодолбежного или соот-
ветствующего зубофрезерного станка. Применение головки оправ-
дывается только при массовом производстве зубчатых колес одного
модуля и числа зубьев. После такой обработки зубчатые колеса
получаются неточными и необходима чистовая обработка обыч-
ным дисковым зуборезным долбяком или шевером.
При расчете профиля резцов головки вначале определяются
координаты профиля впадины в торцовом сечении колеса, а за-
тем, так как резцы имеют задний и передний углы, координаты
профиля пересчитываются аналогично призматическим фасонным
резцам.
В настоящее время ВНИИ предложена модернизированная
конструкция зубодолбежной головки, в которой используются
быстросменные регулируемые резцы более простых конструкций,
что удешевляет эксплуатацию головки.