Вопросы по РPP и ТH
1. Назначение нормативов расчета режимов резания и TH.
2. Основное, штучное и машинное время.
3. Алгоритм пользования нормативами.
4. Анализ условий и требований производства, определение исходных технологических данных.
5. Выбор инструмента.
6. Сила сопротивления резания. Действие сил Р, Р, Р, на инструмент, заготовку, станок.
7. Действие сил Р, Р, Р. на резец.
8. Действие сил Р, Р, Р, на заготовку.
9. Действие сил Р. Р, Р, на станок.
10. Влияние СОЖ на составляющие силы резания.
11. Влияние обрабатываемого и инструментального материала на составляющие силы резания.
12. Элементы резания при токарной обработке.
13. Свободное и несвободное точение.
14. Скорости резания при обтачивании и растачивании резцами из твердого сплава.
Т 15. Работа с высокими скоростями резания и подачами и основные условия ее
осуществления.
16. Скорость резания при сверлении.
17. Скорость резания при нарезании резьбы.
18. Скорость резания при фрезеровании.
19. Скорость резания при фрезеровании против подачи и по подаче.
20. Влияние прерывистости резания на стойкость инструмента и допустимую скорость резания.
21. Последовательность выбора факторов режимов резания.
22. Выбор периода стойкости при одноинструментальной обработке.
23. Предельные глубины резания и подача.
24. Составляющие режима резания.
25. Многоинструментальная обработка. Расчет режимов резания.
26. Особенности расчета режимов резания при многоинструментальной обработке.
27. Определение расхода инструмента.
1.Лекция
1.Общие понятия РPP и ТH.
1.1 Назначения нормативов и их особенности.
Нормативы предназначены для технического нормирования труда и
расхода инструментов, составления управляющих программ для станков с
ЧПУ и организации рациональной эксплуатации резцов при обработке
деталей обшемашиностроительного применения на универсальном
металлорежущем оборудовании с ручным управлением и с ЧПУ при серийном и мелкосерийном использованы для разработки САПР ТП.
Нормативы предусматривают:
-широкое использование современных инструментальных материалов
(вольфрамосодержащих сплавов новых марок, том числе с износостойкими
покрытиями, безвольфрамовых ТC, режущей керамики, СТМ, и т.д.)3;
- переход в большинстве случаев с напаянных резцов на сборные, учет
конструкций этих резцов при назначении режимов резания;
-учет типоразмеров станка, жесткости и виброустойчивости технологической системы при выборе инструментов и режима резания;
-учет ограничений на режимы резания, связанных с надежностью
инструмента, требованиями и конструктивными особенностями станков;
- возможность выбора режимов резания по критериям минимальных
приведенных затрат, максимальной производительности и минимальных
затрат при заданном расходе инструмента;
- получение данных по расходу инструмента с учетом вероятности его
разрушения;
-возможность быстрого выбора стартовых режимов резания по
небольшому числу основных таблиц.
1.2.Штучное и машинное время.
Время на проведение определенной операции над одной заготовкой
называется штучным. Оно складывается и следующих времен:

где Тшт - штучное время в мин;
То - основное (технологическое) время в мин;
Тв-вспомогательное время в мин;
Tобс - время на обслуживание рабочего места в мин:
Tотд - время перерывов на отдых и личные надобности в мин.
Основное (технологическое) время- это время, в течение которого происходит процес снятия стружки. При работе на стаке основное (технологическое) время может быть машинно-ручным.
Машинное время — время, в течение которого происходит процесс снятия стружки без непосредственного участия рабочего (например, время на точение валика на токарном станке при включенной механической подаче); в дальнейшем это время будем обозначать через Тм.
Машинное время за один проход: 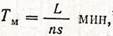
где L — путь инструмента в направлении подачи в мм; n — частота вращения заготовки (шпинделя) в об/мин; s — подача в мм/об.
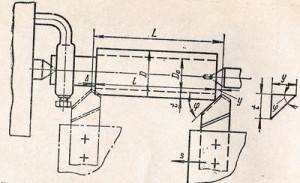
Рис.1.
В свою очередь (рис. 1): L = l + у + Δ мм,
где I — размер обработанной поверхности в направлении подачи в мм; у — величина врезания в мм; Δ — выход режущего инструмента (перебег) в мм;
Δ. = 1÷2 мм
Величина врезания у определяется из прямоугольного треугольника (рис.1):
у = tctgф мм,
При поперечном точении валика (рис. 23, а):
При поперечном точении трубы (рис. 23, б):
При разрезке валика отрезным резцом с режущей кромкой, параллельной
Оси рис: 
При работе резцом с наклонной режущей кромкой
мм
При разрезке трубы резцом с режущей кромкой, параллельной оси (рис. 2):
мм
а резцом с наклонной режущей кромкой:
Если при обработке заготовки приходится делать несколько проходов, с условием, что все они совершаются при одинаковой частоте вращения и подаче, то машинное время:
мм

где i — число проходов
Количество проходов зависит от припуска * на обработку, и, если предположить, что каждый проход совершается с одинаковой глубиной резания (последний проход, точнее переход, производится с меньшей глубиной, чем предыдущие), то:
i=h/t
где h— припуск на обработку на сторону в мм; t— глубина резания в мм.
Подставив в формулу машинного времени выражение для числа проходов, получим:

Машинно-ручное время - это время, в течение которого на станке
происходит процесс снятия стружки с непосредственным участием рабочего
(например, время на подрезку торца валика на токарном станке с ручной
подачей).
Вспомогательное время - время на установку, закрепление и снятие
заготовки и готовой детали; на пуск и остановку станка; на изменение чисел
оборотов станка и величины подачи; на установку, снятие и подвод к
заготовке режушего инструмента; время на промер заготовки и готовой
детали.
Время на обслуживание рабочего места- время на уход за рабочим
местом при выполнении данной работы. Сюда входит время на подналадку
регулирование станка в процессе работы; время на правку инструмента, в
его смену вследствие затупления и на его раскладку и уборку в начале
конце смены; время на чистку и смазку станка.
Время перерывов на личные надобности рабочего предусматриваете
для всех видов работ. При выполнении физически тяжелых и утомительны
работ предусматривается еще время и на отдых. Время на естественные
надобности и отдых, как и время на обслуживание рабочего места, дается
процентном отношении от основного и вспомогательного времени.
При изготовлении партии деталей в количестве n шт. время на партию
Тларт подсчитывается по формуле:
Т - подготовительно-заключительное время на партию в ми
включающее в себя время на ознакомление с работой, на чтение чертежей,
наладку оборудования и на выполнение пробной обработки.
Лекция 2.
Алгоритм пользования нормативами.
1.Анализ условий и требования производства, определение
исходных технических данных.
- форма, размеры детали и требования к ней
группа операций, группа жесткости технологической системы, группа
обрабатываемых материалов
-точность заготовки и детали. Стадии обработки
-минимальные по точности и максимальные по виброусточивости глубины резания
- уровень надежности инструмента
- СОЖ
- требования и ограничения по производительности, приведенным затратам,
расходу инструмента.
2. Выбор инструмента.
-материал режущей пластины
- вид резца, форма в плане
-тип конструкции резца
-форма передней поверхности и геометрические параметры лезвия
3. Выбор режимов резания
- глубина резания с проверкой по виброустойчивости (для черновой
обработки)
- подача по прочности инструмента (для черновой обработки), подача по
заданной точности или шероховатости поверхности с проверкой по точности
(для чистовой обработке)
- проверка Р.SP. (для черновой обработки)
- скорость резания по износостойкости инструмента
- проверка скорости резания по эргономическим соображениям Vс V,
- проверка N <N,
- частота вращения
-проверка частоты вращения при заданной массе детали (для тяжелых
станков)
- проверка М.S M.p ma
-основное и штучное время
-сравнение производительности с заданной
4. Определение расхода инструмента
- период стойкости Т, число периодов стойкости К и полный период
стойкости Т
- сравнение те временем основным
-расход R
- сравнение расхода лимитом на инструмент R<RnВыбор инструмента.
Лекция 3.
Выбор инструмента.
Основные требования, предъявляемое материалам, определяется условиями, в которых находятся контактные инструментальным поверхности инструмента при срезании с детали припуска, оставляемого на обработку.
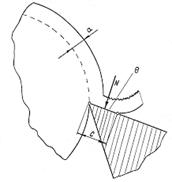
Рис.1. Схема срезания слоя режущим клином инструмента (Б ширина
срезаемого слов, С площадь контакта, N- нормальная сила)
1. Высокая твёрдость (Н, > Н., значительно)
2. Высокая механическая прочность (
). Режущий клип
инструмента должен выдерживать такие высокие давления без хрупкого разрушения и заметного пластического деформирования. Помимо этого режущий инструмент часто приходится работать условиях прерывистого резания (колебательные нагрузки).
При высокой жесткости технологической системы или необходимости
уменьшения подачи соответственно роста скорости резания целесообразно использовать для инструмента материалы повышенной износостойкости. При пониженной жесткости технологической системы, необходимости повышения подачи и надежности инструмента целесообразно выбирать инструментальные материалы повышенной прочности.
В процессе резания вследствие превращения механической энергии в
тепловую со стороны детали на инструмент действует мощный тепловой на передней поверхности инструмента поток, и в результате чего устанавливается весьма высокая температура
-800-900 "С.
Из-за интенсивного разогревания контактные поверхности инструмента теряют свою исходную твердость, размягчаются и быстро изнашиваются.
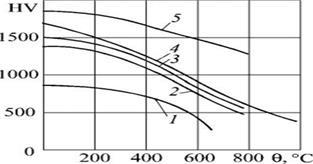
Рис 2 Влияние температуры на твердость инструментального материала.
3.Высокаятеплостойкость
4.Малочувствительность изменениям (прерывистое резание)
5.Высокая износостойкость. Под износостойкостью понимают
способность инструментального материала сопротивляться при резании удалению его частиц с контактных поверхностей инструмента.
6.Экономичность инструментального материала.
Всем перечисленным требованиям в тои или иной степени отвечают
следующие группы инструментальных материалов:
1) Углеродистые и легированные инструментальные стали У9А, У10,
У12- HRС 61-63. вследствие отсутствия в стали легирующих химических элементов углеродистые стали хорошо шлифуются и являются дешевыми.
Недостаток -низкая теплостойкость (200-250℃), быстрая изнашиваемость. Изготавливают ручные слесарные инструменты, метчики, плашки, развертки, сверла, зенкера, концевые фрезы.
XBS, ХВГ, 9ХС -HRC 63-65. Протяжки крупных размеров.
2) высоколегированные инструментальные (быстрорежушие) стали и
сплавы PIR, Р9, Р12. Р6М3, Р6М5 HRC 60-63. Тeплостойкость 600℃.
Изготавливают фасоннве резцы, винтовые сверла, зенкеры, развертки,
метчики, плашки, винторезные головки, цилиндрические, осевые и концевые фрезы, фасонные и резьбовые фрезы, долбяки, шеверы, протяжки.
3) твердые сплавы- вольфрамовая, титано-вольфрамовая, титано-
тантало-вольфрамовая.
Допускают высокие скорости резания, недостаток прочность на изгиб и ударная вязкость меньше, чем у высоколегированных сплавов.
Сплавы группы ВК - обработка хрупких материалов (чугуны).
HRA 87-92. Можно обрабатывать закалённые стали.
Сплавы группы ТК - обработка некоторых сталей и сплавов,
обладающих высокой твердостью и вязкостью, с большими сечениями срезаемого слоя, при малой жесткости технологической системы CПИД. Сплавы группы ТТК по применению являются универсальными и их можно использовать при обработке как сталей, так и чугунов. При выборе марки твердого сплава в пределах каждой группы необходимо руководствоваться следующим основным правилом: чем тяжелее условия работы инструмента в силовом отношении, тем больше кобальта должен содержать сплав, и чем легче силовой режим, тем больше должно содержаться карбидов титана и вольфрама.
Вольфрам влияет на прочность, титан на износостойкость.
Если целесообразно использование одного и того же инструмента на
нескольких переходов, то его выбирают по наиболее трудоемкому,
Нагрев до 900℃.
4) минеральная керамика основа кристаллическая окись алюминия,
микролит ЦМ-332, теплостойкость около 1200℃. допустимая скорость в
1,3-2 раза больше, чем в твердых сплавах
5) алмазы и кубический нитрид бора (алмаз кристаллический
углерод). Температура нагрева 1500- 1700℃. недостаток высокая хрупкость относительно низкая теплостойкость Обработка закаленных сталей.
Лекция 4
Сила сопротивлении резания. Действие сил
, на
инструмент, заготовку и станок.
При токарной обработке в условиях
равнодействующая R сила сопротивления резанию раскладывается на три
Rаимно перпендикулярные составляющие силы, действующие на резец:
Рz - силу резания, или тангенсальную силу, касательную к поверхности
резания и совпадающую с направлением главного движения станка;
Рx - осевую силу, или силу подачи, действующую параллельно оси
заготовки в направлении, противоположенном движению подачи;
Py – радиальную силу, направленную горизонтально и
перпендикулярно оси обрабатываемой заготовки.
Равнодействующая сила R, как диагональ параллелепипеда, равна

и 
Рис. Разложение равнодействующей силы R на составляющие.
На соотношение между силами Рz. Py. Px. влияют элементы режимы
резания, геометрические элементы режущей части инструмента, материал
обрабатываемой заготовки, износ инструмента и др.
Приборы, предназначенные для измерения составляющих называют динамометрами. Если динамометр измеряет одну составляющую, то он называется
однокомпонентным, резания, составлявшую, двухкомпонентным и три трехкомпонентным.
Для исследования процесса резания:
1) при точении, растачивании, нарезании резьбы резцом и кругом
шлифовании применяют трёхкомпонентные динамометры:
2) при сверлении, зенкеровании, развертывании, нарезании резьбы
называется метчиком а двухкомпонентные, измеряющие составляющую силы резания, направленную вдоль оси инструмента, и крутящий момент.
3)при фрезеровании плоскостей, фасонных поверхностей, венцов зубчатых
колес, однокомпонентные плоском шлифовании - однокомпонентные
трехкомпонентные динамометры;
4) при протягивании, зубодолблении- в основном однокомпонентные
динамометры.
По принципу действия различают динамометры: упруго-механические,
гидравлические и упруго-электрические.
Действия сил на резец
Сила резания Рz, изгибает резец в вертикальной плоскости, сила Рy,
стремится оттолкнуть резец от заготовки, а сила Рx стремиться изогнуть
резец в горизонтальной плоскости и вывернуть его из резцедержателя.
Очевидно, что чем больше вылет резца 1, тем больше будет изгибающий
момент
кГмм,
тем, следовательно, большим должно быть сечение державки резца. Во
набивание смещения резец от действия сил Рy и Рx он должен быть прочно
закреплен резцедержателе.

касательные напряжения от крутящего момента:

Сила Р, кроме нормальных напряжений от изгибающего момента и
касательных напряжений от перерезывающей силы при изгибе, создает
касательные напряжения от крутящего момента:
Сила Р, кроме сжатия, создает продольный изгиб.
Напряжения, вызванные в державке силами Рz. Py. Px не должны
превышать напряжений, допускаемых материалом державки по его
прочности жесткости. В практике, однако, принято рассчитывать резец
только на плоский изгиб по силе Рz, не учитывая деформаций от сил Рy и Рx.
Наряду с напряжениями в державке резца. сила Рz, создает большие
напряжения и в режущей части инструмента пластинке. В зависимости от
значений переднего угла пластинка может испытывать деформации изгиба и
среза или деформации сжатия. Для каждого резца сила Рz должна быть не
больше определённой величины, иначе напряжения, выpванные этой силой,
достигнут предела прочности и пластинка разрушится. Это особо
важно для резцов, оснащенных пластинками из твердых сплавов или
минералокерамических материалов (вследствие их большой хрупкости).
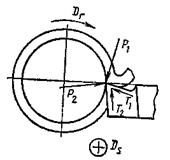
Pис. схема действия сил на режущую пластинку:
а- при положительном значении у.
6- при отрицательном значении у:
Силы Рz. Рx, Рy. оказывают большое влияние на режущую часть
инструмента и в том случае, когда напряжения не достигли ее предела
прочности, т.к. чем больше эти силы, тем интенсивнее протекает износ
инструмента в процессе резания.
При увеличении главного угла в плане отношение
будет
непрерывно возрастать, достигая максимума при
=90. Вследствие чего
сила Р. достигает максимального значения, а сила Р, минимального.
Влияние силы резания на составляющие силы резания.
При увеличении глубины резания и подачи растет площадь сечения
срезаемого слоя, что вызывает возрастание всех составляющих силы резания,
однако на практике во всех случаях глубина резания на составляющие силы
резания влияет больше.
В формулах

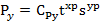

определяющих связь между глубиной резания, подачей и составляющими
силы резания, это обстоятельство выряжается неравенством показателей
степени
. Но ширина срезаемого слоя влияст на силу Р более сильно
чем толщина.
Изменение скорости резания влияет на составляющие силы резания
коэффициента усадки стружки. При резании материалов, не склонных к наростобразованию, коэффициент усадки монотонно убывает при увеличении скорости резания. Так же ведут себя и составляющие силы резания уменьшающиеся при увеличении скорости резания.
Увеличение радиуса переходного лезвия вызывает уменьшение
переходного угла в плане в различных точках лезвия. Кроме того, увеличение
длины переходного лезвия ухудшает условия стружкообразования у
вершины резца. Вследствие этого силы Р. и Р. при увеличении радиуса
возрастают, а сила Р. уменьшается.



Действия сил на заготовку.
Сила Рх прижимает заготовку к переднему центру (или стремиться
сдвинуть заготовку в осевом направлении при креплении се в патроне и создаёт момент:
кГмм
который вывертывает заготовку из центров
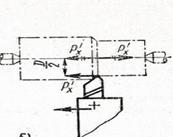
Рис. Действие сил Рz Рx Рy на заготовку.
Действие сил на станок.
Сила резания Рz, будучи наибольшей по своему значению и совпадая с
направлением скорости резания, через резец действует на суппорт и станину. Сила Рz через заготовку действует на центры и заднюю бабку. Пo этой силе производится расчёт ответственных деталей
станка и мощности, затрачиваемой на резание.
Радиальная сила Рy действует через резец на суппорт и станину, а сила
Рy через заготовку на шпиндель, центры и заднюю бабку станка. По этой силе производится расчет давления на подшипники шпинделя.
Сила подачи Рх действует через резец на механизм подачи станка, а
сила Рх через заготовку- на шпиндель и его опоры в осевом направлении.
Сила Рх преодолевается механизмом подачи станка, а потому в основном по ней и рассчитываются детали коробки подач, фартука и упорные подшипники шпинделя, а также мощность, потребная для осуществления движения подачи.
Лекция 5
Сила резания.
На силы Рz Рx Рy влияют в основном следующие факторы:
1. Глубина реяния.
2. Подача.
3. Передний угол
.
4. Радиус закрепления при вершине резца.
5. СОЖ
6. Скорость резания.
7. Износ реза.
8. Главный угол плане
.
9. Обрабатываемый материал.
Влияние СОЖ на составляющие силы резания.
При изнашивании резца только по задней поверхности силы Р. Р, Р.
растут непрерывно, причем особенно сильно увеличиваются горизонтальные
составляющие Р, и Ра если одновременно изнашиваются передняя и задняя
поверхности, то при резании сталей в начальный период изнашивания силы
Р. Р, Р, остаются постоянными или даже несколько уменьшаются.
Это объясняется тем, что рост сил за счет увеличения площадки износа
задней поверхности и притупления главного лезвия компенсируется
увеличением переднего угла вследствие образования лунки на передней
поверхности. При дальнейшем изнашивании реза силы Рz Рx Рy вновь
растут. Хорошо развитый нарост, выполняя функции режущего клина,
прикрывает контактные поверхности инструмента, и их изнашивание мало
сказывается на росте составляющих силы резания. Количественно влияние
затупления резца на составляющие силы резания учитывают поправочным
силовым коэффициентом
.
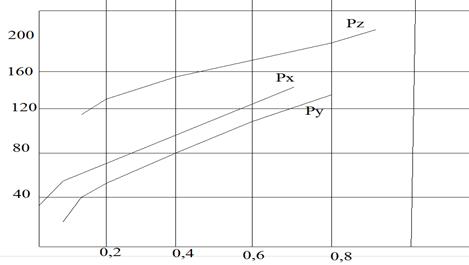
Рис. Влияние затупления резца на силы Рz Рx Рy. при изнашивании
резца только по задней поверхности.
Применение СОЖ, обладающих высокими смазочными свойствами,
облегчат условия стружкообразования, уменьшает коэффициент усадки
стружки и величину относительного сдвига. Это связано в основном с
уменьшением среднего коэффициента трения и силы трения на передней поверхности. Вследствие улучшений условий стружкообразования
составляющие силы резания при применении СОЖ уменьшаются, а также
происходит уменьшение шероховатости обработанной поверхности,
снижение интенсивности износа режущего инструмента.
Все применяемые в настоящее время СОЖ можно разбить на две
основные группы: главным образом охлаждающие и главным образом
смазывающие.
шероховатости обработанной поверхности,
К первой группе относятся жидкости с малой вязкостью, большой
теплоемкостью и теплопроводностью. Сюда относятся водные растворы
минеральных электролитов и водные эмульсии. Ввиду их большой теплоемкости они применяются в тех случаях, когда основной целью является охлаждающее действие для повышения стойкости режущего инструмента (при обдирочных работах, когда имеет место большое
тепловыделение и чистота обработанной поверхности не имеет большого
значения).
К жидкостям второй группы, обладающим высокой маслянистостью,
относятся минеральные, растительный, животные и компаундированные
масла (смесь минеральных масел с растительным или животным), а также
керосин и растворы в масле или керосине поверхностно-активных веществ.
Жидкости этой группы применяются при чистовых и отделочных работах,
когда требуются высокие частота и точность обработанной поверхности.
Эффект уменьшения главной составляющей силы резания при
применении различных СОЖ оценивают поправочным силовым коэффициентом
, значения которого при резании сталей зависимости от
применения СОЖ колеблются в пределах 0,97- 0,75.
Влияние обрабатываемого и инструментального материала на
составляющие силы резания.
Механические свойства обрабатываемого материала весьма сложно и
противоречиво влияют на составляющие силы резания. С одной стороны,
повышение прочности и твердости обрабатываемого материала увеличивает
угол сдвига, что уменьшает коэффициент усадки стружки и величину сдвига.
В результате этого уменьшаются работы деформации и стружкообразования
и, как следствие, составляющие силы резания. С другой стороны, с
повышением прочности и твердости напряжения на условной плоскости
увеличивает работы деформации, стружкообразования и составляющие силы резания. В зависимости от того что является преобладающим, силы Рz Рx Рy при увеличении прочности
обрабатываемого материала могут возрастать и уменьшаться. Если при
увеличении прочности материала коэффициент усадки стружки уменьшается
сравнительно мало, то силы Рz Рx Рy возрастают, а если увеличение
прочности сопровождается значительным снижением коэффициента усадки,
возрастают, то это приводит к уменьшению сил.
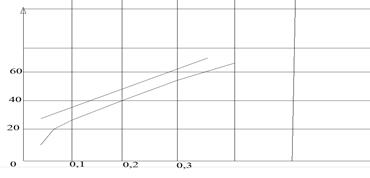
Рис. Влияние толщины срезаемого слоя а на силу Рz, приходящуюся
на единицу длины главного лезвия при резании стали 20X,сплавов ВТ1 и ВТЗ.
Лекция 6
Элементы резания при токарной обработке.
1. Скорость, подача и глубина резания.
Скорость резания- величина перемещения точки режущей кромки относительно
поверхности резания в единицу времени в процессе осуществления главного движения.
м/мин
Гле D- наибольший диаметр поверхности резания, мм
об/мин
При продольном точении (если диаметр заготовки вдоль всей оси ее
длины одинаков, а число оборотов неизменно) скорость резания имеет
постоянную величину на протяжении всего времени резания. При подрезке
торца, когда резец перемещается от периферии заготовки к центру или,
наоборот, от центра к периферии, скорость резания при постоянном числе
оборотов переменна. Она имеет наибольшее значение у периферии и равна
нулю в центре. Однако и в этом случае в расчет принимается максимальная
скорость резания, соответствующая диаметру D.
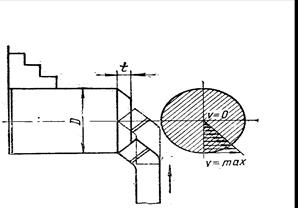
Рис. Изменение скорости резания при поперечном точении.
Подача- величина перемещения режущей части кромки относительно
обработанной поверхности в единицу времени в направлении движения подачи.
При токарной обработке различают продольную подача, когда резец
перемещается в направлении, параллельном оси заготовки; поперечную
подачу, когда резец перемещается в направлении, перпендикулярном к оси
заготовки и наклонную-под углом к оси заготовки.
Различают перемещения резца за 1 мин, и подачу за 1 оборот заготовки, т.е. величину относительного перемещения резца за время 1 оборота заготовки. Минутная подача обозначается,
в мм/об, а подача за 1 оборот в мм/об:
мм/об
Глубина резания- величина срезаемого слоя за 1 проход, измеренная в
направлении, перпендикулярном к обработанной поверхности. Глубина
резания всегда перпендикулярна направлению движения подачи, и при
наружном продольном точении она представляет собой полуразность между
диаметром заготовки и диаметром обработанной поверхности, полученной
после 1 прохода:
мм
Ширина среза
- расстояние между обрабатываемой и обработанной
поверхностями, измеренное вдоль режущей кромки.
Толщина среза а- расстояние между двумя последовательными
положениями поверхности резания, измеренное в направлении,
перпендикулярном к режущей кромке в плоскости передней поверхности резца.
Рассмотрим зависимость между толщиной среза а и подачей s, между
шириной среза b и глубиной резания при s < t.
При
из прямоугольного треугольника КNL следует, что
или

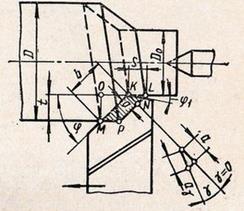
Рис. Сечение среза (s<t)
При
из прямоугольного треугольника КОМ следует, что ширина
среза

Из приведенных формул видно, что при постоянных подаче и глубине
резания t с увеличением главного угла в плане
толщина среза
увеличивается, а ширина уменьшается.
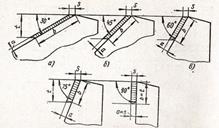
Рис. Изменение толщины и ширины среза с изменением главного
угла в плане
(при s< t)
При
= 90 толщина среза а равна подаче s, а ширина среза b равна
глубине резания t.


в зависимости от соотношения между подачей и глубиной резания
принято называть срез прямым, когда s < t квадратным, когда s=t, и
обратным, когда s >t.
Площадь поперечного сечения среза PLKМ
мм2
Вследствие увеличенной толщины (и немного ширины) стружки
плошать поперечного сечения стружки (срезанного слоя) будет больше
площади поперечного сечения среза.
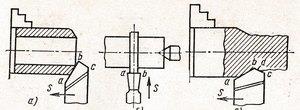
Рис. Свободное и несвободное резание.
Площадь поперечного сечения среза (f=аb представляет собой площадь
номинального или расчетного сечения. Однако номинальное сечение
получается только при свободном резании (когда в работе принимает участие
лишь главная режущая кромка) или случае, когда резец имеет площадку со
вспомогательным углом в плане
и длина площадки больше подачи. В
этих случаях резец будет снимать весь предназначенный для срезания слой,
не оставляя на обработанной поверхности остаточных гребешков.
При несвободном резании на обработанной поверхности остаются
гребешки, размеры которых зависят от подачи, радиуса закругления при
вершине резца и главного и вспомогательного углов в плане. Это хорошо
показано на рис. за 1 оборот заготовки резец переместился на величину
подачи и из положения 1 перешел в положение 2, оставив на обработанной
поверхности гребешок высотой Н.
Если обозначить действительное сечение среза через
, площадь
остаточных гребешков через
, то

Высота остаточных гребешков во многом определяет величину
шероховатостей (микрогеометрию) обработанной поверхности: чем меньше
высота Н, тем выше чистота обработанной поверхности (меньше
шероховатость).
Объем стружки, снятой за 1 мин работы, может быть вычислен по
формуле:
см3/мин
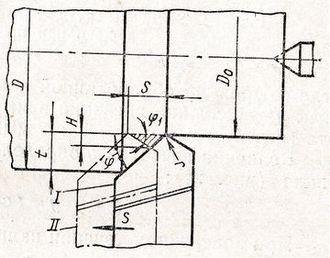
Рис. Остаточный гребешок при точении.
При резании резцом с радиусом закругления R=0 теоретическая высота
гребешка Н определится как
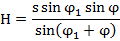
Когда теоретический профиль обработки поверхности получается как
след криволинейного участка режущей кромки ВCF с радиусом r, высота
оставшихся гребешков Н определится:
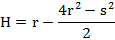
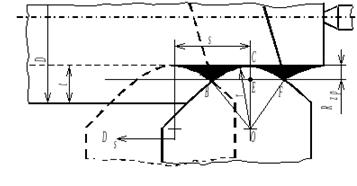
Рис. Профили обработанной поверхности
Высота гребешков (шероховатость) уменьшается с уменьшением
подачи s главного
и вспомогательного
углов в плане и
с увеличением радиуса г закругления при вершине резца в плане.
Наряду с рассмотренным влиянием s,
,
, г (которые в основном
воздействуют как чисто геометрические факторы), на шероховатость
(микрогеометрию) обработанной поверхности оказывает влияние в процессе
стружкообразования и ряд других факторов. К ним в основном относятся
скорость резания, свойства обрабатываемого металла, передний угол, СОЖ,
упругие деформации поверхности, шероховатость режущей кромки инструмента, износ инструмента.
Лекция 7.
Виды фрезерования.
t – глубина фрезерования.
B- ширина фрезерования
Главное движение при фрезерование – вращательное (его имеет фреза), движение подачи (обычно прямолинейное) может иметь как заготовка, так и сама фраза.
При фрезерование зуб за один оборот фрезы находится под воздействием стружки относительно малое время. Большую часть оборота он проходит по воздуху, не производя процесс резания. При этом зуб охлаждается, что положительно сказывается на его стойкости. Для продолжения процесса стружкообразования вдоль всей длины заготовки зуб должен вновь врезаться в срезаемый слой, что сопровождается ударом о его режущую кромку. Ударная нагрузка приводит к снижению стойкости зуба фрезы и в отдельных случаях – к его полному разрушению
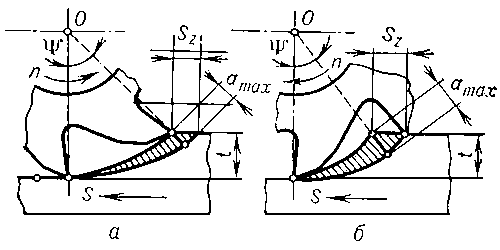
Рис.Врезание зуба при встречном цилиндрическом фрезеровании.
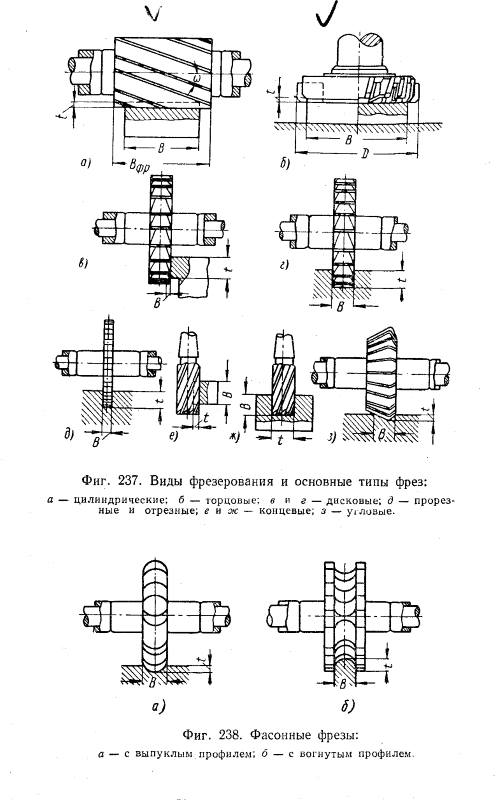
При движениях фрезы и заготовки (встречное цилиндрическое фрезерование) зуб фрезы должен начинать резание с малой (нулевой) толщины, чего, однако, вследствие наличия радиуса округления между передней и задней поверхностями он сделать не может. Вместо начала резания в точке К зуб начнет стружкообразование только в некоторой точке М, где толщина среза будет равна примерно радиус округления p. На участке же КМ зуб скользит по упрочненной поверхности резания, образованной впереди идущим зубом, что вызывает большое трение и износ по задней поверхности.
Периодичность работы зуба фрезы, переменная толщина и ширина среза (а следовательно, переменная и площадь поперечного сечения среза), а также непостоянное число зубьев, одновременно находящихся в работе, вызывают переменное значение сил, моментов и мощности, необходимых для осуществления процесса стружкообразования.
Подача- относительное перемещение заготовки и фрезы при вращение последний. У обычных фрезерных станков подача может происходить в горизонтальной (горизонтальная подача) и в вертикальной (вертикальная подача) плоскостях.
При фрезеровании различают три размерности подача: подача на один зуб фрезы – в мм/об, подача за 1 мин – 