XXV II ДЛЯ АВТОМАТИЗИРОВАННОГО
ПРОИЗВОДСТВА 1
Производительность автоматической линии или автоматическо-
го станка зависит в значительной степени от применяемого режу-
щего инструмента. Последний должен удовлетворять не только
обычным условиям, предъявляемым к режущему инструменту,
как-то: обеспечению чистоты и точности обрабатываемых деталей,
необходимой стойкости и прочности, экономичности, — но также
и специфическим условиям, обусловленным автоматическим обо-
1 Подробно см. Р ы в к и и Г. М. и Эстерзон М. Л. Пути повышения режи-
мов работы автоматических линий. — «Станки и инструмент», 1959, Л"° 10.
Рывки н Г. М. Высокопроизводительная инструментальная оснастка для
автоматического производства. —«Станки и инструмент», 1961, № 2.
рудованием. К таким условиям относится обеспечение размерной
стойкости инструмента, стабильность его работы, быстросменность
и взаимозаменяемость.
Указанные условия, обеспечивающие непрерывность процесса
обработки и влияющие на производительность и эффективность
работы автоматизированного производства, зависят в большей
мере от конструкции режущего инструмента.
Для обеспечения наибольшей непрерывности работы режущего
инструмента в условиях автоматизированного производства необ-
ходимо в первую очередь исключить потери времени, складываю-
щиеся из времени, необходимого на установку и закрепление ин-
струмента; на настройку инструмента для получения требуемых
размеров обрабатываемой детали как в начале, так и в процессе
работы инструмента до момента снятия его на переточку; на сня-
тие изношенного инструмента.
Учитывая специфику работы в условиях автоматизированного
производства и стремясь сократить потери времени, конструкторы
за последние годы разработали большое количество разнообраз-
ных конструкций, в которых нашли отражение следующие идеи:
а) применение взаимозаменяемого инструмента, настраиваемого
на размер, что исключает потери времени на первоначальную на-
ладку; б) использование сил резания для частичного или полного
крепления инструмента, что упрощает конструкции механизма
крепления инструмента, обеспечивая более высокую точность
установки и, главное, сокращение времени на установку, закреп-
ление; открепление и снятие режущей части или самого инстру-
мента; в) встройка узлов автоматической подналадки и регули-
рования инструмента для компенсации систематических погреш-
ностей размеров детали, что обеспечивает повышение размерной стой-
кости инструмента и сокращает тем самым указанные выше потери
времени; г) использование принципа обновления режущих участков
одной и той же кромки (прерывное или непрерывное), обновления рез-
цов (зубьев) и, наконец, самих режущих инструментов; последнее
выполняют магазинные загрузочные устройства, из которых инстру-
мент попадает в рабочее положение.
Наряду с указанными проблемами для автоматических линий боль-
шое значение имеет формирование и отвод стружки в условиях работы
автоматического станка. В этом направлении также найдены решения,
обеспечивающие нормальный стружкоотвод.
Ниже приводятся отдельные конструкции инструментов для автома-
тических линий с указанием их особенностей.
На автоматических линиях, и особенно для обработки тел враще-
ния, широко применяются резцы, оснащенные пластинками твердого
сплава. На рис. 363, а показана рекомендуемая ВНИИ типовая конст-
рукция резца 1 с механическим креплением многогранной твердосплав-
ной пластинки 2. Резец закрепляется на станке с помощью клиновид-
ного сухаря 4, зажатого винтом 5.
432
433
Винт 3 служит для регулирования положения резца, а каждый резец
снабжен винтом 6, который позволяет настраивать длину L вне станка,
на специальном приспособлении. Настройка резца вне станка позво-
ляет уменьшить время, потребное на смену инструмента.
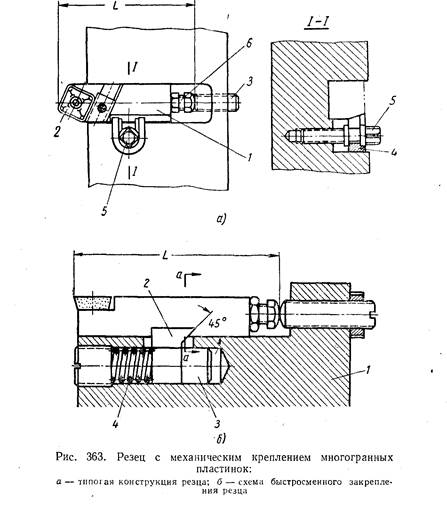
На рис. 363, б показана схема быстросменного закрепления резцов.
При этом используется принцип окончательного закрепления инстру-
мента с помощью сил, возникающих в процессе резания. Пружина 4
в данном случае служиттолько для незначительного прижима тягой 3
с крючком 2, входящим в паз державки 1. Регулирование длины резца L
производится отдельно вне станка.
Основное отличие сверл, зенкеров, разверток, цековок и другого,
так называемого осевого инструмента, применяемого на автоматических
линиях, от обычного инструмента заключается, как правило, в конст-
рукции хвостовика.
На рис. 364 показаны примеры конструкций хвостовика.Кониче-
ский хвостовик имеет лыску для дополнительного зажима с помощью
винта (рис. 364, а). Часто применяемые конструкции цилиндрических
хвостовиков служат для быстрого закрепления инструмента (рис.
364, б). Регулировочный винт позво-
ляет обеспечить настройку на длину
L вне станка.
Для регулирования размеров
длины инструментов в рабочем по-
ложении применяют переднюю
резьбовую часть с регулировочной
гайкой и контргайкой (рис. 364, б).
На агрегатных станках и в авто-
матических линиях находят широ-
кое применение сверла спиральные
стандартной конструкции. Часто
при обработке корпусных деталей в
линии требуется совместить в одну
операцию сверление отверстия и
снятие фаски или сверление отвер-
стия двух ступеней под головку
болта. Для этой цели применяются
ступенчатые сверла двух видов: пе-
реточенные из стандартных и спе-
циальные четырехленточные свер-
ла. Применяются также ружейные
сверла (см. рис. 197) для сверления
глубоких отверстий и сверла с от-
верстиями для подвода охлаждающей жидкости (см. стр. 237). Для
обработки ступенчатых отверстий, выточек торцовых поверхностей
широко применяются комбинированные инструменты.
Целесообразность применения сложного комбинированного инстру-
мента в каждом отдельном случае должна быть проверена экономиче-
ским расчетом.
Для нарезания резьбы на автоматических линиях применяются
метчики, резьбонарезные и резьбонакатные головки, для фрезерных
операций — различные фрезы (торцовые, цилиндрические, концевые,
дисковые и т. д.; см. гл. XIX).
Наибольшее применение на автоматических линиях обработки кор-
пусных деталей получили торцовые фрезы сборных конструкций с
ножами, оснащенными твердым сплавом. Рекомендуется снабжать тор-
цовые фрезы одним широким зачистным ножом, выступающим па
небольшую величину (0,02—0,04 мм) по отношению к другим ножам,
434
435
что позволяет при больших минутных подачах получить высокую
чистоту поверхности.
Концевые фрезы для удобства смены и настройки изготовляются
с цилиндрическим хвостовиком, показанным на рис. 364, б, и настраи-
ваются вне станка на нужный размер.
Протяжки находят применение на автоматических линиях для обра-
ботки как корпусных деталей, так и тел вращения. С целью повышения
размерной стойкости начинают применять протяжки, оснащенные
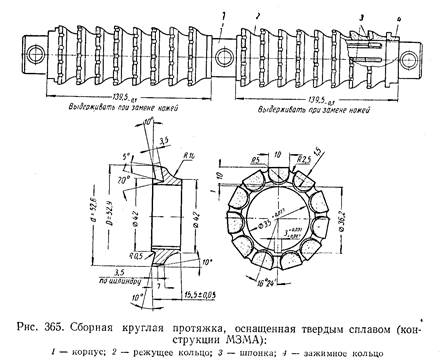
жены в полость шпинделя и в магазин. После обработки определенного
количества деталей шпиндельная бабка 1 отходит назад по стрелке А;
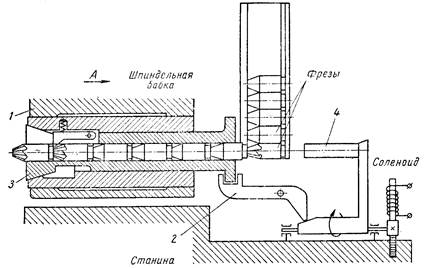
Рис. 366. Схема магазина для автоматической замены концевого инструмента
вначале рычагом 2 разжимается цанга 3, а затем, при дальнейшем дви-
жении, посредством штыря 4, подведенного копирным устройством,
изношенная фреза выталкивается и заменяется новой.
М ЕТОДЫ ПОВЫШЕНИЯ СТОЙКОСТИ
И ОБЩЕГО СРОКА СЛУЖБЫ
И НСТРУМЕНТОВ
твердым сплавом. Например, на заводе малолитражных автомобилей
для полуотверстий крышек коренных подшипников применяются
сборные круглые протяжки (рис. 365), состоящие из ряда колец, стя-
нутых общим стержнем.
При проектировании инструмента для автоматических станков или
линий следует использовать все возможности для увеличения размер-
ной стойкости за счет применения твердых сплавов или быстрорежущих
сталей повышенного качества. Однако не всегда удается найти доста-
точно приемлемое решение. Тогда используется принцип обновления
(замена режущих кромок, зубьев или самих инструментов).
На рис. 366 показана схема магазина конструкции ВНИИ для авто-
матической замены концевых зубозакругляющих фрез. Фрезы зало-
Изготовленный из правильно подобранного инструментального
материала режущий инструмент может иметь высокую или низкую
стойкость, так как высокие режущие свойства инструмента обеспечи-
вают не только важнейший фактор — материал, но также оптимальную
геометрию и правильно проведенную технологию обработки инстру-
мента (термическую обработку, шлифование, заточку и т. д.) и условия
эксплуатации инструмента.
После правильно проведенной термической обработки режущая
кромка инструмента приобретает необходимую, характерную для дан-
ного инструментального материала твердость и износостойкость.
Существует ряд методов, позволяющих повысить стойкость режу-
щей части инструмента (при прочих равных условиях) за счет ироведе-
436
437
ния дополнительных операций. К таким методам относятся: а) методы
насыщения поверхностного слоя инструмента (цианирование, хромиро-
вание, сульфидирование); б) методы повышения стойкости за счет улуч-
шения структуры при термической обработке (обработка холодом,
обработка паром); в) методы повышения качества поверхности инстру-
мента (доводка, притирка).
Цианирование — химико-термический процесс, который заклю-
чается в насыщении поверхностного слоя стали углеродом и азотом
путем диффузии при определенной температуре. В зависимости от
метода насыщения в промышленности различают цианирование в жид-
ких средах, газовое цианирование и сухое цианирование с твердым
карбюризатором. В зависимости от температуры цианирование разде-
ляется на высокотемпературное (в диапазоне 800—850° С) и низкотем-
пературное (в диапазоне 550—560° С).
В производстве инструментов из быстрорежущей стали применяется
только низкотемпературное цианирование полностью обработанных
инструментов, так как, если термически обработанный и заточенный
инструмент подвергать цианированию при температурах выше обычных
температур отпуска, будет понижена твердость, что приведет не к повы-
шению стойкости, а к резкому снижению ее.
Широкое применение на заводах имеет жидкое цианирование инст-
румента из быстрорежущей стали при температуре 550—560° С. Про-
цесс насыщения стали углеродом и азотом производится в ваннах (тиг-
лях), наполненных расплавленной солью (обычно цианистый натрий
NaCH).
В процессе работы идут химические реакции окисления:
2NaCN + О2 = 2NaCNO,
далее образовавшийся цианид NaCNO реагирует с кислородом воздуха:
2NaCNO + 02 = Na3C03 + СО + N2.
Окись углерода СО реагирует с железом, входящим в состав быст-
рорежущей стали, образуя карбид железа:
2СО + 3Fe = Fe3C + CO2.
Выделяющийся атомарный азот также реагирует с железом и леги-
рующими элементами, образуя нитриды.
Карбиды железа и нитриды повышают твердость до HRC 68—70
и износостойкость поверхности режущей части инструмента. Время
выдержки в цианистых ваннах зависит от размера и конструкции инст-
румента и колеблется в пределах 5—30 мин.
Цианированный быстрорежущий инструмент имеет повышенную
стойкость до 2—3 раз. Повышение стойкости — результат как повы-
шенной твердости поверхностного слоя, так и пониженного коэффици-
ента трения при резании, что уменьшает износ и повышает красностой-
кость инструмента.
Рекомендуется цианирование с глубиной слоя 0,01—0,03 мм, так
как при больших слоях режущая кромка инструмента получается
хрупкой. Жидкому низкотемпературному цианированию подвергают
протяжки, сверла, резьбовой инструмент и некоторые другие виды
инструмента из быстрорежущей стали.
Сульфидирование — процесс насыщения поверхностных слоев
металла серой. Образовавшиеся на поверхности инструмента сернистые
соединения снижают коэффициент трения и повышают износостой-
кость инструмента. Процесс производится при температуре 550—560° С
в ваннах следующего состава: 39% хлористого кальция; 25% хлорис-
того бария и 17% хлористого натрия; с добавлением сернистых соеди-
нений: 13,7% сернистого железа (в порошке); 3,4% сернокислого
калия и 3,4 % желтой кровяной соли.
Выдержка от 40 до 90 мин. По данным некоторых исследований
сульфидированный инструмент имеет стойкость в 1,5—2 раза выше.
Хромирование — в производстве инструмента главным образом
электролитическое в гальванических ваннах с толщиной слоя до
0,025 мм. Хромированию можно подвергать готовые инструменты из
различных сталей — быстрорежущей, легированной или углеродистой.
Применяется хромирование долбяков, протяжек и некоторых других
инструментов.
Обработка в атмосфере водяного пара. Процесс обработки паром
быстрорежущих инструментов заключается в предварительной про-
мывке инструмента при температуре около 70° С следующим составом
на литр раствора: от 20 до 40 г соды Na2C03, от 20 до 40 г каустической
соды NaOH и от 20 до 40 г трипатрийфосфата Na3P04; затем промытый
горячей водой инструмент загружается в электропечь с герметическим
затвором (можно использовать печи для отпуска инструмента). Сна-
чала температура медленно поднимается до 340—380° С и выдержива-
ется в течение 15—30 мин до полного прогрева; затем печь продувается
водяным паром, и при повышенной до 540—560° С температуре инстру-
мент выдерживается до 30—40 мин; затем охлажденный до 50—70° С
инструмент опускают в подогретое минеральное масло. После обработки
паром и погружения в масло на инструменте образуется тонкая (0,05 м м)
черная пленка окислов, а так как процесс происходит по существу
при температуре дополнительного отпуска для.быстрорежущей стали,
то инструмент получает повышенную среднюю стойкость (конечно,
если он был правильно закален). В процессе обработки паром не
может быть исправлена плохая термическая обработка инструмента.
Повышение стойкости до 2 раз и некоторая стабилизация показа-
телей стойкости вследствие улучшения условий отвода и уменьшения
налипания стружки, например, на ленточках сверл, обеспечили внед-
рение этого процесса в промышленность.
Обработка холодом. Как один из процессов улучшения структуры
инструмента из быстрорежущей стали применялся процесс дополни-
тельной обработки инструмента холодом. Однако сложность оборудо-
вания для ведения процесса обработки холодом при температурах
до 80° С ниже нуля (холодильные установки) привела к тому, что этот
процесс не применяется.
438
439
Процесс обработки холодом по сравнению с правильно проведенным
процессом термической обработки инструмента особых преимуществ
не дает, но может улучшить структуру материала инструмента за счет
более полного распада остаточного аустенита.
Доводка. Для повышения стойкости режущие кромки следует дово-
дить. По данным исследователей заточка и доводка режущих кромок,
особенно алмазными кругами, позволяет повысить среднюю стойкость
ряда инструментов, особенно чистовых, в 2—3 раза и более, так как
улучшает качество поверхности инструмента, а следовательно,и усло-
вия работы режущей части инструмента.
Методы восстановления режущего инструмента. Окончательно изно-
шенный инструмент, например зенкер, развертка, резец и т. д., можно
восстановить. Методы восстановления сборного и цельного инстру-
мента различны. Возможность восстановления заложена в конструк-
циях сборных инструментов. Например, корпуса сборных фрез, раз-
верток, зенкеров и т. д. могут служить очень долго и выдерживают
многократную смену изношенных ножей. Во многих случаях эта воз-
можность легкого восстановления и обеспечивает целесообразность
выбора сборной конструкции инструмента. В отдельных конструкциях
сборного инструмента вопрос замены ножей решается по-разному.
В настоящее время, особенно в конструкциях резцов и фрез, преду-
сматривается применение неперетачиваемых многогранных пластинок.
Такой инструмент восстанавливается очень просто. Когда износились
все режущие кромки пластинки, она снимается и заменяется новой.
Державка служит до тех пор, пока можно на ней закреплять пластинку.
Восстановление инструмента цельной конструкции, а также инст-
румента с напаянными пластинками значительно сложнее и не всегда
оправдывается экономически,
Основными путями при восстановлении цельного инструмента явля-
ются.
1. Перешлифовка инструмента на ближайший размер с соответст-
вующим углублением стружечных канавок. Подобным путем могут
восстанавливаться такие инструменты, как зенкеры, развертки, боль-
шинство видов цельных фрез.
При восстановлении методом шлифования отверстие насадных инст-
рументов остается в первоначальном виде, но может также хромиро-
ваться в размер.
2. Ряд инструментов можно восстановить путем отжига изношен-
ного инструмента с последующей полной механической обработкой
на новый размер. Отверстие насадного инструмента после отжига или
растачивается на другой размер, или в него вставляется втулка. Из
поломанных быстрорежущих фрез могут быть изготовлены пластинки
для напайки на резцы и т. д.
Восстановление инструмента следует производить только тогда,
когда это оправдывается экономически.

Раздел ШЛИФОВАНИЕ
XI