Введение в САПР
Обзор
Современные предприятия не смогут выжить во всемирной конкуренции, если не будут выпускать новые продукты лучшего качества (quality, Q), более низкой стоимости (cost, С) и за меньшее время (delivery, D). Поэтому они стремятся использовать огромные возможности памяти компьютеров, их высокое быстродействие и возможности удобного графического интерфейса для того, чтобы автоматизировать и связать друг с другом задачи проектирования и производства, которые раньше были весьма утомительными и совершенно не связанными друг с другом. Таким образом сокращается время и стоимость разработки и выпуска продукта. Для этой цели используются технологии автоматизированного проектирования (computer-aided design — CAD), автоматизированного производства (computer-aided manufacturing — САМ) и автоматизированной разработки или конструирования (computer-aided engineering — CAE). Чтобы понять значение систем CAD/CAM/CAE, мы должны изучить различные задачи и операции, которые приходится решать и выполнять в процессе разработки и производства продукта. Все эти задачи, взятые вместе, называются жизненным циклом продукта (product cycle). Пример жизненного цикла продукта, описанного Зейдом [166], с незначительными усовершенствованиями приведен на рис. 1.1. Прямоугольники, нарисованные сплошными линиями, представляют два главных процесса, составляющих жизненный цикл продукта: процесс разработки и процесс производства. Процесс разработки начинается с запросов потребителей, которые обслуживаются отделом маркетинга, и заканчивается полным описанием продукта, обычно выполняемым в форме рисунка. Процесс производства начинается с технических требований и заканчивается поставкой готовых изделий.
Операции, относящиеся к процессу разработки, можно разделить на аналитические и синтетические. Как следует из рис. 1.1, первичные операции разработки, такие как определение необходимости разработки, формулирование технических требований, анализ осуществимости и сбор важной информации, а также концептуализация разработки, относятся к подпроцессу синтеза. Результатом подпроцесса синтеза является концептуальный проект предполагаемого продукта в форме эскиза или топологического чертежа, отражающего связи различных компонентов продукта. В этой части цикла делаются основные финансовые вложения, необходимые для реализации идеи продукта, а также определяется его функциональность. Большая часть информации, порождаемой и обрабатываемой в рамках подпроцесса синтеза, является качественной, а следовательно, не удобной для компьютерной обработки.

Рис. 1.1. Жизненный цикл продукта
Готовый концептуальный проект анализируется и оптимизируется — это уже
подпроцесс анализа. Прежде всего вырабатывается аналитическая модель, поскольку анализируется именно модель, а не сам проект. Несмотря на быстрый рост количества и качества компьютеров, используемых в конструировании, в обозримом будущем отказаться от использования абстракции аналитической модели мы не сможем. Аналитическая модель получается, если из проекта удалить маловажные детали, редуцировать размерности и учесть имеющуюся симметрию. Редукция размерностей, например, подразумевает замену тонкого листа из какого-либо материала на эквивалентную плоскость с атрибутом толщины или длинного и тонкого участка на линию с определенными параметрами, характеризующими поперечное сечение. Симметричность геометрии тела и нагрузки, приложенной к нему, позволяет рассматривать в модели лишь часть этого тела. Вообще говоря, вам уже приходилось заниматься подобным абстрагированием при анализе структур в курсе основ механики. Вспомните, что вы всегда начинали анализ с построения упрощенного эскиза структуры. Типичные примеры анализа: анализ напряжений, позволяющий проверить прочность конструкции, контроль столкновений, позволяющий обнаружить возможность столкновений движущихся частей, составляющих механизм, а также кинематический анализ, показывающий, что проектируемое устройство будет совершать ожидаемые движения. Качество результатов, которые могут быть получены в результате анализа, непосредственно связано с качеством выбранной аналитической модели, которым оно ограничивается.
После завершения проектирования и выбора оптимальных параметров начинается этап оценки проекта. Для этой цели могут изготавливаться прототипы.
В конструировании прототипов все большую популярность приобретает новая технология, названная быстрым прототипированием (rapidprototyping). Эта технология позволяет конструировать прототип снизу вверх, то есть непосредственно из проекта, поскольку фактически требует только лишь данных о поперечном сечении конструкции. Если оценка проекта на основании прототипа показывает, что проект не удовлетворяет требованиям, описанный выше процесс разработки повторяется снова.
Если же результат оценки проекта оказывается удовлетворительным, начинается подготовка проектной документации. К ней относятся чертежи, отчеты и списки материалов. Чертежи обычно копируются, а копии передаются на производство.
Как видно по рис. 1.1, процесс производства начинается с планирования, которое выполняется на основании полученных на этапе проектирования чертежей, а заканчивается готовым продуктом. Технологическая подготовка производства —
это операция, устанавливающая список технологических процессов по изготовлению продукта и задающая их параметры. Одновременно выбирается оборудование, на котором будут производиться технологические операции, такие как получение детали нужной формы из заготовки. В результате подготовки производства составляются план выпуска, списки материалов и программы для оборудования. На этом же этапе обрабатываются прочие специфические требования, в частности рассматриваются конструкции зажимов и креплений. Подготовка занимает в процессе производства примерно такое же место, как подпроцесс синтеза в процессе проектирования, требуя значительного человеческого опыта и принятия качественных решений. Такая характеристика подразумевает сложность компьютеризации данного этапа. После завершения технологической подготовки начинается выпуск готового продукта и его проверка на соответствие требованиям. Детали, успешно проходящие контроль качества, собираются вместе, проходят тестирование функциональности, упаковываются, маркируются и отгружаются заказчикам.
Выше мы описали типичный жизненный цикл продукта. Посмотрим теперь, каким образом на этапах этого цикла могут быть применены технологии CAD, САМ и САЕ Как уже говорилось, компьютеры не могут широко использоваться в подпроцессе синтеза, поскольку они не обладают способностью хорошо обрабатывать качественную информацию. Однако даже на этом этапе разработчик может, например, при помощи коммерческих баз данных успешно собирать важную для анализа осуществимости информацию, а также пользоваться данными из каталогов.
Непросто представить себе использование компьютера и в процессе концептуализации проекта, потому что компьютер пока еще не стал мощным средством для интеллектуального творчества. На этом этапе компьютер может сделать свой вклад, обеспечивая эффективность создания различных концептуальных проектов. Полезными могут оказаться средства параметрического и геометрического
моделирования, а также макропрограммы в системах автоматизированной разработки чертежей (computer-aided drafting). Все это типичные примеры систем CAD. Система геометрического моделирования (geometric modeling system) — это
трехмерный эквивалент системы автоматизированной разработки чертежей, то
есть программный пакет, работающий с трехмерными, а не с плоскими объектами. О разработке чертежей речь пойдет в главе 4, а о геометрическом моделировании — в главе 5.
В аналитической фазе проектирования ценность компьютеров проявляется по-настоящему. Программных пакетов для анализа напряжений, контроля столкновений и кинематического анализа существует столько, что приводить какие-либо названия смысла не имеет. Эти программные пакеты относятся к средствам автоматизированного конструирования (САЕ). Главная проблема, связанная с
их использованием, заключается в необходимости формирования аналитической
модели. Проблемы не существовало бы новее, если бы аналитическая модель
автоматически выводилась из концептуального проекта. Однако, как уже отмечалось, аналитическая модель не идентична концептуальному проекту — она выводится из него путем исключения несущественных деталей и редукции размерностей. Необходимый уровень абстракции зависит от типа анализа и желаемой точности решения. Следовательно, автоматизировать процесс абстрагирования достаточно сложно, поэтому аналитическую модель часто создают отдельно. Обычно абстрактная модель проекта создается в системе разработки рабочих чертежей или в системе геометрического моделирования, а иногда с помощью встроенных средств аналитического пакета. Аналитические пакеты обычно требуют, чтобы исследуемая структура была представлена в виде объединения связанных сеток, разделяющих объект на отдельные участки, удобные для компьютерной обработки. Если аналитический пакет может генерировать сетку автоматически, человеку остается задать только границы абстрактного объекта. В противном случае сетка также создается пользователем либо в интерактивном режиме, либо автоматически, но в другой программе. Процесс создания сетки называется моделированием методом конечных элементов (finite-element modeling). Моделирование этим методом включает в себя также задание граничных условий и внешних нагрузок.
Подпроцесс анализа может выполняться в цикле оптимизации проекта по каким-либо параметрам. Разработано множество алгоритмов поиска оптимальных решений, а на их основе построены коммерчески доступные программы. Процедура оптимизации может считаться компонентом системы автоматизированного проектирования, но более естественно рассматривать эту процедуру отдельно.
Фаза оценки проекта также выигрывает от использования компьютера. Если для оценки проекта нужен прототип, мы можем быстро сконструировать его по заданному проекту при помощи программных пакетов, генерирующих код для машины быстрого прототипирования. Такие пакеты считаются программами для автоматизированной подготовки производства (САМ). Разумеется, форма прототипа должна быть определена заранее в наборе входных данных. Данные, определяющие форму, получаются в результате геометрического моделирования. Обзор существующих технологий быстрого прототипирования дан в главе 12. Быстрое прототипирование — удобный способ конструирования прототипа, однако еще удобнее пользоваться виртуальным прототипом, который часто называется «цифровой копией» (digital mock-up) и позволяет получить столь же полезные сведения.
Когда аналитические средства для работы с цифровыми копиями станут достаточно мощными, чтобы давать столь же точные результаты, что и эквивалентные эксперименты на реальных прототипах, цифровые копии начнут вытеснение обычных прототипов. Эта тенденция будет усиливаться по мере совершенствования технологий виртуальной реальности, позволяющих нам ощущать цифровую копию так же, как реальный прототип. Построение цифровой копии называется виртуальным прототипированием. Виртуальный прототип может быть создан и в специализированной программе геометрического моделирования. Виртуальное прототипирование подробно рассматривается в главе 13.
Последняя фаза процесса разработки — подготовка проектной документации. На этом этапе чрезвычайно полезным оказывается использование систем подготовки рабочих чертежей. Способность подобных систем работать с файлами позволяет систематизировать хранение и обеспечить удобство поиска документов
Компьютерные технологии используются и на стадии производства. Процесс производства включает в себя планирование выпуска, проектирование и приобретение новых инструментов, заказ материалов, программирование машин с ЧПУ, контроль качества и упаковку. Компьютерные системы, используемые в этих операциях, могут быть классифицированы как системы автоматизированного
производства. Например, программа автоматизированной технологической подготовки (computer-aided process planning — САРР) используется на этапе подготовки производства и относится к системам автоматизированного производства (САМ). Как отмечалось выше, подготовка производства с трудом поддается автоматизации, поэтому полностью автоматических систем технологической подготовки в настоящий момент не существует. Однако существует множество хороших программных пакетов, генерирующих код для станков с числовым программным управлением. Станки этого класса позволяют получить деталь нужной формы по данным, хранящимся в компьютере. Они аналогичны машинам для быстрого прототипирования. Программирование станков с ЧПУ рассматривается в главе 11. К системам автоматизированного производства относят также программные пакеты, управляющие движением роботов при сборке компонентов и перемещении их между операциями, а также пакеты, позволяющие программировать координатно-измерительную машину (coordinate measuring machine — СММ), используемую для проверки продукта.
Итак, вы получили представление о том, каким образом компьютерные технологии используются в операциях, составляющих жизненный цикл продукта, и какие задачи решаются при помощи систем автоматизированного проектирования.
Технологии CAD, САМ и САЕ будут определены в следующем разделе.
Определение CAD, САМ и САЕ
Согласно предыдущему разделу, автоматизированное проектирование (computer-aided design — CAD) представляет собой технологию, состоящую в использовании компьютерных систем для облегчения создания, изменения, анализа
и оптимизации проектов [59]. Таким образом, любая программа, работающая с
компьютерной графикой, так же как и любое приложение, используемое в инженерных расчетах, относится к системам автоматизированного проектирования.
Другими словами, множество средств CAD простирается от геометрических про-
грамм для работы с формами до специализированных приложений для анализа
и оптимизации [166]. Между этими крайностями умещаются программы для
анализа допусков, расчета масс-инерционных свойств, моделирования методом
конечных элементов и визуализации результатов анализа. Самая основная
функция CAD — определение геометрии конструкции (детали механизма, архитектурные элементы, электронные схемы, планы зданий и т. п.), поскольку геометрия определяет все последующие этапы жизненного цикла продукта. Для этой
цели обычно используются системы разработки рабочих чертежей и геометрического моделирования. Вот почему эти системы обычно и считаются системами
автоматизированного проектирования. Более того, геометрия, определенная в
этих системах, может использоваться в качестве основы для дальнейших опера-
ций в системах САЕ и САМ. Это одно из наиболее значительных преимуществ
CAD, позволяющее экономить время и сокращать количество ошибок, связанных с необходимостью определять геометрию конструкции с нуля каждый раз,
когда она требуется в расчетах. Можно, следовательно, утверждать, что системы
автоматизированной разработки рабочих чертежей и системы геометрического
моделирования являются наиболее важными компонентами автоматизированного проектирования.
Автоматизированное производство (computer-aided manufacturing — САМ) — это технология, состоящая в использовании компьютерных систем для планирования, управления и контроля операций производства через прямой или кос-
венный интерфейс с производственными ресурсами предприятия. Одним из
наиболее зрелых подходов к автоматизации производства является числовое
программное управление (ЧПУ, numerical control — NC). ЧПУ заключается в
использовании запрограммированных команд для управления станком, который
может шлифовать, резать, фрезеровать, штамповать, изгибать и иными способа-
ми превращать заготовки в готовые детали. В наше время компьютеры способны
генерировать большие программы для станков с ЧПУ на основании геометрических параметров изделий из базы данных CAD и дополнительных сведений,
предоставляемых оператором. Исследования в этой области концентрируются
на сокращении необходимости вмешательства оператора.
Еще одна важная функция систем автоматизированного производства — программирование роботов, которые могут работать на гибких автоматизированных участках, выбирая и устанавливая инструменты и обрабатываемые детали на станках с ЧПУ. Роботы могут также выполнять свои собственные задачи, например
заниматься сваркой, сборкой и переносом оборудования и деталей по цеху.
Планирование процессов также постепенно автоматизируется. План процессов
может определять последовательность операций по изготовлению устройства от начала и до конца на всем необходимом оборудовании. Хотя полностью автоматизированное планирование процессов, как уже отмечалось, практически невозможно, план обработки конкретной детали вполне может быть сформирован
автоматически, если уже имеются планы обработки аналогичных деталей. Для
этого была разработана технология группировки, позволяющая объединять схожие детали в семейства. Детали считаются подобными, если они имеют общие
производственные особенности (гнезда, пазы, фаски, отверстия и т. д.). Для автоматического обнаружения схожести деталей необходимо, чтобы база данных
CAD содержала сведения о таких особенностях. Эта задача осуществляется при
помощи объектно-ориентированного моделирования или распознавания элементов (глава 5). Технология группировки описывается в главе 10.
Вдобавок, компьютер может использоваться для того, чтобы выявлять необходимость заказа исходных материалов и покупных деталей, а также определять их
количество исходя из графика производства. Называется такая деятельность
планированием технических требований к материалу (material requirements planning — MRP). Компьютер может также использоваться для контроля состояния
станков в цехе и отправки им соответствующих заданий.
Автоматизированное конструирование (computer-aided engineering — CAE) — это технология, состоящая в использовании компьютерных систем для анализа геометрии CAD, моделирования и изучения поведения продукта для усовершенствования и оптимизации его конструкции. Средства САЕ могут осуществлять
множество различных вариантов анализа. Программы для кинематических рас-
четов, например, способны определять траектории движения и скорости звеньев
в механизмах. Программы динамического анализа с большими смещениями могут использоваться для определения нагрузок и смещений в сложных составных
устройствах типа автомобилей. Программы верификации и анализа логики и
синхронизации имитируют работу сложных электронных цепей.
По всей видимости, из всех методов компьютерного анализа наиболее широко
в конструировании используется метод конечных элементов (Jinite-element method — FEM). С его помощью рассчитываются напряжения, деформации, тепло
обмен, распределение магнитного поля, потоки жидкостей и другие задачи с непрерывными средами, решать которые каким-либо иным методом оказывается
просто непрактично. В методе конечных элементов аналитическая модель структуры представляет собой соединение элементов, благодаря чему она разбивается
на отдельные части, которые уже могут обрабатываться компьютером.
Как отмечалось ранее, для использования метода конечных элементов нужна
абстрактная модель подходящего уровня, а не сама конструкция. Абстрактная
модель отличается от конструкции тем, что она формируется путем исключения
несущественных деталей и редуцирования размерностей. Например, трехмерный объект небольшой толщины может быть представлен в виде двумерной оболочки [2]. Модель создается либо в интерактивном режиме, либо автоматически.
Готовая абстрактная модель разбивается на конечные элементы, образующие
аналитическую модель. Программные средства, позволяющие конструировать
абстрактную модель и разбивать ее на конечные элементы, называются препроцессорами {preprocessors). Проанализировав каждый элемент, компьютер собирает результаты воедино и представляет их в визуальном формате. Например, области с высоким напряжением могут быть выделены красным цветом. Программные средства, обеспечивающие визуализацию, называются постпроцессорами (postprocessors). О методе конечных элементов речь пойдет в главе 8.
Существует множество программных средств для оптимизации конструкций.
Хотя средства оптимизации могут быть отнесены к классу САЕ, обычно их рассматривают отдельно. Ведутся исследования возможности автоматического определения формы конструкции путем объединения оптимизации и анализа [18].
В этих подходах исходная форма конструкции предполагается простой, как,
например, у прямоугольного двумерного объекта, состоящего из небольших элементов различной плотности. Затем выполняется процедура оптимизации,
позволяющая определить конкретные значения плотности, позволяющие достичь определенной цели с учетом ограничений на напряжения. Целью часто
является минимизация веса. После определения оптимальных значений плотности рассчитывается оптимальная форма объекта. Она получается отбрасыванием элементов с низкими значениями плотности. Введение в оптимизацию
дается в главе 9.
Замечательное достоинство методов анализа и оптимизации конструкций заключается в том, что они позволяют конструктору увидеть поведение конечного
продукта и выявить возможные ошибки до создания и тестирования реальных
прототипов, избежав определенных затрат. Поскольку стоимость конструирования на последних стадиях разработки и производства продукта экспоненциально
возрастает, ранняя оптимизация и усовершенствование (возможные только благодаря аналитическим средствам САЕ) окупаются значительным снижением
сроков и стоимости разработки.
Таким образом, технологии CAD, САМ и САЕ заключаются в автоматизации
и повышении эффективности конкретных стадий жизненного цикла продукта.
Развиваясь независимо, эти системы еще не до конца реализовали потенциал интеграции проектирования и производства. Для решения этой проблемы была
предложена новая технология, получившая название компьютеризованного интегрированного производства (computer-integrated manufacturing — С1М). CIM
пытается соединить «островки автоматизации» вместе и превратить их в бесперебойно и эффективно работающую систему. CIM подразумевает использование
компьютерной базы данных для более эффективного управления всем предприятием, в частности бухгалтерией, планированием, доставкой и другими задачами,
а не только проектированием и производством, которые охватывались система-
ми CAD, САМ и САЕ. CIM часто называют философией бизнеса, а не компьютерной системой. В этом учебнике технологии CIM рассматриваться не будут.
Рис. 1.2. Шкаф для аудиосистемы
Предположим, что в технических требованиях для разработчика указано, что шкаф
должен иметь четыре полки: одну для проигрывателя компакт-дисков, одну для
проигрывателя аудиокассет, одну для радиоприемника и одну для хранения ком-
пакт-дисков. Вероятно, разработчик сделает множество набросков конструкции,
прежде чем придет к варианту, изображенному на рис. 1.2. На данном этапе он
может пользоваться автоматизированной системой разработки рабочих чертежей
(если задача решается в двух измерениях) или системой геометрического моделирования (в случае трех измерений). Концептуальный проект может быть отправлен в отдел маркетинга по электронной почте для получения отзыва. Взаимодействие разработчика с отделом маркетинга может происходить и в реальном
времени через объединенные в сеть компьютеры. При наличии подходящего
оборудования подобное взаимодействие может быть удобным и продуктивным.
Информация о готовом концептуальном проекте сохраняется в базе данных.
Туда попадают сведения о конфигурации мебели (в нашем случае — вертикальное хранение компонентов аудиосистемы друг над другом), количестве полок,
распределении полок по компонентам и тому подобные данные. Другими слова-
ми, все особенности проекта, которые можно увидеть, взглянув на рис. 1.2, упорядочиваются и помешаются в базу данных с возможностью считывания и изменения в любой последующий момент.
Следующий шаг — определение размеров шкафа. Его габариты должны быть выбраны таким образом, чтобы на каждую полку можно было поставить одну из
множества имеющихся на рынке моделей аудиотехники соответствующего класса. Значит, нужно получить сведения об их размерах. Эти сведения можно взять
в каталоге или в базе данных производителей или поставщиков. Доступ к базе данных осуществляется аналогично доступу к книгам и их содержимому при
подключении к электронной библиотеке. Разработчик может даже скопировать
сведения в свою собственную базу данных, если он планирует часто пользоваться ими. Накопление сведений о проекте подобно накоплению форм и файлов
при работе с текстовыми процессорами. Форма конструкции, изображенной на
рис. 1.2, должна изменяться в соответствии с полученными сведениями.
Затем разработчик должен выбрать материал для шкафа. Он может взять натуральный дуб, сосну, ДСП, сталь илу что-нибудь еще. В нашем случае выбор
осуществляется интуитивно или исходя из имеющегося у разработчика опыта.
Однако в случае продуктов, рассчитанных на работу в жестких условиях, в частности механических устройств, разработчик обязательно учитывает свойства материалов. На этом этапе также полезна база данных, потому что в ней могут быть
сохранены свойства множества материалов. Можно воспользоваться даже экспертной системой, которая выберет материал по свойствам, хранящимся в базе
данных. Информация о выбранном материале также помещается в базу.
Следующий шаг — определение толщины полок, дверец и боковых стенок. В простейшем случае, который мы рассматриваем, толщина может определяться глав-
ным образом эстетическими соображениями. Однако она должна быть по крайней
мере достаточной для того, чтобы избежать прогиба под воздействием установленной в шкаф техники. В механических устройствах высокой точности и структурах, рассчитанных на большие нагрузки, такие параметры, как толщина, должны определяться точным расчетом, чтобы избежать деформации. Для расчета
деформации структур широко используется метод конечных элементов. Как уже
было объяснено, метод конечных элементов применяется к аналитической моде-
ли конструкции. В нашем случае аналитическая модель состоит из каркасных
сеток, на которые разбивается шкаф, рассматриваемый в приближении лис-
тов. Переход к приближению листов может быть выполнен автоматически при
помощи алгоритма преобразования к средним осям (medial axis transformation —
MAT) [146]. Элементы оболочки приближения листов также могут генерироваться автоматически1. Параметры нагрузки, которые в нашем случае есть просто
веса соответствующих устройств, считываются из базы данных точно так же, как
и сведения о размерах. Определяя зависимость прогиба полок от их толщины,
разработчик может выбрать подходящее значение этого параметра и сохранить
его в базе данных. Этот процесс может быть автоматизирован путем интеграции
метода конечных элементов с процедурой оптимизации. Аналогичным образом
можно определить толщину боковых стенок и дверец, однако сделать это можно
и просто из эстетических соображений.
Затем разработчик выбирает метод сборки полок и боковых стенок. В идеале метод также может быть определен из расчета прочности структуры в целом или
при помощи экспертной системы, имеющей сведения о методах сборки.
После завершения этапов концептуализации проекта, его анализа и оптимизации разработчик переходит к работе над проектной документацией, описывающей
шкаф с точностью до мельчайших подробностей. Чертежи отдельных деталей (полок, дверец и боковых стенок) изготавливаются в системе разработки рабочих чертежей. На этом этапе разработчик может добавить некоторые эстетические детали, например декоративные элементы на дверцах и боковых стенках. Детальные
чертежи помещаются в базу данных для использования в процессе производства.
Изготовление шкафа осуществляется в следующем порядке. Форма каждой де-
тали наносится на необработанный материал (в нашем случае дерево) и вырезается пилой. Количество отходов можно снизить, располагая детали на кусках дерева оптимально. Разработчик может испытывать разные варианты размещения
на экране компьютера до тех пор, пока не будет найдена конфигурация с минимальным количеством отходов. Компьютерная программа может помочь в этой
работе, рассчитывая количество отходов для каждой конфигурации. Программа
более высокого уровня может самостоятельно определить наиболее экономичное размещение деталей на заготовке. В любом случае конечная конфигурация
сохраняется в компьютере и используется для расчета траектории движения пилы
станка с числовым программным управлением. Более того, программные средства позволяют разработать зажимы и крепления для процедуры выпиливания,
а также запрограммировать системы передачи материала. Эти системы могут
быть как простыми конвейерами, так и сложными роботами, передающими необработанный материал на распилку и забираю! ними готовые детали. Подготовленные детали должны быть собраны вместе. Процесс сборки также может выполняться роботами, которые программируются автоматически на основании описания конечного продукта и его деталей, хранящегося в базе данных. Одновременно проектируются зажимы и крепления для автоматизированной сборки. Наконец, робот может быть запрограммирован на покраску шкафа после сборки. В настоящее время зажимы и крепления для сборки проектируются или выбираются планировщиком процессов, а программирование роботов осуществляется в интерактивном режиме путем перемещения рабочего органа робота вручную.
Общий вид получившегося сценария показан на рис. 1.3, из которого видно, каким образом база данных позволяет интегрировать системы CAD, САЕ и САМ,
что и является конечной целью CIM.
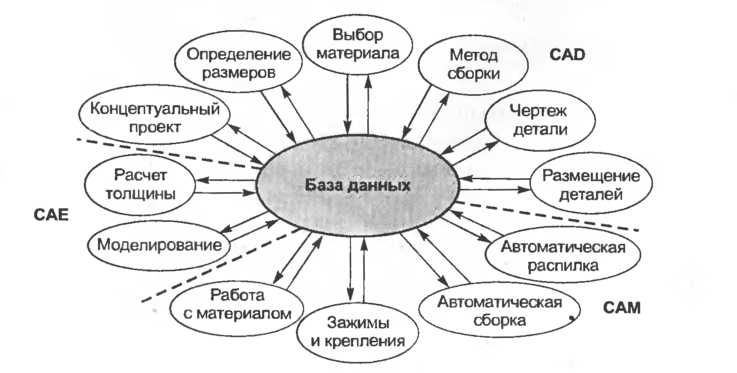
Рис. 1.3. Интеграция CAD, CAM и САЕ через базу данных
Система Автоматизированного Проектирования
САПР (CAD System - Computer Aided Design System) - это система, реализующая проектирование, при котором все проектные решения или их часть получают в результате вычисления и составления математических моделей на ЭВМ.
В настоящий момент выделяют три основные подгруппы САПР:
- машиностроительные САПР (MCAD - Mechanical Computer Aided Design)
- архитектурно-строительные САПР (CAD/AEC - Architectural, Engineering, and Construction)
- САПР печатных плат (ECAD - Electronic CAD/EDA - Electronic Design Automation)
Наиболее развитым среди них является рынок MCAD, по сравнению с которым секторы ECAD и CAD/AEC довольно статичны и развиваются слабо.
САПР в машиностроении
CAD – computer Aided Design
Общий термин для обозначения всех аспектов проектирования с использованием средств вычислительной техники. Обычно охватывает создание геометрических моделей изделия. А также генерацию чертежных изделий и их сопровождений.
CAM – Computer Aided Manufacturing
Общий термин для обозначения системы автоматизированной подготовки производства, общий термин для обозначения ПС подготовки информации для станков с ЧПУ. Традиционно исходными данными для таких систем были геометрические модели деталей, полученных из систем CAD.
CAE – Computer Aided Engineering
Система автоматического анализа проекта. Общий термин для обозначения информационного обеспечения условий автоматизированного анализа проекта, имеет целью обнаружение ошибок (прочностные расчеты) или оптимизация производственных возможностей.
PDM – Product Data Management
Система управления производственной информацией. Инструментальное средство, которое помогает администраторам, инженерам, конструкторам и так далее управлять как данными так и процессами разработки изделия на современных производственных предприятиях или группе смежных предприятий.
CAD/CAM/CAE/PDM эти системы вместе и представляют собой единый комплекс САПР.
История САПР из Интернета
Термин «САПР для машиностроения» в нашей стране обычно используют в тех случаях, когда речь идет о пакетах программ, которые в англоязычной терминологии называются CAD/CAM/CAE.
Идея автоматизировать проектирование зародилась в конце 50-х годов прошлого века, почти одновременно с появлением коммерческих компьютеров. А уже в начале 60 системы подготовки производства.
Доктор Патрик Хэнретти (Patrick Hanratty) основал компанию Manufacturing and Consulting Services (MCS) и разработал методики, которые составили основу большинства современных САПР. Вскоре появились и другие CAD-пакеты. В то время они работали на мэйнфреймах и мини-компьютерах и стоили очень дорого. Лишь крупные предприятия могли позволить себе идти в ногу со временем и использовать современное оборудование для выполнения сложных математических расчетов.
Параллельно с развитием CAD-систем бурное развитие получили CAM-системы автоматизации технологической подготовки производства. В 1961 г. был создан язык программирования APT (Automatic Programming Tools), впоследствии этот язык стал основой многих других языков программирования применительно к оборудованию с числовым программным управлением. Разработанный к 1950 г. метод конечных элементов послужил толчком к развитию систем инженерного анализа CAE. В 1963 г. был предложен способ применения метода конечных элементов для анализа прочности конструкции путем минимизации потенциальной энергии.
Так в 1971 г. компания MSC.Software выпустила систему структурного анализа MSC.Nastran, которая до сих пор занимает ведущее положение на рынке CAE систем.
К середине 80-х годов системы САПР для машиностроения обрели форму, которая существует и сейчас. Появление микропроцессоров положило начало революционным преобразованиям в области аппаратного обеспечения — наступила эра персональных компьютеров. Но для трехмерного моделирования мощности первых ПК не хватало. Поэтому в 80-е годы поставщики «серьезных» средств автоматизации проектирования ориентировались на компьютеры на базе RISC-процессоров, работавшие под управлением ОС Unix, — они были, намного дешевле мэйнфреймов и мини-машин. Параллельно снижалась стоимость ПО, и к началу 90-х средняя цена рабочего места значительно снизилась — САПР становились доступнее. Но в массовый продукт они превратились лишь тогда, когда компания Autodesk разработала свой знаменитый пакет AutoCAD стоимостью на тот момент всего 1 тыс. долл., что было в десятки раз меньше существовавших до этого систем. Правда, в те времена мощности ПК хватало лишь для двумерных построений — черчения и создания эскизов. Однако это не помешало новинке иметь огромный успех у пользователей.
Наиболее бурное развитие САПР происходило в 90-х годах, когда Intel выпустила процессор Pentium Pro, а Microsoft — систему Windows NT. Тогда на поле вышли новые игроки «средней весовой категории», которые заполнили нишу между дорогими продуктами, обладающими множеством функций, и программами типа AutoCAD. В результате сложилось существующее и поныне деление САПР на три класса: тяжелый, средний и легкий.
Традиционно, продукты САПР для машиностроения разделены на три класса: тяжелый, средний и легкий. Такая классификация сложилась исторически, и хотя уже давно идут разговоры о том, что грани между классами вот-вот сотрутся, они остаются, так как системы по-прежнему различаются и по цене, и по функциональным возможностям.