И ПОДАЧАМИ И ОСНОВНЫЕ УСЛОВИЯ ЕЕ ОСУЩЕСТВЛЕНИЯ
Машинное время может быть уменьшено за счет увеличения подачи
или числа оборотов (скорости резания). Сокращение машинного
времени вследствие значительного повышения подачи принято назы-
126
вать силовым резанием, вследствие повышения скорости реза-
ния — скоростным резанием.
В отношении стойкости режущего инструмента (т. е. времени
работы инструмента до определенной величины износа) выгоднее
увеличивать подачу, так как увеличение подачи оказывает меньшее
влияние на нагрев, а следовательно, и на износ режущего инстру-
мента, чем увеличение скорости резания (см. стр. 96).
Но увеличение подачи имеет определенные пределы, так как при
этом: 1) увеличиваются силы, действующие на систему СПИД, что
приводит к повышению термодинамической нагрузки, приходящейся
на единицу длины режущей кромки инструмента; при недостаточной
прочности режущей кромки увеличение сил может вызвать ее разру-
шение и преждевременный вывод инструмента из строя; увеличенные
силы могут вызвать искажение формы обработанной поверхности
(овальность, эллиптичность, выпуклость и др.) и способствовать повы-
шенному износу всех деталей системы; 2) ухудшается чистота (микро-
геометрия) обработанной поверхности, а потому начиная с некоторой
величины подачи обработанная поверхность не будет отвечать техни-
ческим условиям на нее; 3) увеличиваются степень и глубина упроч-
нения обработанной поверхности, что не всегда целесообразно.
Поэтому уменьшить машинное время после установления макси-
мально допустимой подачи можно повышением числа оборотов (ско-
рости резания).
Увеличение скорости резания (начиная примерно с v» 50 м/мин),
в отличие от увеличения подачи, приводит к уменьшению сил, воз-
никающих при резании (см. рис. 80), к улучшению чистоты (микро-
геометрии) обработанной поверхности (см. рис. 57) и к уменьшению
упрочнения.
Но высокие скорости резания увеличивают путь трения (износа)
за одинаковое время и резко повышают тепловыделение и температуру
нагрева поверхностей контакта резца с заготовкой и стружкой, что
снижает твердость материала резца, а следовательно, повышает его
износ за одно и то же время работы (т. е. вызывает снижение стойкости
резца). Поэтому для работы на высоких скоростях резания необхо-
димо иметь инструмент, режущая часть которого сделана из достаточно
износотеплостойкого материала, например, твердого сплава или
керамики.
Но режущий инструмент должен обладать также и достаточной
прочностью режущей кромки. Твердые сплавы и керамические мате-
риалы, обладая высокой твердостью и теплоизносостойкостью, в то
же время очень хрупки и плохо выносят ударную нагрузку, нагрузку
на изгиб и срез. Поэтому для упрочнения режущей кромки у этих
резцов принимают иногда отрицательные передние углы (см. рис. 115,
б — д).
При чистовой (s = 0,1 мм/об, t = 0,5 мм) обработке углеродистых
сталей резцом с пластинкой твердого сплава скорости резания дости-
гают 2600 м/мин и выше; при чистовой обработке чугунов резцом,
127
оснащенным керамической пластинкой — 3780 м/мин, при обработке
алюминиевых сплавов — 5000 м/мин и выше.
Резание металлов инструментом, оснащенным пластинками твер-
дого сплава, с увеличенной (максимально возможной по условиям
работы) скоростью наряду с повышением производительности обес-
печивает 8—9-й класс чистоты обработанной поверхности (ГОСТ
2789—59), позволяет обрабатывать закаленные стали, уменьшает
удельный расход мощности, затрачиваемой на резание и снижает
себестоимость обработки.
Такие преимущества скоростного резания металлов привели к его
широкому распространению не только при точении, но и при фрезеро-
вании, сверлении, зенкеровании, развертывании, резьбонарезании и
других видах обработки. Все шире оно применяется и при работе
на многорезцовых станках, автоматах и полуавтоматах. На скорост-
ные режимы обработки переводят не только отдельные участки и
пролеты, но и цехи.
Скоростное резание металлов впервые получило развитие в СССР;
еще в 1936—1937 гг. советские исследователи и инженеры впервые
в мировой практике провели научные исследования скоростного реза-
ния металлов, включая и скоростную обработку закаленных сталей.
Важную роль в успешном освоении и внедрении высокопроизво-
дительного резания металла сыграла наша металлургическая про-
мышленность, разработавшая высококачественные твердые сплавы.
Значительный вклад в развитие и внедрение высокопроизводи-
тельного резания металлов внесли советские новаторы производства.
Такие прославленные мастера скоростного резания, как Г. С. Борт-
кевич, П. Б. Быков, А. П. Марков, Н. В. Угольков, В. К. Семинский,
Н. Н. Симоновский, А. Н. Гончаров, И. Г. Белов, Ю. Диков, С. М. Бу- '
шуев, Е. Ф. Савич, В. И. Жиров и др., не только успешно применяют
и широко внедряют высокие элементы режима резания, но и являются
авторами ряда усовершенствований, способствующих дальнейшему
развитию высокопроизводительного резания металлов. Большая роль
в осуществлении силового резания металлов принадлежит токарю-
новатору В. А. Колесову.
Резание металлов с повышенными режимами вызывает, соответст-
венно, повышенные требования к станку, инструменту, приспособле-
ниям и вопросам техники безопасности.
Требования, предъявляемые к станку. Станок для резания метал-
лов на высоких скоростях должен быть достаточно мощным, жестким
(виброустойчивым), высокоскоростным, долговечным, безопасным для
работы и должен обеспечивать возможность уменьшения не только
машинного (за счет увеличения п и s), но и вспомогательного времени.
Последнее требование вызывается тем, что наиболее полный эффект
от скоростных элементов режима резания может быть получен только
тогда, когда наряду с уменьшением машинного времени будет умень-
шаться и вспомогательное время, которое в мелкосерийном произ-
водстве может достигать 40—80% штучного времени.
128
Станок для скоростного резания должен иметь также хорошую
смазку, надежное и быстрое закрепление заготовки, инструмента и
приспособлений, хорошо отбалансированные вращающиеся детали;
станок должен быть правильно установлен на фундаменте (лучше на
отдельном для каждого станка во избежание вибраций, могущих
возникнуть от воздействия рядом работающего станка).
Резание металлов на высоких скоростях с успехом можно осуще-
ствлять не только на новых, специально построенных для этого стан-
ках, но и на станках старых конструкций и моделей после их модер-
низации.
Требования, предъявляемые к инструменту. Инструмент для
высокопроизводительного резания должен быть достаточно прочным,
жестким, иметь оптимальную геометрию, высокое качество заточки,
быть технологичным в изготовлении и удобным в эксплуатации.
Большое внимание должно уделяться качеству заточки1, так как
зачастую только неправильная заточка и доводка режущего инстру-
мента снижают его производительность и весь эффект от скоростных
режимов резания. Наиболее целесообразной является централизо-
ванная заточка и доводка режущего инструмента (при высокой степени
механизации этих процессов), так как наряду с более высоким каче-
ством централизованная заточка освобождает рабочего (станочника)
от вспомогательных операций.
Требования, предъявляемые к приспособлениям. Приспособления
для высокопроизводительного резания металлов должны быть жест-
кими, мощными, быстродействующими, надежными и удобными.
Применяемые приспособления должны способствовать снижению вспо-
могательного времени и обеспечивать получение высококачественных
обработанных поверхностей. Широкое распространение находят экс-
центриковые, гидравлические и пневматические зажимные устройства,
а также устройства для автоматического получения размеров (упоры,
автоматические остановы, лимбы и приборы-счетчики, фиксирующие
величину продольного и поперечного перемещения инструмента,
приборы для автоматического контроля и регулирования размеров
в процессе обработки, и др.).
Повышению точности обработки содействует применение патро-
нов и оправок с гидропластом2 и резиной, применение жестких и
износостойких люнетов и центров. Патроны должны быть хорошо
отбалансированы и во избежание разрыва при высокой скорости
должны иметь стальной корпус, а во избежание самоотвинчивания
при торможении — дополнительное крепление. При скоростном точе-
нии обычно применяют вращающийся центр (задний), причем наилуч-
шей конструкцией (особенно при тяжелых работах) является такая,
1 См. стр. 472, а также работы [48, 49].
2 В приспособлениях с гидропластом для передачи давления применяют пласти-
ческие вещества, смесь сала с парафином, гидропласт Д (резиноподобная масса
с воздушными включениями следующего состава: 78% днбутилфталата, 20% поли-
хлорвиниловой смолы ПБ-2, 2% сгеарата кальция).
129
когда вращающийся центр встроен непосредственно в. пиноль задней
бабки.
Для уменьшения времени и облегчения условий труда при уста-
новке и снятии крупных приспособлений необходимо использовать
подъемные механизмы (электротельферы, кошки и др.); при установке
инструмента рекомендуется применять шаблоны и мерные подкладки.
Техника безопасности при скоростной обработке. При скоростной
обработке за короткие промежутки времени образуется большое
количество сильно разогретой стружки, поэтому вопросы техники
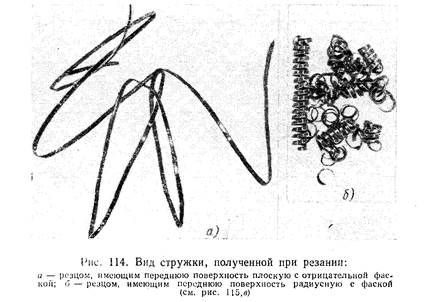
безопасности имеют большое значение. При точении стали стружка
может сходить в виде ленты (рис. 114, а), наматываться на заготовку
и отдельные части станка, мешая нормальному проведению процесса
резания; такая стружка представляет большую опасность для рабочего
и неудобна для транспортировки. При точении чугуна и бронзы
стружка разлетается веером на далекое расстояние от станка,
угрожая, не только работающему на данном станке, но и окру-
жающим.
Для защиты от чугунной и бронзовой стружки применяют резцы
с отсасывающим устройством, специальные ограждения (кожухи и
экраны) и индивидуальные средства защиты (очки, козырьки). Для
удобства наблюдения за работой в ограждениях' предусматривается
смотровое окно, в которое вставляется высокопрочное стекло.
Во избежание получения длинной, неудобной и опасной стальной
стружки применяются так называемыестружколоматели-стружкозавп-
ватели1, с помощью которых стружка превращается в спираль не-
большого радиуса и ломается на небольшие куски (рис. 114, б).
Для безопасной работы на повышенных режимах резания необхо-
димо иметь неподвижный упор, ограничивающий конечное положение
суппорта и исключающий, например, возможность удара кулачков
патрона о суппорт или резец.
Каждый рабочий должен строго выполнять все пункты инструкции
по технике безопасности.