IV ПРОЦЕССА РЕЗАНИЯ МЕТАЛЛОВ
Металл, срезанный с заготовки режущим инструментом, назы-
вается стружкой.
Процесс резания (стружкообразования) является одним из
сложных физических процессов, при котором имеют место упругие
и пластические деформации; этот процесс сопровождается большим
трением, тепловыделением, наростообразованием, завиванием и
усадкой стружки, упрочнением и износом режущего инструмента.
Вскрыть физическую сущность процесса резания и установить при-
чины и закономерности явлений, которыми он сопровождается —
основная задача науки о резании металлов. Правильное и полное
решение этой задачи дает возможность рационально управлять про-
цессом резания и делать его более производительным, качественным
и экономичным.
ПРОЦЕСС СТРУЖКООБРАЗОВАНИЯ И ТИПЫ СТРУЖЕК
Под действием режущего инструмента срезаемый слой подвер-
гается сжатию. Процесс сжатия, как и процесс растяжения, соп-
ровождается упругими и пластическими деформациями.
Из диаграммы растяжения мягкой
стали (рис. 25) видно, что вначале
(до точки а) растягиваемый образец
имеет упругие (обратимые) деформа-
ции, затем наступает текучесть метал-
ла (участок ас), после чего происхо-
дят пластические (необратимые) де-
формации, заканчивающиеся разру-
шением (разрывом).
Пластическое деформирование за-
ключается в сдвиге одних слоев отно-
сительно других по так называемым
плоскостям скольжения, которые сов-
падают в,основном с направлением наибольших сдвигающих на-
пряжений. Такие сдвиги имеют место как между отдельными ча-
стицами кристаллического зерна (монокристалла, рис. 26), так и
между самими зернами в поликристалле1; в результате сдвигов
изменяется форма зерен, их размер и взаимное расположение.
Процесс пластического деформирования сопровождается большим
тепловыделением и изменением свойств металла; одним из таких
изменений является упрочнение металла (повышение твердости,
а следовательно, и хрупкости).
'При сжатии картина будет аналогична описанной, только
вместо удлинения образца произойдет его укорочение. Процесс
сжатия при резании отличается от обычного сжатия образца, за-
ключенного между двумя сближающимися поверхностями, тем, что
срезаемый слой связан с остальной массой заготовки; поэтому, если
обычное сжатие образца может быть названо свободным сжатием, то
1 Линии сдвига (линии Чернова) легко наблюдаются на отполированном цилинд-
рическом образце, подвергаемом растяжению или сжатию.
36
37
сжатие срезаемого слоя при резании можпо назвать несвободным
сжатием.
Исследования, проведенные акад. В. Д. Кузнецовым [13] и д-ром
техн. наук проф. В. А. Кривоуховым [14, 15], показали, что основ-
ные закономерности свободного сжатия имеют место и при несво-
бодном сжатии и что процесс стружкообразования представляет собой
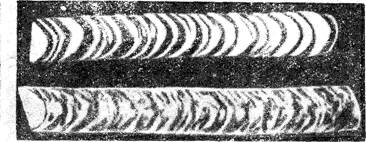
Рис. 26. Сдвиги в монокристалле олова при растяжении
(по П. А. Ребиндеру и В. И. Лихтману).
процесс упруго-пластического деформирования (сжатия) срезаемого
слоя.
В зависимости от условий обработки срезанный слой (стружка)
может быть различных видов.
При обработке пластичных металлов (сталей) имеют место три
основных типа стружек: элементная, ступенчатая и сливная (рис. 27, а,
б — в), а при обработке малопластичных металлов — стружка над-
лома (рис. 27, г).
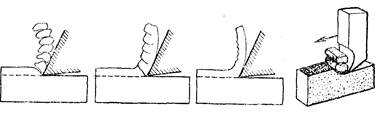
* ' 6) 8> п
Рис. 27, Типы стружек:
а — элементная; 6 — ступенчатая; в — сливная; г — сгружка надлома
Э л е м е н т и а я с т р у ж к а получается при обработке твердых
и маловязких металлов с малой скоростью резания. Она состоит
из отдельных пластически деформированных элементов, слабо связан-
ных или вовсе не связанных между собой. Образование таких эле-
ментов стружки было наглядно показано еще И. А. Тиме, положившим
начало научному исследованию процесса стружкообразования (1868—
1870 гг.).
На рис. 28 дана схема образования элементной стружки при
свободном резании. Под влиянием силы Р2, приложенной к рез-
цу, последний постепенно вдавливается в массу металла, сжима-
ет его своей передней поверхностью и вызывает сначала упругие,
а затем пластические де-
формации.
По мере углубления
резца растут напряжения
в срезаемом слое, и ко-
гда они достигнут вели-
чины прочности данно-
го металла, произойдет
сдвиг (скалывание) пер-
вого элемента по плоско-
сти сдвига АВ, состав-
ляющей с направлением
перемещения резца (с
обработанной поверх-
ностью) угол . Угол
называется углом
сдвига (скалывания).
После скалывания
первого элемента струж-
ки резец своей передней
поверхностью сжимает
(деформирует) следую-
щий близлежащий слой
металла, в результате че-
го образуется второй
элемент, отделяющийся
от основной массы ме-
талла по плоскости мак-
симальных касательных
напряжений под тем же углом ; и т. д. В своих опытах И. А. Ти-
ме установил, что в зависимости от угла резания б угол А =
= (180° — ) = 145 ¸ 155° (чем большеd, тем больше ).
Наблюдая за потускнением тщательно отполированных боко-
вых поверхностей свинцовых пластинок И. А. Тиме первый устано-
вил, что срезаемый слой подвергается пластическому деформиро-
ванию.
Позднее (1892—1893 гг.) проф. К. А. Зворыки и опреде-
лил положение плоскости скалывания теоретическим путем,
подтвердив данные И. А Тиме (по Зворыкину угол = 135 ¸157°).
Последние работы советских исследователей показали, что в
38
39
широком диапазоне положительных и отрицательных значений перед-
него угла резца угол Д имеет несколько большую величину (135—170°)
[16] и что по всей ширине среза угол сдвига не является величиной
постоянной [17]. Поэтому плоскость сдвига правильнее называть
поверхностью сдвига.
Используя киносъемку, проф. В. А. Кривоухов получил отчет-
ливую картину образования элементной стружки при малой ско-
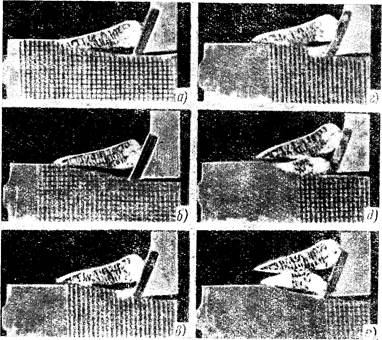
Рис. 29. Образование элементной стружки (по В. А, Кривоухову).
роста резания (0,625 мм/мин) стали 45 (рис. 29). На рис. 29, а
один из элементов хотя и образован, но еще окончательно от
основной массы металла не отделен. На рис. 29, б этот элемент
отделился и резец при своем движении продолжает деформацию
и образование следующего элемента (рис. 29, в, г и д), причем
поверхностная часть слоя, превращаемого во второй элемент,
уже подверглась пластическому деформированию на некоторую
глубину при образовании предыдущего элемента, о чем го-
ворит искривление предварительно нанесенной сетки. На рис.
29, д видно, что перед отделением элемента по поверхности сдви-
га сначала, вследствие концентрации напряжения, появляется опе-
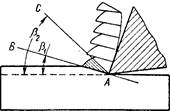
|
режающая трещина1, которая, распространяясь кверху, переходит
в поверхность сдвига. Окончательно отделенный второй элемент
(рис. 29, е) располагается под первым. Искажение сетки, нанесен-
ной предварительно на боковую поверхность пластинки, показы-
вает, что оба элемента по всему их объему подверглись пласти-
ческой деформации. Искажение
сетки вблизи поверхности сдвига
показывает, что пластической де-
формации подверглись и эти слои
металла.
Применив впервые к исследова-
нию процесса резания металлогра-
фический метод (1912—1914 гг.),
Я. Г. Усачев показал, что микро-
структура стружки отлична ОТ МЙК- Рис. 30. Схема образования струж-
роструктурЫ ОСНОВНОЙ массы обра- ки (по Я. Г. Усачеву).
батываемого металла и что в самой
стружке имеются плоскости скольжения АС (рис. 30), не совпа-
дающие по направлению с поверхностью сдвига АВ. Обнаружен-
ные Я. Г. Усачевым плоскости скольжения представляют собой
плоскости, в которых происходят относительные сдвиги частиц ме-
талла при его пластическом деформировании (сжатии), перед тем
как элемент стружки отделится от основной массы металла по
поверхности сдвига. Эти плоскости скольжения являются вынуж-
денным направлением относительных сдвигов частиц металла при
образовании стружки, что приводит зерна металла к сильной де-
формации.
На рис. 31 дана микрофотография стальной стружки, на кото-
рой видно, что по сравнению с зернами основной массы металла зерна
стружки сильно деформированы (вытянуты) в направлении плоско-
стей скольжения под углом .
Ступенчатая стружка (см. рис. 27, б) получается при
обработке сталей со средней скоростью резания. Прирезцовая сто-
рона такой стружки гладкая, а противоположная сторона имеет
зазубрины с выраженным направлением отдельных прочно связан-
ных между собой элементов.
Сливная стружка (см. рис. 27, в) получается при обработ-
ке сталей с высокой скоростью резания. Она сходит с резца в виде
ленты, без зазубрин, присущих ступенчатой стружке.
Процесс образования сливной стружки может быть представлен
в следующем виде. Под действием силы Р, приложенной к резцу,
в обрабатываемой заготовке в зоне oecbdo (рис. 32) создается на-
1 Опережающая трещина, образующаяся во время деформации очередного
элемента и переходящая затем в поверхность сдвига этого элемента, имеет место
в основном при обработке малопластичных металлов (и особенно при больших 6 и а
И малых v).
40
41
пряженное состояние, а следовательно, происходит пластическое де-
формирование.
Каждая частица металла, попадая в граничную зону oecb, на-
чинает пластически деформироваться. На рис. 32 это показано схе-
матически в виде вытянутых зерен. По мере перехода от границы
oecb к границе ой пластическое деформирование (сдвиг) частиц ме-
талла возрастает [18]. На границе od, т.е. в поверхности наиболь-
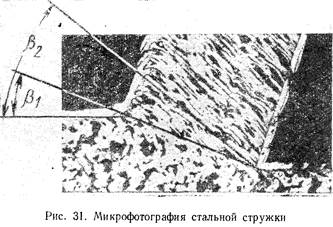
ших сдвигов, происходит последний сдвиг элементов малой тол-
щины относительно друг друга в направлении под углом 2 и
переход срезаемого слоя толщиной а в сливную стружку толщиной
а1. Поверхность сдвига, направленная под углом , является в
этом случае верхней границей зоны, непрерывно подвергающейся
пластическому деформированию от воздействия резца. При эле-
ментной же и ступенчатой стружке эта поверхность была поверх-
ностью, по которой происходило разрушение (скалывание) среза-
емого слоя на отдельные элементы.
Чем больше скорость резания, меньше угол резания, тверже
обрабатываемый металл, больше толщина среза и выше маслянис-
тость смазывающе-охлаждающей жидкости, тем больше угол .
Пластическое деформирование при резании происходит не только
в зоне oecbdo. Стружка, особенно ее прирезцовые слои толщиной
а2,, подвергается дополнительной пластической деформации от дей-
ствия сил трения во время скольжения стружки по передней по-
верхности резца. В результате этой деформации зерна металла
у прирезцовой стороны стружки располагаются в направлении, па-
раллельном передней поверхности резца. Толщина а 2составляет
2—20% толщины стружки.
Дополнительной деформации, вследствие упругого последейст-
вия обработанной поверхности и большого ее трения о заднюю по-
верхность резца, подвергаются и слои, расположенные близко к
обработанной поверхности (толщина а3, см. рис. 32).
Принимая во внимание, что срезанная стружка пластически дефор-
мирована по всей ее толщине и что пластическая деформация распро-
страняется также в глубину от обработанной поверхности и от поверх-
ности резания, общую зону распространения пластической деформации
при стружкообразовании можно очертить границей b с ef (см. рис. 32) 1.
Кроме указанных типов
стружек, при обработке ста-
лей могут образовываться и
промежуточные стружки. Чем
больше скорость резания и
вязкость обрабатываемого ме-
талла, меньше угол резания и
толщина среза и выше каче-
ство смазывающе-охлаждаю-
щей жидкости, тем стружка
ближе к сливной.
Еще И. А. Тиме в своих ра-
ботах указывал на перемен- Рис. 32. Схема пластически сдеформиро-
ность силы, действующей на резец ванной зоны при резании
резец со стороны срезаемого
слоя. Наименьшее значение при элементной стружке будет в начале
деформации при образовании первого элемента. По мере про-
движения резца и увеличения деформации элемента сила резания
будет возрастать, достигнет своего наибольшего значения в мо-
мент скалывания элемента, а затем уменьшится до некоторого
значения, но не упадет до нуля, так как деформация второго эле-
мента стружки начинается несколько раньше, чем заканчивается
скалывание первого элемента. Такое колебание силы резания вы-
зывает неравномерную нагрузку на резец, заготовку и все части
станка, что при недостаточной жесткости может привести к виб-
рациям и ухудшению качества обработанной поверхности. При
ступенчатой стружке изменение силы резания будет меньшим, чем
при элементной, и работа будет протекать более спокойно. Еще
меньшее изменение силы резания будет при сливной стружке, что,
наряду с более равномерной нагрузкой на систему СПИД, будет спо-
собствовать получению и менее шероховатой обработанной поверх-
ности.
Таким образом, по типу стружки можно судить о качественной
стороне протекания процесса резания. Получение сливной стружки
вместо стружки скалывания и ступенчатой во многом подтверждает
правильность назначенных геометрических элементов режущей части
резца и элементов режимов резания.
1 Н а рис. 32 дан пример свободного резания (строгания), когда поверхность
резания и обработанная поверхность совпадают.
42
43
Стружка надлома (см. рис. 27, г) получается при обработке
малопластичных металлов (твердого чугуна, твердой бронзы).
Стружка состоит из отдельных как бы выломанных элементов, раз-
нообразных по форме и не связанных или очень слабо связанных
между собой. Опережающая трещина при образовании стружки
надлома распространяется сразу вдоль всей поверхности сдвига, по
которой стружка отделяется от основной массы металла. «Сыпучая»
стружка надлома пластически
мало деформирована, но она
создает резко неравномерную
нагрузку на всю систему СПИД
(станок — приспособление — ин-
струмент— деталь). Обработан-
ная поверхность при такой
стружке получается шерохова-
той, с большими впадинами и
выступами. Будучи слабо свя-
занными между собой, элемен-
ты стружки надлома имеют
малое относительное перемеще-
ние по передней поверхности
резца.
В определенных условиях,
при обработке чугунов средней
твердости, стружка ' надлома
может получиться в виде ко-
лец (рис. 33), несколько напоминая сливную стружку. Но сход-
ство со сливной стружкой здесь только внешнее. Доста-
точно слегка сжать такую стружку в руке, как она легко
разрушается на отдельные элементы, свойственные стружке над-
лома.
При соприкосновении резца с деформируемой частью металла
вследствие большого давления резца и вызванного этим давлением
пластического деформирования близлежащих к передней поверхно-
сти слоев, а также вследствие наличия микронеровностей на перед-
ней поверхности резца между ними (т. е. между резцом и деформиро-
ванным слоем) происходит зацепление. Это зацепление создает на
передней поверхности резца тонкий заторможенный слой А (рис. 34).
Чем грубее обработана передняя поверхность резца, тем больше тол-
щина заторможенного слоя, относительно которого начнет течь пласти-
чески деформированный по всей толщине среза и уходящий в стружку
металл. Торможению тонкого слоя металла в зоне деформации содей-
ствует и молекулярное сцепление (прилипание) поверхностей контакта
стружки и резца.
При перемещении стружки силы внутреннего трения, действую-
щие в слоях перехода от тонкого заторможенного слоя к основной
массе стружки, производят дополнительные деформации в этих слоях,
направление сдвигов которых совпадает с направлением передней
поверхности резца 1.
В заторможенном слое, который деформирован больше слоев
стружки, соприкасающихся с ним, сдвиги происходят со значительно
меньшими скоростями, а потому наличие заторможенного слоя, рас-
положенного у самой режущей кромки, создает такие условия, при
которых наибольшее относительное скольжение
стружки по передней поверхности резца, а сле-
довательно, и трение, вызванное этим скольже-
нием, будет протекать на некотором расстоянии
от режущей кромки. Этим и объясняется, что
несмотря на наибольшее давление у самой ре-
жущей кромки, износ резца по передней поверх-
ности (в виде лунки) начинается на некотором
расстоянии от режущей кромки (рис. 95). Центр
лунки износа принято называть центром
давления стружки на резец.
Из изложенного следует, что наряду с нор-
мальным давлением, которое испытывает пе-
редняя поверхность резца при деформации
(сжатии) срезаемого слоя, она подвергается также воздействию и сил
трения, имеющих место в поверхностях контакта сходящей стружки
с передней поверхностью резца. Очевидно, чем меньше будет коэффи-
циент трения между поверхностями скольжения, тем меньше будут
силы трения и деформации струж-
ки, а также и общее давление на
резец.
1 При рассмотрении дополнительной деформации стружки на стр. 42 понятие «заторможенный слой» было опущено и для простоты рассуждений рассматривалось трение только о переднюю поверхность резца (внешнее трение).
|
Еще Я. Г. Усачев показал, что
деформациям подвергается не только
срезаемый слой, но и слои основной
массы металла, от которых произво-
дится отделение стружки, т. е. по-
верхность резания и обработанная
поверхность (глубина пластической
деформации поверхностного слоя а3
показана на рис. 32). Эти деформа-
ции, особенно упругие, создают вы-
пучивание металла Нуп (рис. 35),
которое вызывает давление металла на задние поверхности инстру-
мента, а так как последние имеют перемещение относительно поверх-
ности резания и обработанной поверхности, то наряду с нормальным
давлением на задние поверхности инструмента будут действовать еще
и силы трения.
44
45
Таким образом, резец, вклинившись под действием приложенной
к нему силы в обрабатываемый металл, находится в тесном контакте
с деформируемыми им слоями, которые (при обработке сталей и отсут-
ствии опережающей трещины) как бы обтекают его режущую кромку,
переднюю и заднюю поверхности и создают действующие на инстру-
мент нормальные давления и силы трения Т и Т1 (рис. 35). Нормаль-
ные давления на переднюю и заднюю поверхности распределяются
неравномерно (см. рис. 35): наибольшие нормальные давления нахо-
дятся у вершины резца (вблизи плоскости резания).
Возникающие при резании и остающиеся в поверхностных слоях обработанной
поверхности остаточные напряжения (сжатия или растяжения) оказывают влияние
на износостойкость и усталостную прочность детали.
Исследования, проведенные по резанию конструкционных сталей, показывают
[19, 20], что при точении обычными резцами ( > 0) остаточные напряжения
растяжения возрастают при увеличении подачи s, глубины резания t, радиуса
закругления r при вершине резца в плане и радиуса округления р режущей
кромки.
•Влияние скорости резания на остаточные напряжения более сложно. При реза-
нии сталей с увеличением скорости срезания остаточные напряжения растяжения
уменьшаются и, начиная с некоторой скорости (150—500 м/мин), переходят в оста-
точные напряжения сжатия (50—60 кГ/мм2).
При изменении переднего угла от 0 до —300,остаточные напряжения растяжения
переходят в остаточные напряжения сжатия.
Отжиг обрабатываемого металла снимает остаточные напряжения.
§ 2. РАБОТА, ЗАТРАЧИВАЕМАЯ НА РЕЗАНИЕ
Представляя процесс резания как процесс упруго-пластического
сжатия и принимая во внимание силы трения, действующие на поверх-
ностях режущего инструмента, общую работу Л, затрачиваемую на
резание, можно выразить как сумму, состоящую из следующих соста-
вляющих этой работы:

где Ау — работа, затрачиваемая на упругие деформации;
Апл — работа, затрачиваемая на пластические деформации;
Amp . п. п — работа, затрачиваемая на преодоление трения по перед-
ней поверхности;
Amp . 3. п — работа, затрачиваемая на преодоление трения по задней
поверхности.
При обработке пластичных металлов Ау незначительна, а
потому наибольшими составляющими работы в этом случае будут Л„.„
Amp . п. п И Amp . 3. п
При обработке м а л о и л а с т и ч н ы х металлов (например,
чугунов) А,и будет мала, и основными составляющими работы будут
Ау,Аш,,, „. „иЛ„ф. з. „, причем вследствие относительно Малого сколь-
жения стружки надлома по передней поверхности инструмента работа
Ащр. а. а будет значительно меньше, чем работа Amp . 3. п.
46
НАРОСТ ПРИ РЕЗАНИИ МЕТАЛЛОВ
При некоторых условиях резания на передней поверхности резца,
у его режущей кромки, образуется так называемый нарост (рис. 36).
Он имеет клиновидную форму и представляет собой часть обрабаты-
ваемого металла, сильно cдеформированного, заторможенного и часто
прилипшего (приваренного) к резцу. Твердость нароста может быть
в 2—3 раза больше твердости обрабатываемого металла, и нарост сам
может срезать слой металла. Являясь как бы продолжением резца,
нарост изменяет его геометрию (угол резания при наросте меньше
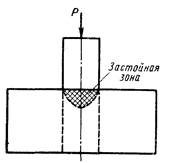
Рис. 36. Схема нароста на резце: Рис. 37. Застойная зона перед
а — устойчивый нарост; б — разрушение нароста nyaнсоном
угла резания резца б, полученного при заточке), а потому, перемещаясь
вместе с резцом, нарост оказывает влияние на деформацию срезаемого
слоя, на износ резца, на силы, действующие на резец, и на качество
обработанной поверхности. Поэтому явлению наростообразования при
резании уделяется большое внимание.
Впервые правильное объяснение нароста как «застойной зоны»
сильно деформированного металла перед передней поверхностью резца
дал Я. Г. Усачев. Все последние исследования по этому вопросу, веду-
щая роль в которых принадлежит советским ученым, полностью
подтверждают это положение.
Застойная зона всегда обнаруживается под пуансоном при его вдавливании
в твердое тело (рис. 37). Резец представляет собой тот же пуансон, но условия работы
его иные: деформируемый слой имеет свободный сход по передней поверхности резца
и на эту поверхность несимметрично распределено давление. Отличной поэтому будет
и форма застойной зоны, образующейся в результате деформации металла при ре-
зании.
На рис. 38, а дана микроструктура всего нароста (застойной зоны), а на
рис. 38, б — микроструктура его вершины (с увеличением в 250 раз). Из рис. 38, а
следует, что тело нароста имеет несимметричную, клинообразную форму, что вер-
шина нароста округлена, но не имеет ярко выраженной границы отделения от основ-
ной массы металла, так как именно здесь происходит последовательный переход
исходной структуры обрабатываемого металла в структуру нароста; по своей струк-
туре нарост неоднороден и отличен от структуры обрабатываемого металла и стружки.
47
Нарост не является стабильным и одинаковым по размерам вдоль
всей длины режущей кромки даже при условиях, особенно благоприят-
ных для его образования. Вследствие сильного трения между стружкой
и наростом и трения в месте контакта нароста с обработанной поверх-
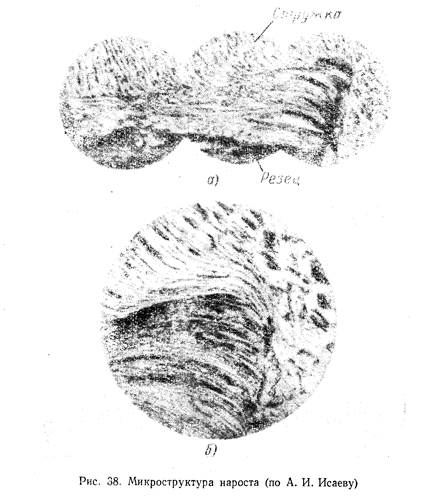
ностыо и поверхностью резания частицы нароста уносятся стружкой
и этими поверхностями (см. рис. 36, б); нарост при этом, разрушаясь
частично или полностью, периодически восстанавливается за счет
новых частиц металла из основной его массы. Подвергаясь воздействию
сил в направлении движения стружки и обработанной поверхности,
ати частицы сначала растягиваются, а затем по мере их углубления
в тело нароста, сильно сжимаются, что и приводит к большому упро-
чнению нароста.
Так как нарост уменьшает угол резания резца (что способствует
более легкому отделению стружки), защищает режущую кромку от
истирающего действия со стороны сходящей стружки и со стороны об-
работанной поверхности, удаляет от режущей кромки центр давления
стружки на резец и несколько защищает режущую кромку от воздей-
ствия теплоты, возникающей при резании, то при грубой (черновой)
обработке нарост не считается особенно
вредным.
При чистовой же обработке, когда
необходимо получить высокое качество
обработанной поверхности, нарост не-
желателен. Если бы нарост отсутство-
вал, то резец образовывал бы относи-
тельно мало шероховатую обработанную
поверхность I (пунктирная линия на
рис. 36, соответствующая глубине реза-
ния t 1). Более шероховатой была бы
обработанная поверхность, если бы на-
рост был абсолютно устойчивым (поверх-
ность //, соответствующая глубине ре-
зания t 2), так как вследствие округления и неровностей вершины
нароста, а также больших сил трения по его затылочной поверхности
обработанная поверхность имела бы большие разрывы, происхо-
дившие в момент отделения обработанной поверхности от нароста.
Но так как нарост разрушается и вновь образуется, то действительная
толщина среза и глубина резания 1 все время изменяются (t2 > t 1),
что и приводит к значительно большей действительной высоте неров-
ностей на обработанной поверхности, чем шероховатость на поверх-
ности / или //.
Наряду с ухудшением чистоты обработанной поверхности измене-
ние размеров нароста приводит и к изменению размера обработанной
поверхности по диаметру.
Исследования показывают, что при малых скоростях резания
(2—5 м/мин) вследствие элементной стружки и низкой температуры,
возникающей при резании, нарост на резце отсутствует (рис. 39). По
мере увеличения скорости резания стружка из элементной переходит
в ступейчатую и сливную; наблюдается течение пластически деформи-
руемых слоев, и температура резания такова, что образующаяся зона
застоя не только упрочняется и затормаживается на передней по-
верхности резца, но и приваривается к ней. Скорость резания, соот-
ветствующая наибольшей высоте нароста, находится в пределах
10—20 м/мин. При дальнейшем увеличении скорости резания
1 Периодическое изменение толщины среза и глубины резания может привести
К вибрациям, что также ухудшает качество обработанной поверхности.
48
49
температура становится выше, застойная зона, размягчаясь, умень-
шается, переходя в тонкий, заторможенный, но не приваренный
слой.
Величины скорости резания, при которой нарост имеет наиболь-
шую высоту и скорости, начиная с которой нарост на резце будет
отсутствовать, зависят от условий обработки. По данным проф.
А. М. Розенберга и д-ра техн. наук А. Н. Еремина [221 чем выше твер-
дость обрабатываемой стали, боль-
ше угол резания резца и больше
толщина среза (т. е. чем выше
температура резания при одина-
ковых скоростях резания), тем
при меньших скоростях исчезает
нарост.
Наивысшей скоростью реза-
ния (в зависимости от условий
обработки), при которой нарост
еще может иметь место, является
скорость 90—100 м/мин. При об-
работке твердых сталей нарост
может исчезнуть при скорости
20 м/мин.
Скорость резания
Рис. 40. Влияние скорости резания па угол резания, создаваемый наро- стом, усадку стружки, силу резания и коэффициент трения (по А. М. Розеп- бергу и Л. Н. Еремину)
|
Изменение высоты нароста при-
водит к изменению угла резания
создаваемого наростом (рис. 40,
верхняя кривая).
Так как основанием нароста
являются топкие заторможенные
слои деформируемого металла, то
все факторы, содействующие умень-
шению трения на передней поверхности резца, будут затруднять и
условия для наростообразования. Чем меньше шероховатость перед-
ней поверхности резца, тем хуже условия для наростообразования.
Снижает наростообразование также применение смазывающе-охлаж-
дающих жидкостей и уменьшение угла резания (при угле резания
d == 45° нарост совершенно отсутствует). Меньшую склонность к наро-
стообразованию имеет инструмент, оснащенный пластинками твердого
сплава (по сравнению с инструментом из сталей).
Мы рассмотрели нарост как застойную зону, приваренную к резцу.
Однако в зависимости от давления, температуры в месте контакта за-
стойной зоны с резцом и от способности к свариванию контактирую-
щихся металлов застойная зона может привариться и к стружке.
Встречаются случаи, кагда застойная зона не приваривается ни к резцу,
ни к стружке, но может быть обнаружена при отводе резца из-под
стружки.
При прерывистом резании (строгании, фрезеровании) нарост хотя
и образуется на резце, но периодически отпадает, так как процесс ре-
зания в этих случаях сопровождается резко переменной (ударной)
нагрузкой на инструмент. Реже обнаруживается нарост на резце и
при обработке чугунов, когда образуется стружка надлома и имеет
место пульсирующе-ударная нагрузка на режущую кромку.
§ 4. ЗАВИВАНИЕ СТРУЖКИ, УСАДКА
СТРУЖКИ И УПРОЧНЕНИЕ
Наглядным доказательством наличия пластических деформаций
при резании металлов является завивание стружки, ее усадка и упроч-
нение (повышение твердости). Последнее имеет место как в стружке,
так и на поверхности резания и
на обработанной поверхности (на
некоторой глубине).
Завивание стружки.
Завивание стружки в спираль
вызывается тем, что слои струж-
ки, прилегающие к резцу, деформи-
руются. На рис. 41 видно, что со
стороны действия силы Р слои по-
лучают утолщение, приобретают
клинообразную форму, в результате
чего и создается кривизна (завива- рис. 41- Схема завивания стружки
ние). Завивание вызывается и тем,
что, встречаясь с резцом, особенно при наличии нароста, стружка
в некоторой точке а (см. рис. 36, а) вынуждена резко изменить напра-
вление движения и изогнуться. Завиванию содействует также и нерав-
номерное охлаждение стружки по толщине; стружка сильнее охлаж-
дается (а следовательно, и сжимается) в наружных слоях, так как
в прирезцовых слоях действует тепло от трения о переднюю поверх-
ность резца.
В зависимости от условий обработки стружка может завиться
в плоскую (логарифмическую) или в винтовую спираль. Стружка
в виде плоской спирали образуется при отрезании (см. рис. 24, а)
и свободном поперечном точении буртика резцом, у которого главный
угол в плане = 90°, а угол наклона главной режущей кромки = 0
(см. рис. 20, б). Если же при точении буртика резец будет иметь ¹90°,
или угол ¹ 0, стружка будет завиваться в винтовую спираль.
Завивание стружки в винтовую спираль происходит и при несвобод-
ном точении, что вызывается в основном различной скоростью схода
отдельных точек стружки, уменьшающейся вдоль ширины среза, при
переходе от обрабатываемой поверхности к обработанной (vD > vD 0,
см. рис. 120, а).
На завивание стружки оказывают влияние следующие основные
факторы: угол резания, толщина среза (подача), глубина лунки на
передней поверхности резца, скорость резания и смазывающе-охлаж-
дающая жидкость.
50
51
Исследования показывают, что чем больше угол резания и меньше
толщина среза, тем больше завивается стружка (т. е. тем меньше ее
радиус кривизны). С увеличением глубины лунки износа на перед-
ней поверхности резца радиус завивания стружки уменьшается
(рис. 42, а), а с увеличением скорости резания увеличивается
(рис. 42,6).
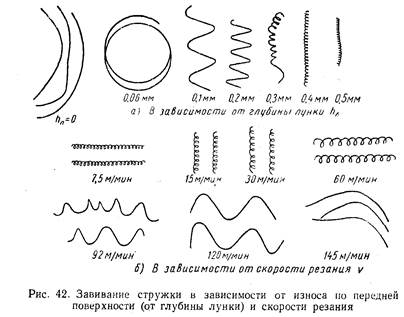
Усадка стружки.-В результате пластического сжатия сре-
заемого слоя стружка оказывается короче того участка, с которого
она срезана, т. е. L< L 0 (рис. 43).
Укорочение стружки по длине принято называть продоль-
ной усадкой стружки; величина ее характеризуется коэф-
фициентом усадки.
Коэффициент усадки k представляет собой отношение длины
участка, с которого срезана стружка, к длине самой стружки, т. е.

Так как L < L 0, то коэффициент
усадки k > 1, и в зависимости от
условий обработки он может дохо-
дить до 6—8.,
Если пренебречь изменением
плотности металла в процессе ре-
зания, то (объем срезаемого слоя
(среза) можно приравнять к объе-
му уже срезанного слоя (стружки),
а потому укорачивание стружки по длине должно сопровождаться
увеличением ее площади поперечного сечения. Это увеличение пло-
щади поперечного сечения стружки принято называть попереч-
ной усадкой стружки, и оно (увеличение) происходит в
большей степени за счет увеличения толщины стружки и в мень-
шей — за счет увеличения ее ширины.
Приравнивая объем срезаемого слоя к объему стружки и пре-
небрегая величиной площади остаточных гребешков, можно за-
писать
Д-е = /А

Применение смазывающе-охлаждающих жидкостей способствует
уменьшению радиуса завивания стружки.