Скорость резания — величина перемещения точки режу-
щей кромки относительно поверхности резания в единицу времени
в процессе осуществления главного движения 1.
При токарной обработке, когда обрабатываемая заготовка
диаметром D мм (диаметр обработанной поверхности D 0 мм, см.
рис. 16) вращается с некоторым числом оборотов п в минуту, ско-
рость резания в точках режущей кромки МК будет величиной пе-
ременной. Однако в расчетах скорости резания принимается ее
максимальное значение, определяемое по формуле
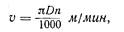
где D — наибольший диаметр поверхности резания в мм.
Из приведенной формулы легко определить число оборотов
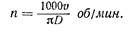
1 При более строгом определении скорость резания — функция окружной скорости вращения заготовки и скорости перемещения резца (продольной по- дачи) [12J
|
При продольном точении скорость резания имеет постоянную
величину на протяжении всего времени резания (если диаметр за-
готовки вдоль всей ее длины одинаков, а число оборотов неизмен-
но). При подрезке
же торца, когда резец
перемещается от перифе-
рии заготовки к центру
или, наоборот, от центра
к периферии, скорость
резания при постоянном
числе оборотов перемен-
на. Она имеет наиболь-
шее значение у перифе-
рии и равна нулю в цент-
ре (рис. 17). Однако и в
этом случае в расчет
принимается максималь-
ная скорость резания,
соответствующая диа-
метру D.
При растачивании (см. рис. 13) скорость резания также рассчиты-
вается по наибольшему диаметру поверхности резания (в данном слу-
чае — по диаметру обработанной поверхности).
Подача (точнее, скорость подачи) — величина перемещения
режущей кромки относительно обработанной поверхности в еди-
ницу времени (или величину, ей эквивалентную) в направлении движе-
ния подачи.
При токарной обработке различают продольную подачу,
когда резец перемещается в направлении, параллельном оси заго-
товки (см. рис. 16); п о п е р е ч ну ю подачу, когда резец переме-
щается в направлении, перпендикулярном к оси заготовки (см. рис. 17),
и наклонную — под углом к оси заготовки (например, при обта-
чивании конической поверхности).
Различают минутную подачу, т. е. величину относительного
перемещения резца за 1 мин, и подачу за один оборот заго-
товки, т. е. величину относительного перемещения резца за время
одного оборота заготовки (из положения / резец переместился в по-
ложение //, рис. 16). Минутная подача обозначается sM в мм!мин,
а подача за один оборот — s в мм/об. Между ними существует сле-
дующая зависимость: 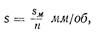
где п — число оборотов заготовки в минуту.
Г л у б и н а резания — величина срезаемого слоя за один
проход, измеренная в направлении, перпендикулярном к обработан-
ной поверхности (см. рис. 16). Глубина резания всегда перпенди-
кулярна направлению движения подачи, и при наружном продоль-
ном течении она представляет собой полуразность между диаметром
заготовки и диаметром обработанной поверхности, полученной после
одного прохода:

При растачивании глубина резания определяется как полураз-
ность между диаметром отверстия после обработки и диаметром от-
верстия до обработки (см. рис. 13).
При подрезке (см. рис. 17) за глубину резания принимается вели-
чина срезаемого слоя, измеренная в направлении, перпендикуляр-
ном к обработанному торцу (к обработанной поверхности); при отре-
зании (см. рис. 14) глубина резания равна ширине отрезного резца
(ширине канавки).
§ 2. ШИРИНА, ТОЛЩИНА И ПЛОЩАДЬ
ПОПЕРЕЧНОГО СЕЧЕНИЯ СРЕЗА
Ширина среза b — расстояние между обрабатываемой и
обработанной поверхностями, измеренное вдоль режущей кромки
(рис. 18).
28
29
Тол щ ина среза (7- расстояние между двумя последова-
тельными положениями поверхности резания, измеренное в направ-
лении, перпендикулярном к режущей кромке в плоскости передней
поверхности резца.
Рассмотрим зависимость между толщиной среза а и подачей s,
между шириной среза b и глубиной резания / при s < t (см.
рис. 18).
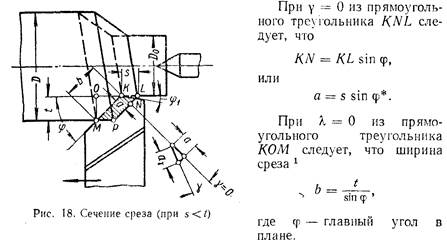
Из приведенных формул видно, что при постоянных подаче s и
глубине резания t с увеличением главного угла в плане <р толщина
среза увеличивается, а ширина уменьшается. На рис. 19 графичес-
ки показано изменение толщины и ширины среза при увеличении
главного угла в плане от 30 до 90°. При ср = 90° толщина среза а
равна подаче s, а ширина среза Ь равна глубине резания t. Это же
следует и из формул.
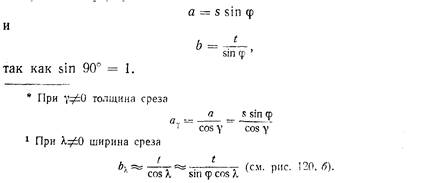
При обычных подсчетах толщины и ширины среза влияние углов и можно
не учитывать; при проведении исследовательских работ, когда это может влиять
на точность измерений или подсчетов, поправку на углы и необходимо принимать
во внимание.
Глубина резания и подача характеризуют процесс резания в ос-
новном с технологической (производственной) его стороны.
Толщина и ширина среза более полно, чем глубина резания и
подача, характеризуют и объясняют физическую сторону процесса
резания. В зависимости от соотношения между подачей и глубиной
резания принято называть срез п р я ы ы м, когда s < t, квадрат-
н ы м, когда s = t, и о б р а т н ы м, когда s > t.
Площадь поперечного сечения среза PLKM
(см. рис. 18)
f = ab = ts мм 2.
Вследствие увеличенной толщины (и немного ширины) стружки
площадь поперечного сечения стружки (срезанного слоя) будет
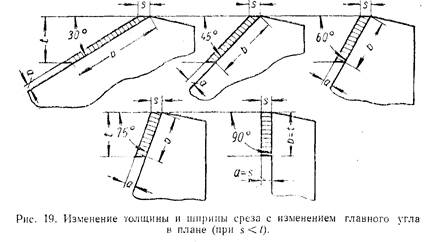
больше площади поперечного сечения среза (см. стр. 53). Площадь
поперечного сечения среза f = а b ммг представляет собой площадь
номинального или расчетного сече и и я. Однако номиналь-
ное сечение получается только при свободном резании (когда в ра-
боте принимает участие лишь главная режущая кромка, рис. 20, а и б),
или в случае, когда резец имеет площадку со вспомогательным уг-
лом в плане = 0 и длина площадки больше подачи. В этих
случаях резец будет снимать весь предназначенный для среза-
ния слой, не оставляя на обработанной поверхности остаточных
гребешков.
1 При так называемом несвободном резании наряду с главной режущей
кромкой u b в работе принимает участие и вспомогательная режущая кромка
be (рис. 20, а).
При несвободном резании (рис. 20, в) на обработанной поверх-
ности остаются гребешки, размеры которых зависят от подачи,
радиуса закругления при вершине резца и главного и вспомога-
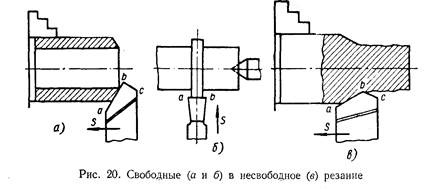
тельного углов в плане. Это хорошо показано на рис. 21, где за
один оборот заготовки резец переместился на величину подачи s и
из положения / перешел в положение //, оставив на обработанной
поверхности гребешок высо-
той H.
Если обозначить действи-
тельное сечение среза через f 0
площадь остаточных гребеш-
ков через f 2 то

Высота остаточных гребеш-
ков во многом определяет ве-
личину шероховатостей (мик-
рогеометрию) обработанной
поверхности: чем меньше вы-
сота Н, тем выше чистота (см.
стр. 63) обработанной поверх-
ности (меньше шероховатость).
Объем стружки, снятой за 1 мин работы, может быть вы-
числен по формуле
Q = vts см3/мин.
ШТУЧНОЕ И МАШИННОЕ ВРЕМЯ
Время на проведение определенной операции над одной заго-
товкой Тш складывается из следующих элементов:

где Тшт — штучное время в мин;
Т0 — основное (технологическое) время-в мин;
Тв — вспомогательное время в мин;
Т0бс — время на обслуживание рабочего места в мин;
Тотд — время перерывов на отдых и личные надобности в мин.
Основное (технологическое) время — это время, в
течение которого происходит процесс снятия стружки. При работе
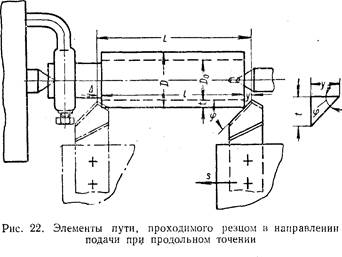
на станке основное (технологическое) время может быть машинным
и машинно-ручным.
Машинное время — время, в течение которого происхо-
дит процесс снятия стружки без непосредственного участия рабо-
чего (например, время на обтачивание валика на токарном станке
при включенной механической подаче). В дальнейшем это время
будем обозначать через Тм.
При токарной обработке машинное время за один проход
может быть подсчитано по формуле

где L — величина пути инструмента в направлении подачи в мм;
п -— число оборотов заготовки (шпинделя) в минуту;
s — подача в мм/об.
В свою очередь (рис. 22)

32
В. А. Аршинов 33
где /— размер обработанной поверхности в направлении подачи
в мм;
у — величина врезания в мм;
— выход режущего инструмента (перебег) в мм; =
= 1¸2 мм.
Величина врезания у определяется из прямоугольного треуголь-
ника (рис. 22, справа):
у — tc tg .мм,
При поперечном точении валика (рис. 23, а)

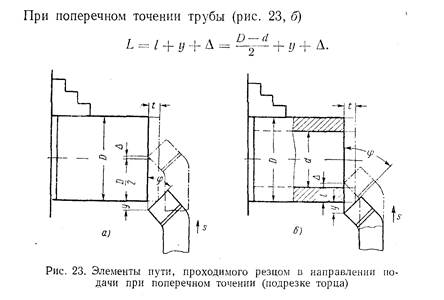
Как и при продольном обтачивании, при поперечном точении
отогнутым резцом

При отрезке (разрезке) валика отрезным резцом с режущей
кромкой, параллельной оси (см. рис. 24, а)

При работе резцом с наклонной режущей кромкой (рис. 24, б)

34
При отрезке (разрезке) трубы резцом с режущей кромкой, па-
раллельной оси (рис. 24, s),

а резцом с наклонной режущей кромкой

Если при обработке заготовки приходится делать несколько про-
ходов при условии, что все они совершаются с одинаковым числом
оборотов и подачей, то машинное время

где i — число проходов.
Количество проходов зависит от припуска1 на обработку, и ес-
ли предположить, что каждый проход совершается с одинаковой

глубиной резания (в практике последний проход, точнее переход,
производится с меньшей глубиной, чем предыдущие), то

где h — припуск на обработку на сторону в мм;
t — глубина резания в мм.
Подставив в формулу машинного времени выражение для чис-
ла проходов, получим
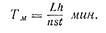
1 Под припуском подразумевается слой металла, который необходимо срезать
с заданной заготовки.
35
Машинное время при работе на универсально-токарных стан-
ках составляет 35—50% штучного. Уменьшение машинного време-
ни — важный фактор в повышении производительности труда.
Из формулы видно, что Тм можно уменьшить, с одной стороны,
за счет уменьшения L и h, с другой, за счет увеличения t, s, n (v).
Величина L зависит от размера обработанной поверхности
(размера готовой детали), и при одноинструментной обработке
уменьшение L может иметь место лишь за счет уменьшения вели-
чины врезания и величины выхода режущего инструмента. Боль-
шое влияние на уменьшение L достигается многоинструментной
обработкой, когда применяются, например, одновременно два рез-
ца; длина L в этом случае разбивается на два участка размером
Чем меньше припуск на обработку h, т. е. чем ближе заготов-
ка по своей форме и размерам к форме и размерам детали, тем
меньше металла будет переведено в стружку, тем более благопри-
ятны условия для срезания припуска за один проход, тем меньше,
следовательно, будет затрачено времени на получение готовой детали
и ниже ее себестоимость.
На увеличение же основных элементов режима резания —
глубины, подачи и скорости (числа оборотов) влияет ряд факторов,
которые изучаются в курсе «Резание металлов и режущий инструмент»
и будут рассмотрены ниже.
Машинно-ручное время — это время, в течение которого на станке
происходит процесс снятия стружки с непосредственным участием рабочего (напри-
мер, время на подрезку торца валика на токарном станке с ручной подачей).
Вспомогательное время — это время на установку, закрепление
и снятие заготовки и готовой детали; на пуск и остановку станка; на изменение
чисел оборотов станка и величины подачи; на установку и подвод к заготовке режу-
щего инструмента; время на промер заготовки и готовой детали и т. д.
Время на обслуживание рабочего места — время на уход
за рабочим местом при выполнении данной работы. Сюда входит время на подна-
ладку и регулирование станка в процессе работы; время на правку инструмента,
на его смену вследствие затупления и на его раскладку и уборку в начале и в конце
смены; время на чистку и смазку станка.
Время перерывов на личные надобности рабочего преду-
сматривается для всех видов работ. При выполнении физически тяжелых и утоми-
тельных работ предусматривается еще время и на отдых. Время на естественные на-
добности и отдых, как и время на обслуживание рабочего места, дается в процент-
ном отношении от основного и вспомогательного времени.