XV
§ 1. ОСНОВНЫЕ ЭЛЕМЕНТЫ КОНСТРУКЦИИ СВЕРЛ
По конструкции все существующие типы сверл сводятся к сле-
дующим основным группам: спиральные сверла, сверла с прямыми
канавками, перовые сверла, сверла для глубоких отверстий, сверла для
кольцевого сверления, центровочные сверла и специальные комби-
нированные сверла. Каждый из приведенных типов имеет значи-
тельное количество разновидностей конструкций.
Разберем основные конструктивные элементы наиболее распро-
страненных спиральных сверл (см. рис. 173). К конструктивным
элементам относятся: D — диаметр сверла; 2 — угол режущей
части (угол при вершине); — угол наклона винтовой канавки;
, у, — геометрические параметры режущей части сверла, т. е.
передний и задний углы и угол резания; d — толщина сердцевины
(или диаметр сердцевины); b —- ширина пера (зуба); f — ширина
ленточки; обратная конусность; форма режущей кромки и профиль
канавки сверла; /0 — длина рабочей части; L — общая длина сверла.
Диаметр сверла всегда следует брать немного меньше, чем диаметр
просверливаемого им отверстия, так как происходит «разбивка», т. е.
увеличение диаметра отверстия при сверлении.
Данные для выбора диаметра сверла приведены в ГОСТе 885—64.
Допуски на диаметр спиральных сверл в зависимости от условий ра-
боты следовало бы давать различные, однако в действительности
трудно предвидеть точное назначение сверла, и поэтому допуски на
диаметр принимаются единые.
Диаметр направляющей части спирального сверла с целью умень-
шения трения о стенки отверстия уменьшается по направлению к хво-
стовику, т. е. направляющая часть сверла имеет обратную конус-
ность:
Диаметр сверла в мм................................. 1—6 Св. 6 до 18 Св. 18
Обратная конусность в мм на каждые
100 мм длина....................................... 0,03—0,07 0,0-1—0,08 0,05—0,10
В табл. 15 приведены рекомендуемые значения угла со в зависи-
мости от диаметра у сверл общего назначения. В табл. 16 приводятся
рекомендуемые значения угла наклона со и угла 2ср для сверл в за-
висимости от обрабатываемого материала.
Сердцевина и поперечная кромка сверла. Размер (диаметр) сердце-
вины у спиральных сверл является важнейшим элементом. При недо-
статочном диаметре сердцевины сверло будет менее жестким, а следо-
вательно, будет выдерживать меньшие крутящие моменты. С другой
стороны, при уменьшении сердцевины значительно уменьшается
осевое усилие и облегчается процесс сверления, так как уменьшается
поперечная кромка.
■• ' Данные табл. 16 относятся к сверлам, начиная с диаметра 10 мм и
выше; у более мелких сверл следует принимать иные углы; кроме того,
данные таблицы предусматривают изготовление сверл из быстрорежущей,
углеродистой или легированной стали, но не из твердого сплава.
Размер сердцевины для сверл из углеродистой и быстрорежущей
стали, по данным инструментального завода «Фрезер», принимается
в следующих пределах: у сверл диаметром от 6 до 10 мм в пределах
(0,2 ¸ 0,25) D; у сверл свыше 10 мм диаметр сердцевины принимается
равным (0,13 ¸ 0,16) D. Сверла с пластинками твердого сплава имеют
другие соотношения: сердцевина у них делается относительно боль-
шой, так как такое сверло сильно ослабляется при врезании пластинки.
230
231
Принимаются следующие значения диаметра сердцевины для сверл
с пластинками твердого сплава: для сверл диаметром до 10 мм серд-
цевина равна (0,27 ¸ 0,3) D; для сверл диаметром свыше 10 мм она
равна (0,25 ¸0,26) D.
У сверл, канавки которых обрабатываются на фрезерном станке,
диаметр сердцевины по направлению к хвостовику увеличивается
на 1,4—1,8 мм на 100 мм длины. Это обеспечивает большую проч-
ность и жесткость сверла.
Ширина пера, b выбирается из соображений прочности сверла,
а ширина канавки — из условия достаточного пространства для
помещения стружки и отвода ее от режущей кромки во время работы
сверла. Обычно принимают ширину пера равной ширине канавки,
т. е. при двух перьях равной '/4 окружности сверла. Однако для
сверл с большим углом со ширину канавки следует немного увели-
чивать. В чертежах сверл ширина пера b дается псрпеи/.икулярно
винтовой канавке. Для быстрорежущих сверл заводом «Фрезер»
принимается
Значения коэффициентов в этой формуле:
коэффициент С определяется в зависимости от углов 2ср и со следую-
щим образом:
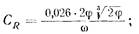
коэффициент, учитывающий изменение диаметра перемычки,
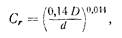
где d — диаметр перемычки (сердцевины) сверла.
Коэффициент, учитывающий влияние диаметра канавочной фрезы,
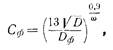
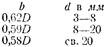
Ферма режущей кромки и поперечного сечения
канавки сверла [32]
Режущая кромка сверла — линия, образованная пересечением передней по-
рерхности канавки сверла и задней поверхности заточки, —обычно выполняется
прямолинейной. Однако, как показали исследопания, большего постоянства перед-
него угла у можно добиться при криво-
линейной (выпуклой) режущей кромке.
Форма поперечного сечения канавки
сверла в чертежах не указывается, а при-
водится другой элемент — профиль зуба
канавочной фрезы (у сверл с фрезерован-
ными канавками) или профиль прокатан-
ной заготовки (у витых сверл).
Профиль канавочной фрезы (форма
его показана на рис. 191) можно опреде-
лить двумя методами: графическим, когда
профиль фрезы строится по заданному
профилю сперла, и аналитическим, при
котором кривые профиля рассчитываются
по аналитическим формулам.
Все элементы профиля [6 и 39]
канавочной фрезы (радиусы R 0,
RK и ширину В; рис. 191) можно определить упрощенным аналити-
ческим способом.
Приближенная формула для определения радиуса R 0 профиля
фрезы для сверла диаметром D имеет следующий вид [99]:
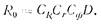
232
D ф — диаметр канавочной фрезы.
Радиус закругления вершины фрезы
RK = CKD,
Ск — коэффициент, определяемый по формуле
С к = 0,015 75.
Так как угол обычно мал (равен 10°), можно приближенно
принять
В» R 0 + RK.
Построенный или рассчитанный профиль фрезы, строго говоря,
пригоден только для одного диаметра сверла при определенных зна-
чениях угла наклона винтовой линии, угла при вершине, размера
сердцевины. Но при таких условиях потребовалось бы большое коли-
чество фрез. Поэтому практически одной фрезой обрабатываются
сверла в определенном диапазоне диаметров; получающиеся при этом
неточности не пмекп большого значения.
Рабочая часть сверла может быть получена не только фрезерова-
нием, но и завивкой.
Основное отличие витых сверл заключается в том, что винтовые
канавки у них получены не.фрезерованием, а путем прокатки круглой
заготовки (рис. 192) и последующей завивки. При такой технологии
сокращается расход быстрорежущей стали.
23З
Существует несколько способов получения витых сверл (секторный
прокат, поперечный прокат, продольно-винтовой прокат и т. д.)1.
Ленточка f — узкая полоска зуба, отшлифованная по диа-
метру, принимается обычно в пределах (0,06—0,07) диаметра сверла
по ширине и (0,03—0,02)
диаметра сверла по высоте.
Ленточка — важный элемент;
от нее зависит направле-
ние сверла и потери на из-
лишнее трение при сверле-
нии.
Длина l 0 рабочей
части сверл приводится
в соответствующих стандар-
тах. У сверл, оснащенных
твердым сплавом, длину ра-
бочей части следует брать
короче, чем у быстрорежу-
щих сверл, так как запас на
переточку из-за небольшой
длины пластинки будет зна-
чительно меньше. Как общая
длина сверла, так и длина
рабочей части влияет на жест-
кость сверла, поэтому там,
где нет необходимости при-
менять длинные сверла (на-
пример, при центровании),
следует применять укорочен-
ные сверла, чтобы уменьшить
опасность поломки.
Форма хвостов и-
к а сверла определяется ме-
тодом крепления сверла. Мел-
кие сверла (диаметром до
10—12 мм) изготовляются с цилиндрическим хвостовиком и закреп-
ляются в зажимных патронах. Более крупные сверла изготовляются
обычно с коническим хвостовиком.
§ 2. ОСОБЕННОСТИ КОНСТРУКЦИЙ ОТДЕЛЬНЫХ
ТИПОВ СВЕРЛ
В настоящее время стандартами охвачены основные типы сверл,
в том числе: а) сверла из углеродистых и быстрорежущих сталей,
с цилиндрическим и коническим хвостовиками, различной длиной
1 Подробно приводится в курсам технологии режущего инструмента,
(короткие, нормальные, длинные и т. д.); б) сверла, оснащенные
твердым сплавом с цилиндрическим и коническим хвостовиками;
в) центровочные сверла. Основные конструктивные размеры сверл
указаны в ГОСТах. Ниже остановимся кратко на описании сверл,
оснащенных твердым сплавом,
и ряда нестандартизованных
конструкций, но нашедших
применение в промышлен-
ности.
Сверла, оснащен-
ные твердым с п л а -
в о м, применяют для сверле- ■
ния чугуна, закаленной ста-
ли, пластмассы, стекла, мра-
мора и др., особенно в тех
случаях, когда сверление
производится на высоких ско-
ростях с небольшими по ве-
личине подачами. Существует
несколько типов сверл, осна-
щенных твердыми сплавами.
Цельные, так называемые
монолитные сверла, изготов-
ляют небольших диаметров.
На рис. 193, а показано сверло
конструкции института твер-
дых сплавов. На рис. 193, б
показана конструкция твердо-
сплавного монолитного свер-
ла, изготовляемого по спосо-
бу, предложенному ВНИИ.
Размеры сверл: D —
= 2¸10 мм; общая длина
L = 30 ¸ 65 мм; длина рабо-
чей части l 0 =15¸45 мм;
ширина ленточки f = 0,2 ¸
¸ 0,6 мм; толщина сердце-
вины k =0,9 ¸ 5 мм. Сверла,
изготовляемые из твердого сплава марок ВК6М и ВК8М, предназна-
чаются для обработки закаленных, нержавеющих и жаропрочных
сталей, термореактивных пластмасс и керамики. Применение монолит-
ных твердосплавных сверл обеспечивает повышение стойкости до
10 раз и выше по сравнению с быстрорежущими.
Сверла с косыми канавками просты по конструкции: в цилиндри-
ческой державке (рис. 193, в) из стали 9ХС прорезается паз, в кото-
рый впаяна пластинка из сплава ВК8. Такие сверла удобны при
сверлении неглубоких отверстий.
234
235
Сверла с винтовыми канавками предназначаются для сверления
отнесений в хрупких и в вязких металлах при высоких режимах ра-
боты, а также в неметаллических материалах. На рис. 193, г показано
(.'снащенное твердым сплавом сверло с коническим хвостовиком. Вин-
товые канавки имеют переменный шаг. Вначале у режущей части угол
наклона — 5 ¸ 6°, а часто даже равен 0 (т. е. прямая канавка),
а дальше канавка идет под небольшим углом наклона о =15 ¸20°.
Длина канавки принимается от 4,5 до 5,5 диаметра. Общая длина
сверла также соответственно меньше, чем у сверл из быстрорежущей
стали.
Ввиду ограниченного числа переточек обратная конусность должна
быть больше, чем у нормального сверла, и равна 0,6—0,8 мм на
100 мм длины. Для возможности работы с кондуктором конусность
делается только на длине пластинки, а корпусГсверла шлифуется по
цилиндру.
На рис. 193, д показано сверло с прямыми канавками (по данным
завода «Фрезер»). Такое сверло предназначается для сверления в чу-
гуне и в хрупких материалах отверстий глубиной до 2—3 диаметров.
Сверла для глубоких отверстий. Если глубина отверстий превы-
шает 5 D, то такие отверстия принято называть глубокими.
При большой глубине отверстия условия резко изменяются:
ухудшается отвод стружки и тепла, уменьшается жесткость сверл
и т. д. Поэтому обычное спиральное сверло непригодно для глубокого
сверления. Применяют два способа сверления глубоких отверстий:
1) обычный способ, при котором весь материал, отделяемый от заго-
товки, превращается в стружку; отверстия диаметром до 70 мм чаще
всего сверлятся именно так; 2) способ кольцевого сверления, при
котором высверливается кольцевая полость, а в центральной части
отверстия остается стержень; таким способом сверлятся отверстия
больших диаметров, так как для меньших отверстий сверло оказы-
вается непрочным.
Сверла для глубокого сверления можно разделить на: 1) много-
кромочные сверла с перемычкой, т. е. сверла, имеющие две главные
режущие кромки; 2) однокромочные сперла, или сверла односторон-
него резания.
На рис. 194 показаны некоторые конструкции мпогокромочных
сверл. В настоящее время в СССР для изготовления мпогокромочных
сверл применяется технология, разработанная инж. П. Я- Овчин-
никовым. В короткой заготовке сверлятся два отверстия, в которые
вставляются стержни из наполнителя; затем производится прокатка
профиля сверла, и длина заготовки соответственно увеличивается.
После завивки в процессе нагрева (при термической обработке) на-
полнитель удаляется, и в сверле остаются глубокие отверстия для
охлаждения, располагающиеся по винтовой линии (рис. 194, а).
На рис. 194, б показано спиральное двухкромечнос составное
сверло с четырьмя направляющими ленточками (вместо двух), обра-
зующими каналы для охлаждающей жидкости. Отвод стружки осу-
ществляется через внутренние отверстия и стебель, представляющий
собой трубку. Охлаждающая жидкость под давлением 10—20 a m
подается в пространство между наружным диаметром стебля и стен-
ками отверстия.
Сверление производится на специальном станке, имеющем устрой-
ство для подвода жидкости.
Спиральное короткое сверло с наружным отводом стружки
(рис. 194, в) также имеет две главные режущие кромки. При сверлении
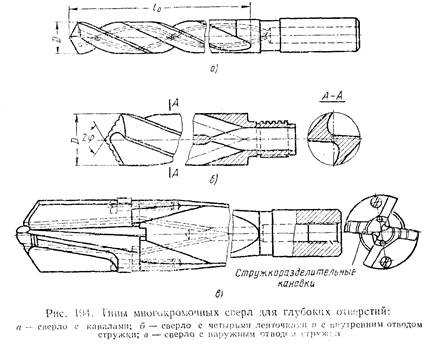
жидкость подводится по каналу в стебле сверла и распределяется
при помощи отдельных мелких отверстий по режущим кромкам свёрла.
Для спокойной работы сверла необходимо обеспечить форму стружки
в виде мелких завитых спирален (это касается всех сверл для глубо-
кого сверления). Для этой цели на кромках сверла делают стружко-
разделительиые канавки. Это сверло, однако, не обеспечивает прямо-
линейной оси отверстия, оо оипо если заточка произведена непра-
вильно п длина режущих кромок различна.
Можно обеспечить глубокое сверление, если взять длинное сверло
с обычной геометрией и сверлить, часто приостанавливая процесс и
вынимая сверло, с тем чтобы охладить его и удалить накопившуюся
в канавках стружку Такое сверление (оно носит название «шаг за
шагом») малопроизводительно. В СКБ-8 разработано сверло (рис. 195),
237
имеюш.ее очень крутые винтовке канавки, = 50 ¸ 65° (по виду
сверло напоминает бурав для дерева) и измененную форму стружечных
канавок по сравнению со стандартными сверлами. Сверло хорошо
выводит стружку из зоны резания и позволяет осуществлять сверление
глубоких отверстий. Предназначаются сверла для сверления отверстий
длиной более 10 d в чугуне, стали, легких сплавах и дереве.
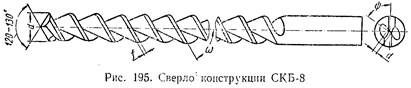
Для получения лучших результатов в отношении прямолиней-
ности оси отверстия необходимо устранить совсем или ослабить вред-
ное влияние перемычки на увод сверла в сторону. Достигается это
путем применения сверла с отверстием для образования сердечника.
Такое сверло не обращает в стружку весь металл, а оставляет тонкий
стержень (сердечник), благодаря чему улучшается направление сверла.
Основным преимуществом многокромочных сверл является их
высокая производительность по сравнению с однокромочными. Вместе
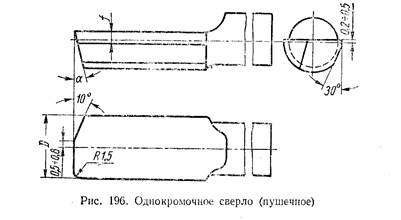
с тем все конструкции многокромочных сверл в той или иной степени
имеют общий недостаток — наличие поперечной кромки (перемычки).
Даже идеально заточенное многокромочное сверло с перемычкой не
гарантирует от увода сверла с оси детали. Многокромочные сверла не
гарантируют также чистоты поверхности отверстия, так как вслед-
ствие наличия перемычки работают с вибрациями. Указанные недо-
статки многокромочных сверл частично устраняются при использо-
вании сверл одностороннего резания.
На рис. 196 показана простейшая конструкция однокромочного,
так называемого пушечного сверла (или лопаточного). Оно представ-
ляет собой стержень, передний конец которого срезан до центра и
заточен под соответствующими углами. Во избежание заедания сверла
в отверстии передняя поверхность расположена выше центра на
0,2—0,5 мм в зависимости от диаметра сверла.
Сверло имеет главную режущую кромку, направленную перпен-
дикулярно оси отверстия и на 0,5—0,8 мм проходящую через центр.

Вспомогательная режущая кромка может быть срезана под углом 10°.
Сверло работает с направлением по предварительно надсверленному
отверстию. Для направления по отверстию сверло имеет цилиндриче-
скую поверхность, которая опирается о стенки просверленного от-
верстия. Геометрия сверла невыгодная: угол резания 90", задний
угол 8—10°. Для уменьшения трения направляющей о стенки отвер-
стия срезана лыска иод углом 30° и направляющая имеет обратный
конус в пределах 0,03—0,05 мм на 100 мм длины.
Для получения точных отверстий с прямолинейной осью приме-
няются так называемые ружейные сверла. Они также представляют
собой инструмент одностороннего резания. Такое сверло (рис. 197, а) *
* На рис. 197, б в целях ясности чертежа показаны реакции сил Rw и RN, равные
им, но противоположно направленные.
238
239
состоит из двух основных частей: режущей части, изготовляемой из
быстрорежащей стали или из твердого сплава, и зажимной части
или стебля сверла, изготовляемого из углеродистой стали. Стебель
представляет собой длинную трубку, которой придают форму, пока-
занную в сечении по CD. По внутреннему отверстию в трубке к ре-
жущей части сверла под высоким давлением подается охлаждающаяся
жидкость, которая выполняет двойную роль: она отводит тепло от
режущей части сверла и удаляет образующуюся стружку из зоны
резания.
Сверло во время работы испытывает одностороннее кручение, сжа-
тие и продольный изгиб; необходимо ввиду этого обеспечить доста-
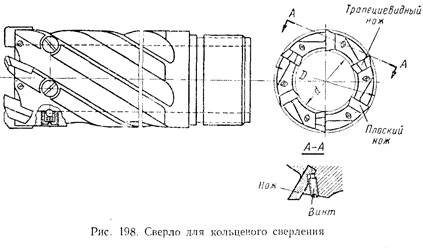
точную жесткость державки, следовательно, канал должен быть наи-
меньшим; с другой стороны, для обеспечения свободного выхода
стружки из канавки сверла требуется дать максимальное сечение
канавке. Поактически установлен и рекомендуется угол =
= 100 ¸ 120°.
Сверла для кольцевого сверления. При сверле-
нии отверстий большого диаметра (D > 80 мм) вырезается кольце-
вая полость, а в середине остается сердечник, который затем может
быть удален. Сверло для кольцевого сверления (рис. 198) состоит из
корпуса с закрепленными в нем ножами, причем режущие кромки
ножей выступают со стороны торца, наружного диаметра корпуса и
со стороны его внутреннего диаметра. При вращении ножи вырезают
кольцевую полость. За трапециевидным прорезным ножом следует
плоский зачистной. Для направления сверла при глубоком
сверлении в отверстии корпус сверла имеет направляющие лен-
точки (или иногда кулачки, которые изготовляются из пластмассы
или дерева).
§ 3. ЗАТОЧКА СВЕРЛ
Станки для заточки сверл можно разбить на три группы: 1) для
конической заточки, когда поверхности сверла, образуемые при за-
точке, являются коническими; 2) для винтовой заточки, когда поверх-
ности сверла, образуемые при заточке, являются винтовыми; 3) для
-плоской заточки.
На рис. 199, а и б показаны два способа заточки свгрл на стан-
ках, относящихся к п е р в о й группе. Они различаются между
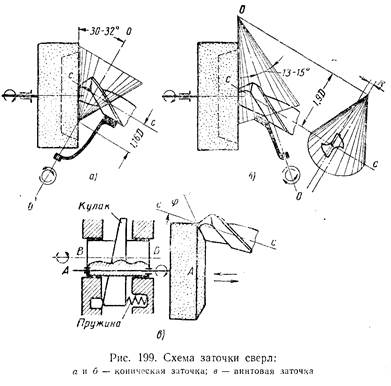
собой только схемой расположения оси воображаемого конуса отно-
сительно сверла.
Приспособление для установки сверл (губкодержатель) конструи-
руется таким образом, чтобы вершина конуса, по которому произво-
дится заточка, была расположена на определенном расстоянии от
оси сверла; при первом способе (рис. 199, а) это расстояние равно
1,16 D, а при втором способе (рис. 199, б)— 1,9 D. Кроме того, ось
конуса смещается от оси сверла на расстояние К, равное ]/13—]/10
Диаметра сверла. Различное расположение осп воображаемого ко-
240
241
нуса относительно оси сверла дает различную картину изменения
задних углов по всей длине режущей кромки сверла. Для сверла
лучше, когда задний угол у наружного диаметра меньше, чем у центра.
Поэтому наибольшее распространение получила заточка по второму
способу, которая резко увеличивает задний угол по направлению
к центру сверла. Заточка по первому способу увеличивает задний угол
значительно меньше.
Широкое распространение имеет в и н т о в а я заточка (рис. 199, в)
Сверло, зажатое в патроне, медленно вращается вокруг своей оси СС.
Шлифовальный круг, кроме основного вращения вокруг оси АА,
получает еще дополнительные движения — вращение вокруг оси ВВ
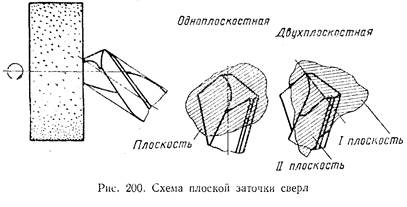
(ось шпинделя смещена относительно оси втулки, и последняя полу-
чает независимое вращение) и возвратно-поступательное переме-
щение вдоль оси, которое осуществляется посредством кулака.
Дополнительное вращение шлифовального круга обеспечивает пе-
ремещение его рабочей поверхности по режущей кромке сверла.
Таким образом, все относительные перемещения шлифовального
круга и сверла так связаны между собой, что в результате полу-
чается заточка задних поверхностей сверла по винтовой поверх-
ности.
Такой метод заточки позволяет получить более резкое увели-
чение заднего угла (на 25%) к центру сверла и имеет преимущества
перед более распространенной заточкой по первому и второму спо-
собам.
Плоская заточка (рис. 200) используется для мелких
сверл диаметром до 3 мм и реже для сверл больших диаметров. В по-
следнем случае необходимо иметь так называемую двухплоскостную
заточку, обеспечивающую необходимые задние углы для режущей
кромки и образование второго затылка на нерабочей части пера,
устраняющего затирание задней поверхности.