XV 1 И РАЗВЕРТКАМИ
Сверла из быстрорежущей стали обеспечивают обработку отвер-
стий по 4—5-му классу точности и по 3—4-му классу чистоты
(Ñ 3 — Ñ 4 по ГОСТу 2789—59). Сверла с пластинками твердых спла-
вов, работающие на более высоких скоростях резания, обеспечивают
обработку отверстий по 3—4-му классу точности и до 4—5-го класса
чистоты (Ñ 4 — Ñ 5). Для получения более точных отверстий (4—3-й
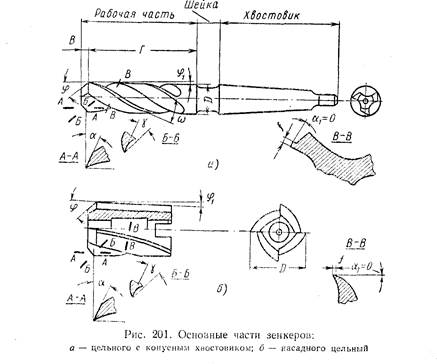
класс точности) и с более чистой обработанной поверхностью (до
6-го класса чистоты) применяют зенкерование.
Процесс зенкерования осуществляется при помощи инструмента,
называемого зенкером (рис. 201), который служит для даль-
нейшей обработки отверстий, полученных после отливки, штамповки
или сверления. Эта обработка отверстия может быть либо оконча-
тельной, либо,промежуточной (получистовой) перед развертыванием,
Дающим еще более точные отверстия и с более чистой обработанной
поверхностью (3—1-й класс точности, 7—9-й класс чистоты).
По характеру работы зенкер подобен сверлу при рассверливании
отверстия. По конструкции и оформлению режущих кромок зенкер,
242
243
предназначенный для увеличения диаметра отверстии, несколько от-
личается от сверла.
Процесс развертывания осуществляется при помощи инструмента,
называемого р а з в е р т к о п. Развертка (рис. 202) во многом напо-
минает зенкер. Основное ее отличие от зенкера заключается в том,
что она снимает значительно меньший припуск и имеет большее число
зубьев 1 — от 6 до 12 (у зенкера три-четыре зуба).
Зенкеры и развертки изготовляют как из инструментальных быстро-
режущих сталей Р18 и Р9, так и с пластинками твердых сплавов
(Т15К6 при обработке сталей; ВК8 ВК6 и ВК4 при обработке чугу-
нов); ручные развертки изготовляют из стали 9ХС.
§ 1. ОСНОВНЫЕ ЭЛЕМЕНТЫ РЕЖУЩЕЙ ЧАСТИ
ЗЕНКЕРА И РАЗВЕРТКИ
Р а б о ч а я часть зенкера (см. рис. 201 и 202) и развертки
снабжена режущими перьями и состоит, в свою очередь, из двух
частей: режущей В и калибрующей Г. Режущая (заборная) часть,
наклоненная к оси под главным углом в плане ср (угол конуса режущей
части 2), выполняет основную работу резания.
1 За исключением специальных однозубых и.двузубыx разверток.
Калибрующая часть служит для направления инстру-
мента при работе, для калибрования отверстии и сохранения размера
'инструмента после его переточки. У развертки, в отличие от зенкера,
калибрующая часть состоит из двух участков: цилиндрического Д
и конического В, так называемого обратного конуса (рис. 202). Обрат-
ный конус делается для уменьшения трения инструмента об обрабо-
танную поверхность и уменьшения величины разбивки отверстия.
Режущие части зенкера и развертки имеют передний угол у. задний
угол а, угол заострения и угол резания .
П е р е д н и и у г о л у у зенкеров из инструментальной стали
равен 10—40°, у разверток — 0 ¸ 10° (0° — для чистовых разверток
и при резании хрупких металлов). У зенкеров с твердосплав-
н ы м и пластинками угол у равен от + 5 до — 5°, а у разверток от 0
до - 5°.
Задний у г о л а на режущей части у зенкеров и разверток
делается 6—15° (большие значения для малых диаметров); задний
угол на калибрующей части равен нулю, так как имеется цилиндри-
ческая ленточка f.
Г л а в и ы й угол в плане у зенкера 30—60°. У развер-
ток из инструментальных сталей: для ручных разверток = 0,5 ¸
¸ 1,5°; для машинных при обработке сквозных отверстий в вязких
металлах (стали) -= 15°, при обработке сквозных отверстий в чугу-
нах = 5°. При развертывании глухих, а также сквозных отверстий
по 3-му классу точности и грубее = 45 ¸ 60°. У разверток, оснащен-
ных пластинками твердых сплавов, = 30 ¸45".
§ 2. ЭЛЕМЕНТЫ РЕЖИМА РЕЗАНИЯ И СРЕЗА
Как и сверло, зенкер и развертка совершают два движения: вра-
щательное и поступательное (рис. 203 и 204).
Сжорость резания

где D — диаметр в мм;
п — число оборотов в минуту.
Подача — величина перемещения зенкера или развертки вдоль
оси за один оборот (s мм/об). Подача, приходящаяся на один зуб зен-
кера (развертки),

где z — число зубьев инструмента.
Минутная подача 
Тол щ и н а срез а, снимаемая каждой режущей кромкой
(рис. 203, а и 201),

2-15
Толщина среза при развертывании (см. рис. 204) обычно незначи- мый (0,02—0,05 мм) и a £ , что вызывает сосредоточение давления
|
Рис. 203. Элементы резания при зенкеровании
со стороны срезаемого слоя вблизи режущей кромки, большую дефор-
мацию срезаемого слоя, а также большое трение по задней поверх-
ности зуба развертки и интенсивный ее износ.
Ширина среза b равна длине ак-
тивной части режущей кромки:
_£_ = Rzr У*
где t — глубина резания в мм. Г л у б и на резания
D -- D„
|
sin ф 2 sin ф
-w/1 Drr--Jt -i/—1
Рис. 204. Элементы реза- ния при развертывании
|
где D — диаметр инструмента в мм;
D 0 — диаметр ранее полученного отвер-
стия в мм.
Глубина резания определяется припус-
ком на обработку; при з е н к е р о в а н и и
t до 7 мм (на сторону).
Ниже приведены средние значения припусков под зенкеро-
ван и е после сверления:
/Диаметр зенкера
в мм.................... До 20 21—35 3G—45 46-50 51—60 61—70 71—80
Припуск на сторо-
ну "в мм............. 0,5 0,75 1 1,25 1,5 1,75 2
Глубина резания для чистовых (окончательных) разверток
принимается 0,05—0,25 мм на сторону. Для предварительной (черно-
вой) развертки припуск на сторону может быть увеличен в 2—3 раза.
Ниже приведены средние значения припусков при чистовом (окон-
чательном) развертывании.
Диаметр разверт-
ки в мм............... До 5 6—10 11—15 16—30 31—50 51—60 61—80
Припуск на сторо-
ну в мм.............. 0,05 0,075 0,1 0,125 0,15 0,2 0,25
Площадь поперечного сечения среза, приходя-
щаяся на одну режущую кромку,

Общая площадь поперечного сечения среза
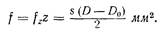
Машинное время при зенкеровании и развертывании под-
считывается по формуле

где L — полный путь, проходимый инструментом в направлении
подачи, в- мм;
I — глубина обрабатываемого отверстия в мм (см. рис. 203, б);
у — величина врезания в мм; у = t ctg cp, при одинарной заточке;
(y» (t — 0,5) ctg 60° + 0,5 ctg 30°, при двойной заточке под
углами = 60° и = 30°;
А — величина перебега в мм ( = 1 ¸ 3 мм).
§ 3. ОСЕВАЯ СИЛА 5! МОМЕНТ
В результате сопротивления срезаемого слоя разрушению (струж-
кообразованию) на зенкер и развертку в процессе резания будут дей-
ствовать силы, Которые необходимо преодолеть механизму главного
движения и механизму подачи станка.
Как и при сверлении, на зенкер действуют осевая сила1
(сила подачи) и м о м е н т от сил сопротивления резанию.
Момент
М = См Dz м fxsy м KM кГ ■ мм.
При зенкеровании конструкционных сталей с в = 75 кГ/'мм2
зенкером, оснащенным сплавом Т15К6, См = 943; z м = 0,75; хм = 0,8;
ум = 0,95 197].
Осевая сила и момент при развертывании незначительны (вследст-
вие малой глубины резания), а потому подсчитыьаются редко.
1 Обычно незначительной величины.
2-16
247
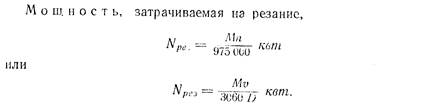
Необходимая (потребная) мощность электродвигателя станка

§ 4. ИЗНОС И СТОЙКОСТЬ ЗЕНКЕРОВ
И РАЗВЕРТОК
В общем случае при обработке сталей зенкер из быстро-
режущей стали изнашивается по задней поверхности, по угол-
кам, по ленточке и по передней поверхности (см. рис. 205, а).
При обработке зенкером отверстия, к поверхности которого не
предъявляется особых требований по чистоте, пли когда зенкерованые
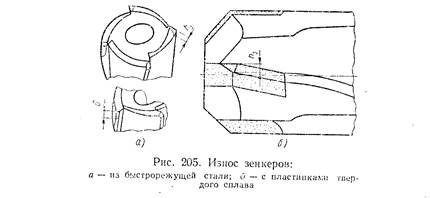
является промежуточной (не окончательной) операцией, за критерий
износа принимается оптимальный износ. Если же зенкер предназна-
чается для окончательной обработки поверхности (Ñ5—Сб), то за кри-
терий износа принимается технологический износ (т. е. такая его вели
чина, начиная с которой не получается допустимая точность или чи-
стота обработки). За лимитирующий износ зенкеров из и и с т р у -
м е н т а л ь и ы х с т а л е й при обработке сталей принимается из-
нос по задней поверхности h 1, = 1,2 ¸ 1,5 мм, при обработке чугунов—
износ по уголкам — 0,8 ¸ 1,5 мм.
Зенкеры с п л а с т инка м и тверд ы х сплавов изна-
шиваются в основном по задней поверхности и уголку (рис. 205, б).
За лимитирующий износ принимается износ по задней поверхности
h 3 = 1 ¸ 1,6 мм.
Средние периоды стойкости для зенкеров 30—100 мин [67].
Так как развертки работают с малыми толщинами среза
и на относительно низких скоростях резания, то они изнашиваются
в основном по задней поверхности и уголку; захватывается при этом
и ленточка.
Развертка является чистовым (отделочным) инструментом, а по-
тому за критерий ее износа принимается технологический износ. Мак-
симально допустимая величина износа по задней поверхности для раз-
верток из инструментальных сталей h 3, = 0,6 ¸ 0,8 мм.
Для разверток с пластин-
ками твердых сплавов
h ;, = 0,4 ¸0,7 мм (рис. 206).
При работе изношенной разверт-
кой отверстие становится эксцент-
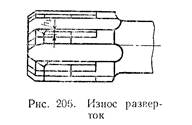
ричиым и может быть меньше и больше номинального размера раз-
вертки. Последнее объясняется тем, что зубья развертки изнаши-
ваются обычно неравномерно. Мелкая стружка и металличе-
ская пыль, образующиеся при развертывании, заклиниваясь
между стенкой отверстия и изношенным в большей степени зубом, соз-
дают отжим развертки на некоторую величину (рис. 207). Противо-
положный зуб начинает срезать слой большей глубины, увеличивая
диаметр отверстия и создавая его эксцентричность. Заклиненная мел-
кая стружка царапает при этом обработанную поверхность, ухудшая
ее чистоту (микрогеометрию).
Кроме указанного, по мере увеличения износа нарост становится
более прочным, что также приводит к увеличению диаметра отверстия
и к ухудшению чистоты обработанной поверхности.
На разбивку отверстия ' (увеличение диаметра обработанной
поверхности) большое влияние оказывает соосность развертки и
1 В практике встречаются случаи «отрицательного» ртбивания отверстия,
т. е." уменьшение диаметра обработанной поверхности по отношению к диаметру
развертки, которой данная поверхность была получена. Это может быть при малых
углах , когда увеличиваются упругие деформации обработанной поверхности.
24й
249
предварительно обработанной поверхности: чем точнее соосность, тем
меньше разбивка.
Для машинных разверток из инструментальных сталей при обра-
ботке стали стойкость Т = 40 ¸ 120 мин, а при обработке чугуна
Г = 60 ¸ 180 мин [97].
Для разверток с твердосплавными пластинками Т = 23 ¸ 180 мин
при обработке незакаленных сталей и Т = 30 ¸ 240 мин при обра-
ботке чугуна [100].
§ 5. СКОРОСТЬ РЕЗАНИЯ ПРИ ЗЕНКЕРОВАНИИ
И РАЗВЕРТЫВАНИИ
На скорость резания, допускаемую режущими свойствами зенкера
и развертки, оказывают влияние следующие факторы: обрабатывае-
мый материал, материал режущей части, диаметр, глубина обрабаты-
ваемого отверстия, подача, период стойкости и смазывающе-охлаждаю-
щая жидкость.
Скорость может быть подсчитана по формуле
|все обозначения те же,
что и при рассверливании (см. стр. 228].
В табл. 17 приводятся значения Cv, zv, m, xv и yv для зенкеров,
а в табл. 19 — для разверток. Приведенные в табл. 17 и 18 значения
применимы при обработке горячекатаной стали с охлаждением эмуль-
сией, при обработке серого чугуна — всухую. В случае измененных
условий обработки на приведенные значения С„ необходимо учесть по-
правочные коэффициенты, численно равные поправочным коэффи-
циентам, вводимым при сверлении (см. гл. XIV), или учесть их через
коэффициент К v в формуле для vu.
Таблица 17
Значения Cv, m, zv, xv и у v для зенкеров [97]
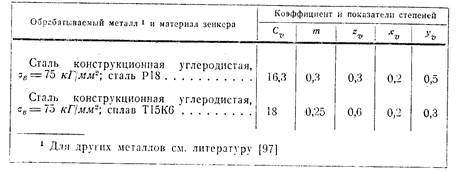
При развертывании с охлаждением эмульсией конструкционных
углеродистых, хромистых и хромоникелевых незакаленных
250
сталей развертками с пластинками твердого сплава
марки Т15К6 НИБТН рекомендует следующую формулу [100]:
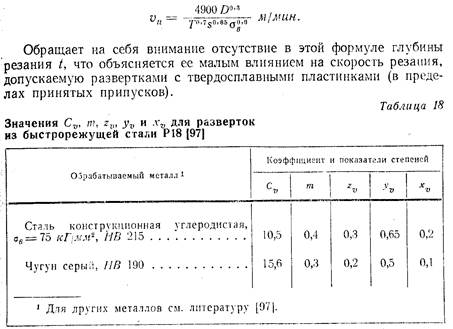
При зенкерованин и развертывании применяют смазывающеохла-
ждающие жидкости. Так как процесс развертывания совершается при
относительно низких скоростях резания и с малыми толщинами среза,
то условия для проявления эффективных свойств жидкости здесь
особенно благоприятны. При соответствующем подборе жидкости
исчезают налипы мелкой стружки на поверхности зуба развертки,
уменьшается заедание развертки, повышаются качество и точность
обработанной поверхности и увеличивается стойкость развертки.
При обработке сталей применяют эмульсии, сульфофрезол (за ис-
ключением обработки легированных сталей), компаундированные и
растительные масла; при обработке ковкого чугуна — эмульсии; при
обработке серого чугуна—эмульсии, керосин или обрабатывают всу-
хую; при обработке алюминия применяют скипидар с керосином.
§ 6. НАЗНАЧЕНИЕ ЭЛЕМЕНТОВ РЕЖИМА РЕЗАНИЯ
ПРИ ЗЕНКЕРОВАНИИ И РАЗВЕРТЫВАНИИ
Порядок назначения режимов резания тот же, что и при сверлении.
1. Подача s при зенкерованин, при прочих одинаковых усло-
виях, допускается большей, чем при сверлении и рассверливании.
Это объясняется тем, чю, имея лучшие условия работы (отсутствие
поперечной кромки, более рациональные углы резания вдоль режущей
кромки, меньшая глубина резания), зенкер имеет и большее число ре-
жущих кромок, так что при одной и той же подаче s. общая подача s
при зенкерованни будет больше.
Рекомендуемые подачи приводятся в справочниках по режимам
резания 151,97, 98, 100]. Выбранная по таблицам справочников подача
корректируется, затем, по кинематическим данным станка.
2. После выбора подачи, зная глубину резания (припуск на обра-
ботку на сторону) и задавшись стойкостью, определяют скорость
р е з а и и я, допускаемую режущими свойствами инструмента.
3. По найденной скорости резания подсчитывают число обо-
ротов, которое корректируется по кинематическим данным станка
(берется ближайшее меньшее или ближайшее большее, если оно не пре-
вышает больше, чем на 5%).
По скорректированному числу оборотов па подсчитывавшей дейст-
вительная скорость резания, с которой будет производиться обработка.
4. При зенкерованни производится проверка вы-
бранных элементов режима резания по прочности слабого звена меха-
низма главного движения станка (при работе на малых числах оборо-
тов шпинделя) п по мощности электродвигателя станка аналогично
тому, как это производится при сверлении (прочность механизма подачи
станка при зенкерованни обычно не проверяется, так как осевая сила
при зенкерованни незначительна).
При р а з в е р т ы в а н и и, вследствие незначительных вели-
чин момента, осевой силы и мощности, затрачиваемой на резание, эле-
менты режима резания по прочности и мощности станка обычно не про-
веряют.
5. Подсчитывают м а ш и и и о е в р е м я.
Глава РАСЧЕТ И КОНСТРУИРОВАНИЕ ЗЕНКЕРОВ
XVII И РАЗВЕРТОК
§ 1. ОСНОВНЫЕ ЭЛЕМЕНТЫ КОНСТРУКЦИЙ
ЗЕНКЕРОВ И РАЗВЕРТОК
Зенкер и развертка (см. рис. 201 и 202), помимо рабочей части
(см. стр. 244), определяемой такими конструктивными элементами,
как D — диаметр, l 0 — длина рабочей части, z — число зубьев, углы
режущей части (2, , , ), / — ленточка на калибрующей части,
имеют соединительную часть в виде цилиндрического
или конического хвостовика (в случае насадного инструмента соеди-
нительной частью является отверстие). Имеются еще и другие конст-
руктивные элементы, определяющие конкретный тин зенкера или
развертки.
Диаметр зенкера и развертки. Зенкер предназначен для предва-
рительной обработки отверстия после сверла под развей гьшаине; дна-
метр его выбирается меньше номинального диаметра отверстия на не
личину припуска под развертывание.
Если зенкер предназначен для окончательной обработки отверстий,
диаметр его принимается с учетом допуска отверстия, величины раз-
бивки и запаса па износ.
По ГОСТу 1677—53 «Техни- Таблица 19
ческие условия» зенкер, пред- Отклонении размеров диаметра
назначенный для предвари- зенкеров
тельного зенкерованни отвер-
стий под развертку, обозна-
чается «зенкер № 1>, зенкер,
предназначенный для окон-
чательной обработки отвер-
стий — «зенкер № 2». В табл.
19 приведены отклонения раз-
меров диаметра зенкера.
Развертка обрабатывает
более точные отверстия, и кон-
структору при назначении диаметра развертки необходимо учитывать:
1) разбивку, так как отверстие, получаемое после развертки, почти
всегда несколько больше размера диаметра развертки; 2) запас на
износ, так как развертка изнашивается по диаметру от трения о стенки
обрабатываемого отверстия; 3) допуски
на изготовление самой развертки.
1 Разбивка в отдельных случаях может иметь не только положптель:ую, но и отрицательную величину, когда отверстие после развертывания может бы гь меньше развертки (например, при обработке высокопрочна'; пли очень вязких м.гл-риалов').
|
На рис. 208 схематично показано
расположение полей допусков па диаметр
развертки в зависимости от допуска об-
рабатываемого отверстия. Буквой А
обозначен допуск на отверстие. Линия
C D — верхнее отклонение диаметра раз-
вертки, она лежит пила- верхнего от-
клонения диаметра отверстия на вели-
чину максимальной 1 разбивки Р max.
Максимальная величина разбивки зави-
сит от условий работы (в том числе и
соосности развертки с обрабатываемым
отверстие:,.), диаметра развертки, класса
точности развертываемого отверстия
Линия EF показывает нижнее отклоне-
ние диаметра развертки, a Pmin — мини-
мальную величину разбивки. Таким об-
разом, между верхним CD и нижним Е F отклонениями лежит поле
допуска Б на развертку. Это ноле допуска разбивается на допуск
2 53
на изготовление В и запас на износ И Ниже приводятся рекомендуе-
мые величины допусков (табл. 20).
Таблица 26